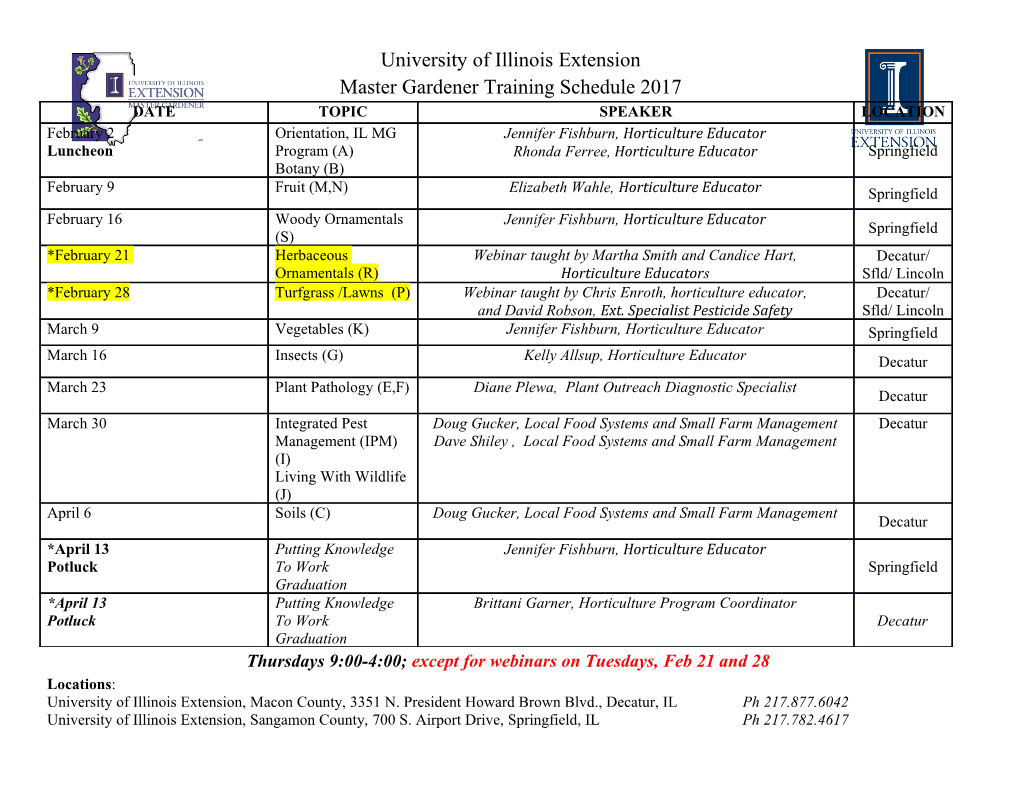
CE NTRE for RESEARCH and TECHNOLOGY HELLAS INSTITUTE for SOLID FUELS TECHNOLOGY and APPLICATIONS (CE.R.T.H. / I.S.F.T.A. ) OVERVIEW of LOW TEMPERATURE CARBONISATION Present Status – Properties, Yields and Utilisation of LTC chars – Survey of Various Methods – Pre-treatment Conditions & Effects – Advantages, Economic & Technological Development Report prepared for ISFTA – May 2004 OVERVIEW of LOW TEMPERATURE CARBONISATION Present Status – Properties, Yields and Utilisation of LTC chars – Survey of Various Methods – Pre-treatment Conditions & Effects – Advantages, Economic & Technological Development CE.R.T.H. / I.S.F.T.A. Report prepared in the framework of CFF OPET – E.C. co-funded project Contract # NNE5 – 2002 – 97 WorkPackage # 4: Promotion of Low-Temperature Carbonisation (LTC) Technology Prepared by Dr. George Skodras & Mr. Panayiotis S. Amarantos Scientific Coordinator Dr. George Skodras ii EXECUTIVE SUMMARY Low temperature carbonisation is essentially a process for producing fuels-solid, liquid, and gaseous – from coal and other carbonaceous material, such as biomass and organic wastes. The products from the various low temperature processes, however, vary in quantities and qualities depending on the coal used and the nature of the treatments to which it has been exposed. The differences can be of great significance in the selection of a process for a given application, and careful study is necessary before a choice can be made. The process descriptions have shown that many methods for the low-temperature carbonisation of coal are available for use, and from them chars with a wide variety of characteristics can be obtained. One desirable characteristic of char is its smokeless quality. This property, together with suitable form characteristics, has won for the lump char produced by certain processes important places in the domestic fuel market in Great Britain and in other European countries. The second product, also of major importance, has been the large volume of tar. During 1920s there was a common expectation that the values of these products, especially the chemicals to be derived from the tar, plus possible economies in the carbonisation processes as compared to high-temperature coke ovens, would lead to attractive profits from a low temperature plant. Engineers and inventors have proposed a great amount of work and innumerable designs. Of all the processes worked on during that period, only one-the present Disco process - survived. There are five necessary conditions to be met if a low-temperature carbonisation process is to be rendered technically and economically feasible: 1) Universal applicability to different types of high-volatile coals 2) Production of a firm, abrasion –resistant product iii 3) Maintenance of desirable temperature conditions through the system to produce a uniform tar 4) Maintenance of an output which is economically attractive, a condition dependent on rabidity of heat transfer and involving oven design and the thickness of the coal bed 5) Smooth, trouble-free oven operation The two processes in regular commercial use are the Disco process of the Consolidation Coal company, this plant being located near Pittsburgh, Pennsylvania, and the stoker carbonisation process, operated by Shawinigan Chemicals Ltd. in Canada. In addition to these plants, the Parry process has been operated experimentally on lignite by the Texas Power and Light Company at the power installation for the Aluminum Company of America at Rockdale, Texas. The Lurgi-Spulgas process also has operated in North Dakota for some time on the local lignite. A process for producing a metallurgical formed coke from Wyoming subbituminous coal was announced, and production of a low-temperature char is one of the first steps. This plant is operated by Food Machinery and Chemical Company and the United States Steel Corporation at Kemmerer, Wyoming. In Europe, Japan, and other parts of the world, the Kruoo-Lurgi, Lurgi-spulgas and Rochdale gas re-circulation appear to be most widely in use, but work is proceeding at a number of locations on smaller-scale units of other carbonisation methods. Although many processes have been realised, they have been operated on different coals, in different ways, and for widely different objectives. Little correlation between them is available. Each process has often functioned on pretty much an experimental scale, without reaching the more critical stage of successful commercial practice. The engineer entering the low-temperature field finds it almost a virgin one, which encompasses first the selection of a process for a given need, then the design and engineering with the identification and definition of the problems to be faced, and finally plant operation and meeting the unexpected developments. For these reasons commercial evaluations of processes are still very difficult iv Low temperature chars differ markedly from high-temperature cokes in appearance and properties. Generally, pieces of low temperature chars are black to dull grey, with an open, porous structure. They are softer, more friable, and weigh less than high-temperature coke. Both the apparent and true densities are lower. The volatile content of the char usually lies in the range from about 20% down to 9 or 10%. When heated, a char gives off much hydrogen, and the gas burns with an almost non-luminous flame. Because of the high volatile content and the open structure, char ignites readily and burns freely. These qualities make a lump char an ideal fuel for the open domestic grade. The quality of a charcoal can be represented by a great many other properties including charcoal yield, fixed-carbon content, moisture content, calorific value, elemental composition, hardness (abrasion resistance), compressive strength, bulk and true densities, surface area, porosity and pore volume distribution, electrical resistivity, and reactivity. The high reactivity of chars necessitates their thorough quenching or cooling unless they are to be used very shortly. In general, the properties of chars are greatly affected by the coals from which they have been produced and by the conditions to which they have been exposed during carbonisation. Commercial utilisation of low temperature chars includes domestic or industrial fuel, blast furnace fuel, reducing agent, electrodes and other uses. Product distribution and how it is influenced by coal pyrolysis conditions have been studied. Lignite and bituminous coal are exhibiting quite different behaviour. Lignite products up to 700K are mainly water. Subsequently the evolution of CO 2 and tar starts. At slightly higher temperatures CO, hydrocarbons and H 2 are observed due to defunctionalisation. The hydrocarbons mainly consist of methane and ethylene. Based on char and gaseous products analyses, it is clear that the lignite char becomes relatively enriched in C, since even at the highest temperature only about 20% of the original carbon is lost. In the case of bituminous coal product distribution is dominated by tar. H 2O is formed at relatively low temperature, below 700K. Carbon content profile is fundamentally different than that of lignite and it continuously decreases over the whole temperature range. Up to 50% of the originally present carbon is volatilised eventually. The hydrogen profile shows an analogous pattern that is in good agreement with the predominant evolution of tar. Apart from coal type, v pyrolysis conditions that affect product distribution are the temperature, retention time, heating rate, pressure and particle size distribution. Economic and market prospects of LTC technologies are quite promising, since such fuel pre-reatment technology fits into the European, North American and global market developments, fulfils technical and cost efficiency demands, and meets International Protocols and Agreements. Among key-points of LTC development is the market tendency for expansion of small- and medium-sized power generation plants. Traditional plants can easily be retrofitted by LTC add-on module, whereas old plants can cost efficiently upgraded and still meet the new environmental norms and regulations. Potential LTC project development offers economical benefits, such as decreased total cost of the end-product Clean Coal, environmental control cost savings, increased profits due to efficiency improvement, and reduced raw material cost, since domestic renewable sources and agricultural wastes utilisation is feasible. Major technical and scientific benefits of LTC technologies employment include (a) preventive environmental protection, (b) improved boiler efficiency, (c) total cost savings that may exceed 10%, (d) reuse of industrial residuals, since flexible multi fuel operation is possible, (e) enhancement of fuel diversity and security, (f) elimination of environmental and health care risks, and (g) reduced boiler corrosion, resulting in maintenance cost savings. One of the major LTC advantages is fuel availability, since it offers potential utilisation of alternative biomass and food industry wastes, whose disposal may present today high cost and technical deficiency, such as (a) waste vegetable oils (co-combustion), (b) non usable – non recyclable residuals from bio-diesel production, (c) biomass residues, such as straw pellets and husk, (d) energy crops, such as short rotation wood and sawdust, (e) biomass waste, i.e. demolition wood, and (f) meat meals from animal by-product processing industry. Among known limitations that LTC technologies present are (a) reduced efficiency
Details
-
File Typepdf
-
Upload Time-
-
Content LanguagesEnglish
-
Upload UserAnonymous/Not logged-in
-
File Pages165 Page
-
File Size-