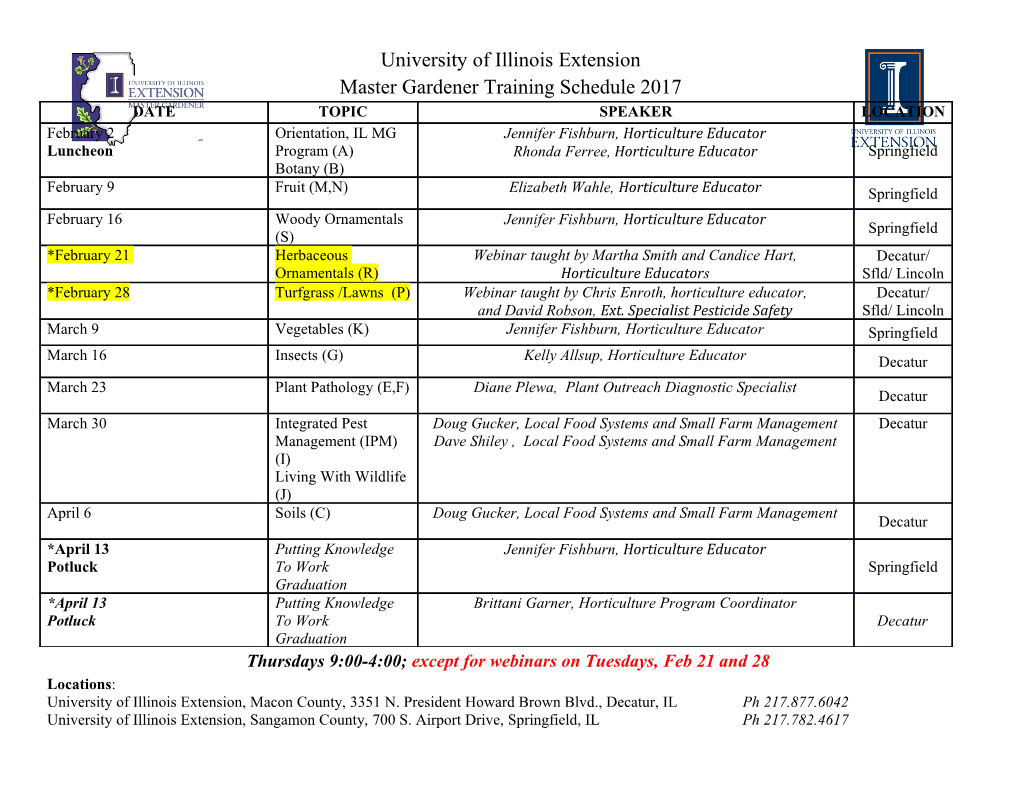
Validating Automotive Frame Torsion Stiffness Measurement Techniques A thesis submitted to the Division of Research and Advanced Studies of the University of Cincinnati in partial fulfillment of the requirements of the degree of Master of Science from the Department of Mechanical and Materials Engineering of the College of Engineering and Applied Science by Alexander Young Bachelor of Science, University of Cincinnati, 2011 13 July 2016 Committee: Randall Allemang, Ph.D., Chair Allyn W. Phillips, Ph.D. David Brown, Ph.D. Abstract The stiffness, particularly torsion stiffness, of a frame, body or chassis is of paramount concern to the automotive structural engineer. An accurate measurement of torsion stiffness has several useful applications, among which are the characterization of construction quality, model calibration and suspension tuning. Static techniques for measuring torsion stiffness are perhaps as old as the automotive industry itself, and each manufacturer has its own version of the classical static torsion stiffness test. It is also common for a manufacturer to quote a new model’s torsion stiffness in industry publications, the values of which continually increase with improving material and construction technologies. In recent years, dynamic methods have emerged which approach the problem of measuring torsion stiffness using experimental frequency response function (FRF) and modal analysis techniques. The primary purpose of this thesis is to further determine the utility of one such dynamic method, namely, the enhanced Rotational Compliance Function (eRCF), in terms of its accuracy in relation to an implementation of the classical static torsion stiffness test. To this end, two automotive frames made by the University of Cincinnati Formula SAE® (UC-FSAE) Team are the test structures. When compared to typical commercial automotive structures, which contain embedded frames and surface shear panels, these steel triangulated frames are considered simple structures. In order to produce quality static values, the UC-FSAE static torsion stiffness measurement apparatus is to be updated and improved. ii iii Acknowledgements I would like to first acknowledge my colleagues in the automotive industry, Jeff Poland of BMW Manufacturing Company, as well as Luc Cremers, Martin Kolbe and Helmut Schneeweiss of BMW-AG, who provided training and years of invaluable access to their expertise in this field. Secondly, I’d like to thank the members of this committee, who have been generous of their time, not only during my graduate work, but also during my work in the automotive industry and as an undergraduate student. Thirdly, I’m indebted to the 2016 UC-FSAE team members who assisted me in the course of this work, particularly Greg Claire, Kristine Huizing, Thomas “Woody” Neumann Stone and Oge Okoh. Fourthly, this thesis would not be possible without Thomas Steed and Hasan Pasha whose work at UC laid its foundation. Lastly, I would like to express my gratitude to my family who were constant sources of encouragement during the course of my graduate work. iv Table of Contents 1 Introduction: Torsion Stiffness and Its Importance to the Automotive Structure 1 2 Background and Theory 9 2.1 The Static Torsion Stiffness Test 9 2.2 The Enhanced Rotational Compliance Function 15 3 Results and Discussion 22 3.1 Results: Static 22 3.2 Results: eRCF 27 4 Calibration of a Finite Element Model 34 5 Conclusions and Recommendations 40 References 43 Appendix 45 A1 Quarter-car Model Parameters 45 A2 TSMM Parts 46 A3 eRCF Formulation 53 A4 eRCF MPE 55 v List of Figures 1.1 Hooke’s Law 1 1.2 Springs in Series 5 1.3a Quarter-car Model with Rigid Body 6 1.3b Quarter-car Model with Compliant Body 6 1.4 Acceleration due to Road Input and the Effect of Body Stiffness 7 2.1.1 Typical Static Torsion Test Configuration 9 2.1.2 UC-FSAE 2016 Frame Static Torsion Stiffness Testing 11 2.1.3a UC-FSAE 2016 Frame Node Block Attachment to I-beam 12 2.1.3b UC-FSAE 2016 Frame Node Block Model 12 2.1.4a One Corner of TSMM with PCB® Load Cell 12 2.1.4b One Corner of TSMM Exploded View 12 2.1.5 UC-FSAE Static Torsion Stiffness Test Configuration 13 2.2.1 eRCF Configuration 16 2.2.2 FRFs to eRCF: Enhancement and Scaling 18 2.2.3 Portion of eRCF Used in MPE Part 1 19 2.2.4 Portion of eRCF Used in MPE Part 2 19 2.2.5 eRCF Model Elements 20 3.1.1 UC-FSAE 2014 Frame Static Torsion Stiffness Hysteresis Loops 22 3.1.2 UC-FSAE 2016 Frame Static Torsion Stiffness Hysteresis Loops 23 3.1.3 UC-FSAE 2016 Hub-to-hub Static Torsion Test 24 3.1.4 UC-FSAE 2016 Hub-to-hub Static Torsion Stiffness Hysteresis Loops 25 3.2.1 PCB® Modal Impact Hammers 27 3.2.2 UC-FSAE 2014 eRCF Model and Static Stiffness Estimate 28 3.2.3 UC-FSAE 2016 eRCF Model and Static Stiffness Estimate 30 vi 3.2.4 UC-FSAE 2014 Frame as Springs in Series 32 4.1 UC-FSAE 2016 ANSYS® Model Mesh 36 4.2 MAC for FEA vs EMA Mode Shapes 38 vii List of Tables 3.1.1 UC-FSAE 2014 Frame Static Torsion Stiffness Results 23 3.1.2 UC-FSAE 2016 Static Torsion Stiffness Results 24 3.1.3 UC-FSAE 2016 Hub-to-hub Static Torsion Stiffness Results 25 3.2.1 eRCF MRIT DSP Parameters 28 3.2.2 UC-FSAE 2014 Frame eRCF Static Estimates Based on Varying 29 Frequency Bands 3.2.3 UC-FSAE 2016 Frame eRCF Static Estimates Based on Varying 30 Frequency Bands 3.2.4 UC-FSAE 2016 Frame Two-sided SDOF Static Compliance 31 (x105) 3.2.5 UC-FSAE 2016 Frame Residual Flexibility Static Compliance 31 (x105) 3.2.6 UC-FSAE 2014 Frame Springs in Series Calculated vs. 32 Measured 4.1 FE Model Calibration Steps 34 4.2 First Iteration of FE Model Material Properties 37 4.3 Final Iteration of FE Model Material Properties 37 4.4 Hub-to-hub Stiffness Comparison 39 5.1 Comparing Section Rigidity 42 viii 1 Introduction: Torsion Stiffness and Its Importance to the Automotive Structure In his seminal paper “Of Springs” (“De Potentiâ Restitutiva”), published in 1678, Robert Hooke summarized his experiments using various elastic wires, springs and weights, observing, “It is very evident that the Rule or Law of Nature in every springing body is, that the force or power thereof to restore itself to its natural position is always proportionate to the distance or space it is removed therefrom, whether it be by rarefaction…of its parts the one from the other, or by a Condensation…of those parts nearer together [1].” Hooke’s Law, as it is commonly known, is the first order relationship between force and deformation, stated mathematically, = 1.1 Figure 1.1: Hooke’s Law The proportionality constant, K, is known as stiffness and is equivalent to the force (tension or compression) required to produce a given deformation (elongation or shortening); thus, its units are force per length [F/L]: 1 1.1a = Hooke’s Law applies to torsional springs as well, where the torsion stiffness units are moment (or torque) per angle of twist ([F-L/RAD] or [F-L/DEG]): 1.2 = Hooke also concluded that linear springs are important components of harmonic motion, and his work in this field laid the foundation for the mechanics of elastic bodies. In mechanics of materials, the angle of twist due to an applied torque on a shaft is a function of its length, shear modulus, G, and polar moment of inertia, J: 1.3 = The equation can be rearranged in terms of torque per stiffness yields the familiar torsion stiffness constant. It is then clear that the stiffness decreases as the length of the section increases [2]. 1.3a = 1.3b = = = With the advent of the industrial revolution, the concept of stiffness went from a subject of academic inquiry to myriad applications, an enduring example being the automobile structure. The horse-drawn carriage may seem the obvious structural forerunner to the modern automobile, however, the development of the bicycle played an equal, if not more important, 2 role. The bicycle was the first mass produced mode of self-transportation, and immediate attention was given to producing a lightweight structure in order to reduce the energy expended by the rider. In the 1870s alone, the bicycle industry saw such innovations as the tangential- spoked wheel, differential gearing (for tricycles) and triangulated tubular frame construction. In addition, better paved roads and a demand for motorized self-transportation were direct consequences of the popularity of the bicycle. In 1895, the Englishman, F. W. Lanchester, made the first attempt to design a chassis, made of brazed steel tubes, which could carry engine and powertrain while still providing a solid floor for the passenger compartment. In the following two decades, as the popularity of the horseless carriage grew, innovations in mass production, steel and the oil and gas industry were seen. By the end of the 1920s, comfort was becoming important to the average car buyer who now demanded an enclosed passenger compartment. Such comforts challenged the automotive structural designer who needed to keep weight down, and the answer came in the form of improved sheet metal quality and forming techniques. Similar challenges were addressed in the 1930s as the customer began to desire aesthetically pleasing vehicles which meant long and low bodies with flowing lines. In the 1930s, the unit-body or unibody design became an alternative to the frame-over-chassis design.
Details
-
File Typepdf
-
Upload Time-
-
Content LanguagesEnglish
-
Upload UserAnonymous/Not logged-in
-
File Pages64 Page
-
File Size-