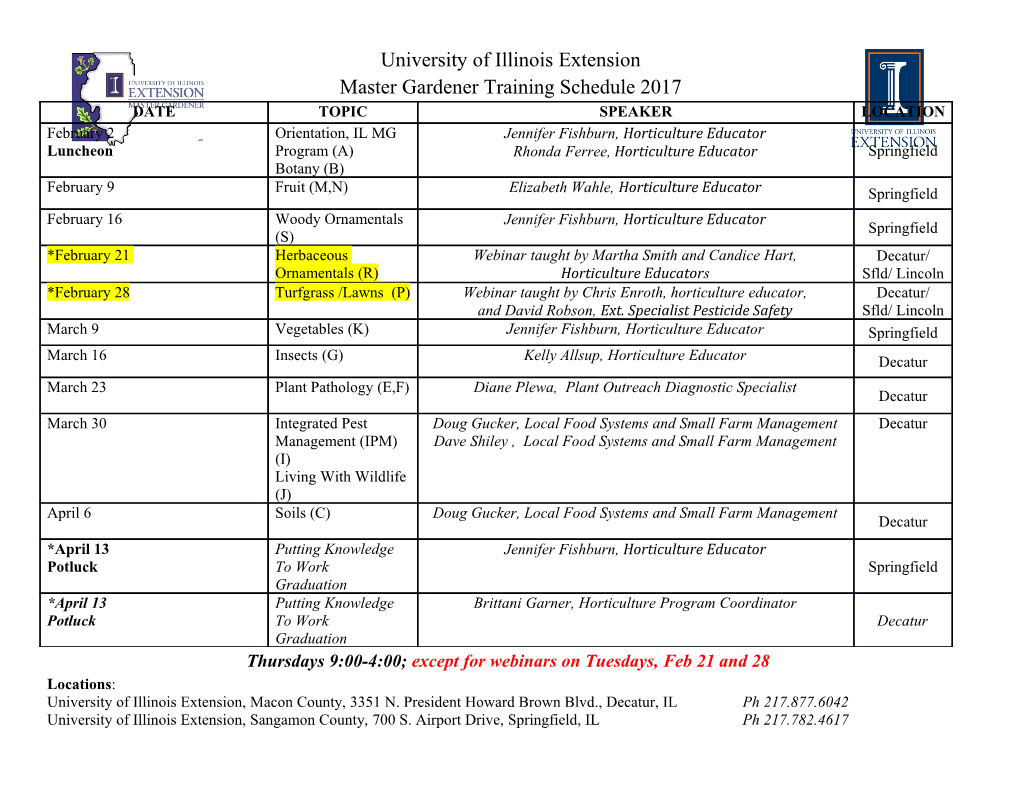
AN INVESTIGATION OP THE EFFECTS OP THE USE OP INDIVIDUAL THROTTLE VALVES FOR EACH CYLINDER OF A MULT I- CYLINDER INTERNAL COMBUSTION ENGINE A Thesis Presented to The Faculty of the Division of Graduate Studies Georgia Institute of Technology In Partial Fulfillment of the Requirements for the Degree Master of Science in Mechanical Engineering b7 Edward Joseph Schatz June 1952 2^3260 V ii AN INVESTIGATION OP THE EPPEGTS OP THE USE OP INDIVIDUAL THROTTLE VALVES POR EACH CYLINDER OP A MULT I-CYLINDER INTERNAL COMBUSTION ENGINE Approved . -n /- •**- ^2_ Date Approved by Chairmaiyv1^^ ^ / ^J / iii ACKNOWLEDGEMENTS I wish to express my gratitude to Professor Robert L. Allen for suggesting this problem and for his aid in the pursuance of the investigation. Also I would like to thank Mr. T.D. Sangster and Mr. J.W. Davis for their help in the construction of equipment. TABLE OP CONTENTS PAGE Acknowledgements iii List of Tables v List of Figures v^ List of Symbols and Abbreviations vii Introduction 1 Apparatus 5 Test Procedure 7 Discussion 9 Results 11 Conclusions 13 Bibliography 15 Appendix I, Diagrams and Photographs 16 Appendix II, Tables and Curves 22 Appendix III, Sample Calculations 46 LIST OP TABLES TABLE PAGE I OBSERVED DATA GROUP A 23 II OBSERVED DATA GROUP B 26 III OBSERVED DATA GROUP C 28 IV OBSERVED DATA GROUP D 30 / CALCULATED DATA GROUP A 32 VI CALCULATED DATA GROUP B 35 VII CALCULATED DATA GROUP c 37 VIII CALCULATED DATA GROUP D 39 LIST OP FIGURES FIGURE PAGE 1 Theoretical Throttled Otto Cycle 17 2 Schematic Drawing of a Single Cylinder Engine Illustrating a Comparison of the Performance of Individual Throttle Valves and Regular Throttle IS 3 Photograph of Instruments 19 4 Photograph of Engine and Fuel System 20 5 Photograph of Manifold with the Individual Throttle Valves 21 6 Thermal Efficiency, 1200 RPM 41 7 Thermal Efficiency, 1400 RPM 42 8 Thermal Efficiency, 1600 RPM 43 9 Thermal Efficiency, 1800 RPM 44 10 RPM Calibration Curve 45 LIST OP ABBREVIATIONS AND SYMBOLS a Area of orifice, 0.00545 square feet A/P Air-Fuel ratio BHF Brake horsepower BP Barometric pressure, inches of mercury DC Dynamometer constant, 6000 E. Thermal efficiency g Gravitational constant 116,000 feet/minute2 Differential pressure drop across the micromanometer, inches of alcohol E Differential pressure drop across the micromanometer, a feet of air Hv Heating value, 20,000 BTU/pound K Orifice coefficient, 0.S25 L Dynamometer load, pounds MP Manifold pressure, inches of mercury Q Air flow, cubic feet per minute R Gas Constant for air RPM Revolutions per minute Ta Temperature of the air, degrees Fahrenheit a. T Temperature of the air, degrees Rankine Wa Weight of air used for a four minute run, pounds W^ V/eight of fuel consumed for a four minute run,pounds Ws Specific weight of alcohol, 49# 3 pounds per cubic foot (ws'a Specific weight of air, pounds per cubic foot AN INVESTIGATION OF TEE EFFECTS OF THE USE OF INDIVIDUAL THROTTLE VALVES FOR EACH CYLINDER OF A MULTI-CYLINDER INTERNAL COMBUSTION ENGINE INTRODUCTION Purpose: The purpose of this investigation is to compare the efficiencies obtained at low load, using individual throttle valves for each cylinder, with those obtained using the conventional throttling method. Objective: It is the object of this investigation to show by means of data obtained from the operation of an Otto cycle engine that an increase in thermal efficiency can be obtained through the use of individual throttle valve3 30 located as to enable a high pressure to be maintained in the intake manifold, thereby eliminating some of the causes of low efficiency at very light loads in the Otto cycle engine, A higher pressure at the intake manifold reduces the expansion of residual gas into the intake manifold when the intake valve opens. As a result, the work usually required fo force this gas back into the cylinder, prior to induction of the fresh charge, is decreased. Also the extra dilution of fresh charge by exhaust gas which may be pulled back into 2 the cylinder due to valve overlap is avoided. In the Otto cycle engine, the conventional method of governing consists of a throttle valve in the carburetor, As this valve is closed, the area through which the fresh charge must flow is progressively decreased. The pressure in the intake manifold is a function of the throttle opening and engine speed and, at a given speed, is a function of the output torque. The pressure in the cylinder at the end of the exhaust stroke, however, is approximately atmospheric at all engine loads and speeds. Consequently, opening of the intake valve causes residual gas to expand into the intake manifold, resulting in a decrease of cylinder pressure to that of the intake manifold. The entire suction stroke of the en­ gine then occurs at manifold pressure, drawing the expanded exhaust gas back into the cylinder as well as the fresh charge of fuel and air, This intake process is shown by path 6-6'il of the theoretical throttled Otto cycle on figure 1. The cross- hatched area of this diagram represents the pumping work of the cycle and can be seen to be a function of the manifold pressure. As the load is decreased, this negative work area becomes larger while the positive work area decreases so that at very light loads, the negative work area becomes suffi­ ciently large to cause an appreciable decrease in thermal efficiency, By using the individual throttle valves and making the 3 volume between each tlirottle and intake valve small enough to allow the pressure in that volume to build up to atmospheric between suction strokes, there is no sudden drop of pressure in the cylinder when the intake valve opens but instead a gradual decrease occurs as the suction stroke progresses, re­ sulting in some other intake path as approximated by line 6-1 on figure 1, It is apparent that a saving of pumping work, proportional to the area between paths 6-1 and 6-6"-l, is achieved, In effect, a comparison of the operation of the regular throttle and the special throttle valves can be shown by con­ sidering the schematic drawing of a single cylinder engine in figure 2, The chamber situated between the throttle valve and intake valve represents an infinite reservoir at a pressure equal to the intake manifold pressure. This would correspond to the condition in the intake manifold of a multi-cylinder engine with six or more cylinders where the intake strokes overlap. When the valve to this chamber is open, the pressure at the beginning of the intake stroke is that of the reservoir and the entire suction stroke occurs at that pressure, as in the case of the regular throttle of the multi-cylinder engine. on the other hand, if the valve to the chamber is closed, the pressure at the start of the intake stroke is atmospheric and gradually decreases to the reservoir pressure as the intake stroke progresses, returning to atmospheric during the three intervening strokes. This would correspond to the case of 4 the individual throttles in a multI-cylinder engine. Review of the Literature: For any given speed and throttle opening, it has been determined that a definite fuel-air ratio exists which will give best-economy and another which will give best-power, Praas says: "The most important single variable determining the fuel-air ratios for each of these conditions is the amount of residual exhaust gas which increases rapidly as the engine is throttled to an idle and materially slows down the flame speed." As a consequence of this increased dilution of fresh charge by residual gas, the relative proportion of combustible vapor is reduced, "Because of this," Praas continues, "the best-power and best-economy mixtures under idling and low power-output conditions are considerably richer than at moder­ ate or high power-outputs." Since that part of the exhaust gas which normally expands into the intake manifold as a re­ sult of valve overlap increases the amount of residual gas, elimination of this expansion by use of the individual throttles should decrease the fuel-air ratios for best-power and best-economy in the low power range. Praas, A.P., Combustion Engines, McGraw-Hill Book Company, Inc., Hew York, 1948, p,158# APPARATUS Engine: The engine used for tliis investigation is a four cy­ linder Continental Red Seal engine, model Y-69, This is an industrial engine whose specifications are as follows: Bore (inches) 2,5 Stroke (inches) ....... 3,5 Displacement (cubic inches).,,.. 68,7 Compression ratio. 6,2:1 For the individual throttles, a butterfly valve was placed at the exit of each of the intake Dorts of the mani­ fold with the shafts projecting vertically downward as shown in figure 5# By locating them in this manner, the pressure drop associated with throttling appears in the small volume between the individual throttle valve and the intake valve of the engine instead of in the intake manifold. Perpendicu­ lar to the extremity of each of these shafts, a lever arm was attached which was connected at the other end to a synchro­ nizing rod for uniform adjustment, A small allowance was made for individual adjustment of these valves to permit closer control of the engine, A friction type stop was put on each shaft to prevent any movement of the valve from its intended setting, To measure the power output, a Taylor hydraulic dyna­ mometer was connected to the engine hj means of a flexible coupling.
Details
-
File Typepdf
-
Upload Time-
-
Content LanguagesEnglish
-
Upload UserAnonymous/Not logged-in
-
File Pages54 Page
-
File Size-