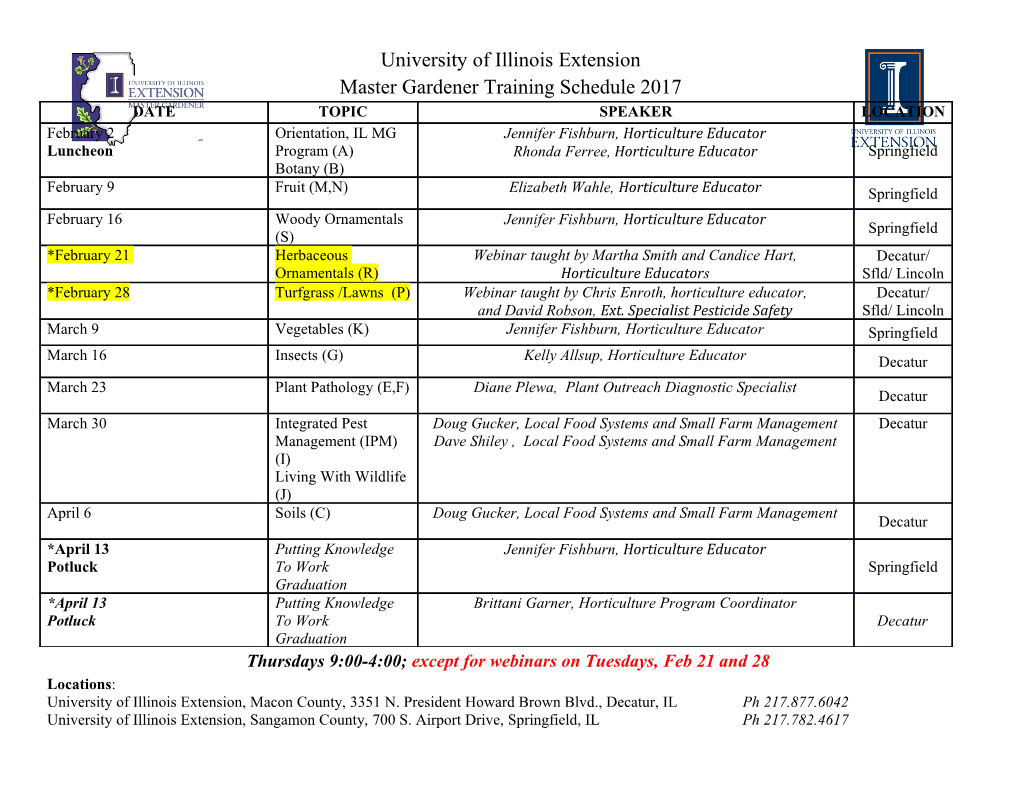
behavior of the process [Weck 2006]. This relative, A SUBSTRUCTURING oriented FRF (Frequency Response Function) Gg is in turn influenced by several other dynamic compliances such as APPROACH FOR that of the machine tool structure GStruc, the cutting tool GTool, the workpiece GWorkpiece, the workpiece holder, etc. SIMULATION OF TIME A variation or modification of any of the components, which lie in the force-flux, will result in the change of the DEPENDENT WORKPIECE system properties, see Figure 1. Machining stability loop Contributions to structure DYNAMICS DURING F F Err x tool Gjg workpiece - MILLING sTt bk cb e F CHRISTIAN BRECHER, PRATEEK CHAVAN, Focus of this paper ROBERT SPIERLING, MARCEL FEY Gg j f( G Tool , G Struc , G Workpiece ,...) Laboratory for Machine Tools and Production Engineering (WZL) of RWTH Aachen University Aachen, Germany Figure 1. Influences on the dynamic compliance of the system machine tool, work piece and tool, based on [Weck 2006] DOI: 10.17973/MMSJ.2018_12_2018105 e-mail: [email protected] With the continuously changing machine position during cutting, the dynamics of the machine structure also During milling, the process forces and poor dynamics of varies. This directly influences the relative compliance the machine may lead to undesirable vibrations between between tool and workpiece and leads to modification workpiece and tool. The magnitude of these vibrations of the process stability boundaries. The simulation of and the chatter tendency depends mainly upon the position and hence time dependent dynamics of the dynamic properties of the Tool-Machine-Workpiece machine has been a subject of great interest in the past system. The dynamic properties of the workpiece can decade. Yigit and Ulsoy employed a displacement vary significantly during the cutting process, while function to describe the change of the dynamic removing a large volume from a workpiece. Therefore, characteristics of the machine tool by assuming the the aim of this paper is to enable the simulation of time flexible joint interfaces with weak nonlinearity [Yigit dependent workpiece dynamics by considering its state 2002]. In [Liu 2011], the authors predicted the variation of material removal. of modal frequencies of machine tools during working using the matrix perturbation method. In [Liu 2014], a A method is proposed to incrementally modify the Finite linear dynamic model with variable coefficients was Element (FE) model of the raw workpiecedepending on proposed. Two unfixed nodes were created to the volume of removed material obtained by a tool- incorporate the varying configuration of the machine workpiece penetration simulation, such that an FE model tool and the explicit mass and stiffness matrices with of the intermittent machined state is obtained. This is respect to a position were set up. realized by substructure decoupling in the physical domain. The time-varying dynamic model of the Apart form the time dependent machine dynamics, the workpiece is thencoupled at four points to spring work piece dynamics also plays a significant role in elementsrepresenting the stiffness of the machine tool determining the stability behavior. Especially in case of table. The developed simulation is subsequently verified thin walled components with complex geometries like by means of vibration measurements and milling tests turbine blades and aerospace components. on a reference workpiece. In [Yang 2016], a method for updating the dynamic KEYWORDS model of the workpiece during cutting process is proposed. This is done by performing modal analysis on workpiece dynamics, dynamics substructuring, physical the FEM model of the initial workpiece, while mode domain, milling shapes and natural frequencies of the in-process 1. INTRODUCTION workpiece could be calculated without re-building and During machining, the relative dynamic compliance re-meshing the instant FEM model at each tool position. between the tool cutting edge and the work piece Recently, the implementation of substructure models determines the machining accuracy and the stability has enabled the efficient prediction of structural MM SCIENCE JOURNAL I 2018 I DECEMBER 2625 modifications. For example, Law used reduced model of the unmachined workpiece using substructure components models of the machine tool axes in order to decoupling in the physical domain (Chapter 3) estimate the FRFs of the machine for different spatial Subsequently, the simulated dynamic behavior of a test configurations. This was then used to estimate the workpiece at different states of material removal is modified stability boundaries [Law 2013, Law 2014]. compared with the measured dynamics of the Brecher et al. suggested a method for coupling the corresponding physical test workpiece (Chapter 4). reduced matrices of the structural components for any Finally, the conclusion and an outlook are presented given machine, workpiece and position configuration (Chapter 5). using multipoint constraints [Brecher 2015, Brecher 2. TOOL-WORKPIECE PENETRATION SIMULATION 2016]. A recent publication by Tuysuz and Altintas 2.1 Discretization of workpiece [Tuysuz 2017] considers time dependent workpiece The discretization of the workpiece is crucial for dynamics using the dual formulation for frequency based determining the accuracy of the penetration simulation substructure decoupling. The FRFs at the relevant points and the computational time. On the one hand, a fine on the workpiece surface are obtained for different meshallows the accurate representation of the machining states by the recursive decoupling of the intermediate machining states of the workpiece but on dynamics of the material removed. This approach is the other hand remains computationally expensive. The suitable for thin-walled, flexible workpieces, where the factors influencing the mesh size are listed in. The mesh flexibility of the work piece is much higher and the size is dependent on the geometry of the raw part, all dynamics of the machine can be neglected. However, in intermediate states and onthe final state. For example, a cases where the workpiece compliance is comparable to mesh with the edge length of an element as a multiple of that of the underlying machine structure (workpiece the depth of cut, will lead to better results in the holder, fixture, table, etc.) the machine stiffness cannot penetration simulation. The mesh itself influences the be ignored. step size of penetration simulation, the discretized tool In this paper, the influence of time dependent workpiece path and the mesh of the subtraction part. Due to their dynamics is considered by combining a Finite Element simple configuration, cubic elements are used for discretization, a tool-workpiece penetration simulation discretization of the workpiece in this paper. Cubic and a substructure decoupling approach. The stiffness of elements with an edge length of 10 mm are chosen here. the underlying machine structure is considered using These elements allow simple rules to determine whether spring elements. The aim is to predict the dynamics of an element is to be considered as penetrated by the tool the workpiece at different stages of material removal or not. during machining. A substructure decoupling technique FE-Mesh of the geometry raw part is utilized for subtracting the volume of material subtraction body geometry step size of the removed by machining from the FE-model of the intermediate parts penetration simulation FE-Mesh unmachined workpiece. For this purpose, a FE-model of geometry finished computing time part a workpiece is created and a method for simulation of tool-workpiece penetration is presented in this paper depth of cut discrete tool path (Chapter 2). Subsequently, a method is presented for Figure 3. Factors influencing the discretization of workpiece removing the volume of machined material from the determine remove discretisation move tool penetrated penetrated volume volume discretisation intermediate work tool tool path piece after final initialize removal CAD model discretisation raw part finished part work piece Figure 2. Procedure for tool-workpiece penetration simulation MM SCIENCE JOURNAL I 2018 I DECEMBER 2626 2.2 Penetration simulation This subtraction of FE is performed by substructure For a known tool path, cutting parameters and decoupling in the physical domain [De Klerk 2008] and is discretized workpiece, discrete intermediate states of described further in Chapter 3. Before decoupling the the workpiece have to be generated.For this, a tool-work elements, a decision has to be made for every finite piece simulation is necessary. element whether it needs to be removed or not. In Inputs for this simulation are a discrete representation addition, the physical properties of the element that has of the workpiece, a discrete tool path and a to be removed must be known before performing the representation of the milling cutter [Altinas 2014]. The subtraction. Since cubic elements are used to discretize penetration simulation process is illustrated in Figure 2. the workpiece, a single cubic element withhomogeneous The material removal process works by identifying theFE material properties serves as a unit for subtraction. elements to be removed and subtracting them The tool, a milling cutter head of Ø50 mm with four repeatedly until an intermediate state of the workpiece inserts, is represented in the penetration simulation as a is achieved.For this process a method to perform the cylinder. The tool path is represented by discrete points
Details
-
File Typepdf
-
Upload Time-
-
Content LanguagesEnglish
-
Upload UserAnonymous/Not logged-in
-
File Pages8 Page
-
File Size-