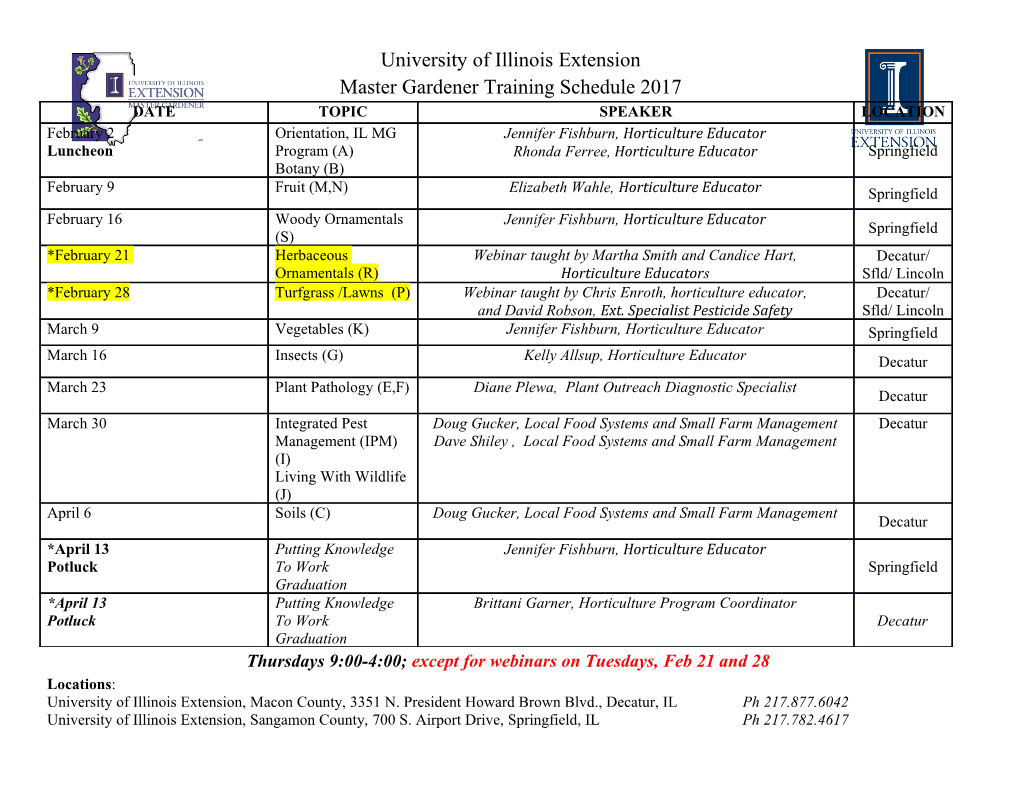
L Quest for bulk in a fine paper machine Authors Petteri Halme Rui Stefanini Jr Keywords Bulk Fine Paper Through studies during the over web has typical dryness of no less Machine Press Section Dryer Section past 5 years focus on this dilemma a than 9698 for uncoated fine Sizing Calender number of technical solutions has papers This offers a totally new become available and can be applied philosophy and possibility for high ABSTRACT in the entire paper machine line These bulk sheet production Paper bulksmoothness combina technologies will help paper machines tions are considered as the most to reach higher production rates WET PRESSING IS NOT NECESSARILY important sheet properties for bearing in mind this bulk preservation THE BUM DESTROYER uncoated woodfree papers From This article discusses the technology Wet pressing influence on paper paper machine technology point of and philosophy of the solutions density and not calendered smoothness view bulk conservation usually developed and their contribution in the is a clear and familiar concept to every requires gentle processing of the web eternal quest for bulk body on all uncoated fine paper Wet which often is contradictory for pressing influence on paper machine highspeed runnability requirements PHILOSOPHY OF REMOVING OPEN runnability is I believe even clearer Highspeed runnability typically DRAWS to ali as high press outcoming dryness requires extreme paper machine Since long time ago it has been is beneficial for both paper machine processing conditions Good example of acknowledged that the position of the capacity and runnability this is the press outcoming dryness as an first open draw in a paper machine will Pressing paper with higher nip always increasing processing parameter determine the first bottleneck for web loads provides dryness but at increasing speeds which usually ask runnability For a long period of time simultaneously has anegative effect on for high dry content to manage web this draw used to be between former bulk Shoe presses have proven to help handling in different sections ofthe paper and press at web dryness of 2024 in this equation to some extent but the machine Unfortunately increasing press Later pickup roll was introduced to correlation between press load and dryness typically means that higher press overcome this problem bulk still remains loads are needed and this again is not Today its common that the first The question will soon arise Is favorable for bulk conservation open draw is located after press it still possible to dream about Another disturbance for good web center roll at web dryness of higher production rates without tear runnability is the quest for low tensile 4250 Ever increasing need for of bulk loss ratio on uncoated woodfree grades higher speeds and savings in raw During past five years a number of Most of printing and writing papers materiais put pressure to move this studies have been carried out on pilot can improve its web runnability by draw further towards a greater paper machines to learn how a fine setting more fibers in machine dryness and sheet strength Closed paper web could be pressed in an 0 direction ie running with high tensile draw technology has moved this first optimal way This includes a number 0 ratio Usually this is not acceptable for open draw all the way down to right of pilot comparison studies as well a The common denominator for all W sheeted uncoated products in front of the size press where the Authors references 1 Metso Paper Jyvaskyla Finland 2 Metso Paper Sorocaba Brazil F than bottom This difference can be corrected in calendering The study continues with closed draw press configurations this time with double nip press with different first press configurations These altii3aL studies suggest that from the bulk point of view lst press should be operated as gently as possible While 2nd press takes care of the final dryness Of k course 2nd press also has an effect on SER YXK ÉSKM bulk but according to studies it has only half of the effect of what the lst Figure 1 Development steps of first open draw press does A double nip press offers only a press trials was the importance of the A threenip press produces a sheet slightly asymmetric sheet coming out first nip for bulk Let us start with the where bottom side is pressed against from press This is an important benefit most famous press concept the three the smooth roll twice but topside not since it will help at paper calendering nip press configuration and the bulk This fact makes the sheet coming out Smooth and symmetric paper can be smoothness curve created with this of the press to be somewhat reached at gende calendering parameters concept asymmetric topside being rougher which helps for bulk preserving i Ai F hLZ9t Y IF IJILIIL iTr IlY RI LAAV L RPN Figure 2 Nip peak pressure effect on dryness and bulk using fresh Scandinavian fine paper furnish 1 F1 LJ L S tu 16C ILsiihl ii fL9 LY W317üILl4h7 I1 Nildl v N ua O N m 41iS9 A a Mu pi9MLY i ká C1Ptir LU s19S1 W 1 51797 21 Figure 4 Bulkroughness window of a double nip Iw Figure 3 Bulkroughness window of three nip press with presses with different 1st press configurations and South European fine paper furnish with South European fine paper furnish a reach its production targets if press is not allowed to operate at high srr tT pressures iãde Answer to this question is simply a to add dryer capacity Nowadays this is possible also without extending paper machine length Figure 5 Bulki Rebuilt impingement technology is roughness window an applicable method to increase of a single nip drying capacity of existing dryer press with South sections In this technology a free r tl 1 5 13 1 European fine standing air dryer unit or units can paper furnishes be added in paper machine basement without disturbing the cylinder Modem shoe press is proven to be a transfer allows first press to operate at arrangement of paper machine itself very a powerful de watering tool the lowest loading conditions still With these units the lost capacity Actually its powerful enough to operate offering safe sheet transfer after nip originated from press highbulk even alone without the assistance of The 2 d press is equipped with mode operation can be compensated other presses A single nip press transferbelt smooth impermeable and capacity targets of the rebuild can equipped with two felts or feltalikes sheet conveyor which automatically be still met is an interesting option for compact cost grabs the sheet on top of it creating so Another dryer related question as efficient water removal for fine papers another drect transfer position a result of press high bulk operation The first press rule is valid for this When press section is built according mode is simply the dryer runnability press configuration too In this case to these rules it has no felt sandwiches Conserving dryness for the sake of the first press is the last press at the and itresults on an even moisture profile bulk is usually a bad news for the early same time Pressing heavily in the nip after the press This is beneficial because dryers Increasing speed increases the makes the calendering curve to move no extra profiling equipment press need for web tension to avoid sheet itself to less bulk direction steambox or rewet sprays are needed disturbance such as wrinkles and A single nip press produces close to which is a clear benefit in bulk fluttering This threat is typically most symmetric sheet after press depending operation cost point of view severe in the first two dryer groups on the felt selection The absolute The dryer runnability components roughness and topography of the sheet DRYER SECTION ROLE GROWS become even more critical as moister depends basically on the felt design STRONGER and weaker sheet run through dryers When analyzing these results an Operating press on high bulk Both dryness and filler content have optimal press configuration for mode plus having closed draw where significant effect on sheet stretching uncoated fine paper pressing can be high draw is no more needed to properties If web is not capable to chosen The idea of the press is to use transfer the sheet to dryers sets maintain its tension it has to be helped as low loading in first press as possible pressure on dryer section operations with runnability components For this purpose the drect transfer First thing to worry about is the dryer presses are the most favorable Direct capacity How can the paper machine FIM PRESS SE COND PRESS 0N Sh 1C Pacas F C41 r 0 W Trshft Figure 7 Impingement dryer blows Figure 6 Direct transfer principie hot air against the web starch amount to the sheet will result eo in a demand for thinner film applied on the surface of the roll in an MSP unit Here very finely grooved rods or even smooth rods are needed 5D 1 It is of worth mentioning also that increasing the solids content of the Figure 8 Dry starch will demand adequate stability ness effect on of the starch itself with sufficient sheet tension at binding ability 1 strain with x c w V fine paper fur FINAL APPEARANCE OF THE SHEET IS nish DETERMINED BY CALENDER Calender determines the final sheet The beginning of fine paper development Generally minimizing quality Target is to produce paper machine dryer should be designed in the Starch amount can be favorable in which is at the same time bulky such a manner that they offer the best terms of bulk optimization Starch smooth and symmetric in smoothness grip of the web when coming out from solids content despite of its strong As press will produce a
Details
-
File Typepdf
-
Upload Time-
-
Content LanguagesEnglish
-
Upload UserAnonymous/Not logged-in
-
File Pages5 Page
-
File Size-