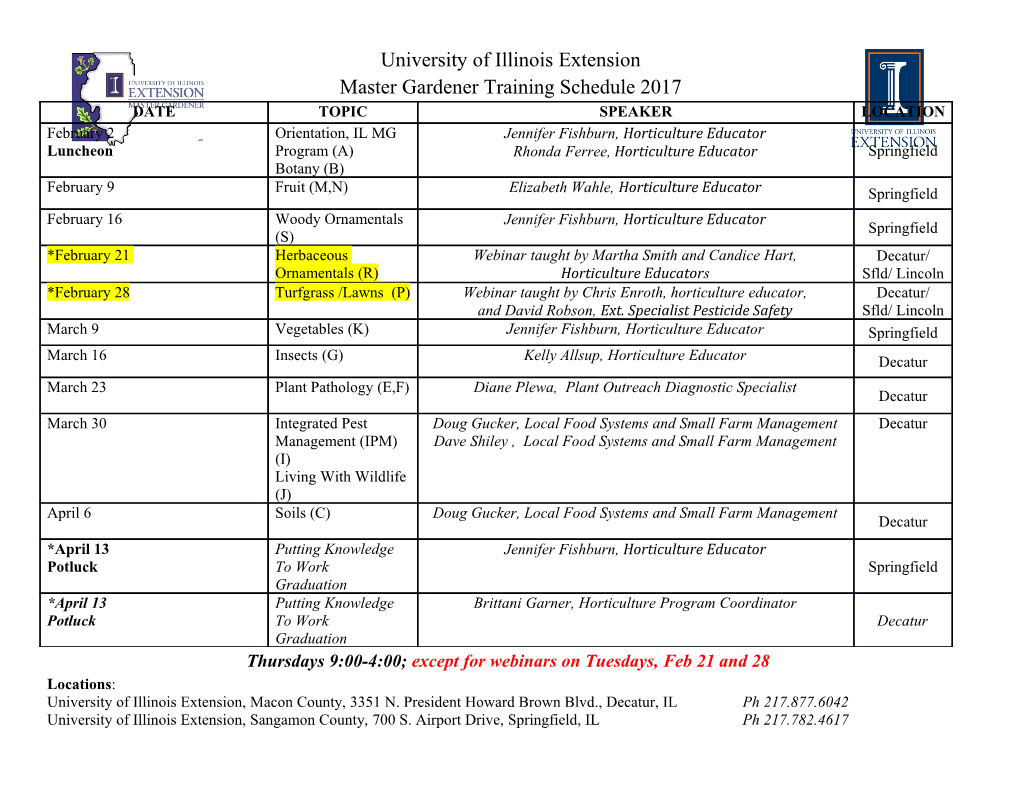
primary focus will be on the grain whisky distillation processes currently found in Scotland. Continuous distillation is a form of distillation where a mixture is con- tinuously fed into the process – and separated fractions are continuously removed as output streams. Distillation is the separation, or partial separation, of a liquid feed stream into individual components or fractions by selective boiling, evaporation and condensation. These continuous processes are generally driven by thermal energy in the form of steam and produces at a minimum two output fractions – at least one volatile distillate fraction which has been boiled and separately recovered as a vapour condensed to a liquid and a bottoms fraction which is the least vola- tile residue which has not been sepa- rately captured as a condensed vapour. Continuous distillation is used widely in the chemical process industries where large quantities of liquid have to be distilled and separated either into single individual components or fractions. This article concentrates on this chemical engineering process as it re- lates to the potable alcohol industry. This is also used extensively in the very large capacity fuel alcohol industry. Continu- ous distillation in the potable alcohol industry has its roots in the early 1820s- 30s when different types of plant were designed, built, installed and operated Stripping and rectifi cation columns at to signifi cantly increase product output Adnams Copper House Distillery (© Adnams) which to that time had been limited to the small batch pot still distillation Continuous distillation processes in the lowlands of Scotland. Continuous distillation The early continuous stills were de- Grappling with grain whisky signed and patented by Robert Stein and Aeneas Coffey, two enterprising production engineers and designers of the time. These early designs, particularly the By Billy Mitchell Coffey stills, form the basis of many of the plants remaining in operation in This is the sixth article in the series to support those Scotland today. The main distillation plant found in studying for the General Certifi cate in Distilling and builds use today will consist of a large wash on the previous article in the series around the batch/pot charger, beer, analyser or stripper column, a rectifying column, various still distillation process. This type of continuous process is overhead condensing process, pumps, widely used, in various forms, in the production of whisk(e)y, pipe work, a fusel oil removal system, heat recovery and reuse, product potable neutral alcohol and non-potable fuel alcohol. off-take streams including systems to remove spent wash, product spirit, and t is also widely used in many other raw material input and pre-distillation fusel oils. Itypes of spirits production around the processes may be very different. The process will also include the world. Although the main focus of this This article will cover the theory, provision of thermal energy in the form article will be grain whisky produc- principles and practicalities – and of steam supplied either through live tion, the theory and risks are common general risks – associated with the steam injection, thermo compressor or across all distilled liquid types – and continuous distillation processes. The re-boiler systems. This is a very ener- 50 z Brewer and Distiller International June 2017 www.ibd.org.uk BASICS OF SPIRITS PRODUCTION l gy-intensive continuous process which Hopefully some, if not all of these can be designed, built and operated on will be more recognisable once you a range of input capabilities ranging have completed this article. from ~1500 litres/hour to larger plant operating at input capacities of well Distillation theory over 60,000 litres/hour. Distillation can be described as a These continuous distillation pro- process for separating the compo- cesses when operated in steady-state nent substances in a liquid mixture conditions are very efficient at recovery by evaporation and condensation. The of ethyl alcohol and various flavour principle of continuous distillation is components from the input wash feed the same as for pot still distillation and are designed to recycle and re- – when a liquid mixture is heated to cover various liquid streams to ensure boiling point, the composition of the ethyl alcohol recovery is maximised vapour above the liquid differs from with little or no loss of alcohol. the liquid composition – and if this In potable alcohol production there vapour is separated and condensed is no one design or layout of plant. into a liquid, it becomes richer in the Designs have evolved from the early lower boiling point compound(s) of the rectangular, wood and copper stills – original liquid. and can now be found as rectangular, This is the basis for continuous circular or a combination of both, and distillation. The liquid/solids mixture is constructed either in stainless steel or Coffey still from Kilbeggan Distillery in heated up and fed into the distillation copper – or a combination of both. As County Westmeath in Ireland. (Photo: column, where the feed initially starts already stated they can be designed, HighKing on Wikimedia Commons) to flow down the column but where constructed, installed and operated as it is in the small-batch pot still the higher volatile (lower boiling point) at a huge range in wash feed input processes. Use of this metal in the compounds are vaporised and rise up rates and product spirit recovery rates. relevant areas of this plant will remove the column. These processes can be operated these undesirable flavour compounds, As this vapour rises it eventually under normal atmospheric pressure, ensuring production of a good consist- cools and while a portion continues under vacuum, at high pressure or a ent quality of product. These off-odour up as vapour, some of it enriched in combination of these. removal reactions are not required in the less volatile components beings Each of these conditions will the large fuel-alcohol plants. to descend as liquid. Figure 1 gives an have variations in energy input and Continuous distillation plants, example of a distillation apparatus for in general will have been chosen to whether operating at low- or high- separating some form of feed into two deliver best fit with your other process input rates lend themselves readily to plant and how they are configured. semi- or fully-automated control. The Condenser Their key task is the same whether key to delivery of product at optimised operating under pressure, vacuum or energy consumption is best achieved atmospheric – to separate the alcohol when operating under steady condi- Cooling Water Reux and other required flavour compounds tions with consistent wash feed, ther- Drum from the fermented wash in a con- mal energy supply, clean condensing Reux tinuous process and to recover the systems, consistent spirit off take and required volume and quality of final recovery and return of recycled liquid product with optimum energy input. streams. Pump The feed material for this process As is the case within the whisky is fermented wash containing ethyl al- industry there is a list of terminologies Overhead product cohol and other minor flavour constit- which are aligned to this continuous pro- Feed uents (which can be either desirable cess – these may include the following: or undesirable in final product), water Fermented wash, wash charger, hot and solid material (mainly unferment- and cold feints, spirit safe, fusel oil Distillation Column Distillation plate ed cereals and yeast.) This fermented column or fusel oil decanter, steam Vapour wash may contain all the solids from thermo compressor or re-boiler, wash Reboiler the cooking, mashing and fermenta- coils or other external heat recovery tion processes, or can be relatively processes, spirit plate, the bend, the Steam solids free where the primary solids bend temperature, overhead con- Condensate have been removed and recovered denser, re-ascending wash lines, down after mashing. comers, valves and triangular pitch, Bottoms Bottom These cereal solids have come rectifier and analyser plates, conge- liquid product from the maize, wheat or malt element ners, on water, on wash, on spirit, off of the mash bill which is governed by spirit, spent wash, pressure relief and Upowing vapour Downowing liquid the capability of the pre-distillation anti vacuum systems, spirit charges processes. and spirit receiver, feints receivers… Figure 1: Separation into two fractions: overhead distillate The use of copper in the manufac- as well as temperature, pressure and product and bottoms product. Note the column itself is ture of these continuous stills is as flows associated with this continuous divided into two sections: Rectifying (above feed) and important in these production plants operation. Stripping (below feed) www.ibd.org.uk Brewer and Distiller International June 2017 z 51 l BASICS OF SPIRITS PRODUCTION 0.75 – they are much less effective than wash is alcohol-free if the process is top vapor any ideal model stage thus the actual fully optimised. There should be no fraction to number of plates required is calculated alcohol loss through this stream. This condenser by dividing the number of theoretical material is boiling water containing reux stages by the plate efficiency. non-fermentable material in solution In principle both the stripping and with grain and yeast debris. It can then r rectification processes could take be removed via heat recovery processes place within the one column but in for further processing as animal feed or downcome r practice these are split into two sepa- potentially as a ‘green’ energy source. Trays rate processes primarily due to the downcome r overall height and practical civil and Rectifier column recti cation mechanical engineering difficulties These columns also vary in shape and Feed encountered in building and erecting size and also in the number of plates. downcome Feed tray a single tall column. Figure 4 shows Hot vapour from the top of the stripper the construction of a McCabe-Thiele column passes through the vapour pipes downcomer model for ethanol-water separation.
Details
-
File Typepdf
-
Upload Time-
-
Content LanguagesEnglish
-
Upload UserAnonymous/Not logged-in
-
File Pages7 Page
-
File Size-