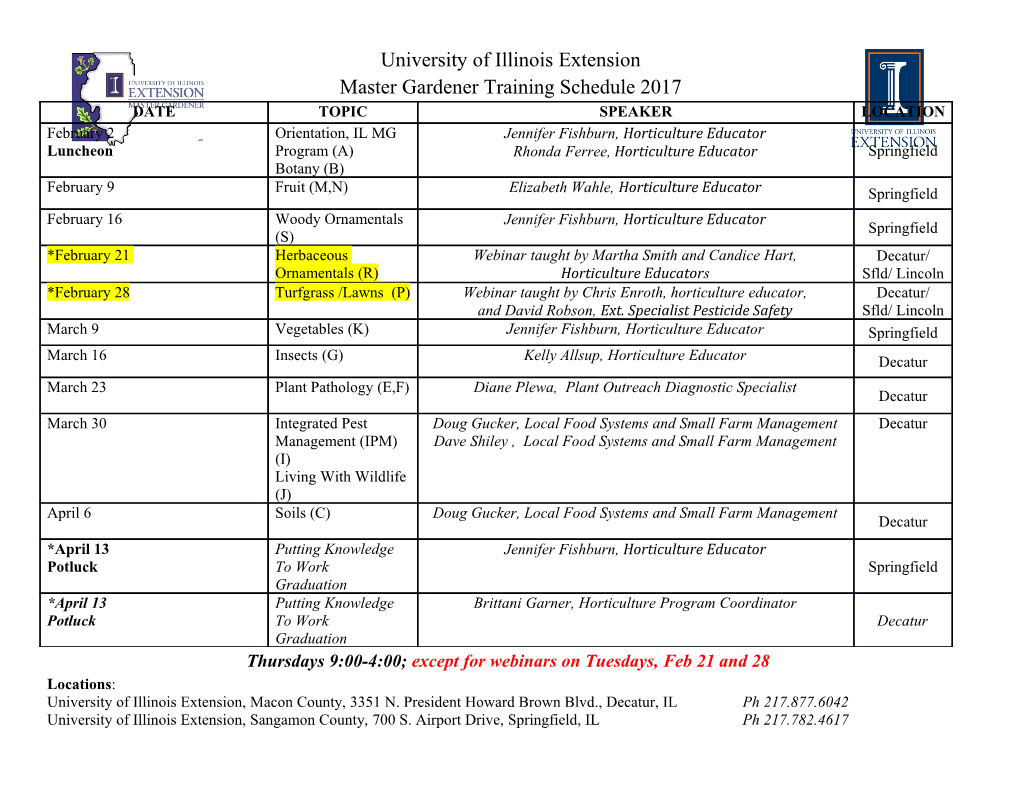
PARAMETRIC VIBRATIONS OF TRAVELING PLATES AND THE MECHANICS OF WASHBOARDING IN BANDSAWS by ZHUSAN LUO B. A. Sc. Nanjing University of Aeronautics and Astronautics, China 1982 M. A. Sc. Nanjing University of Aeronautics and Astronautics, China 1985 A THESIS SUBMITTED IN PARTIAL FULFILLMENT OF THE REQUIREMENTS FOR THE DEGREE OF DOCTOR OF PHILOSOPHY in THE FACULTY OF GRADUATE STUDIES DEPARTMENT OF MECHANICAL ENGINEERING We accept this thesis as conforming to the required standard THE UNIVERSITY OF BRITISH COLUMBIA July 2001 © ZhusanLuo, 2001 In presenting this thesis in partial fulfilment of the requirements for an advanced degree at the University of British Columbia, I agree that the library shall make it freely available for reference and study. I further agree that permission for extensive copying of this thesis for scholarly purposes may be granted by the head of my department or by his or her representatives. It is understood that copying or publication of this thesis for financial gain shall not be allowed without my written permission. Department of Mechanical Engineering The University of British Columbia 2324 Main Mall Vancouver, Canada V6T 1Z4 Date: Abstract This thesis presents a study on the high frequency dynamic behavior of traveling plates subjected to in-plane stresses. The effects of damping, parametric and modulated excitations on the vibration characteristics of the plates are considered. The application of this work to the explanation of the mechanisms responsible for washboarding in bandsaws is presented. A high frequency mode of a traveling plate is defined using the envelope of its mode shapes. Modal analysis of a traveling plate is conducted theoretically and experimentally. The effects of the traveling speed, the in-plane stresses and the plate geometry on the natural frequencies are examined. The self-excited vibration of a smooth band subjected to lateral regenerative forces is studied and the instability regions are determined. In order to model the tooth profiles and the moving lateral cutting forces applied at the teeth of a bandsaw blade, a finite element model is built and three moving plate elements are developed. The stability of the blade is investigated based on this model. The analytical results based on the smooth band model and the finite element model are consistent with the experimental results from modal testing. The vibration responses and stability of a damped spring-mass system and a damped smooth band subjected to both parametric and modulated excitations are investigated. The maximum magnification factor corresponds to the excitation at the lowest exciting frequency due to the effect of regenerative forces. The instability regions of this system are reduced by increasing damping or decreasing regenerative forces. A kinematic model of washboarding is built based on the loci of teeth so that a washboarding pattern can be simulated and the washboarding mode can be determined by decoding the pattern. Two types of washboarding patterns are observed in the cutting tests. Type I washboarding is explained as the result caused by the modulated and forced vibration due to the displacement excitations from the guides. Type II washboarding is caused by the self-excited vibration due to the regenerative cutting forces. ii Table of Contents Abstract 11 Table of Contents Hi List of Tables vi List of Figures v» Nomenclature x» Acknowledgments xv"> 1 Introduction 1 1.1 Background 1 1.2 Previous Research 7 1.3 Objectives and Scope 9 2 Vibration Characteristics of Traveling Bands 11 2.1 Model of the Traveling Band 12 2.2 Mode Coupling and Mode Orders 15 2.3 Effects of the Guide Constraints 20 2.4 Effects of the Blade Speed 25 2.5 Effects of Internal Stresses 27 2.6 Effects of the Tooth Gullet 39 2.7 Summary 46 3 Stability of Traveling Bands Subjected to Parametric Excitations 48 3.1 Model of Regenerative Cutting Forces 49 iii 3.2 Stability Analysis of a Smooth Band 52 3.3 Instability Regions of a Smooth Band 57 3.4 summary 62 4 Modal and Stability Analyses of Moving Blades Using FEA 64 4.1 Modeling Moving Cutting Forces Applied at Tooth Tips 64 4.2 4-Node Moving Bilinear Plate Element 67 4.3 3-Node Triangular Plate Element 71 4.4 Variable-Domain Rectangular Plate Element 80 4.5 Stability Analysis of the Toothed Blade 86 4.6 Analytical Results 91 4.7 Experimental Results from Modal Testing 100 4.8 Summary 113 5 Responses of Damped Systems to Parametric and Modulated Excitations 114 5.1 Modulated Cutting Forces 114 5.2 Stability and Response of a Damped Spring-Mass System 117 5.3 Stability and Response of a Traveling Band 124 5.4 Summary 132 6 Kinematics of Washboarding 134 6.1 Washboarding Patterns Caused by a Single Traveling Wave 135 6.2 Washboarding Patterns Caused by Multi-Traveling Waves 140 6.3 Summary 144 7 Mechanics of Washboarding 146 7.1 Washboarding Caused by Modulated Vibration 147 7.2 Washboarding Caused by Self-Excited Vibration 162 7.3 Comparison of Two Types of Washboarding Mechanisms 168 iv 8 Conclusions Bibliography Appendix A Structure and Parameters of the Bandsaw Appendix B The System Matrices and the Generalized Force Vector in the Equations of Motion of a Moving Plate Appendix C Shape Functions and Explicit Expressions for MDKT Element Matrices List of Tables 2.1 Natural Frequencies of Smooth Bands and Toothed Blades 41 3.1 Effects of the Order of Fourier Series 57 4.1 Natural Frequencies of a Stationary Plate 91 4.2 Natural Frequencies of a Stationary Plate with Internal Forces 92 4.3 Natural Frequencies of a Moving Plate with Internal Forces . 93 4.4 Natural Frequencies of a Moving Plate with Internal Forces 94 4.5 High Natural Frequencies of a Moving Plate with Internal Forces 94 6.1 Washboarding Patterns from Metal Cutting 139 7.1 A Comparison of Washboard Pitches (Type I) 157 7.2 Vertical Pitches of Different Modes 164 7.3 A Comparison of Washboard Pitches (Type II) 166 7.4 Properties of Two Types of Washboarding Patterns 168 A.l Dimensions and Main Parameters of the Bandmill 179 A.2 Geometry of the Bandsaw Blades 179 vi List of Figures 1.1 An industrial bandsaw mill 3 1.2 Schematic of the bandmill 4 1.3 A wide bandsaw blade 5 1.4 Washboarding patterns in bandsaws: (a). Type I; (b). Type II 6 2.1 Bandsaw blade over the cutting span 12 2.2 Mode shapes: (a). Mode (1, 1); (b). Mode (2, 2) 16 2.3 Mode shapes and their envelopes: (a). Mode (1, 1); (b). Mode (2, 2) 17 2.4 Mode shapes and their envelopes: (a). Mode (9, 4); (b). Mode (2, 6) 19 2.5 Typical frequency response functions: (a). Between the upper span and the cutting span; (b). Between the lower span and the cutting span 21 2.6 Effect of the span length on the first lateral and torsional modes 23 2.7 Effect of the span length on high frequency modes 24 2.8 Effects of blade speed on lateral and torsional modes 26 2.9 Effects of blade speed on high modes 27 2.10 Lateral (LI) and torsional (Tl) frequencies increase with strain 28 2.11 Effect of the blade thickness on natural frequencies: (a). First bending mode; (b). First torsional mode 29 2.12 Effect of the blade thickness on high modes 30 2.13 Typical residual stresses induced by roll-tensioning 31 2.14 Effects of tensioning stresses on the first bending and torsional modes ... 31 2.15 Two lowest modes of the stationary band: 33 (a). First torsional mode (1, 2); (b). First lateral mode (1,1) 2.16 Mode shapes, tensioning stresses and strain energy density at the first 33 (a) torsional mode and (b) lateral mode 2.17 Effects of tensioning stresses on high modes 35 2.18 Mode shapes of the blade installed on a tilted wheel (0C=0.4°): vii (a) . Lateral mode; (b). Torsional mode 36 2.19 Effect of the tilt angle on bending and torsional modes 37 2.20 Effect of the tilt angle on high modes 37 2.21 Wheel crown induced stress distribution 38 2.22 Two types of gullets 40 2.23 Meshes of a toothed blade (725 nodes and 914 elements) 40 2.24 Smooth Blade (42A): (a). Mode shape of the smooth blade; (b) . Mode shape at the cross-section at x=L/2 42 2.25 Toothed Blade (42A): (a). Mode shape of the smooth blade; (b). Mode shape at the cross-section at x=L/2 43 2.26 Mode shape of smooth blade (50A) at x=L/2 44 2.27 Mode shape of toothed blade (50A) at x=L/2 44 2.28 Frequency response functions of two toothed blades: (a) . Gullet Type 42A; (b). Gullet Type 50A 45 3.1 Regenerative cutting force: (a). Two balanced side cutting forces; (b) . Two unbalanced side cutting forces 50 3.2 Model of the cutting forces 51 3.3 (a) Natural frequency and (b) real part of the first mode 58 3.4 Stable vibration of a smooth band (F, = (2F„/3, F„)) 59 3.5 Unstable vibration of a smooth band (F, - (Fnl2, 2F„/3)) 59 3.6 (a) Natural frequencies and (b) real parts of eigenvalues of the blade subjected to regenerative cutting forces (Ro=2Q kN, K /=10 kN/m) 61 3.7 Effects of the cutting force coefficient on (a) natural frequency and (b) real part of Mode (9, 2) 62 4.1 Finite element model of the blade 66 4.2 Isoparametric bilinear element: (a).
Details
-
File Typepdf
-
Upload Time-
-
Content LanguagesEnglish
-
Upload UserAnonymous/Not logged-in
-
File Pages205 Page
-
File Size-