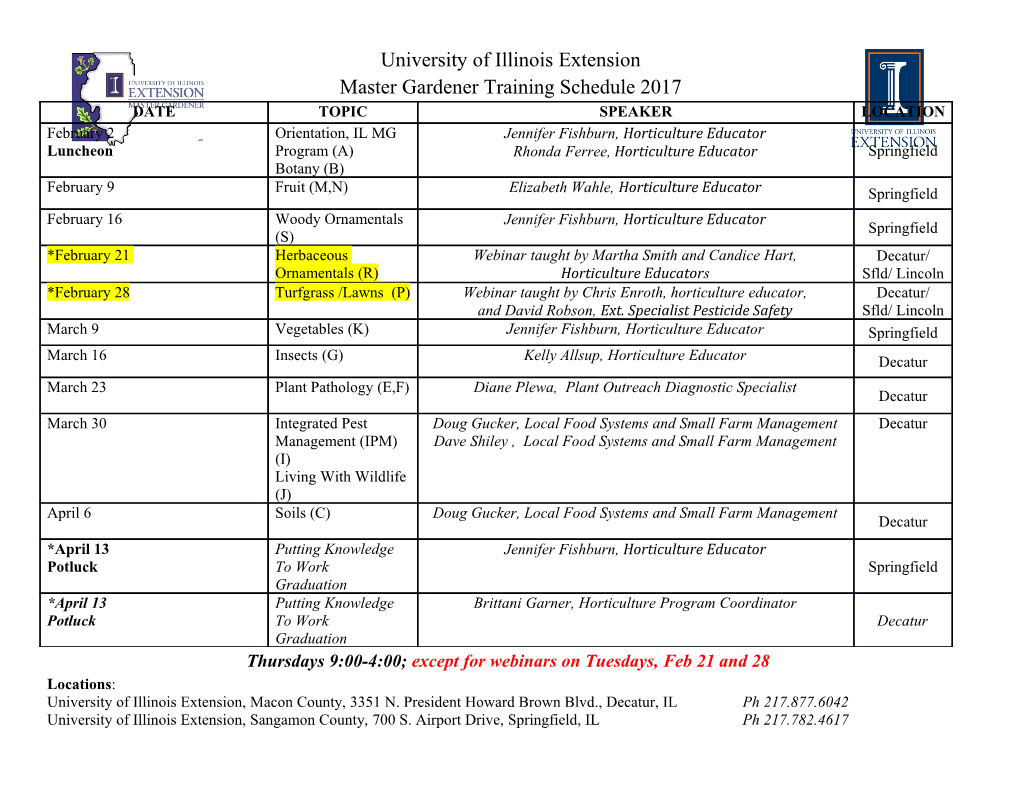
CORROSION SCIENCE SECTION Advancement in Predictive Modeling of Mild Steel Corrosion in CO2- and H2S-Containing Environments Yougui Zheng,* Jing Ning,* Bruce Brown,* and Srdjan Neši´c‡,* ABSTRACT predictions of facilities’ remaining life, and provide guidance in corrosion management. When it comes to Over the past decade, the knowledge related to predicting internal corrosion of mild steel in the oil and gas internal pipeline corrosion for sweet and particularly sour industry, the mechanism of CO2 corrosion is well un- environments has dramatically improved. Advancement in derstood through laboratory investigations.1-2 Hence, understanding of the corrosion mechanisms related to H S 2 models for CO corrosion developed in the past range corrosion environments enabled the development of an inte- 2 from those based on empirical correlations to mech- grated electrochemical model for CO2/H2S uniform corrosion, anistic models describing the different processes involved including the effect of H2S on the protective corrosion product in CO corrosion of carbon steel. In 2002, Nyborg3 formation on mild steel. The latest model of uniform CO2/H2S 2 corrosion of carbon steel accounts for the key processes published a performance-based review of several CO2 underlying of corrosion: chemical reactions in the bulk solution, corrosion models focusing on the ability to account for electrochemical reactions at the steel surface, the mass effects of pH, protective iron carbonate layers, oil wetting, transport between the bulk solution to the steel surface, and the fluid flow, H2S, top-of-the-line corrosion, and acetic corrosion product formation and growth (iron carbonate and acid. Some five years later, Neši´c published a compre- fi iron sul de). The model is able to predict the corrosion rate, as hensive review of the understanding and modeling well as the surface water chemistry, as related to all of the practices for internal corrosion of oil and gas pipelines.4 key species involved. The model has been successfully cali- In the case of H S corrosion, there are numerous brated against experimental data in conditions where cor- 2 rosion product layers do not form and in environments where experimental studies; however, the mechanism of H2S they do, and compared to other similar models. corrosion is still unclear and only a few models have been developed and published in the open literature for KEY WORDS: carbon dioxide, carbon steel, corrosion model, pure H2S or mixed CO2/H2S corrosion. It has been corrosion rate, hydrogen sulfide, uniform corrosion widely observed that the uniform corrosion rate is re- duced in the presence of very small concentrations of INTRODUCTION H2S (1 mbar [0.1 kPa] or even smaller) at room tem- perature and higher. To account for this effect, one Corrosion predictive models are very useful tools that approach is to use a factor related to H2S concentration can be used to determine corrosion allowances, make and correct the predicted sweet (CO2) corrosion rate. For example, in 1999 Anderko, et al.,5 developed a Submitted for publication: February 10, 2015. Revised and accepted: January 20, 2016. Preprint available online: January 21, 2016, mechanistic model to predict the corrosion rates of http://dx.doi.org/10.5006/1667. carbon steel in both CO2- and H2S-containing envir- ‡ Corresponding author. E-mail: [email protected]. onments, which included a thermodynamic calcula- * Institute for Corrosion and Multiphase Technology, Department of Chemical and Biomolecular Engineering, Ohio University, tion to predict corrosion product composition and an 342 W. State St., Athens, OH 45701. electrochemical corrosion model to simulate the ISSN 0010-9312 (print), 1938-159X (online) CORROSION—Vol. 72, No. 5 16/000099/$5.00+$0.50/0 © 2016, NACE International 679 CORROSION SCIENCE SECTION processes of cathodic and anodic reactions on the steel surface, and porous corrosion product layer forma- surface. To get the desired performance, the predic- tion which may or may not be protective. All of these tions of the electrochemical model were simply processes must be taken into account in a predictive correlated to the final steady state corrosion rate model to provide a realistic estimation of the corrosion experimental data by using a surface coverage factor of rate. For CO2 corrosion, an electrochemical mecha- iron sulfide and iron carbonate. Mechanistic verifi- nistic model9-10 based on the key physicochemical cation of this approach using electrochemical kinetics processes has been developed and implemented into data was not performed, and the water chemistry at a software package that is well known and freely 11 the steel surface and in the bulk solution was not available. For H2S corrosion, Sun and Neši´c’s mass distinguished in their model. In 2009, Sun and transfer model6 is also publically available and widely 2,6 2,11 Neši´c modeled CO2/H2S corrosion based on an as- implemented. Based on the recent experimental 12 sumption that in the presence of H2S, the corrosion findings, and the more thorough understanding that rate is always mass transfer controlled as a result of the has emerged in the meantime, a more comprehensive ubiquitous presence of iron sulfide layers. A wide uniform aqueous H2S corrosion model can now be range of experimental results were collected to calibrate formulated and is described next. this model, making it a useful tool for the prediction of The outline of the new physicochemical model transient corrosion rates arising from the growth of iron can be started by picturing aqueous H2S diffusing to a sulfide layers. However, the model consisted of a steel surface, where it reacts rapidly to form a very number of assumptions that were not explicitly verified. thin adsorbed sulfide layer, as suggested by Marcus, In particular, it was universally assumed that the rate et al.13 Following the mechanism proposed by Smith 14 of corrosion in the presence of H2S is always under mass and Wright, it can be written as: transfer control; hence, the electrochemical reactions fi þ → þ were not de ned nor included in the model. This made it FeðsÞ H2SðaqÞ FeSðadÞ 2HðadÞ (1) harder to integrate this model with mechanistic 13 (electrochemical) models of CO2 corrosion. The work of Marcus, et al., indicates that sulfur In earlier papers published by the present adsorbs very strongly to a steel surface and can displace 7-8 − authors, an electrochemical corrosion model of H2S adsorbed H2O and OH . This action results in slowing corrosion without iron sulfide layer growth has been down the kinetics of electrochemical reactions such as developed to describe the corrosion process on a bare Fe dissolution, H2O reduction, and carbonic acid steel surface, thereby avoiding the complex issues reduction, apparently by affecting the double layer. The associated with formation and growth of an iron sulfide electrochemical reactions (both anodic and cathodic) corrosion product layer. The model in the present continue to go forward despite an existing adsorbed paper is mainly focused on the growth and the effect of sulfide layer, albeit at a slower rate. − protective corrosion product layers (iron carbonate or When the surface concentrations of Fe2+ and S2 iron sulfide) on the corrosion by taking a mechanistic ions exceed the solubility limit of iron sulfide (initially approach. The model is able to predict the corrosion mackinawite), solid iron sulfide is thermodynamically rate and also the concentration at the metal surface of stable, and it will precipitate on the steel surface: all of the species involved in the corrosion process. 2þ 2− Fe þ S ⇋ FeSð Þ (2) PHYSICOCHEMICAL PROCESSES ðaqÞ ðaqÞ s UNDERLYING CO2/H2S CORROSION This iron sulfide layer can grow and retard the corrosion rate via a surface coverage effect and a mass CO2/H2S corrosion is a complex process involv- transfer effect (acting as diffusion barrier). The ing multiple physicochemical processes occurring si- present transient corrosion model is somewhat similar, multaneously. These are: chemical reactions in the but also quite different from the model proposed by bulk solution, mass transport of aqueous species Sun and Neši´c6 in some key elements. A comparison through the liquid boundary layer and the porous between the key differences for the two models is surface layer, electrochemical reactions at the steel listed in Table 1. TABLE 1 Differences Between Sun-Neši´c Model6 and the Present Model Sun-Neši´c Model (2009)6 Present Model A thin inner mackinawite film formed by direct chemical reaction A thin adsorbed iron sulfide film affecting directly the kinetics of acting as a solid state diffusion barrier. different electrochemical reactions (retardation effect). A porous outer iron sulfide layer formed by spalling of the inner layer. An outer iron sulfide layer formed via a precipitation mechanism. Corrosion rate is always under mass-transfer control because of the Corrosion rate is not always under mass-transfer control depending porous outer iron sulfide layer and inner mackinawite film. on the kinetics of mass transfer and electrochemical reactions. 680 CORROSION—MAY 2016 CORROSION SCIENCE SECTION MODEL DESCRIPTION These three physicochemical processes are intercon- nected and can be expressed by writing a material The present model describes H2S/CO2 corrosion balance or mass conservation reaction for a thin surface in terms of two main processes: an electrochemical water layer. corrosion process including effect of mass transport from bulk to the surface, and corrosion product for- ∂c N − N surface,j = e,j w,j þ R (3) mation and growth process for iron carbonate and ∂t Δx j iron sulfide. where csurface,j is the concentration of species j, Ne,j is Electrochemical Corrosion Model the flux of species j on the east boundary resulting The concentration of the species can be very from mass transfer from the bulk solution to the fl different in the bulk solution and at the corroding steel surface, Nw,j is the ux of species j on the west surface because of corrosion, mass transfer effects, boundary resulting from electrochemical reactions at and chemical reactions.
Details
-
File Typepdf
-
Upload Time-
-
Content LanguagesEnglish
-
Upload UserAnonymous/Not logged-in
-
File Pages13 Page
-
File Size-