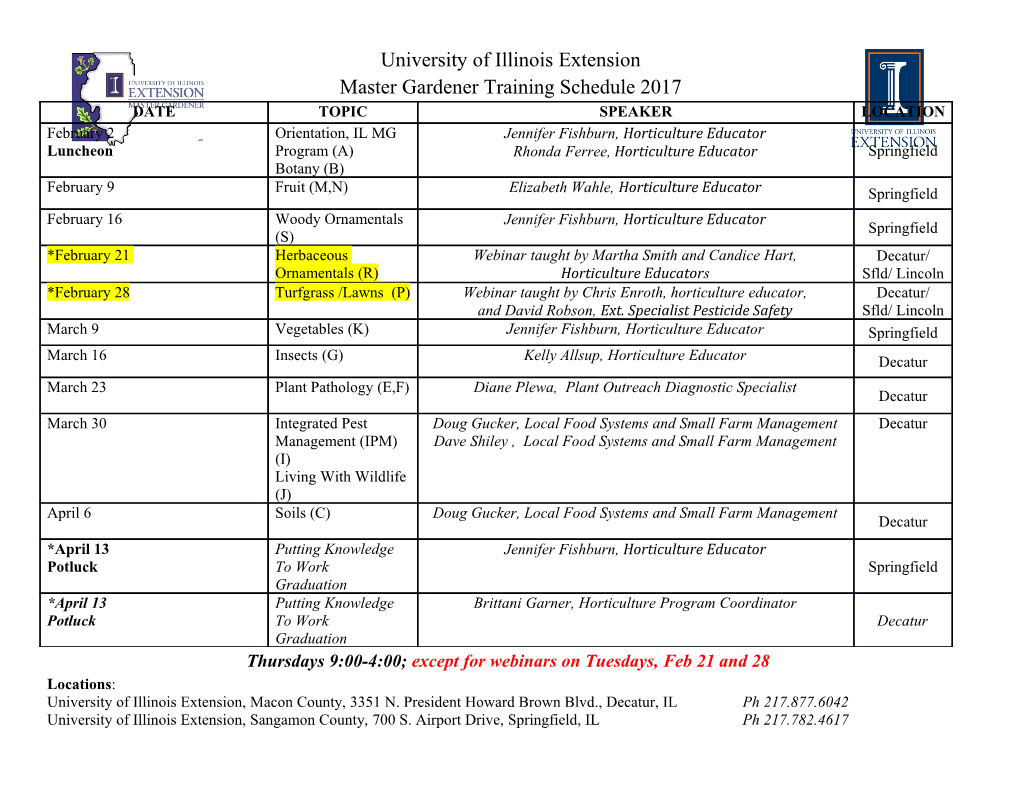
Project No. 11-3212 In-situ Condition Monitoring of Components in Small Modular Reactors Using Process and Electrical Signature Analysis Reactor Concepts Dr. Belle R. Upadhyaya University of Tennessee-Knoxville In collaboraon with: Oak Ridge Naonal Laboratory Timothy Beville, Federal POC Richard Wood, Technical POC In-situ Condition Monitoring of Components in Small Modular Reactors Using Process and Electrical Signature Analysis Final Report – Volume 1 Development of Experimental Flow Control Loop, Data Analysis and Plant Monitoring Report No. NEUP-11-3212-Y3Q4-2014-1 NEUP Contract Number: 00120767 DE-AC07-05IDPS07-07ID14517 Belle R. Upadhyaya (Principal Investigator) J. Wesley Hines (Co-Principal Investigator) Brian Damiano (Collaborator, Oak Ridge National Laboratory) Chaitanya Mehta, Price Collins, Matthew Lish, Brian Cady (Graduate Research Assistants) Victor Lollar, Dane de Wet (Undergraduate Research Assistants) Duygu Bayram (Visiting Scholar) The University of Tennessee Department Nuclear Engineering Knoxville, TN 37996-2300 E-mail: [email protected] TPOC: Richard Wood Federal Manager: Tim Beville December 2014 0 EXECUTIVE SUMMARY In-situ Condition Monitoring of Components in Small Modular Reactors Using Process and Electrical Signature Analysis 1. Background and R&D Objectives For reliable and economic long-term operation of Small Modular Reactors (SMRs), it is imperative that continuous in-situ monitoring of critical equipment must be developed and incorporated in the reactor design phase. This capability is attractive for remote deployment of SMRs with longer fuel cycle duration and for minimizing forced outages, thus enhancing the utilization of these power generating systems in small electric grid environments. These technologies contribute to smart condition-based maintenance, reduced human resources, remote monitoring of reactor components, and autonomous operation. In integral pressurized water reactors (iPWR) and other designs of SMRs, the pressure vessel incorporates most of the critical equipment used for power generation. Examples of such plant components include: steam generators, motors, coolant circulation pumps, motor-operated valves, control rod drive mechanisms (CRDM), in-core instrumentation, and reactor internal structures. The development of these techniques is also important in monitoring critical parameters during severe accidents and for post-accident recovery. Small integral light water reactors have in-vessel space constraints and many of the traditional instrumentation are not practical in actual implementation. In order to resolve this issue, research is being performed to develop techniques for indirect measurement of process parameters. Examples of some of the process measurements of interest are primary coolant flow rate in the reactor vessel, characteristics of motor-driven coolant pumps, water levels in steam generators where the secondary water flows through the steam generator tubing, in a once-through steam generator configuration, and others. The purpose of this NEUP funded research and development project was to develop and demonstrate in-situ equipment monitoring methods for small modular reactors (SMRs) with applications to reactor internals such as coolant pumps, valve-actuators, and control rod drive mechanisms. The overall objective was to integrate electric signature analysis (ESA) and process measurements to perform remote monitoring of SMR components. The primary reactor vessel in a typical SMR has limited space for the installation of control, safety, and system monitoring instrumentation. The focus of this research is to develop monitoring and diagnostics methods 1 using easily accessible measurements. Both experimental and physics-based modeling approaches were developed to establish the feasibility of implementing such techniques and incorporate them during the SMR design phase. Recent activities by light water reactor SMR vendors and developers (NuScale Power, Generation mPower, Westinghouse, CAREM, KAERI, and others) have indicated an increased interest in the development of integral pressurized water reactors for deployment by 2025. SMRs in the 25-200 MWe range are useful for power supply in remote areas, especially in locations with limited infrastructure. SMRs can also be used for co-generation, combining electricity production and process heat for industrial applications, including water desalination. Because of the modular nature of SMRs and limited vessel penetrations, safety and security of such installations are greatly enhanced. The research and development under this project was focused on the following three major objectives: Objective 1: Identification of critical in-vessel SMR components for remote monitoring and development of their low-order dynamic models, along with a simulation model of an integral pressurized water reactor (iPWR). Objective 2: Development of an experimental flow control loop with motor-driven valves and pumps, incorporating data acquisition and on-line monitoring interface. Objective 3: Development of stationary and transient signal processing methods for electrical signatures, machinery vibration, and for characterizing process variables for equipment monitoring. This objective includes the development of a data analysis toolbox. The project tasks were performed in collaboration with the Measurement Sciences and Systems Engineering Division of ORNL. All the tasks and deliverables were completed by the end of the project execution period. 2. Project Technical Summary The following is a summary of the technical accomplishments under this project: A detailed literature review of various SMR types and electrical signature analysis of motor-driven systems was completed. A bibliography of literature is provided at the end of this report. Assistance was provided by ORNL in identifying some key references. A review of literature on pump-motor modeling and digital signal processing methods 2 was performed. An existing flow control loop was upgraded with new instrumentation, data acquisition hardware and software. The upgrading of the experimental loop included the installation of a new submersible pump driven by a three-phase induction motor. All the sensors were calibrated before full-scale experimental runs were performed. MATLAB-Simulink model of a three-phase induction motor and pump system was completed. The model was used to simulate normal operation and fault conditions in the motor-pump system, and to identify changes in the electrical signatures. A simulation model of an integral PWR (iPWR) was updated and the MATLAB- Simulink model was validated for known transients. The pump-motor model was interfaced with the iPWR model for testing the impact of primary flow perturbations (upsets) on plant parameters and the pump electrical signatures. Additionally, the reactor simulation is being used to generate normal operation data and data with instrumentation faults and process anomalies. A frequency controller was interfaced with the motor power supply in order to vary the electrical supply frequency. The experimental flow control loop was used to generate operational data under varying motor performance characteristics. Coolant leakage events were simulated by varying the bypass loop flow rate. The accuracy of motor power calculation was improved by incorporating the power factor, computed from motor current and voltage in each phase of the induction motor. A variety of experimental runs were made for steady-state and transient pump operating conditions. Process, vibration, and electrical signatures were measured using a submersible pump with variable supply frequency. High correlation was seen between motor current and pump discharge pressure signal; similar high correlation was exhibited between pump motor power and flow rate. Wide-band analysis indicated high coherence (in the frequency domain) between motor current and vibration signals. Wide-band operational data from a PWR were acquired from AMS Corporation and used to develop time-series models, and to estimate signal spectrum and sensor time constant. All the data were from different pressure transmitters in the system, including primary and secondary loops. These signals were pre-processed using the wavelet transform for filtering both low-frequency and high-frequency bands. This technique of signal pre- processing provides minimum distortion of the data, and results in a more optimal estimation of time constants of plant sensors using time-series modeling techniques. 3 The experimental loop data indicate a clear relationship between motor power and pump discharge (flow rate). This relationship can be used to infer pump flow rate using the computed motor power. The iPWR physics model was used to simulate normal operation data and operation with faulty sensors, primary coolant flow rate anomaly, and variations in process parameters such as heat transfer coefficients and reactivity feedback coefficients. The iPWR dynamic model was interfaced with the pump-motor model, and this feature was used to introduce variations in the electrical supply frequency and other anomalies in the equipment to simulate their degradation. The iPWR model was extended to include the dynamics of fission product poisoning and its long-term effect on reactor operation. A laboratory scale wireless data acquisition and transmission network was developed and demonstrated successfully. A micro-controller based data acquisition and analysis module was developed and tested for monitoring machinery
Details
-
File Typepdf
-
Upload Time-
-
Content LanguagesEnglish
-
Upload UserAnonymous/Not logged-in
-
File Pages301 Page
-
File Size-