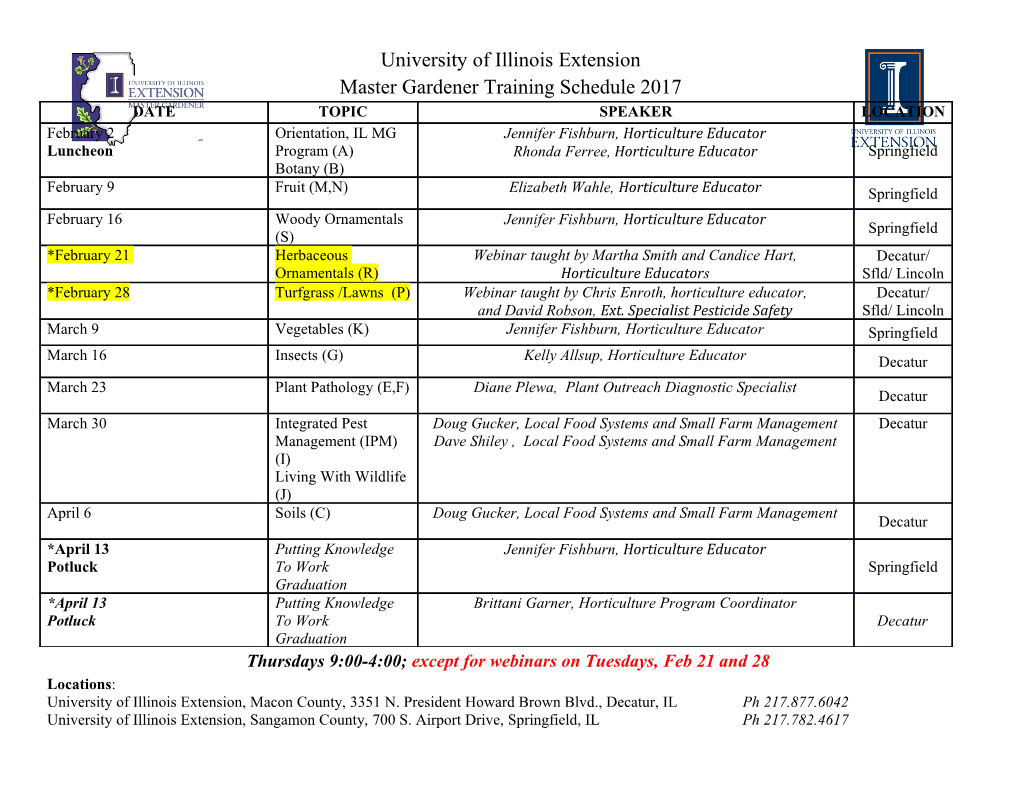
EKOENERGETIKA 4/2018 UOT 678.742 THE PHYSICAL PROPERTIES OF BIOPOLYMERS Ilh.I.Abbasov1 , I.I.Abbasov2, Edmundas Kibirkstis1 1Kaunas University of Technology, 2Azerbaijan State University of Oil and Industry Keywords: Biopolymers, optical density, polysaccha- rides , proteins, polyhydroxyalkanoate (PHA) The classification of biopolymers was given and some biopolymers were described more in detail in this ar- ticle. Some physical properties of biopolymers are mentioned and compared to simple polymers in this article. The optical density of biopolymers is mainly learnt and discussed. 1. Types of biodegradable polymers ma- There are four types of biodegradable polymers: terials coming from agro-resources (Polysaccharides, The classification of biodegradable materials is Proteins) which are called biomass products, shown in the Fig.1 Biopolymers (the full name is coming from microorganisms (polyhydroxyalka- biodegradable polymers) differ from the other noate), Polylactides (PLA) which is obtained by plastics by the possibility of decomposition into using biotechnology and synthesis from renewa- microorganisms by chemical, physical or biologi- ble resources. As it can be seen from Fig.1 Poly- cal impact. These properties of biodegradable caprolactone (PCL) is obtained through classical polymers will be solution for waste problem. chemical synthesis way [1]. Fig. 1 The classification of biodegradable materials [1] ➢ Polysaccharides yesters as the basis of Alpha hydroxy acid. Amer- Starch based polymers are obtained by extraction ican company Metabolix and Procter & Gambler from plant raw materials with subsequent modifi- are stressing out on this area [4] cation. Cellulose based polymers are obtained ➢ Polylactides (PLA) through modification of natural raw material or One of the most perspective biopolymers are the bacterial fermentation [2]. polymers of milk acid-Polylactide (PLA), a raw ➢ Proteins material for the production of which is maize, Natural high molecular weight organic com- Saccharum officinarum and rice etc. There are pounds, built from the residues of 20 amino acids, two ways to obtain PLA from Lactic Acid – di- which are linked by peptide bonds into long rect polycondensation of lactic acid and the chains [3]. polymerization of disclosure of cyclic lactide [4]. ➢ Polyhydroxyalkanoate (PHA) ➢ Polycaprolactone (PCL) The other technological area biopolymers-the Polycaprolactone (PCL) is caprolactone poly- production of polyhydroxyalkanoates (PHA ab- mers. It has a good resistance to water, oils and breviation) belonging to the type of aliphatic pol- solvents. Moreover, it has low viscosity and easi- 7 EKOENERGETIKA 4/2018 ly processed. It can be blended with starch to re- photo elastic method of the stress analysis. This duce the cost and to increase the biodegradability. method was applied to check the residual stress Also, PCL decomposes under physiological con- distribution in polymeric films. ditions (for example in the human body) and Photo elasticity is the display of optical anisotro- therefore received much attention as an implanta- py in isotropic solids under mechanical stress [7]. ble biomaterial [5]. The non-destructive photoelasticity method was 2. The research of biodegradable polymeric applied by testing the character of residual stress- films their properties, characteristics and es distribution in polymeric film material [8]. equipment The views of the distribution of polymeric films Preparation of investigated specimens of bio- residual stresses were captured using colour cam- degradable materials era EO-1312c.The quantitative evaluation of the All specimens are manufactured using extruder stresses, having in mind the mathematical point SJM 35-400. 36 specimens were obtained. of view, was complex thus only qualitative analy- [6]. sis of stresses was carried out in this work [8]. Polymeric films were manufactured using the fol- Optical density testing method and equip- lowing compositions [6]: ment • Pure low-density polyethylene (referred as Proof printing was carried out for samples with- LDPE); out additional surface treatment (virgin surface • LDPE + 3% potato starch + 1% glycerine (re- tension) and with additional treatment by setting ferred as LDPE1); the power at 70 W/min/m2. Such value of power • LDPE + 3% potato starch + 1% glycerine + was selected considering the recommendations of 10% itaconic acid (referred as LDPE2); flexographic printing machine operators from • LDPE + 5% potato starch + 1% glycerine + Lithuanian printing houses. The surface tension 10%itaconic acid (referred as LDPE3); of polymeric materials was increased by using the • LDPE + 2% molasses (dry) + 1% glycerine (re- corona discharge device “Vetaphone Corona- ferred as LDPE4); Plus”. The densitometer “X-Rite Colour” was • LDPE + 2% molasses (liquid) + 1% glycerine used to determine optical density and microscopic (referred as LDPE5). analysis was carried out using the optical micro- The outer view of biodegradable materials Low scope “AM2111 Dino-Lite basics” [9]. Density Polyethylene + Sorbitol (10 %), Low Printability testing results Density Polyethylene + Chitosan (3 %) and Low Polymeric samples were printed using Flexiproof Density Polyethylene + Molasses liquid (3 %) are 100/UV” [6] printing tester and optical density given in the picture was tested with the Spectrodensitometer “X-Rite Research equipment and methods of study of Colour”. Polymeric films were analysed under the biodegradable polymers optical microscope “AM2111 Dino-Lite basics” LDPE, Glycerine 1 %, Molasses (dry) -2%; was used. The results of optical density analysis LDPE, Molasses liquid 2%, Glycerine 1 %; Pure of the researched polymeric film prints are pre- LDPE; PEVD + Chitosan (3%); LDPE + Sorbitol sented in Table 2. [9]. (10 %); LDPE+ Molasses liquid were used for the Table 2. Optical density results [6] Polymeric film Optical density,D Without Surface treatment 70 W/min/m2 surface treatment LDPE 1.23 1.23 LDPE1 1.22 1.22 LDPE2 1.03 1.03 LDPE3 0.83 0.83 LDPE4 0.78 0.78 LDPE5 0.95 0.95 The optical density value of LDPE 1 (D=1.22) 70 W/min/m2 surface treatments. But, the values polymeric film is the highest except LDPE of LDPE 4 (D=0.78) polymeric film are the low- (D=1.23) polymeric film under without and with est compare to LDPE2 (D=1.03), LDPE3 8 EKOENERGETIKA 4/2018 (D=0.83) and LDPE5(D=0.95). [9] The micro- face treatment are shown in Fig. 3.raggedness of photographs of 100% colour patch of microscopic graphic elements etc.). analysis of all tested polymeric films without sur- LDPE LDPE1 LDPE2 LDPE3 LDPE4 LDPE5 Fig.3 The microphotographs of 100% colour 13% for LDPE2 sample and 35% for LDPE3 patch of microscopic analysis of all tested poly- sample. Also, and the layer of inks on surfaces of meric films without surface treatment [6] LDPE 2 and 3 was more solid than before treat- The microphotographs of 100% colour patch of ment. But it could be stated that these two poly- LDPE 1 show that UV inks were inked on surface meric films still require improvement of the man- qualitative. The measured values of optical densi- ufacturing process by changing the parameters of ty of LDPE2 and LDPE3 samples were insuffi- extruder, composition of material and concentra- cient as recommended for UV flexography print- tion of additives. In conclusion, the optical densi- ing (see Table 2). As can be seen from micropho- ty result of LDPE 1 is comparable to traditional tographs shown in Fig.3 and Fig.4 the inking BOPP polymeric films quality of LDPE2 and LDPE3 surfaces was worse Thus, the next step for using this polymeric film than LDPE1. Especially for LDPE3 as the UV for flexography printing should be print quality inks did not form a solid layer but were tended to assessment using the geometrical parameters cri- contract itself into the shape of a drop. Additional teria approach (accuracy of raster dots, the rag- surface treatment increased optical density by gedness of graphic elements etc.). LDPE LDPE1 LDPE2 LDPE3 LDPE4 LDPE5 Fig.4 The microphotographs of 100% colour patch of microscopic analysis of all tested polymeric films with surface treatment 70 W/min/m2[6] 9 EKOENERGETIKA 4/2018 Of course, the final optimization of this new pol- polymer packing materials was carried ymeric film for packaging purposes requires more out. detailed researches considering to mechanical The final optimization of these new de- characteristics (tensile strength, elongation at veloped polymeric films for packaging break, seal strength, coefficient of friction and purposes requires more detailed research- other), barrier properties (permeability to water es for further use of these polymeric films vapour, oxygen, ink migration and other) [9]. in packaging processes and improvement Conclusion of their manufacturing process. But con- Analytical review of packaging materials sidering to the already carried out re- for food based on principles of green en- searches, the LDPE 4 polymeric film con- gineering was carried out. taining dry molasses and glycerin addi- Research of physical-mechanical charac- tives has demonstrated the most encourag- teristics and parameters of biodegradable ing results to be used as biodegradable packaging material. Referenc 1. Biodegradable Polymers https://www.slideshare.net/Imaad08/biodegradable-polymers-25995228 (vis- ited 25.12. 2016) 2. Taseekeev M.S., Yeremeeva L.M. Production of biopolymers as one of the ways to solve the problems of ecology and apk Analytical review Almaty 2009 National Center for Scientific and Technical Infor- mation
Details
-
File Typepdf
-
Upload Time-
-
Content LanguagesEnglish
-
Upload UserAnonymous/Not logged-in
-
File Pages123 Page
-
File Size-