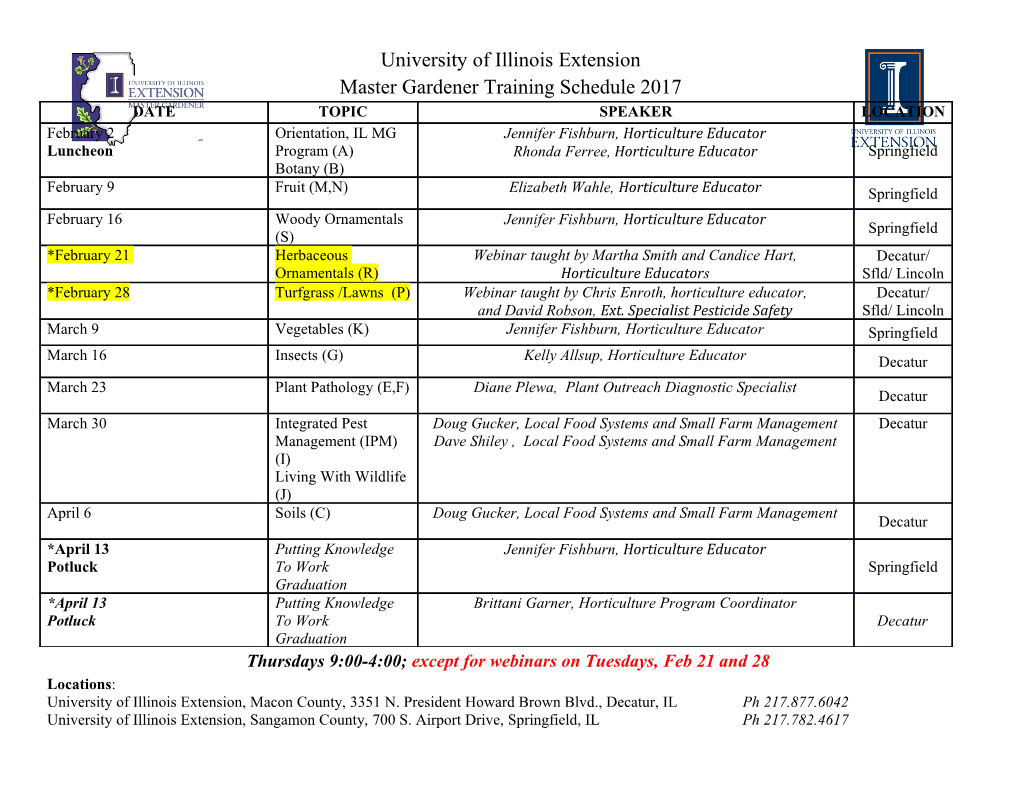
I I NASA TECHNICAL NOTE NASA TN D-6839 l 0- Cr) 00 9 d z c 4 C r/r 4 z EXPERIMENTAL EVALUATION OF A TF3O-P-3 TURBOFAN ENGINE IN AN ALTITUDE FACILITY: AFTERBURNER PERFORMANCE AND ENGINE-AFTERBURNER OPERATING LIMITS by John E, McAulay and Muhmood Abdelwuhub Lewis Reseurch Center Clecelmd, Ohio 44135 NATIONAL AERONAUTICS AND SPACE ADMINISTRATION WASHINGTON, D. C. JULY 1972 EXPERIMENTAL EVALUATION OF A TF30-P-3 TURBOFAN ENGINE IN AN ALTITUDE FACILITY: AFTERBURNER PERFORMANCE AND EN GI NE-AFTER BURNER 0 PER AT1 NG LIMITS by John E. McAulay and Mahmood Abdelwahab Lewis Research Center SUMMARY An investigation was conducted to determine the afterburning steady- state perform- ance and operational limits of a TF30-P-3 turbofan engine. Steady-state performance of the afterburner was obtained over a range of engine-inlet pressures with distortion- free inlet flow. Engine-afterburner altitude operational limits were obtained over a t range of engine-inlet distortions during fixed and transient throttle operation. In addi- tion, a limited amount of data was obtained to determine the engine-afterburner limits during time-variant engine-inlet pressure oscillations. At the Maximum throttle position (full afterburning) the afterburner combustion efficiency and total-pressure-loss ratio were 0.91 and 0.11, respectively, at an engine- inlet Reynolds number index of 0.80. The combustion efficiency decreased to 0.68 at Maximum throttle position and a Reynolds number index of 0.25. During throttle bursts and chops between Military and Maximum throttle position, fan-compressor stalls were encountered. Time histories of pressures in the fan-compressor showed development of rotating stall in the fan hub which quickly propagated and produced complete stali in the high-pressure compressor. The altitude stall limits were substantially reduced as distortion level was increased during either fixed or transient throttle operation. For fixed throttle operation, changing the throttle position from Military to Maximum and closing the compressor bleeds also reduced the altitude stall limits. When time-variant engine-inlet pressure oscillations were imposed, full-face oscillations required the highest amplitude to produce stall. For the other modes of engine-inlet pressure oscil- lation, the co-rotating distortion caused stall with the lewest arr.plitude and the lowest instantaneous distortion. INTRODUCTION With the progressive development of supersonic aircraft, the demands on the engine and its inlet have increased. These demands or requirements are brought about by the desire for greater maneuverability and for operation at higher flight altitudes and Mach numbers. Greater maneuverability and higher flight numbers impose increasing levels of steady-state and time-variant inlet flow distortions. Higher altitudes produce lower engine-inlet Reynolds numbers. Both the increased level of flow distortions and the de- creased Reynolds numbers result in lower fan- compressor stability margins. Further- more, the lower operating pressures brought about by increased altitude can produce substantial degradation in afterburner combustion efficiency and stability. ’ In an effort to quantitatively show the effects of engine-inlet pressure level (i.e. , altitude) and flow distortions on a modern operational afterburning turbofan engine, a co&prehensive program was conducted at NASA Lewis Research Center on the TF30-P-1 and P-3 engines. Results of previously reported nonafterburning tests are given in references 1 to 6. As a part of this overall program, further tests were conducted with the TF30-P-3 engine operating in the afterburning regime. These tests were planned to measure the effect of pressure level, or altitude, on the afterburning steady-state performance and to determine the effect of steady-state and time-variant inlet flow dis- tortions on the engine-afterburner operational limits. This report presents the results of these tests in the afterburning regime. The afterburner steady-state performance is presented as a function of operating pressure level and fuel-air ratio. Engine afterburner operational limits are shown on coordinates of altitude and distortion level for fixed and transient throttle operation. A limited amount of data is presented at fixed throttle settings to show the effect of several kinds of time-variant engine-inlet flow distortions on engine-afterburner operating limits. APPARATUS Engine The engine used for this investigation was a production TF30-P-3 twin-spool turbo- fan engine equipped with an afterburner. The engine, shown schematically in figure 1, includes a three-stage axial-flow fan mounted on the same shaft with a six-stage axial- flow low-pressure compressor. This unit is driven by a three-stage low-pressure turbine. A seven-stage, axial-flow compressor driven by a single-stage, air-cooled turbine makes up the high-pressure spool. The overall pressure ratio of the fan- 2 compressor system is 17, the fan pressure ratio is 2.1, and the bypass ratio is 1.0 at sea-level static Military operating condition. The compressor is equipped with seventh- stage (low compressor) and 12th- stage (high compressor) bleeds. The seventh-stage bleeds are manually operated and are normally opened at flight Mach numbers above 1.5. The 12th-stage bleeds are normally operated automatically so that they are open at low engine speeds and pressure ratios and closed at the higher speeds and pressure ratios. For this investigation, the 12th- stage bleeds were also manually controlled. An ejector nozzle having aerodynamically operated blow-in doors and exit leaves is a part of the normal engine-afterburner assembly. For this investigation, the blow-in doors and exit leaves were removed. Afterburner The afterburner consists of a diffuser duct, a combustion chamber, a flameholder, and seven fuel spray rings. A cross-sectional schematic of the afterburner showing the location of instrumentation is presented in figure 2. The flameholder and spray ring assembly is shown pictorially in figure 3. The diffuser duct consists of two diffuser sections separated by a splitter cone. Fan air and gas generator gases flow through the outer and inner diffuser ducts, respectively. The combustion section is made up of an outer shell and an inner liner which is perforated at its front and louvered at its aft end. The distance from the forward end of the diffuser section to the aft end of the liner is 257 centimeters. The flameholder is a three-ring V-gutter type. Two of these rings are attached directly to the aft end of the diffuser cone, while the third ring is attached further upstream to the diffuser cone by a rod assembly. The projected blockage of the flameholder is approximately 33 percent of the maximum combustion section area. This blockage is not concentrated at a single axial location. Scheduling of the afterburner fuel flow and the exhaust nozzle area is accomplished by an integrated afterburner - exhaust nozzle control. This control operates in con- junction with the main engine conditions. The afterburner fuel is introduced into the . combustion chamber through the spray rings, which are arranged into five separate zones. Zones 2, 3, and 4 each consist of a fuel line, a manifold, feed tubes, and one spray ring. Fuel fed through these zones mixes with the fan airflow. Zone 5 is similar except that it contains two spray rings. Zone 1 fuel system consists of a fuel flow di- vider mounted directly on the afterburner fuel control, two fuel lines leading from the flow divider, two fuel manifolds, three feed tubes, and two spray rings. These two paths of zone 1 fuel flow are designated as zone 1 primary and zone 1 secondary. Zone 1 primary is always used when afterburner fuel is flowing. Fuel is introduced 3 through the zone 1 secondary system only at a main burner pressure level above 124 N/cm 2 abs. Fuel introduced through zones 1 and 5 mixes with the gas generator flow. As afterburner fuel flow is increased, fuel is introduced into gas generator and fan flow successively through zones 1 to 5. Each successive zone fuel flow is additive to the preceding zone flows. The afterburner nozzle consists of 12 equally spaced segments hinged to the after- burner combustion chamber aft end. These nozzle segments are actuated by six hy- draulic cylinders which use fuel as the working fluid. The movement of these segments produces a c>ange in nozzle area. Distortion Devices * Engine-inlet spatial total-pressure distortions were produced either by the air jet system or by screens located upstream of the engine inlet. The air jet system was also used to obtain time-variant pressure osciallations at the engine inlet. The screen con- figurations used during this investigation are shown in figure 4(a). Configurations 1 and 2, which produce the same distortion pattern but are slightly different in magnitude, were designed to reproduce a distortion encountered with the F-111 airplane. The air jet system, which is described in detail in reference 2, is illustrated schematically in figure 4(b). Its primary components are a torus manifold and associated piping, six servo-operated air jet valves of special design (one for each 60' segment) and 54 lines. Each valve supplies high-pressure air to nine lines and in turn to nine jet nozzles located in the engine-inlet duct. The jet nozzles direct the high-pressure air counter to the primary flow from the bellmouth. The high-response servo-operated air jet valves were capable of operating over a range of amplitudes to frequencies of 200 hertz. Ins tal Iat ion ,-The engine with afterburner and the air jet system are shown installed in the alti- tude test chamber in figure 5. The air jet system was not installed during the steady- state afterburner performance tests. The installation was a conventional direct- connect type. The engine was mounted on a thrust-measuring stand which consisted of a test bed suspended from facility supports by four flexure plates.
Details
-
File Typepdf
-
Upload Time-
-
Content LanguagesEnglish
-
Upload UserAnonymous/Not logged-in
-
File Pages36 Page
-
File Size-