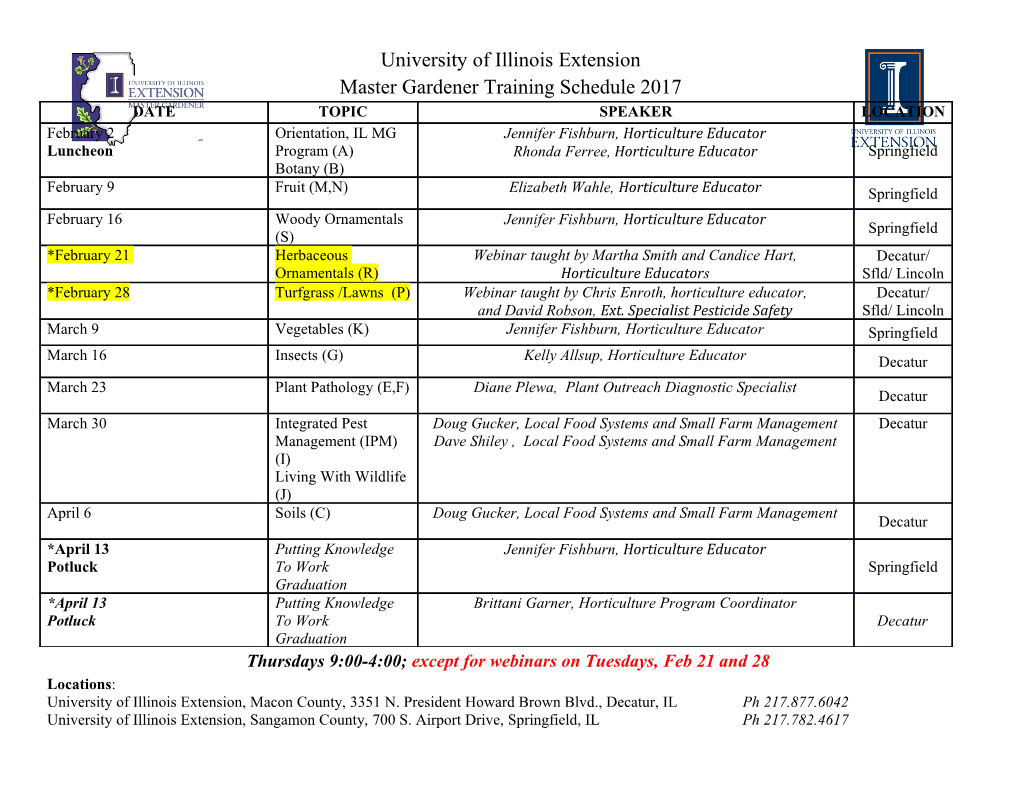
Development and Evaluation of Alternative Electric Thermostat Design Arvid Isaksson Mechanical Engineering, master's level 2018 Luleå University of Technology Department of Engineering Sciences and Mathematics Abstract Introducing an electric thermostat to the thermal management system is a way of actively controlling the temperature of the engine, which has been shown to have several possible gains regarding power, fuel consumption, emissions and engine durability. Complexity, cost and durability are key concerns that have led to no heavy duty truck on the market having an electrically controllable thermostat. This emphasizes the need for exploring alternative solutions that enables electric control of the thermostat according to the needs of heavy commercial vehicles. Several concepts have been generated to solve this problem and a model based approach in Simulink, Matlab and GT Suite was used for the development and evaluation. The most promising concept of combining a BLDC electric motor with a wax body enables electric control with a downsized actuator and full fail-safe function while showing improvements in temperature control performance compared to a traditional wax thermostat. This thesis has increased the knowledge on the subject and could allow for implementing an electrically controlled thermostat in future Scania heavy duty trucks, leading to a more durable engine with lower fuel consumption and emissions. i Preface This master thesis was written by Arvid Isaksson during the first semester of 2018 as a final course in M.Sc. mechanical engineering at Lule˚aUniversity of Technology. The work was conducted at Scania CV AB in S¨odert¨alje, Sweden with Anders Larsson as company supervisor and Jan-Olov Aidanp¨a¨aas university supervisor. I would like to extend my deepest gratitude to all the colleagues at Scania who have helped and encouraged me during this work. Special thanks to Zoltan Kardos, Mattias Strindlund and all at Scania who have contributed to this project by sharing knowledge and showing interest. ii Nomenclature Quantity Description Unit x Linear position of valve [m] mt Mass of valve [kg ] F Linear force exerted on valve [N] Fµ Static friction [N] FS Spring force [N] k Spring constant [N/m ] Finit Spring pretension force [N] rm Mean radius of lead screw thread [m] l Lead or pitch of thread [m] α Helix angle of thread [rad ] N Normal force [N] µ Friction coefficient between thread and nut [−] Fh Hydraulic force [N] ∆P Pressure differential [P a ] p Pressure [P a ] A Area [m2] τ Torque [Nm ] r Radius [m] h Height [m] Tamb Ambient temperature [K] me Mass of engine [Kg ] 2 Ae Surface area of engine [m ] Ce Specific heat constant of engine body [KJ/KgK ] Te Engine temperature [K] Wrad Heat flow out of radiator [W ] m˙ Coolant mass flow over radiator [Kg/s ] Cp Specific heat constant of coolant [KJ/KgK ] n Ratio of fuel energy going to heating the coolant [−] Wfuel Total rate of energy released from burning fuel [W ] Wair Rate of heat transfer from engine to surrounding air [W ] 2 hc Convective heat transfer coefficient [W/m K] Ue Inner energy of engine body [J] m˙ 0 Working point mass flow [Kg/s ] Te0 Target temperature [K] Wfuel 0 Expected average power from engine [W ] 2 hc Convective heat transfer coefficient [W/m K] m˜˙ Deviance from working point mass flow [Kg/s ] T˜e Deviance from target temperature [K] ˙ 2 W˜ fuel Deviance from expected engine power [W/m K] G Transfer function from mass flow to temperature [Ks/Kg ] H Transfer function from engine power to temperature [K/W ] Kp Proportional constant of PIDF controller [−] Ki Integrative constant of PIDF controller [−] Kd Derivative constant of PIDF controller [−] τd Time constant of derivative control term [−] ω Engine rotational speed [rad/s ] iii Contents Abstract ............................................... i Preface ................................................ ii Nomenclature ........................................... iii 1 Introduction .......................................... 1 1.1 Background......................................... 1 1.1.1 Thermal Management System . 1 1.1.2 Wax Thermostat Valve . 2 1.2 Objective ........................................ 4 2 Theory .............................................. 5 2.1 MarketResearch ..................................... 5 2.1.1 ElectricThermostat ................................ 5 2.1.2 Related Technology . 6 2.2 ElectricStepperMotor............................... .... 7 2.3 Valve Control Dynamics . 8 2.4 Hydraulics......................................... 10 2.5 Thermal Management System Model and Control . 11 3 Method ............................................. 14 3.1 ProductNeeds ...................................... 14 3.1.1 ProductCharacteristics . 15 3.1.2 ProductSpecification ............................... 16 3.2 ConceptGeneration ................................... 17 3.3 Conceptselection................................... 17 3.3.1 Conceptscoring .................................. 18 3.4 ModellingandFurtherDevelopment . 18 3.5 Functional Prototype . 19 3.6 ProjectScope...................................... 19 4 Results .............................................. 21 4.1 Hydraulic Actuator Combined With Wax Body Through Cam . 21 4.1.1 Hydraulic Dimensioning . 21 4.2 BLDC Motor Combined With Wax Body . 23 4.2.1 Stepper motor dimensioning . 23 4.3 Rough Design of Final Product and Actuator Placement . 24 4.4 Prototype.......................................... 24 4.4.1 Prototype Simulation . 26 4.4.2 Prototype Assembly . 27 4.4.3 Prototype Testing . 28 4.5 Simulated Temperature Control in GT Suite . 29 5 Discussion ............................................ 37 5.1 Conclusions........................................ 37 5.2 FutureWork ........................................ 38 A Normal Operation ....................................... 40 B Concept Descriptions ..................................... 42 C Concept Evaluation ...................................... 47 iv 1 Introduction Thermal management of the engine is a way to achieve faster warm-up and more optimal working temperatures, resulting in lower emissions, lower fuel comsumption and increased lifespan of engine components. Even though thermal management is an important aspect of the engine performance, the technology used today is often essentially the same as in the early 1900’s. Introducing a smart thermal management system has been shown to have several possible gains on the engine perfor- mance[1][2][3]. The thermostat that controls the coolant flow over the radiator is a possible area of improvement by introducing electronically controllable components and smart control [4][5]. A smart thermostat can improve the coolant flow control and allow different control temperatures [6]. It can also accommodate for additional control goals outside of coolant temperature. There exists passenger vehicles which have successfully incorporated a smart thermostat in their engine design [7][8]. Yet no heavy duty vehicles currently employ this kind of technology. A reason for this might be that the benefits of having smart thermal management in the form of an electronically controllable thermostat, does not currently outweigh the added cost and complexity of replacing the simple and robust wax pellet thermostat used today. This emphasizes the need for a solution which offers smart control over the coolant flow while still being robust and cost-effective, offering a solid business case. 1.1 Background Scania does not currently have an electronically controllable thermostat capable of smart control even though the thermal management might be improved by using one. Incorporating such a solution could give improvements in fuel consumption, emissions and durability of engine components. It is deemed that the solutions that exists today can be improved regarding durability, simplicity and cost-efficiency. 1.1.1 Thermal Management System The thermal management system handles the heat created by the engine and aims for keeping the engine at temperatures that enhance the engine performance. The traditional thermal management system consists of a cooling circuit which is circulated by a water pump connected to the engine crankshaft. The coolant moves through the engine, keeping it at acceptable temperatures. The coolant then reaches the thermostat which based on its temperature, divides the flow to either be cooled in the radiator or go through the bypass to the pump where it is mixed with the cold radiator coolant and recirculated through the engine. The radiator cools the coolant by having air flow through assisted by a cooling fan which creates forced convection. The working principle of the smart thermal management system is the same but the pump and thermostat can be replaced with electronically controllable components such as an electric water pump and smart valve, as seen in Figure 1. 1 Figure 1: Example of smart thermal management system [2]. The thermal management system for heavy duty trucks may also incorporate retarder cooling in case the truck is outfitted with a retarder. The retarder works like a secondary hydraulic brake that is mostly used in downhill driving. When used, high bursts of energy can be introduced into the thermal management system. 1.1.2 Wax Thermostat Valve The wax thermostatic element was introduced to automotive engines in the 1930’s since it was found sub-optimal to constantly cool the engine. The thermostat is designed to not send coolant to the radiator before it is sufficiently hot, decreasing the engine warm-up time. It then keeps
Details
-
File Typepdf
-
Upload Time-
-
Content LanguagesEnglish
-
Upload UserAnonymous/Not logged-in
-
File Pages53 Page
-
File Size-