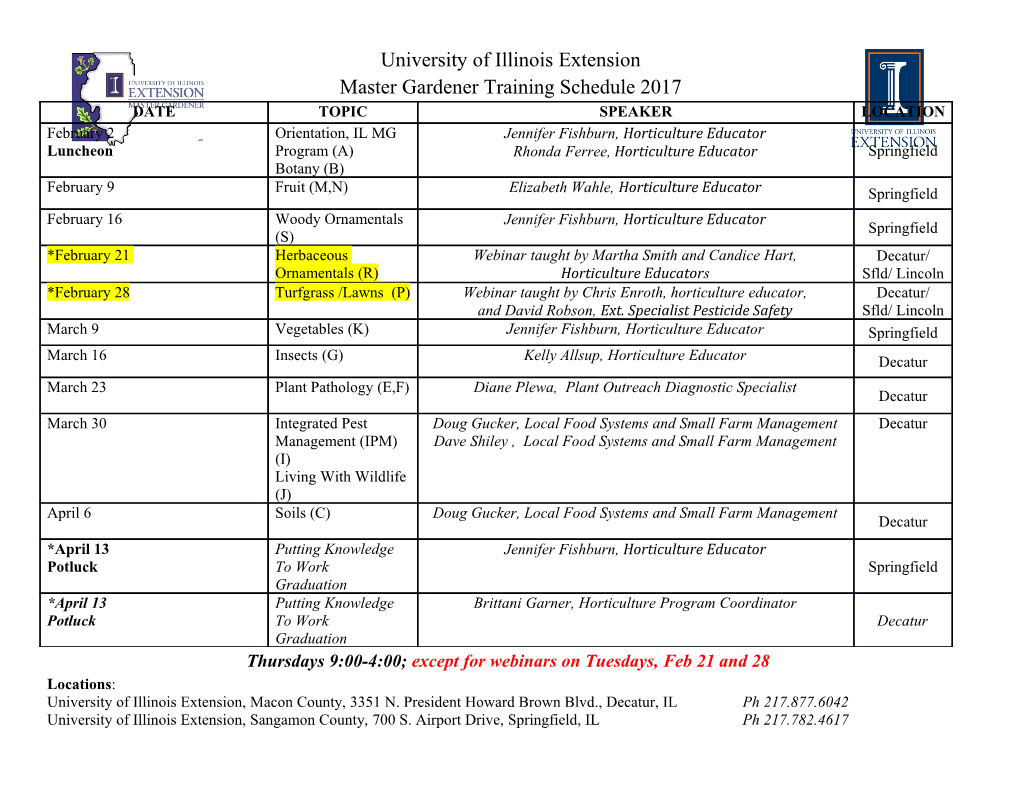
See discussions, stats, and author profiles for this publication at: https://www.researchgate.net/publication/309960723 Structural life enhancement on friction stir welded AA6061 with optimized process and HFMI/PIT parameters Article in The International Journal of Advanced Manufacturing Technology · June 2017 DOI: 10.1007/s00170-016-9697-7 CITATIONS READS 4 43 3 authors, including: Yupiter HP Manurung Mohamed Ackiel Universiti Teknologi MARA Serba Dinamik Group Berhad 78 PUBLICATIONS 453 CITATIONS 16 PUBLICATIONS 66 CITATIONS SEE PROFILE SEE PROFILE Some of the authors of this publication are also working on these related projects: Spot weld View project All content following this page was uploaded by Mohamed Ackiel on 22 June 2018. The user has requested enhancement of the downloaded file. Structural life enhancement on friction stir welded AA6061 with optimized process and HFMI/PIT parameters Yupiter H. P. Manurung, Mohamed Ackiel Mohamed & Azrriq Zainul Abidin The International Journal of Advanced Manufacturing Technology ISSN 0268-3768 Int J Adv Manuf Technol DOI 10.1007/s00170-016-9697-7 1 23 Your article is protected by copyright and all rights are held exclusively by Springer- Verlag London. This e-offprint is for personal use only and shall not be self-archived in electronic repositories. If you wish to self-archive your article, please use the accepted manuscript version for posting on your own website. You may further deposit the accepted manuscript version in any repository, provided it is only made publicly available 12 months after official publication or later and provided acknowledgement is given to the original source of publication and a link is inserted to the published article on Springer's website. The link must be accompanied by the following text: "The final publication is available at link.springer.com”. 1 23 Author's personal copy Int J Adv Manuf Technol DOI 10.1007/s00170-016-9697-7 ORIGINAL ARTICLE Structural life enhancement on friction stir welded AA6061 with optimized process and HFMI/PIT parameters Yupiter H. P. Manurung1 & Mohamed Ackiel Mohamed2 & Azrriq Zainul Abidin3 Received: 5 September 2016 /Accepted: 3 November 2016 # Springer-Verlag London 2016 Abstract This novel study presents an unconventional ap- 65, 25 and 10% for air pressure, impact frequency and indent- proach to find the best governing process parameters of high er diameter, respectively. Secondly, using subsequent post- frequency mechanical impact technique based on multi- weld mechanical treatment, the life cycle number can be ex- objective optimization method. In this investigation, the tended up to 12 times on friction-stirred weld. Finally, based post-weld mechanical treatment is aimed to enhance fatigue on the experimental confirmation test, the proposed method resistance of structural friction-stirred weld subjected to fluc- can effectively estimate the structural life and surface hardness tuating loads by obtaining nominal sub-surface hardness. The within the acceptable range of relative error. experimental study was conducted on aluminium alloy AA 6061 with thickness of 6 mm under varied parameters centred Keywords Fatigue life . Friction stir welding (FSW) . High on indenter diameter, air pressure and impact frequency. The frequency mechanical impact (HFMI) . Pneumatic impact investigation began with obtaining optimum parameters for treatment (PIT) . Optimization single response by using conventional Taguchi method with L9 orthogonal array. Next, advanced optimization approach by means of multi-objective Taguchi method attempts to con- 1 Introduction sider the multiple responses simultaneously which are sub- surface hardness and structural life. As the final results, the The friction stir welding (FSW) process is witnessing a optimum value was acquired by calculating the total normal- growth in a wide range of industrial applications due to the ized quality loss and multiple signal-to-noise ratios based on minimal governing parameters and many other advantages as unequal desirability. The significant level of the parameters a solid state welding compared to the commonly used fusion was evaluated by using analysis of variance. Furthermore, welding process. However, tensile residual stress remains to the second-order model for predicting the objectives was de- be significant concern due to its extensive clamping and stir- rived by applying response surface methodology. It can be ring process which can lead to lower fatigue resistance partic- summarized that, first, the affecting parameters to obtain su- ularly in structures subjected to fluctuating loads triggering a perior structural life can be ordered at significant level of ca. need for improvement [1–3]. The enhancement of the fatigue resistance of welded joints is becoming increasingly significant in many areas such as the * Yupiter H. P. Manurung railway, aerospace and automotive industries. A recent meth- [email protected] od of enhancing the fatigue resistance of welded aluminium alloy (AA) structures is to use modern post-weld treatment 1 Faculty of Mechanical Engineering, Universiti Teknologi MARA processes. Improving the fatigue resistance of welded joints (UiTM), Shah Alam, Malaysia by conventional improvement methods such as grinding, shot 2 Universiti Kuala Lumpur Malaysia France Insitute (UNIKLMFI), peening, air hammer peening or tungsten inert gas (TIG) Kuala Lumpur, Malaysia dressing are well established. However, these techniques are 3 Technogerma Engineering & Consultancy, Mont Kiara, Kuala inconsistent, not always efficient, have limited application Lumpur, Malaysia areas and can cause other related problems. The relatively Author's personal copy Int J Adv Manuf Technol new technique of high frequency mechanical impact (HFMI) most possible minimum value of process performance at the peening of weld toes as well as heat affected zones offers a optimum point of process parameters. Numerous researches favourable alternative for weld improvement. HFMI is termed involving the optimization of process parameters for FSW as a method in which a hardened steel pin impact on the surface well as other welding processes had been carried out previ- of the metal to be treated at a required frequency and pressure ously to obtain the optimal point of governing parameters by magnitude in accordance to specifications. employing the multi-objective Taguchi method (MTM) and There are a quite number of research conducted using con- response surface methodology (RSM). A mathematical model ventional and HFMI methods in the past decades. Rodopoulos was successfully developed for quality features of resistance et al. [3] investigated through experimental study the effects of spot welding [10]. A hybrid TM using the Taguchi quality loss ultrasonic impact treatment (UIT) on the fatigue resistance of function and RSM was employed for the multi-response opti- friction stir welded AA panels. The effects of laser and shot mization of a laser beam cutting process [11]. TM has been peening on the mechanical properties with iso-stress assump- successfully applied to determine the optimal FSW process tion were studied by O. Hatemleh [4] to calculate local stress– parameter combination that would maximize the tensile strain curves of friction stir welded 2195 AA joints. A signif- strength, notch tensile strength and the weld sub-surface hard- icant improvement in the fatigue resistance of friction stir ness of the AA6061 joints by Periyasamy et al. [12]. TM was welded AA7075 by applying ultrasonic peening (UP) was also effectively used to optimize the process parameters of reported out by Qiulin et al. [5] using a self-made device with FSWAA6061 in an attempt to minimize the heat affected zone a stress ratio of R = 0.5. The strengthened layer caused by the (HAZ) distance to the weld line [13]. The prediction of the plastic variation, surface hardening and consistency of tissue, optimum tensile strength by varying process parameters for as well as compressive transversal residual stress induced by joining of a butt joint dissimilar Al–Cu alloy AA2219 and UP were found to be the main reasons for the increased life AA5083 plates using TM technique was investigated by cycle. Microstructural and fatigue properties of FSW made of Koilraj et al. [14]. AA2043 with controlled shot peening was examined by Ali Based on past researches, it is obvious that fatigue strength et al. [6] and stated that the compressive residual stress intro- of material can be improved significantly with the help of duced by the peening process attributed to an increment in the various methods including HFMI and process parameter op- low cycle region. In an attempt to restore the degraded fatigue timization is an important criterion prior to the application of performance due to FSW, laser peening without coating welding and cutting process. However, no attempt has been (LPwC) was applied to FSW AA6061 joints by Sano et al. made yet to employ multi-objective parameter optimization [7] and obtained an increment of 30 MPa from an as-welded for FSW with subsequent post-weld treatment especially value of 90 MPa. It was pointed that a higher fatigue perfor- using the recently innovated pneumatic impact treatment mance can be expected if the processing parameters in LPwC (PIT) which also falls under the generic term of HFMI method were optimized. The effect of HFMI on butt welds, T-joints as mentioned in [15 ]. As first hypothesis in achieving opti- and longitudinal attachments for mild construction steel mum
Details
-
File Typepdf
-
Upload Time-
-
Content LanguagesEnglish
-
Upload UserAnonymous/Not logged-in
-
File Pages12 Page
-
File Size-