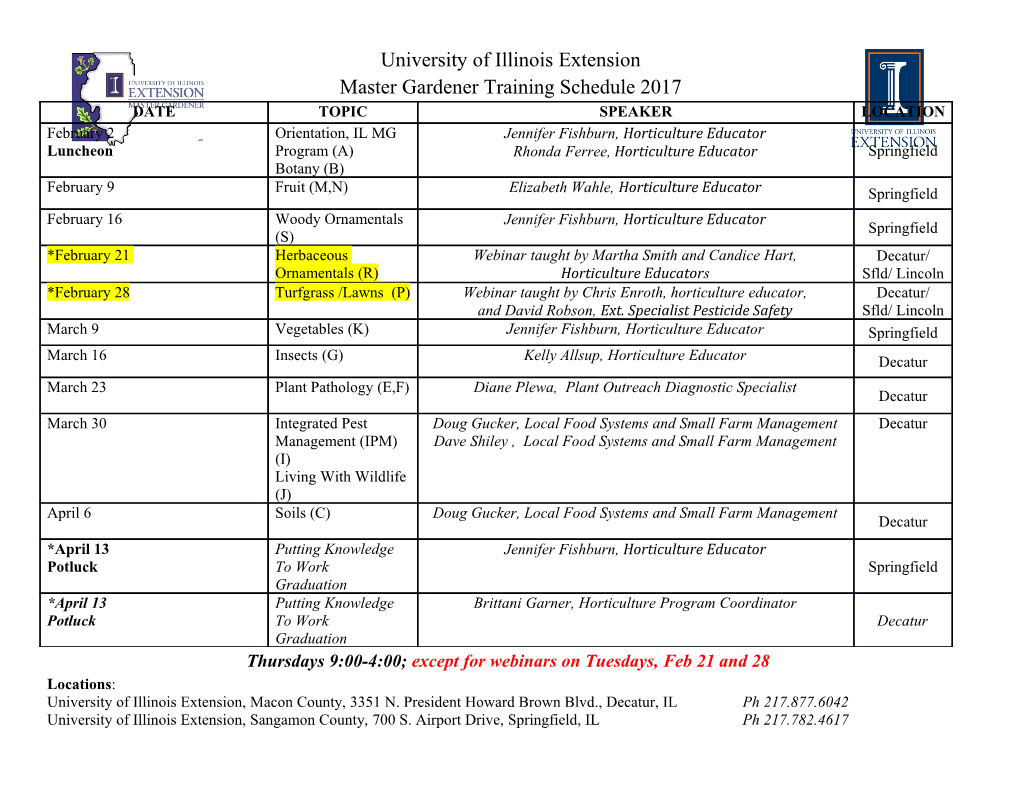
TOOtING COk& .FOR MANUFACTURING 'OPERATIONS INSPACUtI# FINAL REPORT APRIL 1969 N ACSI M ' (THRU) 2(PAGES) (NASA CR ORTMX ORAD NUMBER) (CA oEY) MARIM7IA MA ~rl... TI -RPA-7."-IRpr&,"i DENVER DIVISION I INFORMATI -ERViCE: STUDY OF TOOLING CONCEPTS FOR MANUFACTURING OPERATIONS IN SPACE Final Report Contract NAS8-21279 Control iCNI-8-30-25204(IF), (SI)(IF), (S2)(IF) April 26, 1969 Prepared by: Wayne D. Faber Fredrick J. Gredb Robert E. Boyd Georse W. Smith Program Manager Martin Marietta Corporation P. 0. Box 179 Denver, Colorado 80120 This report" vas prepared by Martin Marietta Corporation under Contract NAS8-821279, A Study of Tooling Concepts for Manufacturing Operations in Space, for the George C. Marshall Space Flight Center of the National Aeronautics and Space Adminis tration. li TABLE OF CONTENTS page I. Introduction. I-i XI. Conclusions/Recommendations . -i III. AAP Mission Analysis... ... ............ .. t-I A. Introduction . ..-. B. Experiments Analysis . .-. I. General ........... .... .11-. 2. M487 . .. .. 111-5 3. M508........... ....................... I1-8 4. M469. ... .... .... ... .... 111-9 C. EVA Requirements for AAP Missions .............. II- I. General ...... ...................... -i . 2. Exserp Integration Requirements ............ ni-l 3. ATM Time Line Study .. ............ 111-12 IV. EVA Analysis ............. ..................... IV- A. Introduction ....... ......................... V~1 B, -- NAR Study Summary and Preliminary EVA Analysis . iV-i C. Serpentuator versus other EVA Mobility Devices . .. IV-3 V. Conceptual Designs ...... .................... ... V-I A. Introduction ....... ..................... ... V-I B. Insero ......... ........................ ... V-i 1. Programmed Motion ..... ................ ... V-I 2. Inserp-ETD Comparison .... .............. ... V-3 EC. xserp Conceptual Design for Dry Workshop Application V-5 1. Guidance and Control. ................... V-5 2. Tip Manipulator System ................. V-6 3. Cargo Transfer..... .................... V-8 4. Liquid Hydrogen Transfer ................. V-9 D. Hermetically Sealed Joints. ; .. ..... V-10 iii PAge VI. Operational Requirements ............. vI-I A. Introduction ................ Vl-1 B. Detailed Joint Design Considerations .... VI-l C. Structural Design Considerations ........ VI-2 D. Preliminary Error Analysis .......... ... VI-2 E. Controls Effort.... ............... .... VI-7 F. System Considerations............... .... VI-10 G. Umbilical Considerations .. ............ VI-lI VII. Space Qualification of Elbow Joint ......... V -I A. Introduction ........ ................ VII-I .B. Serpentuator' System End Item Specification . VII-I C. Serpentuator Hinge Joint Assembly Specification VII-2 D. Test Plan for Hinge Joint Assembly ..... VII-2 Appendix A - AAP Experiments Summary.............. ... A-1 Appendix B - Structural Considerations.............. B-i Appendix C - Detailed Joint Design Recommendations. C-I Appendix D - Reference......... .................. D-1 iv I. INTRODUCTION This document constitutes Martin Marietta's final contract report for NASA Contract NAS8-21279, A Study of Tooling Concepts for Manufacturing Operations in Space (Serpentuator). The Ser­ pentuator concept discussed in this report represents a unique approach to space mobility problems. The device consists of a number of powered links which can be actuated relative to each other, such that the Serpentuator tip can be placed anywhere within a spherical volume. This mechanical linkage can serve as a means of transport, guidance, stabilization, and rendezvous for spade manufacturing operations. The device can be used either internally in the space cluster (Inserp) or externally (Exserp), and allows a flexibility not contained in other mobility devices. During the course of this contract, five major areas of interest pertinent to the Serpentuator concept were investigated. These were: I) application of Serpentuator to AAF related experi­ ments, 2) applicatibn of Serpentuator to a large class of space EVA requirements, 3) conceptual design studies, 4) Serpentuator operational requirements, and 5) space qualification requirements. These specific areas of investigation depart somewhat from the original study plan. This was due to the fact that early results of this study and other MSFC efforts revealed certain areas of special interest. Consequently, direction was supplied by MSFC to concentrate in these areas (references I - 4). Also, this report is organized to provide maximm continuity between the mission analysis sections, rather than to reflect the chronological order of reference I - 4. In general, Section III applies to reference I, Section IV to reference 3, Section V to reference 2, Section VI to reference 3, and Section'VII to reference 4, Section III discusses Serpentuator application to current AAP experiments and presents a brief review of the Com­ patibility Analysis of ATM Experiment Requirements for Serpentuator application. Section IV analyzes a large class of orbital EVA operations, comparing the Serpentuator with other mobility devices. In Section V the Inserp concept is studied for application to AA2 Experiment M487. A conceptual design for a remote controlled Exserp, applicable to the dry launched orbital workshop is also presented. This application was studied for two specific tasks. Section VI discusses the operational requirements for Serpentuator system elements. Included in this analysis are structural con­ siderations, detailed joint design considerations, controls requirements, and umbilical management. Section VII describes 1-1 modifications to an existing Serpentuator System End Item Specifi­ cation, presents an End Item Specification for the hinge elbow joint, and a Test Plan to space qualify a hinge elbow joint. Thus, .Vfihsreport presents the results of specifically assigned analysis tasks rather thaft a complete study of the entire system. 1-2 II. CONCLUSIONS/ RECOMMENDATIONS For the AAP program the best application of the Serpentuator would be on flight 4 for the film cassett removal and replacement. Although there are actually more EVA tasks on flight 2, the Ser­ pentuator probably could not be spaceflight qualified in time for this application. However, since EVA operations for space programs in general can be anticipated and since the Serpentuator would provide a very satisfactory mode of transportation (especially from a safety standpoint) this concept should be pursued early in a space program. Several possibilities are available: 1) the Serpentuator could be included as a part of M-509 and evaluated simultaneously and competitively with other EVA devices, 2) it could be used in conjunction with M-508,.3) it could be included (as Inserp, however, the principle is the same) as an equipment transfer device for M-487, 4) it could be established as a separate experiment, and 5) it could be used for EVA flight 4 for film cassett removal. The issue is that the Serpentuator represents an attractive method for EVA transport and it should be given an opportunity for astronaut evaluation as soon as possible. This is especially true if extensive future EVA along the guidelines of Section IV is anticipated. It appears that the Serpentuator (Exserp): 1) should he about 6"0 ft long with pitch control at the base (although it may be more desirable to make Serpentuator longer and remove pitch control at base), 2) should be pre-programmed for selected points about the cluster, 3) be capable of automatic retrieval, with manual control of the tip only and possible manual vernier control of the main links, and 4) assuming the umbilical requirement remains, the umbilical should be attached along the Serpentuator. It may be desirable to include complete manual control as a backup mode in the event of automatic mode failure, however, the viewing and dis­ play requirements increase considerably. Another mode of control that would minimize computer requirements and operator training would be a master-slave arrangement where a model of the cluster with Serpentuator would be used to command the parent Serpentuator. Built in safety features could be easily incorporated in this type of control. The Serpentuator link elements appear quite capable of space qualification; in fact, there are several designs already available for the elbow hinge joint. The rotary base joint requires further effort. Some suggested changes to space qualify this element are included in this report, however, questions remain with this approach and some initial testing should be conducted. II-1 The ability of the Serpentuator to perform delicate operations remotely requires extensive further study. Conceptually, -this appears feasible, but the ability of the tip adjustments to perform these tasks is not proven. There seems to be no great difficulty in placing the Serpentuator tip in the very near vicinity of the .work station. There are several options to provide this capability. The full capability of the Serpentuator, the accuracy of auto­ mated programming, the feasibility of automatic retrieval, the tip adjustments required, the requirement for telescoping tips, the delicacy of operations feasible, the manner of ,manual tip control, and -the requirement for complete manual control, cannot be ascertained until the control accuracy and capability is established. This is largely dependent on the individual joint capability. The future efforts reqaired for-the Serpentuator, prior to space qualification are: Static Requirements 1. Definition of future requirements
Details
-
File Typepdf
-
Upload Time-
-
Content LanguagesEnglish
-
Upload UserAnonymous/Not logged-in
-
File Pages161 Page
-
File Size-