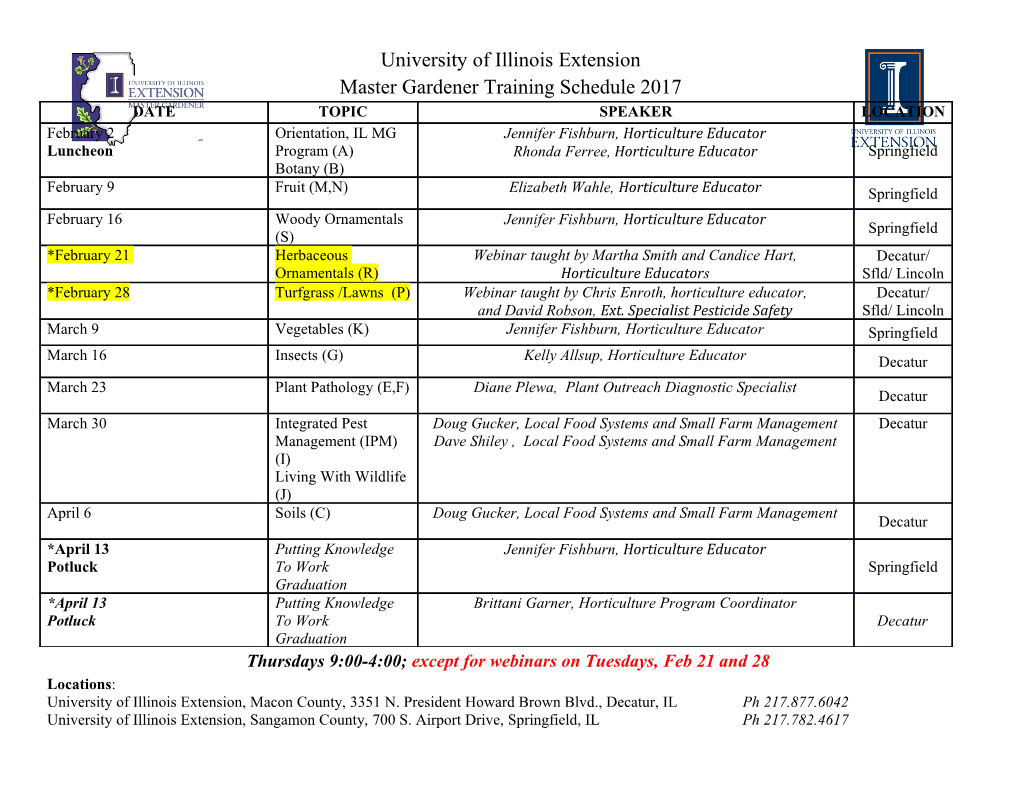
HP PE/SolidDesigner: Dynamic Modeling for ThreeĆDimensional ComputerĆAided Design In most solid modeling CAD systems, knowledge of the history of the design is necessary to avoid unanticipated side-effects when making changes. With dynamic modeling, local geometry and topology changes can be made independently of the model creation at any time, using both direct and dimension-driven methods. The core components enabling dynamic modifications are the tool body and the relation solver. by KlausĆPeter Fahlbusch and Thomas D. Roser HP Precision Engineering SolidDesigner (PE/SolidDesigner)page 15), managed as part and assembly structures, deleted, is a 3D solid modeling design system based onand the ACIS used to create solids. Attributes such as color can be Kernel (see About Kernels" on next page). It providesmodified. the If the set of surfaces is closed, HP PE/SolidDeĆ geometric model needed by design workgroups in productsigner will create a solid from those surfaces automatically. development environments. The system's dynamic modelingOther solid modeling systems, which are historyĆbased, are technology gives the designer the freedom to incorporateunable to import data and then modify it as if it had been changes at any time and at any stage of productcreated developĆ within the system itself. ment, without dependence on the history of the product HP PE/SolidDesigner allows solid parts and assemblies to be design. exported to ACISĆbased systems using Version 1.5 of the HP PE/SolidDesigner is a member of the HP PrecisionACIS EngiĆ SAT file format. This feature provides a direct link to neering Systems (PE/Systems) product family. Today,other HP ACISĆbased applications. PE/Systems consists of: With HP PE/SolidDesigner, users can set part and layout • HP PE/SolidDesigner for solid modeling accuracy. Because users can model with parts of different • HP PE/ME10 for 2D design, drafting, and documentation accuracy by forcing them to a common accuracy, they can • HP PE/ME30 for 3D design import and work on models from other CAD systems regardĆ • HP PE/SurfaceStyler, an engineering styling application inteĆ less of their accuracy. grated with HP PE/SolidDesigner • HP PE/SheetAdvisor, a sheetĆmetal designĆforĆmanufacturĆDynamic modeling is the underlying methodology within HP ability application PE/SolidDesigner. This flexible, nonhistoryĆbased, intuitive • HP PE/WorkManager for product data and workflow design technique provides direct interaction with modeling management tools and designs, allowing the engineer to focus effectively • HP PE/DDSĆC for electrical system design on the design task. • HP PE/Complementary Application Program (CAP), a joint research and development and marketing program thatHP proĆ PE/SolidDesigner allows designers to work with userĆ vides HP PE/Systems users with access to more thandefined 200 features to capture design intent. Users can explicitly leading applications from 70 companies. group a variety of 3D elements such as faces and edges of a part. These features then can be viewed, edited, renamed, HP PE/SolidDesigner deleted, or used to drive changes to a design. HP PE/SolidDesigner makes it easy for designers toHP move PE/SolidDesigner to has variable radius blending, which 3D solid modeling. It supports the coexistence ofallows surface users to create, modify, and remove variable blends. data with solid data and provides the ability to importThey can and now create constant and variable blends during modify surface and solid design data from a varietyone of session. CAD Another new feature, called shelling, provides a systems. It also offers new modeling functionality andquick enĆ way for users to create thinĆwalled parts from solids, hanced ease of use. as in injectionĆmolded parts, for example. Using improved IGES (Initial Graphics Exchange Standard)Also new in HP PE/SolidDesigner is mass property capabilĆ import capability, both surface and wireframe data canity. The be following properties can be calculated for parts and imported. Surface data and solid data can also beassemblies: imported face area, volume, mass, center of gravity, inertia and exported using the STEP (Standard for the Exchangetensor, and of boundary area. Tolerances can be supplied and Product Model Data) format. Once imported, this dataachieved can accuracies are returned. HP PE/SolidDesigner also coexist with HP PE/SolidDesigner solid data. It canincorporates be interferenceĆchecking capabilities, which loaded, saved, positioned, caught to (see footnote on 6October 1995 HewlettĆPackard Journal allow detection of interference, face touching, and noninterĆDynamic Modeling ference of assemblies and part combinations. The resultsDynamic can modeling has been developed by HP to overcome be shown as text reports or in graphic format withthe color many problems designers experience with historyĆbased coding for easy identification. CAD systems. In particular, it aims to remove any dependenĆ cies on history and the need to anticipate future changes. About Kernels. A kernel is the heart of a modeling system. Currently, three kernels are used in various CAD systems.The concept underlying dynamic modeling is to make optiĆ These are Romulus from Shape Data, Parasolid, anmal extension use of technologies without constraining the designer's of Romulus, and the ACIS Kernel from Spatial Technology.creativity and flexibility. In contrast to historyĆbased systems, The ACIS Kernel is rapidly becoming a de factodynamic standard, modeling allows direct manipulation of model eleĆ having been accepted to date by 25 other commercialments licensĆ in 3D space. With dynamic modeling, local geometry ees, 50 academic institutions, and 12 strategic developers.and topology As changes can be made independently of the of July 1995, companies that officially have committedmodel to creation at any time, using both direct and dimensionĆ using ACIS as their underlying technology include MacNealĆdriven methods. In the latter case, dimensions can be speciĆ Schwendler/Aries, Applicon, Autodesk, Bentley Systems, fied at any stage in the design, not just at the outset. CADCentre, HewlettĆPackard, HitachiĆZosen Information Systems, Camax Manufacturing Technologies, Intergraph,The core components enabling dynamic modifications are and Straessle. the tool body and the relation solver. To make a model modification a tool body is created and then transformed to About STEP. The STEP protocol for data exchange isthe the appropriate position. A Boolean operation between the product of a group of international organizations includingoriginal model and the tool body results in the desired PDES/PDES Inc. USA, a joint venture with severalmodel member modification. companies, ESPRIT (European Strategic Program for ReĆ search and Development in Information Technology),HP EuroĆ PE/SolidDesigner is the only currently available CAD pean data exchange technology centers such as CADDETCsolution that uses dynamic modeling. The remainder of this (CADCAM Data Exchange Technical Centre) and GOSET,article describes the underlying technology of dynamic modĆ and ProSTEP, the German industry project for establishingeling and compares it with other methods like parametric STEP in the automotive industry. model modification techniques. HP has been active in STEP technology since 1989State through of the Art projects such as CADEX (CAD Geometry Exchange),Currently, PROĆ solid modelers use two different approaches to DEX (Product Data Exchange), and ProSTEP. HP providescreate the final geometrical model. CSG (constructive solid STEP processors with its HP PE/SolidDesigner 3D solidgeometry) modelers are based on volume set operations modeling software. with volume primitives such as cubes, cones, or cylinders. This approach is characterized by a Boolean engine, which Dynamic Modeling implements the basic operators unite, subtract, and intersect. The sequence of all the Boolean operations, parameters, and CSG tree Currently, the most popular 3D CAD solutions arepositions historyĆ of the primitives are kept in. the ModificaĆ based. When designing with these systems, dimensionstion and of the solid later in the design process can be done by parameters have to be specified at the outset. Theusing model more can primitives or by editing the CSG tree. Local modĆ only be manipulated indirectly by modifying these dimenĆifications of the model are not possible, since no access to sions and parameters. The initial definitions have afaces major or inĆ edges is given. This cumbersome way to modify fluence on the ease or difficulty of carrying outsolids subsequent requires the user to analyze the design beforehand modifications, which can only be reliably implementedand if dissect all it into the necessary primitives and operations. the previous steps in the design process are known.While LaboriĆ anticipating design modifications and building designs ous manipulation may be necessary to make changesout that, of primitives is not typical in the mechanical engineering intuitively, should be achievable in a single step. design process, pure Boolean modelers have proven useful when entering a final design for postprocessing, such as for Unless the history of the design is thoroughly understood,finiteĆelement analysis (FEM) or NC tool path programming. any change made to a model may have unanticipated sideĆ effects. Relatively straightforward changes to the modelBĆRep inĆ (boundary representation) modelers represent the volve many convoluted steps. Future interpretation becomessolid by concatenating surfaces
Details
-
File Typepdf
-
Upload Time-
-
Content LanguagesEnglish
-
Upload UserAnonymous/Not logged-in
-
File Pages8 Page
-
File Size-