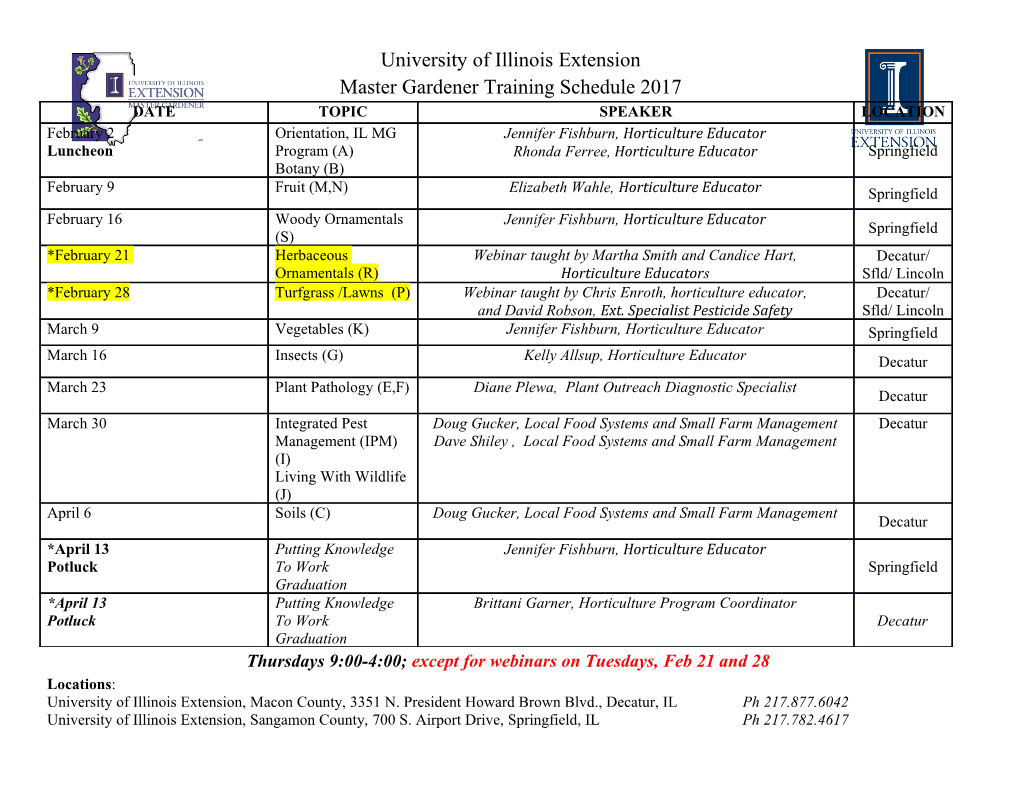
Aug. 24, 1954 W. B. DANCY ET AL 2,687,339 PROCESS FOR THE TREATMENT OF LIQUORS TO RECOWER POTASSIUM AND MAGNESIUM WALUES Filed Jan. 8, 1951 LGRUOR | REACTION TANK-3 4. 15KANTE 7um 6 FTER-5 8 O STORAGEDRYER AND -g FLTRATE 2 CARNATE-29 EVAPORATOR-3 SLURRY 4. OVERFLOW-17-16- THICKENER-15 8 28 CAL CUM } CHLORDE -2O-2--REACTION TANK-9 UNDERFLOW-29 T FER-23 24 2S SOLDS-25 MAGNESUMYa CHORIDE SOLUTION-27 4TTORNEY Patented Aug. 24, 1954 2,687,339 UNITED STATES PATENT OFFICE 2,687,339 PROCESS FOR THE TREATMENT OF LIQ UORS TO RECOVER POTASSUM AND MAGNESUM WALUES William B. Dancy and Robert A. MacDonald, Carlsbad, N. Mex, assignors to International Minerals & Chemical Corporation, a corpora tion of New York Application January 8, 1951, Serial No. 204,983 11. Claims, (CI. 23-38) 1. 2 This application relates to processes for the AccCording to the general method employed treatment of liquors to recover potassium and in the instant invention for the recovery of potash magnesium values therefrom, and more particu values as kainite salts, and of magnesium values larly to processes for the treatment of potassium as magnesium chloride from solutions Or liquors sulfate reject liquors or their equivalents to re containing chlorides and/or Sulfates of magne cover potassium and magnesium compounds sium and of potassium, the liquor is mixed with therefrom. a slurry, the solid phase of which comprises In the processes of producing potassium Sul carnalite (KC.MgCl2.6H2O), and the aqueous fate by the base exchange or metathesis of the phase of which is substantially saturated with magnesium content of langbeinite with the po 10 respect to magnesium chloride. Magnesium tassium content of potassium chloride, there is chloride from the carnallite results in an in produced a mother liquor from which the potas crease of the magnesium chloride concentration sium sulfate crystals have been separated. This in the solution, and kainite salts are crystallized. mother liquor is usually evaporated and cooled The formation of kainite crystals is accompanied in order to separate potassium chloride and leo 15 with a reduction of the Sulfate ion concentra nite crystals from the liquor. The liquor from tion in the magnesium chloride solution. The which the crystalline Salts have been removed kainite salts are separated from the magnesium has heretofore been sent to Waste even though chloride solution, which is evaporated to a point it contains magnesium and potassium com near Saturation with respect to bischofite. S0 pounds. It would be desirable to recover sale 20 dium chloride and kieserite in addition to car able magnesium and potassium products from nallite crystallize from the Solution which is then such reject liquors. decanted or thickened, for example, in the con It is an object of the instant invention to re ventional type thickener which effects the sep cover the potassium and/or the magnesium com aration of liquid substantially free of solids from pounds from liquors containing chlorides and 25 a mixture containing liquid and Solids. The Sulfates of magnesium and potassium. underflow from the thickener, which contains it is a further object of the instant invention the Solid phase Salts, is recycled to the initial to recover saleable potash and magnesium prod step of the process, in which kainite is formed. lucts from potassium sulfate reject liquors or their The kieserite present in the salts is thought to equivalents. 30 react with potassium chloride to form additional It is a further object to recover potash salts, kainite. The overflow from the thickener, a Substantially free of magnesium chloride, and concentrated magnesium chloride Solution, is a magnesium chloride solution from potassium further processed to produce magnesium chemi sulfate reject liquors or their equivalents. cals. It is a further object of the instant invention 35 The liquors which are used as feed materials to recover potash salts, substantially free of mag contain chlorides and/or sulfates of magnesium nesium chloride, and a magnesium chloride solu and of potassium. In one embodiment of the tion, which may be processed to obtain other instant invention, potassium sulfate reject liq magnesium chemicals, from potassium sulfate uors, Such as reject liquors produced in base ex reject liquors or their equivalents. 40 change processes as above-described, and reject These objects and other objects of the instant liquorS produced in processes Such as are de invention Will become more apparent upon a scribed and claimed in U. S. Serial No. 166,715, fuller understanding of the invention as here filed June 7, 1950, U. S. 2,295,257, issued to Butt in after Set forth. et al., and the like, are used. A typical potassium The instant invention involves the treatment 4 5 Sulfate reject liquor suitable for the practice of of liquors or Solutions containing chlorides and the instant invention contains between about Sulfates of magnesium and potassium under con 5.3% and about 6.7% by weight of potassium ditions hereindescribed with a carnallite slurry chloride, between about 1.8% and about 3.3% under conditionS Which result in the formation by Weight of sodium chloride, between about 6.2% of kainite (KCl.MgSO4.3H2O) and a magnesium 50 and about 7.5% by weight of magnesium sulfate, chloride solution. The Solid kainite Salts are between about 15.5% and 18.3% by weight of separated from the magnesium chloride solu magnesium chloride, and between about 66.0% tion. The potash SaltS can be employed as a and about 68.0% by Weight of Water. fertilizer product. The magnesium chloride so It is not essential in the kainite forming step, lution can be further processed into magnesium 55 that is, in the admixing of a slurry whose aque chemicals as desired. Ous phase is Substantially Saturated with respect 2,687,889 3 4. to magnesium chloride and whose solid phase tween about 36% and about 40% by Weight at contains carnallite and kieserite and minor a temperature of between about 115° C. and amounts of sodium chloride, that kieserite and about 120° C. and is thickened at a temperature sodium chloride be present. The instant process of about 90° C. The underflow from the thick may be practiced and is usually initiated by add ener is recycled to the step in which kainite is ing a substantially saturated solution of magne formed, and the overflow, which is a concen sium chloride which contains a suspension of trated magnesium chloride solution, is further carnallite to potassium sulfate reject liquor of processed to recover its magnesium value. equivalent liquors without substantially altering In a further embodiment of the instant novel the over-all process. The presence of kieserite in process, potassium sulfate reject liquor is al the slurry increases the yield of kainite and thus lowed to react with a hot slurry, obtained from increases the reaction efficiency. Thus in the a subsequent step of the process as herein preferred embodiment of the instant novel proc described, which comprises solid phase carnal ess, the slurry containing carnallite and kieserite lite and minor amounts of kieserite and sodium obtained as above-described as underflow from chloride in a solution of magnesium chloride. the thickener is recycled to the kainite forma The mixture is heated at a temperature of be tion Step. tween about 60° C. and about 85°C. for between In the kainite formation step, Sufficient car about two and about four hours. The carnallite nallite slurry is added to the potassium Sulfate and kieserite are dissolved in the liquor, and a reject liquor so that the resulting liquor will be 20 mixture of salts, comprising kainite with minor nearly saturated with respect to carnallite. For amounts of potassium chloride and sodium chlo example, kainite is obtained by mixing between ride, are crystallized. These salts are separated about 1.15 and about 1.35 parts by Weight of from the resulting solution by filtration and are potassium sulfate reject liquor per part of car washed and dried. The kainite salts have a typ maliite slurry. Kainite is formed in the above 25 ical analysis as follows: described slurry at a temperature of between Percent by weight about 10° C. and about 85° C. However, the re Potassium chloride---------------------- 34.9 action is preferably carried out at a temperature Magnesium Sulfate --------------------- 44.6 of between about 60° C. and about 85° C. Al Sodium chloride------------------------- 19.77 though kainite is formed in the slurry through 30 The salts analyzed about 22.09% potassium oxide out the entire temperature range mentioned and about 15% magnesium oxide. About 92.7% above, the rate of formation of kainite is Suf of the potassium oxide is recovered in the form. ficiently rapid to be commercially feasible only of kainite SaltS. attemperatures of above about 60° C. The kainite The solution from which the salts have been salts, which are separated from the solution, have separated is then evaporated to a point near a K2O content of about 22% and magnesium saturation with respect to bischofite, for example, oxide content of about 15%. the solution is evaporated to a magnesium chlo After the removal of the kainite salts from the ride concentration of between about 36% aid magnesium chloride solution, said solution is about 40% by weight. During this evaporation, evaporated to a point near saturation with re 40 carnallite and some kieserite and Sodium chlo spect to bischofite, that is to a magnesium chlo ride are crystallized from the solution. The ride concentration of between about 36.0% and evaporation is carried out at a temperature above about 40% by weight. The evaporation is usually about 60° C., and usually water is removed to carried out at a temperature above about 60 C, the extent of approximately 25% of the feed preferably at a temperature between about 115 solution, but more or less water is driven off, C.
Details
-
File Typepdf
-
Upload Time-
-
Content LanguagesEnglish
-
Upload UserAnonymous/Not logged-in
-
File Pages5 Page
-
File Size-