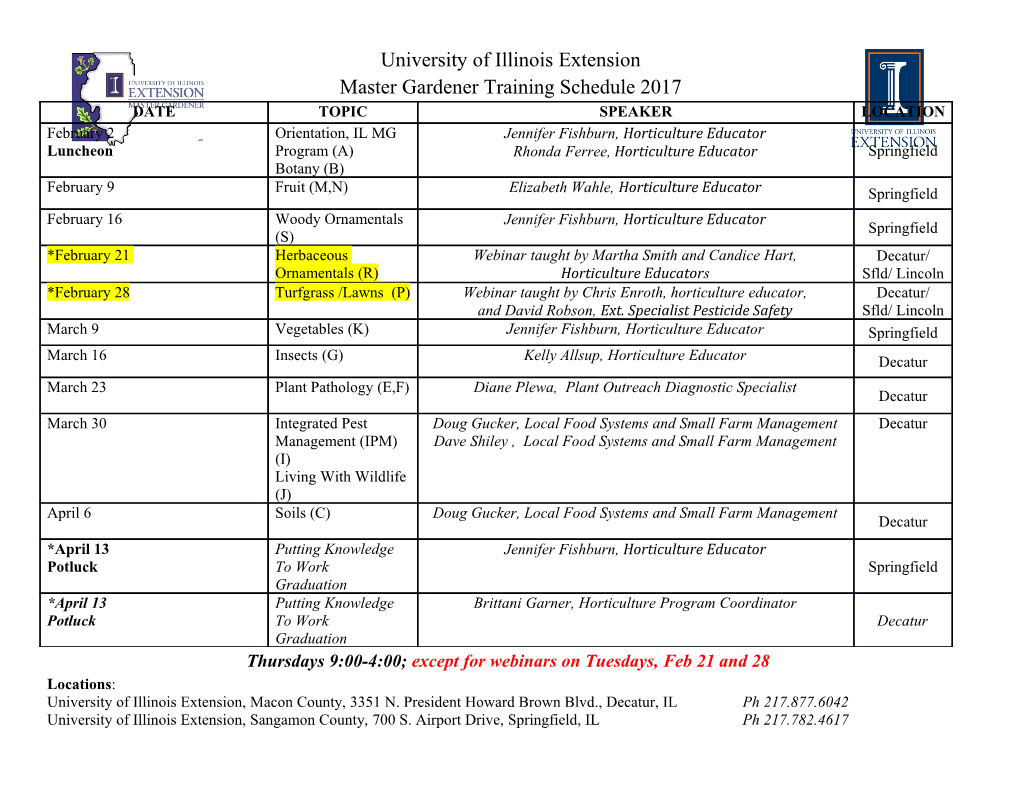
DEGREE PROJECT IN ENGINEERING PHYSICS, SECOND CYCLE, 30 CREDITS STOCKHOLM, SWEDEN 2020 Evaluation of drag estimation methods for ship hulls HAMPUS TOBER KTH ROYAL INSTITUTE OF TECHNOLOGY SCHOOL OF ENGINEERING SCIENCES Abstract This study aims to evaluate to which degree CFD can complement traditional towing-tank experiments, and to develop a computationally cheap and robust methodology for these type of simulations. Two radically different surface ship hulls were chosen for the trials: a capesize bulk carrier and a fast displacement hull. A bare submarine hull was also used to benchmark the software in the early stages of the study. All simulations were Reynolds–Averaged Navier–Stokes (RANS) simulations using the k-!-SST turbulence model. The chosen software was OpenFOAM 5.x and foam-extend 4.1 coupled with the commercial expansion Naval Hydro Pack, which is supposed to handle high Courant numbers well. Producing a high-quality mesh which is able to capture both the free surface and the boundary layers proved to be of utmost importance and the meshing procedure is thus discussed in detail. A majority of the surface ship simulations suffered from a phenomenon known as numerical ventilation. The effect seemed to be much worse for the fast-displacement hull and the drag estimates for this hull deviated around 16.1% from experimental data. The bulk carrier was less affected and the drag estimates for this hull only deviated around 6.3% from experimental data. In order to reduce the computational cost, all surface ship simulations were run with a maximum Courant number of 25 and some consequences of this are also discussed. Acknowledgements I would like to express my greatest appreciation to Marcus Winroth and Mattias Liefvendahl for their patient guidance and unparalleled support throughout this project. I would like to thank everyone from the departments of Underwater Technology and Naval Systems for welcoming me to FOI and for making me feel like part of the group. I would also like to thank Ricardo Vinuesa for all the good feedback and comments I’ve gotten throughout the project. Finally I want to thank Director Nobuyuki Hirata of the National Maritime Research Institute in Japan for providing me with data and answering my questions about his papers. Contents 1 Introduction 1 1.1 Submarines . .1 1.2 Surface Ships . .3 1.3 Ship terminology . .4 1.4 Semi-Empirical Methods . .5 1.5 Fluid Mechanics . .6 1.6 Pressure Gradient Flows . .6 1.7 Turbulence . .6 2 Cases 7 2.1 Case 1: Joubert Bare Hull . .7 2.2 Case 2: Japanese Bulk Carrier . 10 2.3 Case 3: MARIN Systematic Series FDS-5 . 12 3 Method - Computational Fluid Mechanics 14 3.1 RANS . 14 3.2 Eddy viscosity models . 15 3.3 Solving algorithm . 16 3.4 Wall functions . 18 3.5 Two-phase flows . 18 3.6 Rigid Body Motion . 19 4 Computational Setup 20 4.1 OpenFOAM . 20 4.2 Meshing . 20 4.3 Case 1: Joubert Bare Hull . 21 4.4 Case 2: Japanese Bulk Carrier . 24 4.5 Case 3: MARIN Systematic Series FDS-5 . 29 5 Results 32 5.1 Case 1: Joubert Bare Hull . 32 5.2 Case 2: Japanese Bulk Carrier . 35 5.3 Case 3: MARIN Systematic Series FDS-5 . 45 6 Conclusions 50 6.1 Case 1: Joubert Bare Hull . 50 6.2 Surface Ships . 50 6.3 Summary . 52 6.4 Outlook . 52 Appendices 55 A Meshes 55 B Residuals 63 1 Introduction Traditional towing-tank tests are notoriously complex to perform. First an accurate scale model of the ship hull needs to be manufactured, where parameters such as displacement, weight distribution and surface geometry will be sources of error. The next step is to design a measurement campaign where the model is tested under the right conditions. Here the measurement devices, and possibly the testing facilities will introduce errors to the measurements. Finally the data needs to be scaled up to give estimates of the performance of the full scale ship and this process will both introduce new errors and possibly scale up the previously mentioned errors. For these reasons, towing tank tests can easily become very expensive and are usually only performed near the end of the design campaign. A numerical towing tank based on Computational Fluid Dynamics (CFD) could instead allow evaluations of designs multiple times during the design process. See [1] for a relatively recent summary of state of the art numerical ship hydrodynamics. Simulations of full-scale ships would most likely be too computationally expensive due to the high Reynolds numbers and large meshes, but it would be possible to run simulations of models of different scales to further investigate how the final results can be scaled up as accurately as possible. When developing the simulation methodology emphasis was put on keeping down computational costs to allow entire series of hull forms to be tested within a reasonable time frame. In order to ensure that the methodology would work for many different types of ships three vastly different hull types were tested, one high speed displacement hull, one bulk carrier hull belonging to the largest class of bulk carriers and one bare submarine hull. The software chosen as basis for the numerical towing tank was the open source finite volume based software OpenFOAM. 1.1 Submarines The idea of submarines has been around for hundreds of years but it wasn’t until the end of the 18th century that working prototypes were built, the first being Bushnell’s Turtle followed by Fulton’s Nautilus. These early submarines were man-powered military vessels designed for the purpose of planting explosive charges on the underside of warships. Although the vessels were technologically advanced for their time, they had little to no success. Major strides in submarine technology were made over the course of the 1800s and by the end of the century the Holland-class submarine was designed for the British Royal Navy by John Philip Holland. The Holland-class had many features of modern submarines and was powered by a petrol engine coupled with an electric motor. However it was during the 20th century that the development of submarines really took off, mainly due to the two world wars. Many of the early military submarines were however optimized for surface operation and little attention was given to underwater performance. 1 Figure 1: Top: German Type VII-C U-boat (1930s) Bottom: German Type XII U-boat (1940s) Towards the end of the Second World War German designers started to realize the improvements in underwater performance that could be gained by streamlining the hull and removing appendages. The difference in design philosophy can be seen by comparing the earlier Type VII with the later Type XII [2] (see Figure 1). After the war both the British and American navies obtained Type XII’s for evaluation and were stunned by the technological advances that the Germans had made. Their subsequent designs, the British Porpoise-class and American Tang-class, were heavily influenced by the German submarine [3] [4]. Modern day submarines are even more streamlined and are usually based around an axisymmetric base hull, such as the Joubert Bare Hull which is discussed in Chapter 2. 1.1.1 Resistance The resistance acting on a body moving through a 1-phase fluid (constant density) is usually divided into two components, pressure resistance (or form resistance), Rp, and frictional resistance,Rf . Pressure resistance: Since all fluids are viscous to some degree there will be a boundary layer on all surfaces of the body in contact with the fluid. This disrupts the fore-aft symmetry of the pressure acting on the body, resulting in a net drag force known as the pressure resistance. Frictional resistance: The no-slip condition at the surface of the submarine means that the fluid counteracts the movement of the body by exerting tangential shear forces on the surface as it moves forward. The resulting drag coming from these shear forces is referred to as the frictional resistance These resistances are often scaled with the dynamic pressure acting on the body to produce the non-dimensional coefficients Cp and Cf . The scaling is done according to Rp C = (1) p 1 2 2 ρu1S and similarly for Cf , where ρ is the density of the fluid, u1 is the inflow velocity and S is a characteristic area which in this study will be taken as the wet area of the submarine. We want to emphasize that Cp, in this study, refers to the streamwise (x) component of the pressure coefficient. Furthermore, when the coefficients are written with capital letters such as Cp this refers to the integral of the local coefficient values over the entire body, according to Z Cp = cp dSh ; (2) Sh where Sh is the area of the hull and cp is the local coefficient. 2 1.2 Surface Ships Unlike submarines, surface ships have been around for thousands of years and even the earliest designs showed some understanding of ship hydrodynamics. Up until the invention of propeller driven ships it was however not as important to estimate the hydrodynamic drag on the hull. In order to properly dimension the propulsion system of a ship it is crucial to have a good estimate of its resistance at design speed, so when the first steamships were developed in the mid 1800s this immediately became a problem and many of the early propeller driven ships thus had badly dimensioned propulsive systems. In the 1870s William Froude started developing methods for estimating the resistance of full scale ships. He experimented with scale models and performed towed resistance tests using planks of different length and surface texture.
Details
-
File Typepdf
-
Upload Time-
-
Content LanguagesEnglish
-
Upload UserAnonymous/Not logged-in
-
File Pages74 Page
-
File Size-