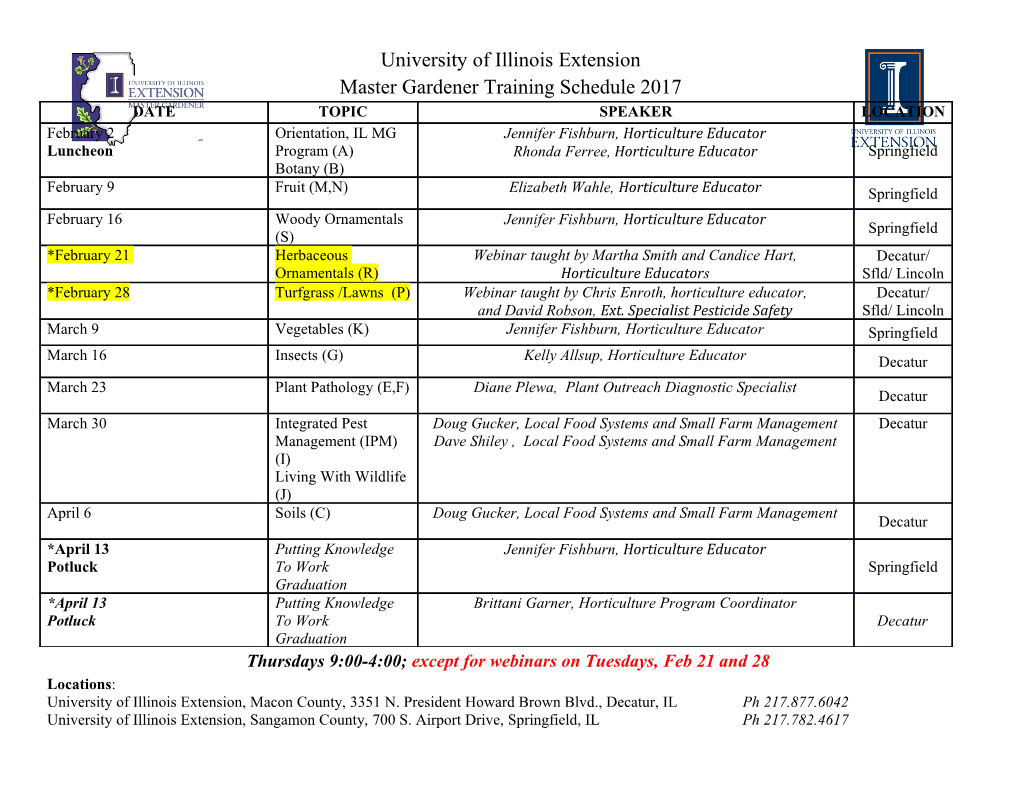
Accelerated Gas-liquid Visible Light Photoredox Catalysis with Continuous-Flow Photochemical Microreactors Natan J. W. Straathof,a,† Yuanhai Su, a,† Volker Hessel, a Timothy Noëla,b* a Eindhoven University of Technology, Department of Chemical Engineering and Chemistry, Micro Flow Chemistry & Process Technology, Building 14 (Helix), De Rondom 70, 5612 AP Eindhoven, The Netherlands. b Department of Organic Chemistry, Ghent University, Krijgslaan 281 (S4), 9000 Ghent, Belgium. † Authors contributed equally to this work. Correspondence should be addressed to T.N. ([email protected]) Abstract In this protocol, a detailed description for the construction and application of an operationally simple photochemical microreactor for visible light gas-liquid photoredox catalysis is presented. The general procedure includes details of an appropriate photochemical setup and representative procedures for the continuous- flow preparation of trifluoromethylated heterocycles and thiols, and disulfides via generation of singlet oxygen. The reported photomicroreactors are modular, inexpensive and can be prepared rapidly from commercially available parts within one hour even by non-specialists. Interestingly, typical reaction times of gas-liquid visible light photocatalytic reactions can be reduced from the hour range in batch to the minute range in microflow. This can be attributed to the improved irradiation efficiency of the reaction mixture and the enhanced gas-liquid mass transfer in the segmented gas-liquid flow regime. 1 Keywords: Photoredox Catalysis, Continuous Flow, Microreactor, Trifluoromethylation, Photocatalytic Oxidation. 2 Introduction Recently, visible light photoredox catalysis has emerged as a new and innovative approach to enable small molecule activation. This activation mode relies on the use of organometallic complexes1 or organic dyes2,3 to absorb photons and to, subsequently, engage in single electron or energy transfer processes with organic substrates (Figure 1). Due to the generally mild reaction conditions and the use of low energy visible light as an abundant and perennial energy source, photoredox catalysis has received an increasing amount of attention and allows for unprecedented reaction pathways in high yield and selectivity. Figure | 1. Representative photocatalysts used in visible light photoredox catalysis. However, some inherent limitations are associated with the use of conventional batch reactors to enable photochemical transformations. One limitation is derived from the attenuation effect of photon transport, which prevents scale up of photochemistry in batch reactors (Lambert-Beer law). Herein, photons are completely absorbed in the outer rim of the reactor, while the center of the reactor receives no light. Consequently, scaling of photochemistry cannot be achieved by simply increasing the dimensions of the reactor design.4-5 Another limitation is the use of gaseous reactants in conjunction with batch reactors, which result in poorly defined interfacial contact areas between the gas and the liquid phase. Due to the 3 difficult handling of gases in batch, such reactants are often avoided by synthetic chemists in research laboratories. In the last decade, the use of continuous-flow microreactors for both photochemical and gas-liquid reactions has gained considerable amounts of attention as it allows for a high degree of control over various reaction parameters6-7. Due to the small dimensions of microreactors, a homogeneous irradiation of the entire reaction medium can be achieved which allows for shorter reaction/residence times, higher reaction selectivity and lower catalyst loadings8-9. Moreover, carrying out gas-liquid reactions in microreactors results in a segmented flow regime (Taylor flow) providing enhanced mixing, increased radial mass transfer and minimal axial dispersion10-13. Here, we report a detailed protocol for the construction and application of a gas- liquid photochemical microreactor starting from commercially available parts. The reactor assembly is next demonstrated in the photocatalytic trifluoromethylation of 14-15 16 heterocycles and thiols using cheap CF3I gas, and in the photocatalytic aerobic oxidation of thiols to prepare disulfides using oxygen gas (Figure 2)17-18. The protocols provide a safe, reproducible and scalable alternative for the traditional batch scale methods. Figure 2 | Overview of the compounds prepared with the photomicroreactor setup. Typical aerobic oxidation conditions (compounds 1-A and 2-A): Thiol, TMEDA (2 equiv.), Eosin Y (5 mol%), Ethanol, 4 Oxygen, White LED. Typical trifluoromethylation conditions (compounds 3-B–6-B): Heterocycle or thiol, TEA or TMEDA (2 equiv.), Ru(bpy)3Cl2.6H2O (1 mol%), CF3I (1.2 equiv.), MeCN, Blue LED. Overview of this protocol We describe the construction of a compact photomicroreactor which is broadly applicable in wide variety of visible light photocatalytic reactions. The design is compact and simple but, nevertheless, highly innovative as it obeys to fundamental chemical and engineering principles. In this protocol, we have specifically focused on gas-liquid photocatalytic reactions since such reaction conditions pose particular technological challenges to synthetic chemistry. However, the design delineated in this protocol is highly modular allowing it to serve as a benchmark example for other photochemical applications. With minor changes, it can easily be extended to other photocatalytic or photochemical protocols, e.g. homogeneous photocatalysis or UV mediated photochemistry19-20. While excellent commercial systems do exist, our protocol allows researchers to rapidly implement the technology in their laboratories as it is simple to assemble, inexpensive in construction and flexible in design, which allows to tailor the reactor to specific requirements. In addition, variation of reaction conditions and parameters (reaction times, gas and liquid flow rates, reagent and catalyst loadings, etc.) can be rapidly achieved without reengineering the design. In Figure 3, a schematic overview is given of the gas-liquid photomicroreactor setup. The microreactor is constructed using high purity perfluoroalkoxyalkane (PFA) capillary tubing (0.75 mm ID, 1/16” OD, 1.1 mL volume) and is coiled around a disposable plastic syringe coated with refractive aluminum tape. An array of light- 5 emitting diodes is wrapped around the reactor and the whole assembly is fixated in a larger diameter disposable plastic syringe. The gas flow rate is monitored and controlled by a mass flow controller (MFC). The liquid flow rate is controlled by syringe pumps. All reactants are mixed in a cross micromixer and the segmented gas-liquid flow is introduced in the photomicroreactor. The reaction can be diluted or quenched upon exiting the photomicroreactor, allowing to control precisely the reaction times. Figure 3 | Schematic overview of a typical continuous-flow photomicroreactor setup for gas-liquid photocatalytic transformations, containing (i) Gas supply and pressure regulator (e.g. trifluoroiodomethane gas or oxygen gas); (ii) Mass flow controller (MFC) assembly to regulate the gas flow (mL min-1); (iii) Mixing zone before entering the photomicroreactor using a cross micromixer; (iv) Photomicroreactor – an assembly of a coiled PFA capillary microreactor with a LED array as light source; (v) Reaction quenching zone. 6 MATERIALS Reagents <Caution> All chemicals should be handled carefully and with proper personal protection (lab coat, chemical resistant gloves and safety goggles). All procedures should take place inside a fume hood; special care should be taken when handling volatile compounds/reagents. Solid and liquid chemical waste products should be disposed of appropriately, as defined by the local and institutional regulations. Solvents used for the preparation of the compounds are purchased in anhydrous form and used as received. Anhydrous solvents are handled using standard Schlenk techniques, hereby replacing the liquid volume by inert gas (argon). Solvents used for the purification of the compounds are of reagent quality and do not need to be anhydrous. <Caution> Extreme care should be taken when handling gaseous reagents such as trifluoroiodomethane or oxygen gas. As these gases are colourless and odourless, extra care should be taken to check for possible gas leaks during and after constructing the reaction setup. Acetonitrile (Sigma-Aldrich, cat. no. 271004). Ethanol (VWR International, cat. no. 20816.367) <Caution> Ethanol is volatile and flammable. Ethyl acetate (Biosolve, cat. no. 05400502) <Caution> Ethyl acetate is volatile and flammable. Petroleum Ether (PE, Biosolve, cat. no. 17150202) <Caution> PE is volatile and extremely flammable. 7 Acetone (Sigma-Aldrich, cat. no. 34850) <Caution> Acetone is volatile and flammable. Thiophenol (Sigma-Aldrich, cat. No. 240249) <Caution> Thiophenol is a volatile and extremely smelly compound. Handle with care and inside the fume hood. 4-acetamidothiophenol (Sigma-Aldrich, cat. no. A8201) 4-mercaptotoluene (Sigma-Aldrich, cat no. T28525) 2-furanmethanethiol (Sigma-Aldrich, cat. no. F20408) <Caution> 2- Furanmethanethiol is a volatile and a smelly compound. Ethyl 1H-pyrrole-2-carboxylate (Sigma-Aldrich, cat. no. CDS000975) 5-Methoxyindole (Sigma-Aldrich, cat. no. M14900) α,α,α-trifluorotoluene (Sigma-Aldrich, cat. no. 547948) <Caution> α,α,α- trifluorotoluene is a volatile compound. N,N,N’,N’-tetramethylethane-1,2-diamine (Sigma-Aldrich, cat. no. T22500) <Caution> N,N,N’,N’-tetramethylethane-1,2-diamine
Details
-
File Typepdf
-
Upload Time-
-
Content LanguagesEnglish
-
Upload UserAnonymous/Not logged-in
-
File Pages40 Page
-
File Size-