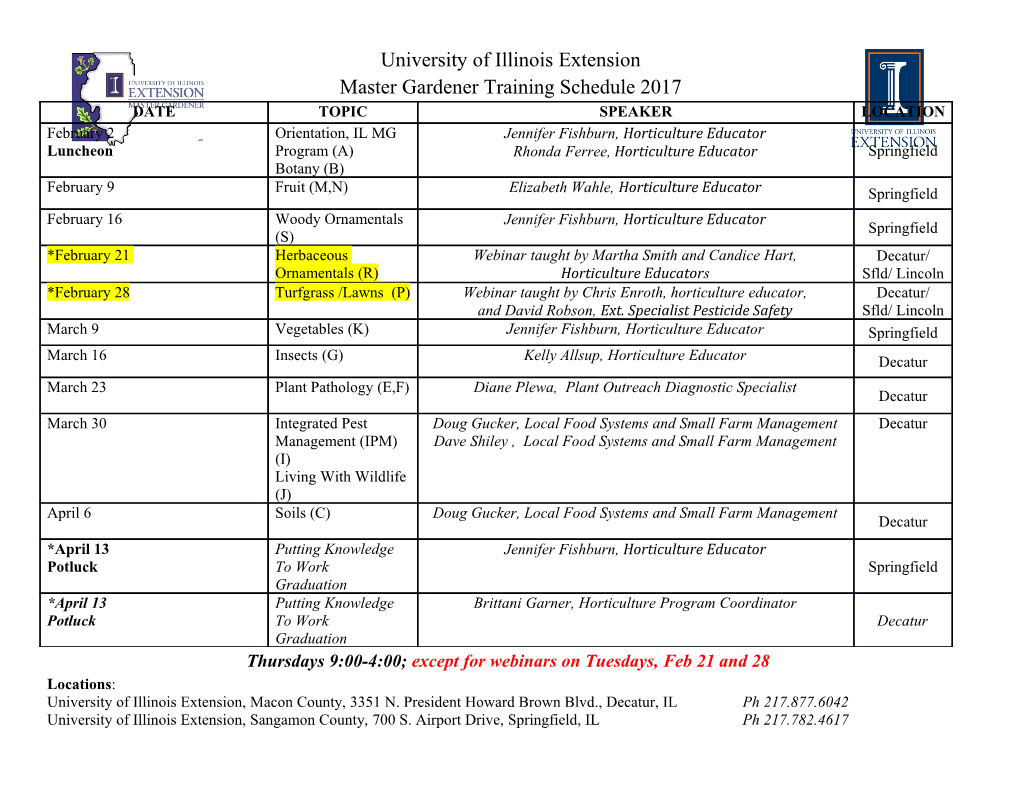
Using Rogowski Coils Inside Protective Relays Veselin Skendzic and Bob Hughes Schweitzer Engineering Laboratories, Inc. © 2013 IEEE. Personal use of this material is permitted. Permission from IEEE must be obtained for all other uses, in any current or future media, including reprinting/republishing this material for advertising or promotional purposes, creating new collective works, for resale or redistribution to servers or lists, or reuse of any copyrighted component of this work in other works. This paper was presented at the 66th Annual Conference for Protective Relay Engineers and can be accessed at: http://dx.doi.org/10.1109/CPRE.2013.6822022. For the complete history of this paper, refer to the next page. Presented at the 66th Annual Conference for Protective Relay Engineers College Station, Texas April 8–11, 2013 Originally presented at the 39th Annual Western Protective Relay Conference, October 2012 1 Using Rogowski Coils Inside Protective Relays Veselin Skendzic and Bob Hughes, Schweitzer Engineering Laboratories, Inc. Abstract—Traditionally, microprocessor-based relays The primary difference between conventional CTs, linear incorporate a secondary current transformer to convert the 5 A couplers, and Rogowski coils can be summarized as follows: or 1 A input current to a lower level for input to an analog-to- Conventional CTs are insensitive to the position of the digital (A/D) converter as part of the input processing. The limits of this input circuit are well known, and relay designers take primary conductor inside the core and provide exceptional them into account when determining operating characteristics. rejection of external magnetic fields, but the core can saturate A Rogowski coil produces an output based on the rate of under high-current fault conditions (including dc offset). change of the current input, so passing the output of the coil Linear couplers do not saturate but are sensitive to external through an integrator produces a signal that is proportional to magnetic fields and the primary conductor position. Similar to the current. There are additional characteristics of a Rogowski linear couplers, Rogowski coils do not saturate, but they also coil that give it particular advantages for use in a include well-controlled geometry with a return loop, which microprocessor-based relay, including the following: improves external magnetic field rejection and makes the coil • An air core. This leads to no saturation, even at very high currents. less sensitive to the primary conductor position. Rogowski coils are well recognized as primary current • A flexible shape. With no iron core, the coil can be shaped and sized to fit the application. sensors and are exceptionally well suited for applications • Immunity to electromagnetic interference. This makes where high-voltage insulation is provided by the adjoining the coil suitable for electrically noisy environments. apparatus, such as in gas-insulated switchgear, dead-tank These advantages, and others, make a Rogowski coil high-voltage breakers, medium-voltage applications (as shown something to consider for the input of microprocessor-based in Fig. 1), and low-voltage applications. relays, where the integration required to obtain the input current is a relatively easy operation. This paper discusses the practical considerations of using this coil in a relay. Complicating and mitigating factors are discussed, along with the performance impact on the relay and practical experiences in the field. Application impacts of Rogowski coil use are presented, including which types of relays are most benefited by this technology. Future implications of this technology are also presented. I. INTRODUCTION Fig. 1. Medium-voltage Rogowski coil design example. Rogowski coil technology is well known in the power The use of Rogowski coils in the CT secondary circuits is industry. Its origins can be traced back to 1912, but at that less known and is documented in this paper with the samples time, the low-energy coil output and the fact that it measures shown in Fig. 2. the derivative of the input current made it impractical for use with the prevailing electromechanical relay technology [1]. Practical applications of Rogowski coil-based technology have been steadily rising, but the rate of adoption remains slow, mostly owing to the excellent performance, high reliability, and low cost delivered by conventional current transformers (CTs). With the advent of modern microprocessors, Rogowski coils are gaining additional momentum and are being slowly brought into everyday applications. Based on their operating principle, Rogowski coils are closely related to linear couplers (air core mutual inductors), which have earned their place in Fig. 2. Conventional CT and the Rogowski coils with conventional CT the most demanding high-current applications, such as arc- components in the middle (core, core with secondary, and completed CT assembly). furnace transformer or low-voltage busbar protection applications. 2 II. THEORY OF OPERATION between the two is the presence (or absence) of the References [1] and [2] provide excellent tutorials on the ferromagnetic core. The behavior of the two, however, is very Rogowski coil theory of operation. For the purposes of this different due to a large change in individual component values paper, it is sufficient to know that the coil produces voltage (spanning several orders of magnitude). output proportional to the derivative of the current enclosed by In the case of conventional CTs [3], the element in the the coil contour. The physical arrangement is illustrated in position of inductor M is the CT magnetizing branch Fig. 3. inductance, which is typically very large (several henries), while the elements in place of Lcoil, Rcoil, and Ccoil (representing transformer leakage inductance, secondary winding resistance, and winding capacitance, respectively) are typically very small, to the point of being neglected in most models. In the case of the Rogowski coil, M is very small (typically several microhenries), while the coil leakage inductance (Lcoil) and the coil winding resistance (Rcoil) are relatively large (several millihenries and 10 to 100 Ω). Winding capacitance is normally distributed but is often approximated with a single capacitor (Ccoil), which determines (in combination with Lcoil) the Rogowski coil self-resonance. Fig. 3. Rogowski coil current sensor. The equivalent circuit model is very useful for designing the electronic circuits necessary to process Rogowski coil Voltage induced at the coil output is equal to (1). signals. Model component values can be entered into a SPICE ddiψ circuit simulator, allowing easy evaluation of the proposed v–== –M (1) out dt dt circuit behavior. Following procedure documents, an easy method for determining the required model parameters is as where: follows: vout is the output voltage. • Mutual inductance, M, is determined by measuring Ψ is the total flux enclosed by the coil. coil sensitivity (mV/A) at a known frequency (e.g., M is the mutual inductance between the primary and the 60 Hz). Simply calculate the inductance that will secondary windings. result in the same voltage drop. i is the primary current. • Leakage inductance is measured directly by using an t is the time. impedance analyzer. Mutual inductance, M, is determined by the physical • Coil winding resistance is measured directly by using dimensions of the coil and can, for most configurations, be an ohmmeter. calculated analytically as a closed-form expression. As long as • Winding capacitance can be estimated by finding the the coil dimensions (winding density, contour length, and first resonance peak in the coil output, taking into volume enclosed by the coil turns) are kept constant, mutual account any capacitance introduced by the output inductance remains constant, thus ensuring constant voltage measurement instrument. A high-impedance transducer gain. The exact path of the contour can vary, thus oscilloscope probe is often appropriate for the task. leading to a very popular flexible Rogowski coil Capacitance is calculated so that it resonates at the implementation. same frequency when connected in parallel with the previously measured Rcoil, Lcoil, and M. III. ROGOWSKI COIL MODEL DEVELOPMENT Fig. 5 illustrates a typical underdamped coil response Similar to the conventional CT, a Rogowski coil can be causing undesirable ringing associated with fast current represented with an equivalent circuit, as shown in Fig. 4, transients. Fig. 6 further explains this ringing by presenting which is very familiar to power engineers. the coil response as a function of frequency. It is easy to see that the coil output (voltage drop across M) increases with frequency until it reaches the coil self-resonance. Beyond the resonance peak, the coil output rapidly decreases. Fig. 7 shows an appropriately damped impulse response that can be achieved by adding carefully selected loading components. Fig. 4. Rogowski coil equivalent circuit. Resistor R3 typically has a dual function, helping with both high-frequency damping and temperature compensation Fig. 4 shows great similarity to the equivalent circuit control. With the damping component values shown in Fig. 7, representation of the conventional (magnetic core-based) CT. the example coil bandwidth exceeds 80 kHz. This is quite normal, given the fact that the main difference 3 IV. APPLICATION CONSIDERATIONS When compared with conventional (magnetic core-based) CTs, Rogowski coils offer a number of distinct
Details
-
File Typepdf
-
Upload Time-
-
Content LanguagesEnglish
-
Upload UserAnonymous/Not logged-in
-
File Pages12 Page
-
File Size-