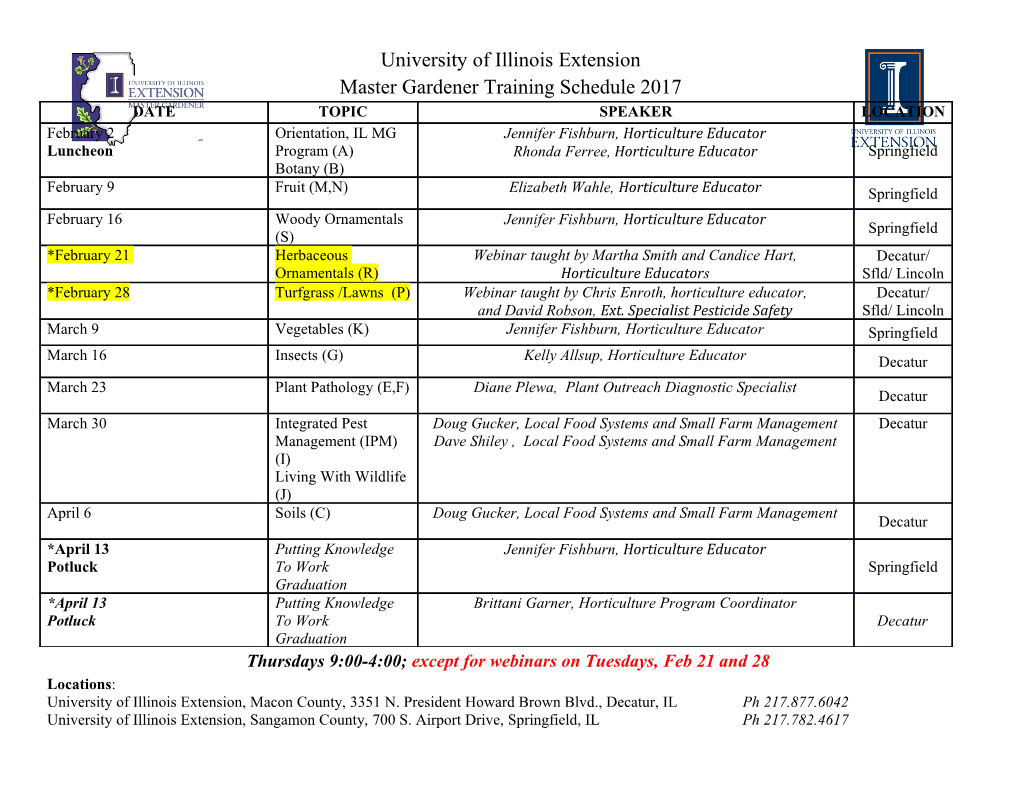
Master Thesis Master's Programme in Mechanical Engineering, 60 Credits Design and Fabrication of Moulds using Additive Manufacturing for producing Silicone Rubber Products Thesis in Mechanical Engineering, 15 credits Halmstad 2020-05-29 Shreyas Kantharaju, Jobin Varghese HALMSTAD UNIVERSITY PREFACE Industries all around the world is looking forward to reducing their investments in design, production and manufacturing processes. They are implementing new technologies to their business for improving performance and productivity. Additive manufacturing is one among those booming technologies which opens new revolutionary methods in the field of manufacturing. It enables to produce complex shaped objects in a less costly and time-consuming ways, it also allows designers to directly test their designs by prototyping and make any design changes if required to improve or optimize the designs. Along with low production cost and less production time the other factors like the product functionality and other properties like strength, surface quality etc., becomes important. This thesis is a part of an on-going project of DiSAM – Digitalization of supply chain in Swedish Additive Manufacturing in collaboration with Halmstad University and Unimer Plast & Gummi AB. The aim of this project is to implement Additive manufacturing technology into the supply chain industry. In this thesis we mainly focus on design and fabrication of a simple and a complex mould geometry for producing Silicone Rubber products using Additive Manufacturing and to test the quality of the product obtained in terms of surface topography. In addition, post- processing methods are implemented to enhance the quality of the moulded silicone rubber products and compared to the reference injection moulding parts. i Abstract Now a days. additive Manufacturing is becoming a major part of the manufacturing industries all around the world. Even, it is still a developing field. Its main advantage is its ability to print different types of shapes, in different sizes and good quality. The additive manufacturing technologies is capable of bring down the costs of the manufacturing when compared to other traditional methods of manufacturing. This technology gives the flexibility to making complex shapes according to the clients and customers requirements also this technology can reduce time and human effort/involvement needed in the manufacturing industries. Now 3D printing has more influence in Swedish market more than ever and this thesis is a part of a project of DiSAM – Digitalization of supply chain in Swedish Additive Manufacturing to implement 3D Printing into Swedish market. This thesis describe how advance materials and new manufacturing technologies can play a very important role in building the future and from this study we are trying to find out whether the additive manufacturing technology can replace the traditional manufacturing process like injection molding. The main aim of the thesis is to design and fabricate a simple mould geometry for producing Silicone Rubber products using additive manufacturing and to assess the quality of the obtained product in terms of surface topography, dimensional accuracy and mechanical properties. Our project partner Unimer Plast & Gummi AB who is a major producer of plastics and rubber products is facing a problem in the production of silicone rubber products. They want to produce a mould for producing silicone rubber products using additive manufacturing. In this thesis we had made the study in two parts, a design part and an analysis part. In the design part we sorted out one material which is suitable for our application that is to produce a mould for making silicone products while in analysis part we made a study about the surface topology and its quality to see whether 3D printed moulds could produce silicone rubber products with same or better surface quality than the one which are produced using conventional injection moulding process. As a result of our study we came to know that high temperature resin can be used for making moulds to produce silicone products and only factor affecting the quality of the surface of mould or silicone product is built orientation and other factors like layer thickness, curing temperature and time does not have any impact on the surface quality. ii ACKNOWLEDGEMENT This thesis is a part of a major project developed by DiSAM for implementing additive manufacturing in Swedish supply chain. We were able to achieve satisfying results from this research. We take this opportunity to thank who all have become a part and helped us to achieve and complete this project. First and foremost, we like to thank God Almighty in helping us in completing this project. We express our sincere gratitude to our Prof. Bengt-Göran Rosén, Department of Mechanical Engineering, Halmstad University, Sweden for his help, generous guidance and support. We express our heartful gratitude to our Supervisor Mr. Amogh Vedantha Krishna, Department of Mechanical Engineering, Halmstad University for being with us in every step, continuous guidance and moral support. We also express our thanks to Mr. Stefan Rosén, Toponova AB, for his help and guidance for taking measurements using GFM MikroCAD and Interferometer instruments. We also express our thanks to FabLab crew, Halmstad University namely Martin Bergman, Joakim Wahlberg, Tim Malmgren and Andre Stadelmann for their help, guidance and support iii LIST OF CONTENTS PREFACE i ABSTRACT ii ACKNOWLEDGEMENT iii LIST OF FIGURES vi LIST OF TABLES viii LIST OF GRAPHS xi 1. INTRODUCTION 1 1.1 BACKGROUND 1 1.1.1 REPRESENTATION OF OUR CLIENT 2 1.2 AIM OF THE STUDY 3 1.2.1 PROBLEM IDENTIFICATION 3 1.3 LIMITATIONS 3 1.4 STUDY ENVIRONMENT 4 2. THEORY 5 2.1 ADDITIVE MANUFACTURING 5 2.2 SILICONE RUBBER 10 2.3 DESIGN OF EXPERIMENTS 11 2.4 SURFACE MEASUREMENTS 12 2.5 DATA ANALYSIS 19 3. METHOD 21 3.1 RESEARCH METHODOLOGY 21 3.2 ALTERNATIVE METHODS 21 3.3 CHOOSEN METHODOLOGY 22 3.4 DATA COLLECTION 31 4. RESULTS AND DISCUSSIONS 33 4.1 PHASE 1 33 iv 4.2 PHASE 2 54 5. CONCLUSION AND FUTURE ACTIVITIES 57 5.1 CONCLUSION FROM OUR RESEARCH 57 5.2 FUTURE RESEARCH ACTIVITIES 57 6. CRITICAL REVIEW 58 REFERENCE 59 APPENDIX 62 v LIST OF FIGURES Figure 1: Classification of Additive Manufacturing 5 Figure 2: FDM Printer Principle 6 Figure 3: FDM Printing Process 7 Figure 4: SLA Printer Working Principle 8 Figure 5: SLA Printer Process 9 Figure 6: GFM MikroCAD Instrument 13 Figure 7: Average Roughness and Root Mean Square Roughness 16 Figure 8: Abbott Curve 16 Figure 9: Material Ratio Curve from MountainsMap 17 Figure 10: Str and Sal Surface Parameters 17 Figure 11: Texture Direction 18 Figure 12: Root Mean Square gradient (Sdq) (Sa = 80 nm, Sdq=11.0 deg). 18 Figure 13: PEEK Printer and the Filament 21 Figure 14: PEEK Printed moulds 21 Figure 15: Methodology Chart 22 Figure 16: Step wise procedure to capture images in GFM MikroCAD 26 Figure 17: Mountains Map software Logo 27 Figure 18: History of Operation Chart for flat surface 28 Figure 19: History of Operation Chart for curved surface 28 Figure 20: Data Analysis Process Flow Chart 29 Figure 21: Part 1 – Identification of significant parameters 30 Figure 22: Part 2 – Identification of significant influence of independent variable on significant parameter 30 Figure 23: Trail testing of silicone sample 33 Figure 24: Silicone Rubber tested at different temperatures according to the table 1 34 Figure 25: PLA and ABS Mould 36 Figure 26: Silicone sample from PLA mould 36 Figure 27: Basic design of the mould in PEEK 36 Figure 28: Silicone sample obtained from PEEK 36 Figure 29: Actual Design of the mould in PEEK with 30*13 mm 37 Figure 30: Silicone samples obtained by using PEEK mould 37 Figure 31: Design 1 Mould printed in HT 39 Figure 32: Silicone Sample from HT 39 Figure 33: Mould break after testing 39 Figure 34: Design 2 Mould 40 Figure 35: Silicone sample D2 -1 41 Figure 36: Silicone sample D2 -2 41 Figure 37: Design 3 Mould 41 Figure 38: Silicone sample of D3 42 vi Figure 39: Design 4 Mould-CAD Images 43 Figure 40: Design 4 actual printed mould 43 Figure 41: Silicone sample of D4 43 Figure 42: Silicone samples obtained using Taguchi Experimentation 44 Figure 43: Reference Silicone Sample 45 Figure 44: Solid Block Design 54 Figure 45: 4-Part Mould Design 55 Figure 46: Sample obtained using 4-Part Mould Design 55 Figure 47: CAD Model of Complex shape silicone sample 56 Figure 48: Sustainability 58 Figure 49: Other silicone samples used for testing and observations with different time and time 59 Figure 50: 3D Printed Tool used to shape silicone rubber 60 Figure 51: Other Mould Design (PLA) 60 Figure 52: Other version of design 4 61 Figure 53: Basic Mould Design (PLA) 61 Figure 54: Design 4 mould under pressure 61 Figure 55: SLA Printed Mould Part (90 Build Inclination) 62 vii LIST OF TABLES Table 1: Surface Parameters Table 14 Table 2: Outline to capture the observations of Silicone Samples 24 Table 3: Taguchi Orthogonal Experimental Design 25 Table 4: Observations from testing silicone rubber without mould 34 Table 5: Observation from the testing of different moulds 38 Table 6: Observation Table on Tested Silicone Samples 44 Table 7: Observation of Silicone Rubber using Taguchi Experimentation 45 Table 8: Comparison in 3D images build inclination of silicone samples at 0 and 90 47 Table 9: Regression Analysis Statistics 48 Table 10: Significant Parameters Table 49 Table 11: Most Significant Parameters obtained using Correlation Analysis 50 Table 12: Taguchi Experiments with Coatings 62 Table 13: Taguchi Experiments without Coatings 62 viii LIST OF GRAPHS Graph 1: Average Roughness Graph 51 Graph 2: Void Volume Graph 52 Graph 3: Core Roughness Depth Graph 53 Graph 4: Density of Peaks Graph 53 ix 1.
Details
-
File Typepdf
-
Upload Time-
-
Content LanguagesEnglish
-
Upload UserAnonymous/Not logged-in
-
File Pages76 Page
-
File Size-