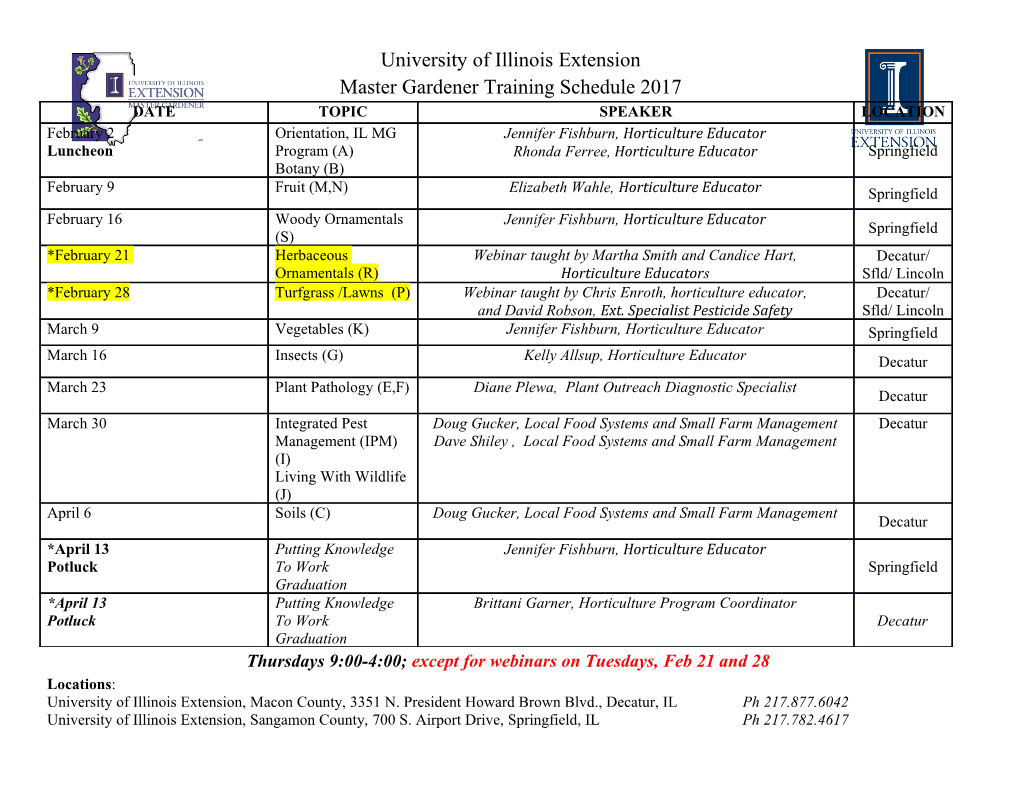
fibers Article Verification and Validation of a Three-Dimensional Orthotropic Plasticity Constitutive Model Using a Unidirectional Composite Canio Hoffarth 1, Bilal Khaled 1, Loukham Shyamsunder 1, Subramaniam Rajan 1,*, Robert Goldberg 2, Kelly S. Carney 3, Paul DuBois 3 and Gunther Blankenhorn 4 1 School of Sustainable Engineering and the Built Environment, Arizona State University, Tempe, AZ 85287, USA; [email protected] (C.H.); [email protected] (B.K.); [email protected] (L.S.) 2 NASA Glenn Research Center, Cleveland, OH 44135, USA; [email protected] 3 George Mason University, Fairfax, VA 22030, USA; [email protected] (K.S.C.); [email protected] (P.D.) 4 Livermore Software Technology Corporation, Livermore, CA 94551, USA; [email protected] * Correspondence: [email protected]; Tel.: +1-480-965-1712 Academic Editors: John W. Gillespie and Subramani Sockalingam Received: 22 January 2017; Accepted: 1 March 2017; Published: 4 March 2017 Abstract: A three-dimensional constitutive model has been developed for modeling orthotropic composites subject to impact loads. It has three distinct components—a deformation model involving elastic and plastic deformations; a damage model; and a failure model. The model is driven by tabular data that is generated either using laboratory tests or via virtual testing. A unidirectional composite—T800/F3900, commonly used in the aerospace industry, is used in the verification and validation tests. While the failure model is under development, these tests indicate that the implementation of the deformation and damage models in a commercial finite element program, LS-DYNA, is efficient, robust and accurate. Keywords: orthotropic composite; plasticity; damage; impact modeling 1. Introduction Modeling and simulation of composites during an impact event is a huge challenge given the wide variety of composites and the associated complexity in characterization of the behavior of the constituent materials as well as the interaction between them. While composites have been in use for decades in a variety of industries such as civil structures, automotive and aerospace, building a predictive model is still daunting. Kaddour et al. [1] list some of the challenges facing the industry. They include (a) shorter life cycles, (b) automated manufacture, (c) production of high volumes, (d) integrating 3D structures into 3D architectures, (e) development of alternative materials, and (f) meeting climate change targets. In the United States, several governmental agencies (including NASA and the FAA) have recognized the importance of building a framework for composites system by forming a public–private consortium. A press release [2] states that “NASA formed the consortium in support of the Advanced Composites Project, which is part of the Advanced Air Vehicles Program in the agency’s Aeronautics Research Mission Directorate. The project’s goal is to reduce product development and certification timelines by 30 percent for composites infused into aeronautics applications.” A major reason for these challenges is the lack of mature material models that should be able to predict, with some degree of certainty, the deformation, damage and failure of composite systems. Several approaches can be used to develop such numerical models. Vaziri et al. [3] categorize the continuum mechanics approaches into four groups—(i) nonlinear elasticity theories; (ii) damage Fibers 2017, 5, 12; doi:10.3390/fib5010012 www.mdpi.com/journal/fibers Fibers 20172017,, 55,, 1212 2 of 1314 theories coupled with elasticity; (iii) classical incremental plasticity theory; and (iv) endochronic theoriesplasticity coupled theory. withExamples elasticity; of these (iii) classicalapproaches incremental and models plasticity can be theory; found and in (iv)[4–9 endochronic]. From the plasticityviewpoint theory. of engineering Examples design, of these models approaches should and be models driven can with be varying found in levels [4–9]. of From input the depending viewpoint ofon engineeringthe complexity design, of the models composite should so bethat driven the material with varying model levels can be of tailored input depending for the required on the complexityresponse. Currently, of the composite however, so many that thematerial material models model are can driven be tailored entirely for by thea few required sets ofresponse. material Currently,properties however,capturing manyorthotropic material deformation models are and driven damage entirely behavior by a. fewThese sets include of material Young’s properties moduli, capturingPoisson’s ratios, orthotropic shear deformation moduli, failure and strain, damage and behavior. reduction These factors include for the Young’s strength moduli, of constituent Poisson’s ratios,parts (fibers) shear moduli, based on failure the strain,failure and of other reduction constituent factors forparts the (matrix strength). ofOthers constituent require parts additional (fibers) basedparameters on the to failure characterize of other failu constituentre using partsclassical (matrix). failure Otherstheories require at the additional macroscopic parameters level, e.g., to characterizeChang–Chang failure or Tsai using–Wu, classical or a mixture failure of theoriesmacroscopic at the level macroscopic and local level,(fiber/matrix) e.g., Chang–Chang driven failure, or Tsai–Wu,e.g., Hashin. or This a mixture type of of approach macroscopic leads leveleither and to models local (fiber/matrix) with only a few driven parameters, failure, wh e.g.,ich provide Hashin. Thisa crude type approximation of approach leadsat best either to the to actual models stress with–strain only curve, a few parameters,or to models whichwith many provide parameters a crude approximationwhich require a at large best number to the actual of complex stress–strain tests to curve, characterize or to models [12]. Often, with many the lack parameters of flexibility which or requiresophistication a large in number these models of complex require tests that to designers characterize adjust [12]. the Often, values the of lacksome of of flexibility the model or sophisticationparameters using in these data models from full require-scale that structural designers tests. adjust the values of some of the model parameters usingIn data the frompresent full-scale approach, structural the composite tests. impact model is divided into a deformation model, a damageIn the model present and approach,a failure model the composite (Figure 1). impact Such a modelpartitioning is divided allows into for athe deformation elastic and model,plastic adeformations damage model to be and captured a failure by model the deformation (Figure1). Such model a partitioning and the reduction allows in for stiffness the elastic to be and captured plastic deformationsby the damage to bemodel. captured In other by the words, deformation the deformation model and themodel reduction simulates in stiffness the nonlinear to be captured material by theresponse damage of model.the composit In othere words,(due to theeither deformation deformation model or simulatesdamage mechanisms), the nonlinear materialand the responsedamage ofmodel the composite simulates (due the tononlinear either deformation unloading ordue damage to stiffness mechanisms), reduction. and theThe damage macroscopic model tabulated simulates thefailure nonlinear model unloadingcaptures failure due to and stiffness does not reduction. rely on characterization The macroscopic of tabulated mechanisms failure leading model to captures failure. failureThe response and does of not a system rely on characterizationcan then be monitored of mechanisms as the leadingfinite element to failure. calculations The response are ofprocessed a system canthrough then the be monitoreddeformation as and the damage finite element models calculations so that the failure are processed model can through be used the to deformation carry out failure and damagepredictions. models The so deformation that the failure model model generalizes can be used the Tsai to carry–Wu out failure failure criteria predictions.. A non- Theassociative deformation flow modelrule is used generalizes and the the yield Tsai–Wu surface failure is based criteria. on strain A non-associative-hardening orthotropic flow rule yield is used function. and the A strain yield surfaceequivalent is based formulation on strain-hardening is utilized in orthotropic the damage yield model function. that permits A strain the equivalent plasticity formulation and damage is utilizedcalculations in the to damagebe uncoupled model and that capture permitss the the nonlinear plasticity unloading and damage and calculations local softening to be of uncoupledthe stress– andstrain captures response. the A nonlinear diagonal unloading damage andtensor local is softeningdefined to of accoun the stress–straint for the directional response.- Adependent diagonal damagevariation tensor of damage. is defined However, to account in composites for the directional-dependent, it has been found that variation loading of in damage. one direction However, can inlead composites, to damage it in has multiple been found coordinate that loading directions in one [19] direction. To account can lead for to this damage phenomen in multipleon, the coordinate terms in directionsthe damage [19 ].matrix To account are semi for this-coupled phenomenon, as explained the terms later. in theThe damage overall matrixframework are semi-coupled is driven by as explainedexperimental later.ly obtained The overall tabulated
Details
-
File Typepdf
-
Upload Time-
-
Content LanguagesEnglish
-
Upload UserAnonymous/Not logged-in
-
File Pages13 Page
-
File Size-