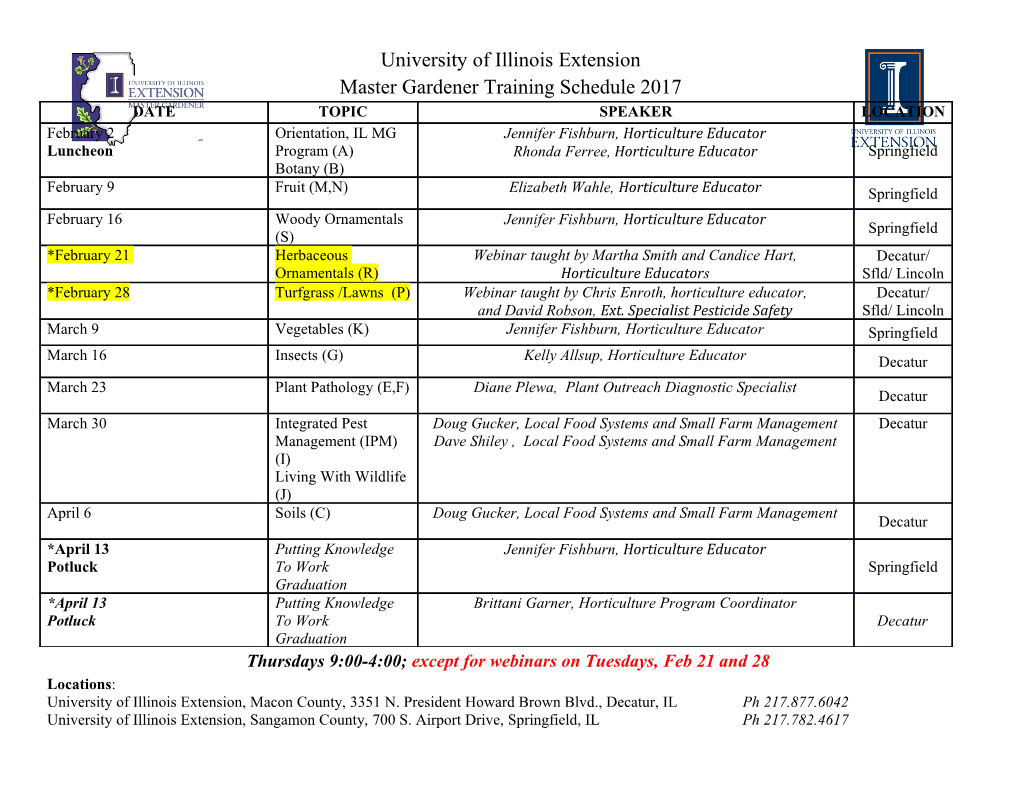
Mechanical Properties • A material’s behavior when subjected to 3. Mechanical Properties of mechanical stresses (load) Materials – Properties include elastic modulus, ductility, hardness, and various measures of strength 3.1 Stress-Strain Relationships • Mechanical properties desirable to the 3.2 Hardness designer, such as high strength, usually make 3.3 Effect of Temperature on Properties manufacturing more difficult 3.4 Fluid Properties • Integration of design and manufacturing 3.5 Viscoelastic Properties • Tension, Compression and Shear tests 1 2 3.1 Stress-Strain Relationships Tensile Test Plastic • Tensile Properties P Deformation Fracture – Elastic modulus Elastic Elongation (EL) =(Lf-Lo)/Lo – ductility Area Reduction (AR) =(Ao-Af)/Ao – hardness Gauge necking – various measures of strength Length • Proportional limit • Elastic limit • Yield strength • Offset yield strength F P • Ultimate Tensile strength, TS = max Measuring Force; Transducer A ASTM standards • Failure Strength o Measuring Displacement; extensometer, strain gauge 3 4 Stress and Strain Diagram Flow Curve • The straight line in a log-log plot shows the F δ • Engineering Stress & Strain σ = , e = relationship between true stress and true e A L strain in the plastic region as – Original Area, Ao o o F L n • True Stress and Strain σ = , ε = ln 0 σ = Kε – Instantaneous Current Area, A A L where K = strength coefficient; and n = strain hardening exponent Slope=E S • strain hardening - true stress increases stress u S f continuously in the plastic region until Reloading Engineering necking. Sy Unloading True strain 5 6 1 Ultimate Point Characteristics log At Maximum load (necking), At necking P = σA σ dP =σdA+ Adσ = 0 σ=K • Ductile and Brittle dσ dA • Perfectly elastic: σ=Eε = − Slope=n=a/b σ A (1) ε=n • Perfectly plastic: σ=Y For a constant volume process • Elastic and Perfectly Plastic Stress 10-3 10-2 10-1 log ε Al = constant 1 –Flow curve: K = Y, n = 0 Eq. (1) can be manipulated dσ • Elastic and Strain hardening Adl + ldA = 0 σ = –Flow curve: K > Y, n > 0 dA dl dε − = = dε With the flow curve, • Nonlinear Strain A l n n −1 n K ε = Kn ε • Temperature-dependent Flow Curve: σ = K ε ∴ ε = n 7 8 Bending and Testing of Brittle Compression Properties Materials • Engineering stress, F • Brittle Materials deform elastically until fracture σ e = – Failure occurs at the outer fibers of specimen when tensile • Engineering strain, Ao strength are exceeded. h − h e = o – Cleavage - separation rather than slip occurs along certain crystallographic planes ho • Three Point Bend Test Barreling due to the friction • Four Point Bend Test 1 .5 FL At the contact surfaces. • Transverse Rupture Strength, TRS = bt 2 F Typically Use K and n from tensile tests n t σ = K ε L b 9 10 Shear Properties Hardness • Brinell Hardness Test: 10mm diameter ball δ Fracture Shear strength with a load of 500, 1000 or 3000kg τ θ 2F b Plastic HB = Yield region 2 2 point ()πDb (Db − Db − Di ) F δ stress, Shear Elastic • Rockwell Hardness Test: A cone shape τ = γ = tanθ = region A b indenter; the depth of penetration is measured. Shear strain, γ • Vickers Hardness Test: Pyramid shape indenter T τ = 1.854F 2 HV = 2πR t 2 τ = Gγ D Rα •For most materials, G ≅ 0.4E γ = L 11 12 2 Shear Plastic Stress-Strain Hardness Relationship • Knoop hardness Test: Pyramid shape • Relationship similar to flow curve indenter 14.2F HK = • Shear stress at fracture = shear strength S D2 – Shear strength can be estimated from tensile • Scleroscope: rebound height strength: S ≅ 0.7(TS) • Durometer: The resistance to penetration – Where did 0.7 come from? (elastic deformation) • Since cross-sectional area of test specimen in torsion test does not change, the engineering • Relationship between Hardness and Strength 2 stress-strain curve for shear is similar to true TS = Kh (HB) where Kh = 500inlb/in stress-strain curve = 3.45in MPa 13 14 Temperature Effect Recrystallization • Effect the all properties • Most metals strain harden at room temperature • Hot hardness • Upon heating to sufficiently high temperature, • Recrystallization(0.5Tm) strain hardening does not occur – Recrystallization - Formation of new strain-free grains – Recrystallization temperature of a given metal = 0.5 Tensile strength ceramics Tm measured on an absolute scale Yield Strength • Recrystallization above the recrystallization Hardness High Alloy Steel temperature takes time. High Carbon Steel • In manufacturing - recrystallization reduces Ductility forces and power. Hot working -Forming metals Low Carbon Steel Ductility and Strength above recrystallization temperature temperature temperature 15 16 Fluid Flow in Manufacturing Viscous behaviors Plastic solid • In many processes, materials (metals, Glass and Polymers) converted from solid to liquid by heating. • A thermoplastic polymer melt non-Newtonian fluids is non-Newtonian Pseudoplastic fluid • Flow is a defining characteristic of fluids shear stress – Viscosity (the resistance to flow) is a measure of the – A fluid exhibiting decreasing internal friction on fluid with velocity gradients viscosity with increasing shear Newtonian fluid – Fluidity (Reciprocal of viscosity) is the easiness of a fluid rate is called pseudoplastic flows • Complicates analysis of constant viscosity • Viscosity can be defined using two parallel plates polymer processes such as Shear rate separated by a distance d injection molding Stress Stress – Shear viscosity is the fluid property that defines the • The material property that relationship between F/A and dv/dy (shear rate); Time Time F dv τ = =η =ηγ τ = ηγ determines the strain Strain & or & Strain A dy d dy subjected to combination of – where η = a constant of proportionality called the dv stress and temperature over coefficient of viscosity, (Pa-s) Time Time 17 time. σ (t) = f (t)ε 18 3 Viscoelastic Behavior of Polymers • Viscoelastic - Combination of viscosity and elasticity 4. Physical (Non-mechanical) • Die swell - In extrusion of polymers, the profile of Properties of Materials extruded material grows in size after being squeezed through the smaller die opening 4.1 Volumetric and Melting Properties −It “remembers” (Shape memory) 4.2 Thermal Properties Materials Viscosity (Pa-s) Materials Viscosity (Pa-s) 4.3 Mass Diffusion Glass @540C 1012 Polymer@151C 115 Glass @815C 105 Polymer@205C 55 4.4 Electric Properties Glass 103 Water@20C 0.001 @1095C 4.5 Electrochemical Processes Machine Oil 0.1 Water@100C 0.0003 19 20 Physical Properties 4.1 Volumetric Properties • Non-mechanical properties that define the • Density (ρ) – lb/in3 or g/cm3 behavior of materials in response to any non- – Specific gravity (ρ/ρ ) physical stimuli such as volumetric, thermal, water electrical, and electrochemical properties – Specific volume (1/ ρ) – Strength-to-weight ratio – T.S./density • Components in a product must do more than withstand mechanical stresses. For example, • Thermal expansion they must conduct electricity (or not), allow – Length ratio - Coefficient of Thermal Expansion (CTE heat to transfer (or not), transmit light and or α) - /°F or /°C. satisfy many other functions. – As T increases, CTE can either increase or decrease • Physical properties often influence process – Phase transformation performance as in machining & –used in shrink fit and expansion fit assemblies microelectronics. 21 22 4.1 Melting Characteristic 4.2 Thermal Properties • Melting point is the temperature at the materials • Specific Heat, C transforms from solid to – The quantity of Heat Energy required to increase liquid. the temperature of a unit mass of a material by 1 – Freezing point - from liquid to -1 degree. solid –H=CW(T2-T1) where H = amount of heat energy; C – Heat of Fusion – An amount Glass (density) = specific heat of the material W = its weight of Heat Energy to accomplish volume Specific transformation. Alloy – Volumetric heat storage capacity, ρC • Supercooled – Below the Pure metal – Thermal conductivity, k freezing point the nucleation Solid Liquid – Thermal diffusivity, k K = of crystals has not been Temperature ρC initiated. • Implication in casting 23 24 4 4.3 Mass Diffusion 4.4 Electrical Properties AB AB AB • Mass Diffusion • Resistivity (in Ω−m) and Conductivity (1/r): – the movement of atoms with in a material (liquid, gas and solid). A E r = R Ohm’s Law: I = • Fick’s First Law: L R dm dc dc = −D A or J = −D dt dx dx • Classes of Materials where ⎛ Q ⎞ – Conductor D = D exp⎜− ⎟ o RT ⎝ ⎠ t=0 t=∞ – Insulator (dielectric) A A A • Fick’s Second Law • Arc if a high enough voltage is applied ∂c ∂ ⎛ ∂c ⎞ ∂J – Superconductor = ⎜ D ⎟ = − ∂t ∂x ⎝ ∂x ⎠ ∂x – Semiconductor – a material whose resistivity is between conductor and insulator. (Si) • Applications: B B B – Surface Hardening • Implication in Electric Discharge Machine(EDM) –Diffusion – Welding 25 26 4.5 Electrochemical Processes • Electrochemistry – A field of science concerned with the relationship between electricity and chemical changes • Electrolytic cell – Electrolyte – Electrodes – anode and cathode • Electrolysis if any chemical change occurs • Farady’s Law – Volume removed, V=CIt, p. 660 • Implications in electroplating and electrochemical machining 27 5.
Details
-
File Typepdf
-
Upload Time-
-
Content LanguagesEnglish
-
Upload UserAnonymous/Not logged-in
-
File Pages5 Page
-
File Size-