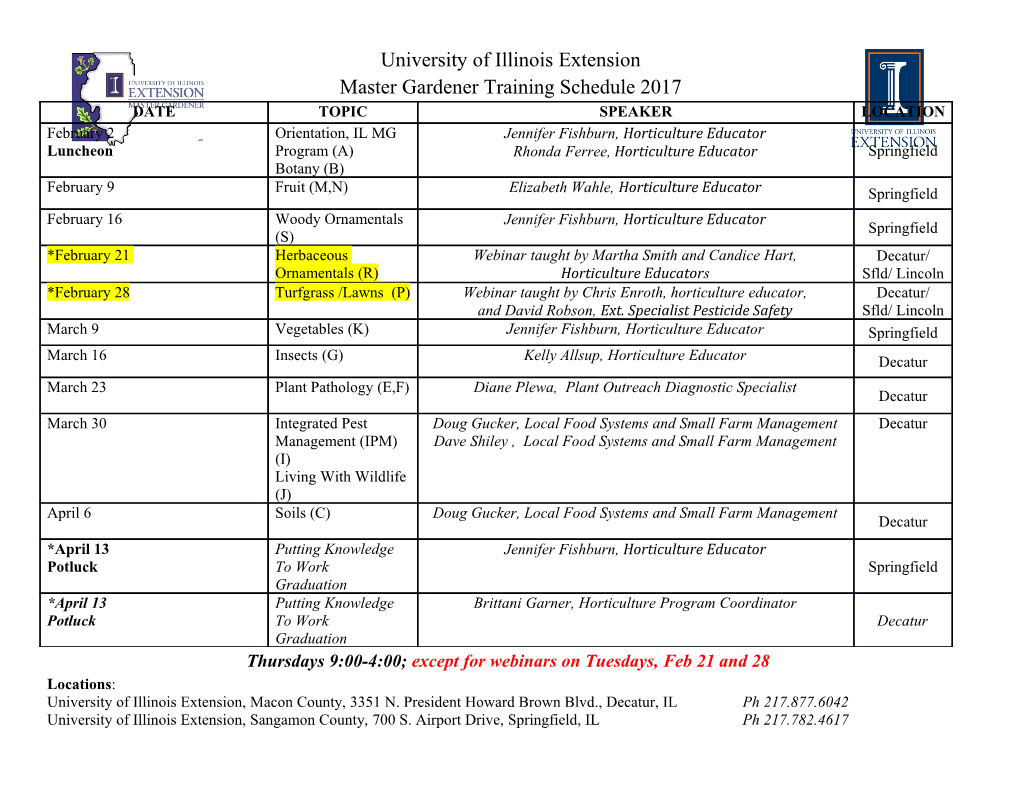
https://ntrs.nasa.gov/search.jsp?R=19680010320 2020-03-12T08:49:02+00:00Z General Disclaimer One or more of the Following Statements may affect this Document This document has been reproduced from the best copy furnished by the organizational source. It is being released in the interest of making available as much information as possible. This document may contain data, which exceeds the sheet parameters. It was furnished in this condition by the organizational source and is the best copy available. This document may contain tone-on-tone or color graphs, charts and/or pictures, which have been reproduced in black and white. This document is paginated as submitted by the original source. Portions of this document are not fully legible due to the historical nature of some of the material. However, it is the best reproduction available from the original submission. Produced by the NASA Center for Aerospace Information (CASI) #a Ae 4009 74 14^^ final Report for ADVANCED TECHNOLOGICAL SATELLITE ELECTRO-MECHANICAL DESPUN ANTENNA GPO PRICE $ CSFTI PRICE(S) S Hard copy (HQ,` Contract No: NAS 5.9521 Microfiche (MF) N 653 July 65 Prepared by Sylvania Electronic Systems Eastern Division Sylvania Electronic Systems An Operating Group of Sylvania Electric Products, Inc. for National Aeronautics and Space Administration Goddard Space Flight Center B 91©7 Greenbelt, Maryland APR g a N68-19789 ti I 66 9s ( (MRW REGE ( _ ^^^ NASpST1 RAtic,^Y g 1tdPU^ $ 0 (R CR TMX OR AD NUMBER) (CA RY) 7{± ^l^9ZSZ^Z^ZZ^^'L Final Report for ADVANCED TECHNOLOGICAL SATELLITE ELECTRO-MECHANICAL DESPUN ANTENNA 19 October 1967 F181-1 Contract No. NAS 5-9521 Prepared By SYLVANIA ELECTRONIC SYSTEMS EASTERN DIVISION SYLVANIA ELECTRONIC SYSTEMS An Operating Group of Sylvania Electric Products, Inc. 100 First Avenue, Waltham, Mass. 02154 Prepared by: ^^ Approved by: L . Blaisdell Rubin Project ManagerEquipment Engineering Laboratory Manager Approved by: r. B. K. a son Senior Scientist Sylvania Electronic Systems for NATIONAL AERONAUTICS AND SPACE ADMINISTRATION GODDARD SPACE FLIGHT CENTER Greenbelt, Maryland TABLE OF CONTENTS Section Page LIST OF ILLUSTRATIONS vi LIST OF TABLES viii 1 INTRODUCTION 1-1 2 SUMMARY 2-1 3 DESIGN REQUIREMENTS 3-1 3.1 RF Subsystem 3-1 3.2 Control Subsystem 3-2 3.3 Environmental and Mechanical Requirements 3-2 4 TECHNICAL DISCUSSION 4-1 4.1 RF Subsystem 4-1 4.1.1 Introduction 4-1 4.1.2 Final Design Description 4-1 4.1.2.1 General 4-1 4. 1.2.2 RF Feed Assembly 4-3 4. 1.2.3 Reflector Assembly 4-5 4.1.3 RF Development Program 4-5 4.1.3.1 Pattern Optimization 4-11 4.1.3.2 Impedance Matching 4-12 4.1.4 Final Performance Summary 4-14 4. 1.4.1 Patterns 4-14 4.1.4.2 Impedance 4-21 4. 1.5 Power Breakdown Considerations 4-21 4.2 Control Electronics 4-24 4.2.1 Mark H Control System 4-25 4.2.1. 1 Over-all System Block Diagram 4-25 4.2.1.2 Mark 11 Control Electronics Block Diagram 4-27 4.2.1.3 The MAR I Control System 4-59 F181-1 ii TABLE OF CONTENTS (Cont.) Section Page 4.3 Control Electronics Packaging 4-62 4.3.1 Introduction 4-62 4.3.2 Despun Antenna Module 4-62 4.3.3 The Mark II System 4-70 4.4 Mechanical Drive Assembly 4-74 4.4.1 Strurture 4-74 4.4.2 Bearings 4-75 4.4.3 RF Structures 4-75 4.4.4 Ejection Mechanism 4-76 4.4.5 Weight Summary 4-77 4.4.5.1 Increased Weight 4-78 4.4.5.2 Increased Vibration Requirement 4-78 4.4.5.3 Increased Bearing Preload 4-80 4.5 Bearings and Lubrication System 4-84 4.5.1 Introduction 4-84 4.5.2 Lubricants - General Considerations 4-85 4.5.3 Effect of Environment 4-86 4.5.4 Bearings 4-87 4.5.4.1 Bearing Life Calculation 4-89 4.5.5 Lubrication System 4-92 4.5.6 Proof of Design Test Program Description 4-96 4.5.6.1 5000 Hour Qualification Test 4-97 4.5.6.2 Lubricant Evaporation Rate Test 4-98 4.5.6.3 Test Plan 4-100 4.5.6.4 Test Equipment 4-104 4.5.6.5 Test Results 4-107 4.5.6.6 Conclusions 4-109 F181-1 iii TABLE OF CONTENTS (Cont.) Section Page 4.5.7 Bearing Analysis Results 4-110 4.5.7.1 Discussions 4-110 4.5.7.2 Conclusion 4-112 4.5.7.3 List of Bearing Analysis Figures 4-112 4.6 Reliability 4-117 4.6.1 Introduction 4-117 4.6.2 Analysis and Prediction Summary 4-117 4.6.3 Component Failure Rates 4-118 4.6.3.1 Integrated Circuits-SUHL 4-118 4.6.3.2 Other Electronic Parts 4-120 4.6.4 Redundancy Techniques 4-121 4.6.5 Reliability Analysis 4-123 4.6.5.1 Quaded Motor Driver (00-469046) 4-123 4.6.5.2 DC-DC Converter 4-124 4.6.5.3 Data Telemetry 4-124 4.6.6 Motor Bearing Lubrication System Reliability 4-125 4.6.6.1 Avco-RAD Reliability Assessment Method (1) 4-126 4.6.6.2 RCA-Montreal Reliability Assessment of Mechanical and Elec tro- Mechanical Parts (2) 4-127 4.6.6.3 Discussion of Significance of Both Methods of Reliability Calculation 4-130 4.6.7 Malfunction Reporting, Analysis and Corrective Action 4-131 4.6.8 Reliability Testing 4-132 4.7 Test Programs 4-132 4.7. 1 Qualification Test Program 4-132 4.7.2 Flight Acceptance Test Program 4-136 4.7.2. 1 Flight Unit Acceptance Test 4-136 4.7.2.2 Spare Flight Unit Acceptance Test 4-137 4.7.3 Spacecraft Vibration Test 4-138 F181-1 iv TABLE OF CONTENTS (Cont.) Appendix Page A RF PATTERN TEST DATA A-1 B RF IMPEDANCE TEST DATA B-1 C CONTROL ELECTRONICS DATA - SYSTEM POWER DRAIN C-1 D VIBRATION TEST REPORTS D-1 E ATS-MDA: SPACECRAFT VIBRATION TEST E-1 F ATS DESPUN ANTENNA (MARK IIk EMI TEST REPORT F-1 G ANALYSIS OF THERMAL ENERGY EXCHANGE BETWEEN THE MECHANICALLY DESPUN ANTENNA AND THE SPACECRAFT G-1 F181-1 v LET OF ILLUSTRATIONS Figure Page 1-1 ATS Mechanical Despun Antenna 1-2 1-2 Artist's Concept of Antenna Mounted on Spacecraft 1-3 4-1 Artist's Concept of Despun Antenna 4-2 4-2 RF Feed Assembly, Cross-Section Drawing 4-4 4-3 Dielectric Support Gap Feed 4-7 4-4 Variations of the Post Feed 4-8 4-5 Current Distribution Diagrams 4-9 4-6 T-Feed Configuration 4-10 4-7 4 GHz Azimuth Pattei n 4-15 4-8 4 GHz Elevation Pattern 4-16 4-9 6 GHz Azimuth Pattern 4-17 4-10 6 GHz Elevation Pattern 4-18 4-11 Azimuth Sidelobe Analysis 4-20 4-12 Final Impedance Plot-Transmit Band 4-22 4-13 Final Impedance Plot-Receive Band 4-23 4-14 Over-all System Block Diagram 4-26 4-15 Mark H Control System Block Diagram 4-28 4-16 Rotor and Stator 4-31 4-17 Encoder Electronics, Schematic Diagram 4-33 4-18 Damper Circuit, Schematic Diagram 4-36 4-19 Damper Waveforms 4-38 4-20 Waveform Generator, Logic Diagram 4-41 4-21 Waveform Generator, Tuning Diagram 4-42 4-22 Quaded Motor Driver, Schematic Diagram 4-43 4-23 Binary Counter 4-45 4-24 Motor Starting Circuit, Block Diagram 4-47 4-25 Motor Starting Circuit, Schematic Diagram 4-48 4-26 DC-DC Converter, Schematic Diagram 4-50 4-27 Telemetry Interfaces Circuit, Schematic 4-52 F181-1 vi LIST OF ILLUSTRATIONS (Cont.) Figure Page_ 4-28 Command Interface Circuit No. 1, Schematic Diagram 4-53 4-29 Command Interface Circuit No. 2, Schematic Diagram 4-54 4-30 Directional Command, Logic Diagram 4-55 4-31 Directional Command, Schematic Diagram 4-56 4-32 Pulse Selection Circuit 4-57 4-33 Basic Control System Block Diagram 4-60 4-34 Despun Antenna Module 4-64 4-35 Stack and Header Assembly 4-66 4-36 Wiring Diagram for Typical Module 4-67 4-37 Close-up View of Weld Performance on Stack 4-68 4-38 Typical Assembly of Modules in Mechanical Despun Antenna System 4-69 4-39 Packaging of Control Electronics 4-71 4-40 Modules Assembled on Two-Sided Printed Circuit Board 4-72 4-41 Bearing Lubrication System for Mechanical Despun Antenna 4-93 4-42 Lubricant Loss, Weight Versus Time 4-99 4-43 Lubricant Loss, Loss Rate Versus Temperature 4-99 4-44 Motor Mount in Vacuum System, Schematic Drawing 4-101 4-45 Vacuum System Layout, Schematic Drawing 4-105 4-46 Motor Mounted to Top Cover of Vacuum Test Chamber 4-106 4-47 Photomicrographs of Test Bearing After 7800 Hours of Operation, 7X and 25X Magnification 4-113 4 -48 Photomicrographs of Test Bearing After 7800 Hours of Operation, 20OX and 40OX Magnification 4-114 4-49 Test Bearing Inner Race 4-115 4-50 Profile Trace of Test Bearing Inner Race After 7800 Hours of Operation 4-116 4-51 Profile Trace of Bearing After 50-Hour Run-in 4-116 4-52 Mark II Control System Reliability Model Block Diagram 4-119 F181-1 vii LIST OF TABLES Table Page 4-1 Weight Summary 4-?9 4-Z ATS Mechanically Despun Antenna - Mark II System Failure Rate, x, and Probabilities of Success, R 4-118 4-3 Malfunction Reports 4-133 F181-1 viii SECTION 1 INTRODUCTION Sylvania was contracted by NASA/GSFC under contract number NA96-9521 to design, fabricate and test five microwave-frequency mechanical despan antenna systems consisting of an RF subsystem, a control electronics subsystem, and a mechanics 1 drive subsystem.
Details
-
File Typepdf
-
Upload Time-
-
Content LanguagesEnglish
-
Upload UserAnonymous/Not logged-in
-
File Pages155 Page
-
File Size-