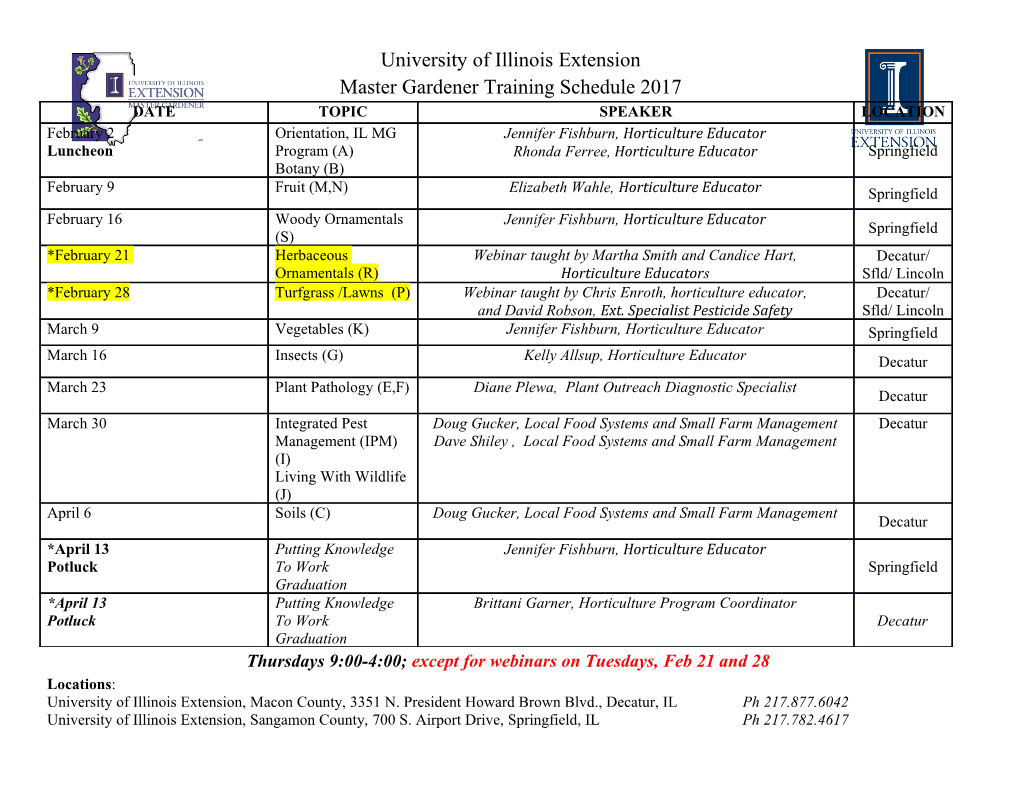
Chapter 12. Engine Ignition This chapter discusses the theory behind the engine ignition models available in ANSYS FLUENT. Information can be found in the following sections. • Section 12.1: Spark Model • Section 12.2: Autoignition Models • Section 12.3: Crevice Model For information about using these ignition models, see Chapter 20: Modeling Engine Ignition in the separate User’s Guide. 12.1 Spark Model The spark model in ANSYS FLUENT will be described in the context of the premixed tur- bulent combustion model. For information about using this model, see Section 20.1: Spark Model in the separate User’s Guide. Information regarding the theory behind this model is detailed in the following sections: • Section 12.1.1: Overview and Limitations • Section 12.1.2: Spark Model Theory 12.1.1 Overview and Limitations Initiation of combustion at a desired time and location in a combustion chamber can be accomplished by sending a high voltage across two narrowly separated wires, creating a spark. The spark event in typical engines happens very quickly relative to the main combustion in the engine. The physical description of this simple event is very involved and complex, making it difficult to accurately model the spark in the context of a multi- dimensional engine simulation. Additionally, the energy from the spark event is several orders of magnitude less than the chemical energy release from the fuel. Despite the amount of research devoted to spark ignition physics and ignition devices, the ignition of a mixture at a point in the domain is more dependent on the local composition than on the spark energy (see Heywood [128]). Thus, for situations in which ANSYS FLUENT is utilized for combustion engine modeling, including internal combustion engines, the Release 12.0 c ANSYS, Inc. January 29, 2009 12-1 Engine Ignition spark event does not need to be modeled in great detail, but simply as the initiation of combustion over a duration, which you will set. Since spark ignition is inherently transient, the spark model is only available in the transient solver. Additionally, the spark model requires chemical reactions to be solved. The spark model is available for all of the combustion models, however, it may be most applicable to the premixed and partially premixed combustion models. The Spark Model used in ANSYS FLUENT is based on a one-dimensional analysis by Li- patnikov [203]. The model is sensitive to perturbations and can be subject to instabilities when used in multi-dimensional simulations. The instabilities are inherent to the model and can be dependent on the mesh, especially near the beginning of the spark event when the model reduces diffusion to simulate the initial laminar spark kernel growth. The instability is susceptible to numerical errors which are increased when the mesh is not aligned with the flame propagation. As the spark kernel grows and the model allows turbulent mixing to occur, the effect of the instability decreases. 12.1.2 Spark Model Theory The spark model in ANSYS FLUENT is based on the work done by Lipatnikov [203] and extended to other combustion models. The derivation of the model can be done in the context of the Zimont premixed combustion model. Zimont Premixed Flame Model The transport equation for the mean reaction progress variable, c, is given by Equa- tion 12.1-1 ∂ρc + ∇ · (ρ~vc) = ∇ · (D ∇c) + ρ U |∇c| (12.1-1) ∂t t u t where Dt is the turbulent diffusivity, ρu is the density of the unburned mixture and Ut is the turbulent flame speed. Since the spark is often very small compared to the mesh size of the model and is often laminar in nature, the Zimont model is modified such that ∂ρc + ∇ · (ρ~vc) = ∇ · ((κ + D )∇c) + ρ U |∇c| (12.1-2) ∂t tt u t where κ is the laminar thermal diffusivity and the effective diffusivity Dtt is given by ( −ttd Dt 1 − exp τ 0 if ttd ≥ 0 Dtt = (12.1-3) Dt if ttd < 0 where is ttd = t−tig and tig denotes the time at which the spark is initiated. Additionally, τ 0 is an effective diffusion time, which you can set. 12-2 Release 12.0 c ANSYS, Inc. January 29, 2009 12.2 Autoignition Models Only turbulent scales that are smaller than the spark radius can contribute to turbulent spark diffusion, so the expression for the effective turbulent diffusivity, Dtt, is ramped up as the spark grows. This creates higher temperatures at the location of the spark and can cause convergence difficulties. In addition to convergence difficulties, small changes in the diffusion time can change the result significantly. Because of these issues, the diffusion time can be controlled by the you, and has a default value of 1e-5 seconds. Other Combustion Models The spark model is compatible with all combustion models in ANSYS FLUENT. However, the premixed and partially premixed models differ in that the progress variable inside the spark region is set equal to 1, a burned state, for the duration of the spark event. Other combustion models have the energy input into the cell. If the temperature exceeds 2500 K or the spark duration is exceeded, no energy from the spark model will be added to the spark cells. The spark model can be used in models other than the premixed and partially premixed combustion models, however, you must balance energy input and diffusivity to produce a high enough temperature to initiate combustion, which can be a nontrivial undertaking. The model’s use has been extended to be compatible with the other models, however, in some cases it simply creates a high temperature region and does not guarantee the initiation of combustion. 12.2 Autoignition Models Autoignition phenomena in engines are due to the effects of chemical kinetics of the reacting flow inside the cylinder. There are two types of autoignition models considered in ANSYS FLUENT: • knock model in spark-ignited (SI) engines • ignition delay model in diesel engines For information regarding using autoignition models, see Section 20.2: Autoignition Models in the separate User’s Guide. The theory behind the autoignition models is described in the following sections: • Section 12.2.1: Overview and Limitations • Section 12.2.2: Ignition Model Theory Release 12.0 c ANSYS, Inc. January 29, 2009 12-3 Engine Ignition 12.2.1 Overview and Limitations Overview The concept of knock has been studied extensively in the context of premixed engines, as it defines a limit in terms of efficiency and power production of that type of engine. As the compression ratio increases, the efficiency of the engine as a function of the work extracted from the fuel increases. However, as the compression ratio increases, the temperature and pressure of the air/fuel mixture in the cylinder also increase during the cycle compressions. The temperature and pressure increase can be large enough for the mixture to spontaneously ignite and release its heat before the spark plug fires. The premature release of all of the energy in the air/fuel charge is almost never desirable, as this results in the spark event no longer controlling the combustion. As a result of the premature release of the energy, catastrophic damage to the engine components can occur. The sudden, sharp rise in pressure inside the engine can be heard clearly through the engine block as a knocking sound, hence the term “knock”. For commonly available gasoline pumps, knock usually limits the highest practical compression ratio to less than 11:1 for premium fuels and around 9:1 for less expensive fuels. By comparison, ignition delay in diesel engines has not been as extensively studied as SI engines, mainly because it does not have such a sharply defining impact on engine efficiency. Ignition delay in diesel engines refers to the time between when the fuel is injected into the combustion chamber and when the pressure starts to increase as the fuel releases its energy. The fuel is injected into a gas which is usually air, however, it can have a considerable amount of exhaust gas mixed in (or EGR) to reduce nitrogen oxide emissions (NOx). Ignition delay depends on the composition of the gas in the cylinder, the temperature of the gas, the turbulence level, and other factors. Since ignition delay changes the combustion phasing, which in turn impacts efficiency and emissions, it is important to account for it in a diesel engine simulation. Model Limitations The main difference between the knock model and the ignition delay model is the manner in which the model is coupled with the chemistry. The knock model always releases energy from the fuel while the ignition delay model prevents energy from being released prematurely. The knock model in ANSYS FLUENT is compatible with the premixed and partially premixed combustion models. The autoignition model is compatible with any volumetric combustion model, with the exception of the purely premixed models. The autoignition models are inherently transient and so are not available with steady simulations. 12-4 Release 12.0 c ANSYS, Inc. January 29, 2009 12.2 Autoignition Models The autoignition models in general require adjustment of parameters to reproduce engine data and are likely to require tuning to improve accuracy. Once the model is calibrated to a particular engine configuration, then different engine speeds and loads can be reasonably well represented. Detailed chemical kinetics may be more applicable over a wider range of conditions, though are more expensive to solve. The single equation autoignition models are appropriate for the situation where geometric fidelity or resolution of particular flow details is more important than chemical effects on the simulation.
Details
-
File Typepdf
-
Upload Time-
-
Content LanguagesEnglish
-
Upload UserAnonymous/Not logged-in
-
File Pages14 Page
-
File Size-