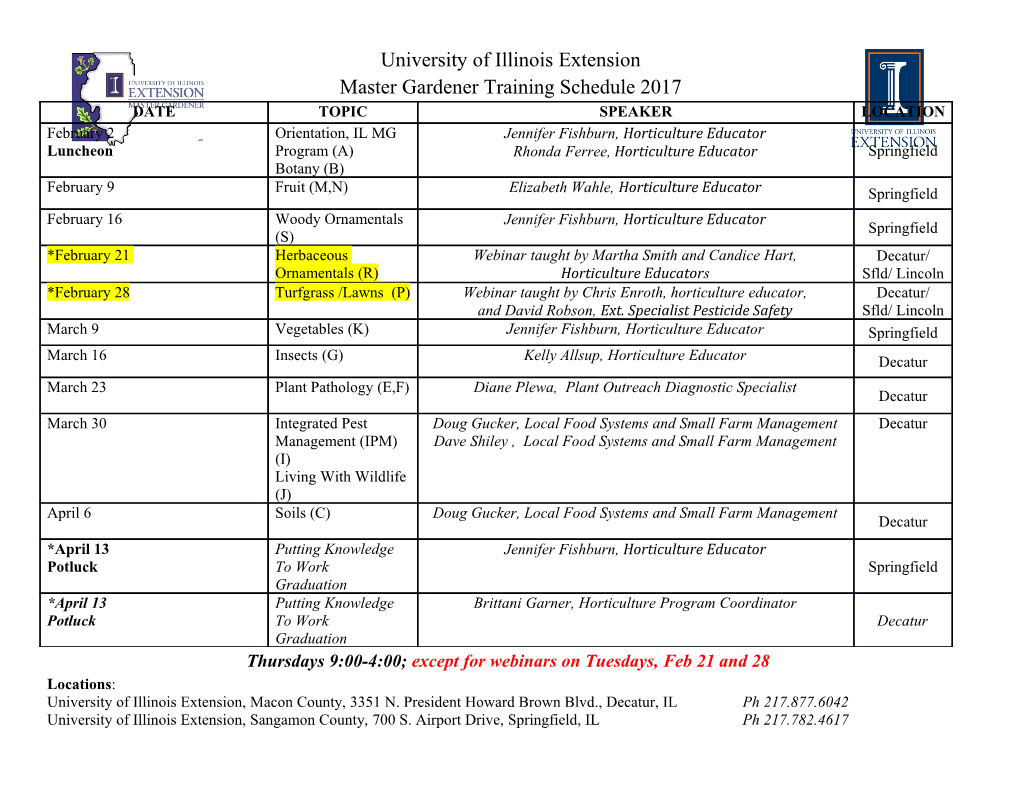
NASF SURFACE TECHNOLOGY WHITE PAPERS 81 (7), 1-9 (April 2017) Iron Tungsten Alloy Plating with Low Friction and Wear Resistance by Kiyohiko Watabe* Technical Manager Product Development Engineering Yuken Industry Co. Ltd. Kariya City, Aichi Prefecture, Japan & Yuken America, Inc. Novi, Michigan USA Editor’s Note: This paper is a peer-reviewed and edited version of a presentation delivered at NASF SUR/FIN 2016 in Las Vegas, Nevada on June 7, 2016. ABSTRACT An alloy plating film developed by finely crystallizing iron and tungsten demonstrates both a high level of hardness and excellent ductility. In addition, low friction can be achieved by its application under a layer of lubricant. The modern automotive industry has been striving to reduce energy loss caused by friction. Low friction and improved durability can be attained by applying this technology to the surface of parts which constantly slide in operation. This in turn contributes to better fuel efficiency. On the other hand, diamond like carbon (DLC), a typical low friction coating, causes peeling at early stages when loaded under high pressure and shows poor synergistic effects with lubricants. Therefore, the application of this coating is not recommended for sliding parts. Alternatively, the wet plating technology we developed does not have these disadvantages. It also has the merit of greater cost performance as compared with DLC produced with PVD technology. Introduction The largest challenge facing the automotive industry these years is CO2 reduction (through lower fuel consumption). They need to meet fuel efficiency regulations that will take effect in various regions in the near future. In mid- to long-term policies, all of the automotive makers have been rigorously working to reduce CO2 in exhaust to cope with global climate changes. In particular regard to the reduction in friction loss in the internal combustion engine, the industry holds high expectations toward the development of surface treatment technologies that can both decrease friction coefficients for engine components sliding with each other and establish high wear resistance for them. Conventionally, dry plating like DLC (diamond-like carbon) and CrN (chromium nitride), and wet plating including electroless nickel plating and hard chromium plating have been used for these engine components (such as piston rings, bubble lifters and crankshaft bearings) which have metal-on-metal sliding contact. DLC provides low friction and excellent wear resistance, but peeling is also likely to occur when the ductility is insufficient. In addition, a peeled hard film is damaging to the contacting surface, and the compatibility is extremely limited to only certain types of lubricants. Furthermore, dry coatings like DLC require a batch process which raises the cost, and so it is not widely used. Electroless nickel plating has excellent covering power, but its friction properties and wear resistance are somewhat insufficient. Further, it requires a high bath renewal frequency and large volumes of waste water subsequently become a burden to the environment. Hard chromium plating is a functional plating process that has been widely used for a long time to achieve wear resistance properties. The greatest concern with this plating is the hexavalent chromium contained in the plating bath that users have to deal with to protect the environment. We have developed a functional plating method which can be wet processed, thereby promoting process cost control, and which also has high wear resistance and low friction properties without nickel and chromium. Page 1 NASF SURFACE TECHNOLOGY WHITE PAPERS 81 (7), 1-9 (April 2017) Plating overview Plating method The plating equipment used in this development is shown in Fig. 1. We used insoluble anodes made of platinized titanium. The bath was mixed with a magnetic stirrer during plating. The plating bath parameters used are shown in Table 1. The bath temperature was 75 ± 5°C and the pH was adjusted to 6.5 with diluted sulfuric acid. Deposition could start around 2.0 A/dm2 of the cathode current density. However, in consideration of practical plating speeds, we proceeded with 7.0 A/dm2 as our main focus. The bath temperature was slightly high, but overall it was a typical electroplating method. The bath was mixed with ferrous sulfate hydrate and sodium tungstate hydrate as shown in Table 2. The total of these metallic salt concentrations was 0.20 mol/L. By using the same amount of the complexing agent, the iron and tungsten became ion- complexed together. Figure 1 - Plating equipment layout. Table 1 - Operating conditions. Item Range Bath temperature 75 ± 5°C Cathode current density 1 ~ 10 A/dm2 pH 6.5 ± 1.5 Mixing Required Table 2 - Plating bath components. Chemical formula Chemical name Na2WO4•2H2O Sodium tungstate dihydrate FeSO4•7H2O Ferrous sulfate heptahydrate Additive A Complexing agent Additive B Electrolyte, etc. Page 2 NASF SURFACE TECHNOLOGY WHITE PAPERS 81 (7), 1-9 (April 2017) Plating film properties Tungsten itself is not deposited via a normal wet plating method. However, when a ferrous type transition metal like iron is also present, it can be co-deposited as an alloy. In this development where the tungsten ratio in the film was controlled to be 50 to 60 wt% under the conditions previously described, we were able to obtain an Fe-W alloy film with excellent hardness and ductility. In addition, as this alloy plating contains much iron like the steel materials used for mechanically sliding parts, we verified that there were good synergistic effects and compatibility with lubricants and that low friction results were readily obtained when a lubricant was used during friction coefficient measurements. Plating film properties Film hardness and behavior versus heat load Figure 2 shows the results of a test done to identify the film hardness, a crucial factor for wear resistance. Measurements were performed with a nanoindenter (Nanoindenter G200 manufactured by MTS), and the results were converted to the Vickers hardness scale. Figure 2 - Comparison of plating hardness. The hardness immediately after plating was confirmed to be HVN 800 by controlling the iron and tungsten ratio in the film. The hardness of this film gradually improved during heat treatment for the film under atmospheric pressure, as shown in Fig. 3. The highest hardness obtained was HVN 1150 at 300 to 500°C. The hardness was reduced after the temperature exceeded 600°C. However, above 400°C, iron crystallization progressed, reducing the ductility of the plating film. Therefore, we determined that 300°C was the appropriate heat treatment temperature and the condition enabling full performance of the heat resistance of the film. Further, the same heat load regimen was applied to the DLC coating and the hardness change was also recorded. In the range above 150°C, the bonding force started to relax, reducing the hardness. As the temperature continued to rise, the hardness decreased markedly. At 300°C, the DLC quickly turned to carbon dioxide and disappeared within a short period of time. Page 3 NASF SURFACE TECHNOLOGY WHITE PAPERS 81 (7), 1-9 (April 2017) Based on the above test results, the hardness of the Fe-W film is considered to be hard among wet plating types. During the normal temperature range, the hardness of the Fe-W film was not as strong as that of the DLC, but this was reversed when 200°C or so was exceeded. Figure 3 - Hardness changes in Fe-W and DLC coatings through heat treatment. Wear resistance A ball-on-disk friction/wear tester was used in this evaluation. The equipment diagram is shown in Fig. 4 while the measurement conditions are indicated in Table 3. High speed tool steel with a hardness of HRC 62 was used for the plating-side disk test samples. The surface roughness was adjusted in such a way that all the plating film test samples showed a post-plating roughness of Ra 0.1 μm. The contacting material was a mirror-finished Φ6mm ball made of high carbon chromium bearing steel. The load to the entire contacting material was 10N. However, because of its round shape, the ball had a point contact with the plating test sample, and that local load was 1.57 GPa. Figure 4 - Schematic diagram of a ball-on-disk friction wear tester. Page 4 NASF SURFACE TECHNOLOGY WHITE PAPERS 81 (7), 1-9 (April 2017) Table 3 - Ball-on-disk friction/wear measurement conditions. Test samples were cleaned with acetone to remove any surface dust and stains before measurements. Liquid paraffin was used as a lubricant so that the impact of the extreme pressure agent did not have to be considered. After a minute volume was applied to the film surface to make a mixed lubrication range, measurements were performed. Air conditioning was used so that the room temperature and relative humidity were maintained at 25°C and 30%, respectively. However, the temperature of the test sample surface was not measured during the test. Generally speaking, wear resistance does not solely depend on the hardness of the film. If the friction resistance is large, or the affinity with other materials is strong, adhesive wear that progresses through adhesion to the contacting material becomes intense. On the other hand, if the friction coefficient and affinity with the contacting material are small but the film is soft, the film will disappear due to simple wear at an early stage. If the film ductility is low, cracks or chipping will occur soon, leading to friction resistance and subsequent adhesive wear. Wear resistance requires a balance of low friction, low affinity with the contacting material and ductility in addition to the hardness of the film. Figure 5 shows post-test wear mark comparison photos. Even though the film hardness of the electroless nickel plating was stronger than the Fe-W plating (without heat treatment) by HVN 100, the film loss volume due to wear was the greatest among all the films and the basis metal was slightly exposed.
Details
-
File Typepdf
-
Upload Time-
-
Content LanguagesEnglish
-
Upload UserAnonymous/Not logged-in
-
File Pages9 Page
-
File Size-