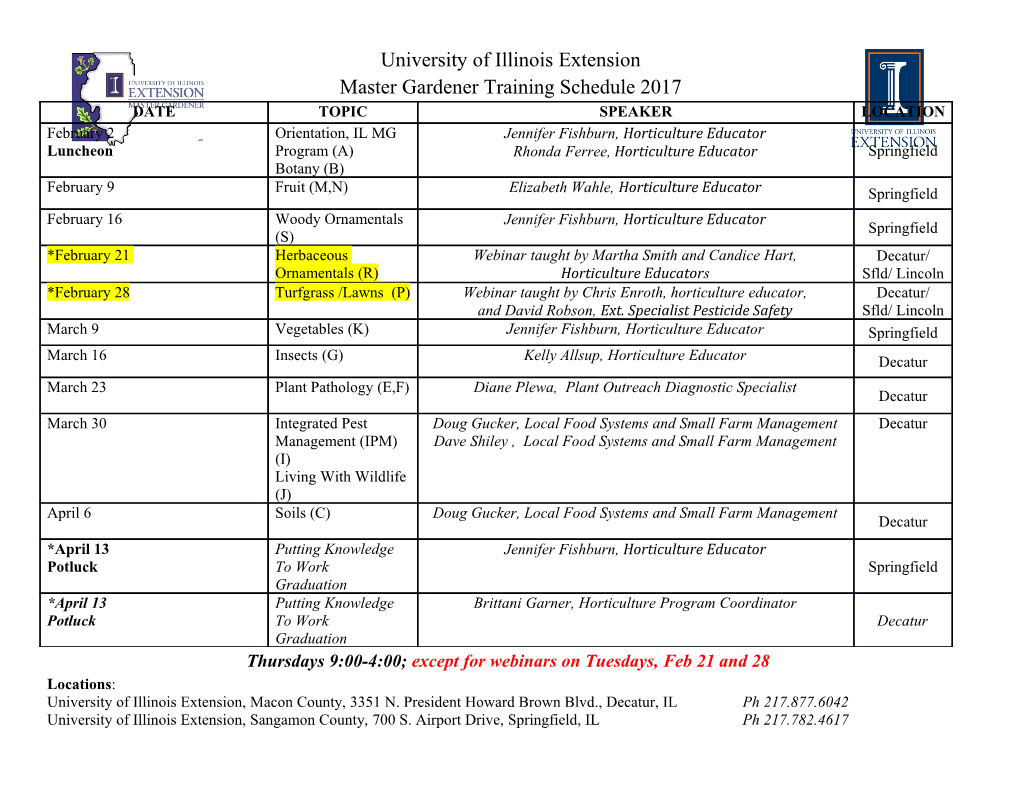
BUSINESS POTATODOSSIER 2/2020 SMART TECHNOLOGY for Potato Chips and Snacks BUSINESS POTATO DOSSIER 2/2020 ISSUE 2 - 2020 SMART content TECHNOLOGY for Potato Chips and Snacks 04 STEAM PEELING 24 FRYING TECHNOLOGY Aviko Belgium Orders AND ACRYLAMIDE Peace of Mind and CONTROL Kiremko Celebrates Equipment Dependability 30th Invicta Steam Peeler Is Paramount Sale in 30 Months 28 FRYING TECHNOLOGIES 08 INNOVATION Why Oil Quality Is Important IN SLICING Slicing Batch-processed 32 PACKAGING Chips Potato Fresh Packers and Covid-19 Challenges 12 LATEST CUTTING TECHNOLOGIES 36 PACKAGING INNOVATION What Works Best in Today's Market? PMMI Talks VFFS Advantages 16 STEAM PEELING INNOVATION 40 CHIPS PACKAGING Newest Peeler Offers EQUIPMENT the Lowest Cost The Age of Digitalisation of Ownership 20 FRYING 44 CONVEYING SYSTEMS TECHNOLOGIES Heavy Duty Construction Is Fry the perfect chip with an Important Criterion Pulsed Electric Fields This project is supported by PB 02 DOSSIER 2/2020 Staying on Top with New Technologies DAN OREHOV COMMENT managing editor hether acquiring or upgrading frying equipment, steam peelers or packaging machinery on the processing line, manufacturers are ready to offer their latest equipment innovation to help processers achieve their best potential. For example, the implementation of continuous PEF W pre-treatment in the chips processing industry is associated with several advantages. It softens the tuber and enables the use of new raw material and new cuts. In addition, a smoother cut with less breakage and starch leakage leads to higher yield and less oil absorption. Also, steam peeling has become an important process in a turnkey potato processing plant, being the preferred peeling method for the French fry industry and becoming a standard method for fresh peeled potatoes, pasteurized potatoes and the flake industry. At the same time, processors need new cutting equipment, as they say in their own words that it takes a connoisseur of potato chips to understand the nuances of flavor, texture, and color, but almost anyone can tell the difference between a potato chip coming from a continuous line and a potato chip coming from a batch line. Lastly, the end-stage packaging processes has advanced tremendously in recent years, as reducing waste is currently top of the agency and many brands are also moving towards using sustainable, fully bio-degradable alternatives to plastic materials. Which equipment do you believe needs an upgrade in your processing plant and which manufacturer would you consider to purchase machinery from? Feel free to send your feedback at [email protected]. Stay safe! n Manufacturers are ready to offer their latest equipment N innovation to help processers achieve their best potential. 03 PB 2/2020 DOSSIER STEAM PEELING Aviko Belgium Orders Peace of Mind and Kiremko Celebrates 30th Invicta Steam Peeler Sale in 30 Months Steam peeling has become an important process in a turnkey potato processing line, in the last 50 years when Kiremko built their experience in this field. By Kiremko PB 04 DOSSIER 2/2020 t is the preferred time decreases significantly. The large peeling method for the diameter inlet door allows high capacity French fry industry and processing, for large or small sized potatoes N has become a standard and small and large batches. The Kiremko I method for fresh Invicta peels more efficiently and thinly than Steam peeled potatoes, any other steam peeler, with 5 to 10% peeling is the pasteurized potatoes increase of yield. The secret of this success is preferred and the flake industry. the combination of an extremely short cycle time, up to 25% faster, with quick filling and peeling AVIKO SETTLES FOR THE BEST steam exhaust. This way the most potatoes method for “We didn’t know of this anniversary of the per hour can be processed at the highest the French Kiremko Invicta Steam peeler at the moment possible yields. fry industry we bought it”, Aviko Belgium Project Manager and has Cor Koole admits. “We just bought it because SUSTAINABLE CHOICE it offers us the highest reliability. We know the Kiremko’s Andy Gowing: “For a sustainable become a Kiremko Invicta from other Aviko locations. production line we save energy by installing a standard Yield, capacity, operational reliability and total condensate removal system. This saving is method for cost of ownership were our main focus. As over 25KW per ton peeled product with a fresh peeled always – with new major projects, like temperature of 50 degrees. The vapor potatoes, Poperinge – we had a good look at what the emission can be reduced to almost zero market has to offer and again Kiremko came emission. To reduce the noise produced when pasteurized out as the best. It’s always nice when your steam is blown off by a steam peeler, we have potatoes and choice is acknowledged by others. That is how developed a silencer. The noise released when the flake we see the celebration of the 30th Invicta industry. they sold to us. And we congratulate them ADVANCED STAINLESS-STEEL with this impressive milestone.” STEAM VESSEL HIGHEST CUSTOMER VALUE • Unique deep-sea technology that Kiremko director Andy Gowing: “We have ensures ultra-even pressure distribution always set ourselves out to be suppliers of • Ultimately balanced and self-correcting leading equipment throughout the potato vessel positions for high speed mixing processing industry: fries, flakes, chips, giving the best peeling results precooked and fresh. To be innovative and • Capacities between 2 up to 90 t/hr. BEST PEELING RESULTS improve ourselves, we work closely together with our customers every day. That is how we • Up to 25% shorter peeling time than meet the market demands in terms of any other steam peeler improvements like higher yields, larger • Optimal heat transfer through capacities, progressive automation, energy advanced condensate separation reduction and environmental concerns. All • 20 % smaller cooking ring resulting a aspects of the business are continually reduction of peel waste up to 10% examined, so we can keep progressing LOWEST TCO towards the best customer value for money.” • Extremely wear-resistant relief valve made of NASA quality materials STEAM PEELING IS A SCIENCE • Less maintenance due to the use of Steam peeling has become an important stainless steel process in a turnkey potato processing, in the • Less maintenance because crucial parts last 50 years when Kiremko built their are protected against steam and heat experience in this field. It is the preferred GENTLE ON THE ENVIRONMENT peeling method for the French fry industry • Integrated vapor extraction for an and has become a standard method for fresh optimal factory climate peeled potatoes, pasteurized potatoes and the • Blow-off condenser for energy flake industry. Due to the Invicta’s unique recovery up to 25 kilowatts per ton of stainless-steel vessel shape, the whole surface peeled product of every potato is heated evenly by steam. As • Shorter peeling times mean less a result of this optimal heat transfer, the steam steam consumption 05 PB 2/2020 DOSSIER steam is blown off creates a noise nuisance hand with other brands and they all say alike: and is a reason why an environmental permit it’s better and more durable. No replacing can be declined. The Kiremko silencer has been vessels every few years, no costly repairs or developed to transform the long-range low maintenance due to rust or other causes.” For frequency sounds into a higher frequency Kiremko the Invicta is just one success story. which can then be substantially reduced in the “At this moment we’re working on a next silencer. Lowering the energy consumption and generation fryer, that has the same mindset to reducing the emissions – both vapor and noise it: Be the best.” - are of great impact to the environment. When you add up the energy reduction of these 30 ARTIFICIAL INTELLIGENCE IN PEELING Kiremko Invicta steam peelers in a year, it’s the To optimize efficiency of the Invicta Steam equivalent of 2 million m3 natural gas, that can Peeler Kiremko designed the PeelGuard ®. heat nearly 1.100 homes for a year. Andy Gowing: “The PeelGuard® is an optical in-line inspection, equipped with a weigh belt, TOTAL COST OF LEADERSHIP so the exact peel result can be calculated Not only the sustainability is secured in the accurately. The system detects the thickness 30 Invicta Steam Peeler, also the durability. The of the removed skin and cooking ring, in order shape of the vessel, the stainless steel that it is to continuously optimize the steam peeler Invicta steam made of and the construction that avoids settings. This way, the PeelGuard® guarantees peelers were direct influence of heat and steam, all make a constantly optimized peeling yield and up- sure that the Invicta is low on maintenance. to-date information with respect to quality of sold by “This leadership in the marketplace results in raw material used. This information can be Kiremko in the lowest Total Cost of Ownership by far. We made available to the customer’s MES and/or 30 months. have customers comparing the Invicta first ERP systems.” ONE STEP IN A TOTAL SOLUTION For Kiremko steam peeling is one of the major potato processing steps where their innovation efforts and product development is directed to. Andy Gowing: “We like to call ourselves total solution providers. When customers like to order a complete line, so they just have one throat to choke, as I always say, Kiremko provides them with product leadership on peeling, cutting, blanching, drying and frying. Together with our strategic partner Idaho Steel we can add flake drying and forming to the menu as well. And for all the other processing steps we have a network of partners in place. And we’re counting.
Details
-
File Typepdf
-
Upload Time-
-
Content LanguagesEnglish
-
Upload UserAnonymous/Not logged-in
-
File Pages46 Page
-
File Size-