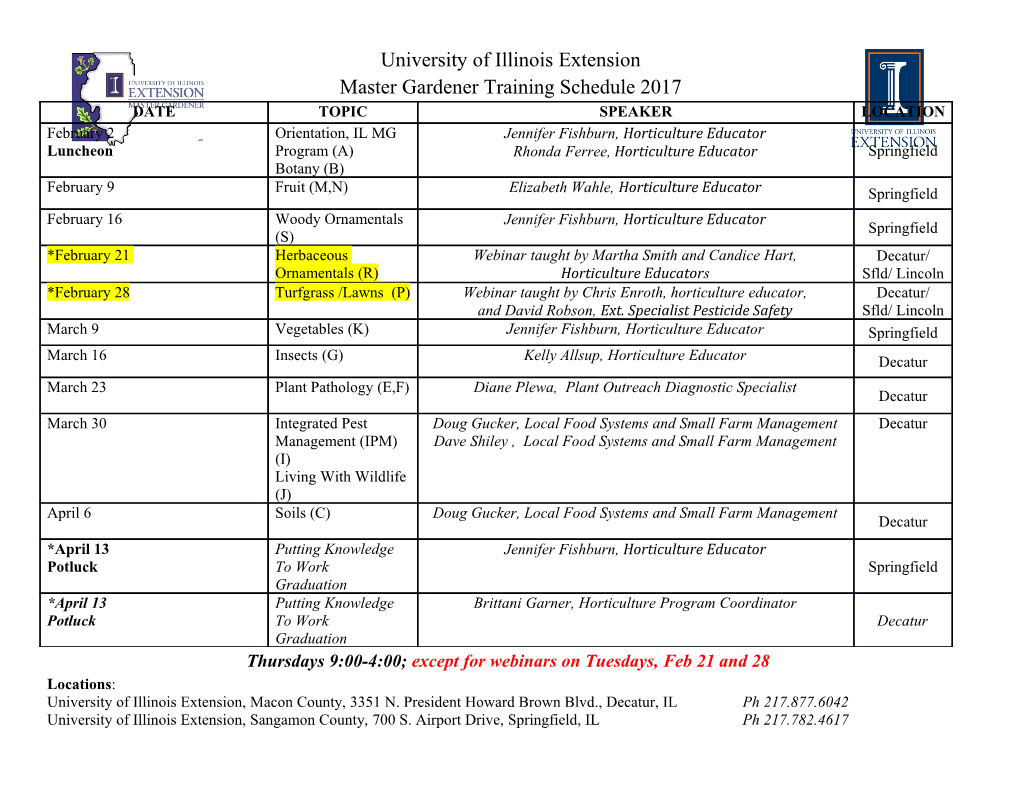
Toward the chill-down modeling of cryogenic upper-stage engines under microgravity conditions using the thermal-hydraulic code COMETE G.-M. Moreau, Kc. Le Thanh, C-H. Bachelet, D. Duri To cite this version: G.-M. Moreau, Kc. Le Thanh, C-H. Bachelet, D. Duri. Toward the chill-down modeling of cryogenic upper-stage engines under microgravity conditions using the thermal-hydraulic code COMETE. EU- CASS 2015 - 6th European conference for aeronautics and space sciences, Jun 2015, Cracovie, Poland. cea-02500837 HAL Id: cea-02500837 https://hal-cea.archives-ouvertes.fr/cea-02500837 Submitted on 6 Mar 2020 HAL is a multi-disciplinary open access L’archive ouverte pluridisciplinaire HAL, est archive for the deposit and dissemination of sci- destinée au dépôt et à la diffusion de documents entific research documents, whether they are pub- scientifiques de niveau recherche, publiés ou non, lished or not. The documents may come from émanant des établissements d’enseignement et de teaching and research institutions in France or recherche français ou étrangers, des laboratoires abroad, or from public or private research centers. publics ou privés. Toward the chill-down modeling of cryogenic upper-stage engines under microgravity conditions using the thermal-hydraulic code COMETE G.-M. Moreau, CEA Grenoble K.-C. Le Thanh, CEA Grenoble C.-H. Bachelet, Snecma Vernon D. Duri, Snecma Vernon Commissariat à l’Energie Atomique et aux Energies Alternatives, DEN, DANS/DM2S/STMF/LMES, 17 rue des Martyrs, F-38054 GRENOBLE, France. Tel: 33 438 78 49 56 Fax: 33 438 78 51 95 SNECMA groupe SAFRAN Forêt de Vernon 27208 VERNON, France. Tel: 33 232 21 70 63 Fax: 33 232 21 77 65 In order to understand the critical microgravity chill-down phase, CATHARE and COMETE 1 ABSTRACT simulations of specially instrumented Ariane 5 The design of the Vinci re-ignitable upper commercial flights will be carried out. During stage cryogenic engine requires detailed such flights an additional chill-down is analysis, modeling activities and experimental performed on the HM7B/ESC-A upper-stage work in order to optimize the engine chill- after the separation of the payload and prior to down phase in a paramount effort to further the upper stage safety neutralization. The increase the launcher payload. Prior to any simulation results will be compared to the Vinci starting sequence the oxidizer and fuel available telemetry data in order to validate the feeding lines and turbo-pumps must be numerical tools and the modeling properly preconditioned and cooled down. methodology. Moreover due to the Vinci re-ignition capability the chill-down phase has to be performed during the upper stage coast phases 2 INTRODUCTION under microgravity conditions. The 180 kN Vinci expander-cycle cryogenic rocket engine is designated to equip the new As a high efficiency of the chill-down process Ariane 6 upper stage and it combines the is required to achieve the minimum significant experience accumulated in consumption of propellants within the designing, developing, qualifying and established duration and temperature criteria to producing the previous European cryogenic fully understand the chill-down thermo-fluid flight-proven engines such as the HM7B and dynamics and to reliably predict the heat the Vulcain family, with new advances in transfer rates and temperature history of the manufacturing processes (powder metallurgy propulsion system, Snecma developed the impellers, cooling channel high speed milling thermal-hydraulic code COMETE by coupling ([R1]-[R5]) and the extensive use of integrated and adapting the unsteady thermal code analytical and numerical tools offering a Samcef-Thermal, developed by Siemens, and significant decrease in terms of tests state-of-the-art thermal-hydraulic code requirements, as well as increased performance CATHARE, developed by CEA. While the and reliability through simplicity of design and former simulates the thermal evolution of recurring cost reduction. complex 3D parts such as the engine turbo- pumps and regenerative circuits of the Vinci engine, the CATHARE code is used to model the hydrogen and oxygen two-phase flows. Since the Vinci engine is designed to be reignited several times the chill-down phase has to be performed not only during the boost phase (EPC flight) of the lower stages but also during the upper stage coast phases. As a consequence of the significant difference in densities between the liquid and gas phases the reduced gravity condition strongly changes the flow patterns (with respect to the 1-g gravity level) and accordingly affects the momentum and energy equations. Boiling and two-phase flow behave differently when the gravity levels vary, leading to a significant reduction in heat Figure 1: View of the Vinci expander-cycle exchange and therefore to a less efficient chill- engine with the nozzle extension deployed down process with potentially higher [R6]. consumption and longer cool down durations [R6]. A high efficiency of the chill-down The liquid oxygen and hydrogen cryogenic process is therefore paramount and the cooling engine is designed for multiple re-ignitions to sequence must be optimized to achieve the increase the versatility of the A6 upper stage in minimum consumption of propellants within delivering and positioning payloads in multiple the established duration and temperature high energy orbits. The re-start capability also criteria whilst taking into account every allows a controlled de-orbiting or injection of extreme external boundary condition range the upper stage in graveyard orbit, hence value. contributing to the protection of the space environment from pollution and debris. In order to address all these issues Snecma in partnership with CEA and Siemens developed An important contribution to the overall the multi-physics code COMETE to meet the performance of the launcher is the engine chill- following goals: down. Prior to any Vinci starting sequence the propellant feeding lines, the turbo-pumps and Predict the flight performance of their bearings must be properly preconditioned different chill-down methods and and cooled down. This process involves sequences in order to reduce the complex unsteady two-phase cryogenic flow propellants consumption by numerical due to the low boiling point of the propellants. testing during the first boost and The complexity of the problem results from the microgravity flight phases. non-linear interaction of the fluid dynamics Predict the global behavior of the chill- and heat transfer during phase-change. The down system, the duration to meet the initial phase of chill-down is dominated by the temperature criteria of the turbo- massive evaporation of the cryogens. As the pumps, with respect to the Net Positive system cools down, slugs of liquid entrained Suction Pressure (NPSP) margins and by the gas stream, flow through the system in a the bearing temperature requirements. two-phase film boiling mode followed by the Perform structural analysis during the propagation of the liquid quenching front thermal transient of the turbo-pumps accompanied by nucleate boiling. As the assembly in order to identify thermal system further cools down, the two-phase flow stress concentration areas. undergoes several flow regime transitions until Support the Vinci testing campaign it reaches a single-phase liquid flow. These activities. phenomena are inherently unstable and can lead to extreme flow and pressure fluctuations. Assess the risk of propellant The flight hardware may also be subject to solidification inside the chill-down mechanical stresses due to thermal differential purge lines and the margins with contraction. respect to the triple point pressure and temperature of the cryogens. Predict the thrust generated by the ground chill-down model up to the flight vented cryogens. prediction simulation. The limits of the existing procedure are listed as well as the The successful contribution of the multi- logic of the experimental numerical activities physics code COMETE to the Vinci engine carried out to validate the global behavior of Critical Design Review (CDR) regarding the the code and the soundness of the fitting chill-down performance simulations and feed procedure by simulating the HM7B-equipped valves opening sequences along with the study ESC-A upper stage. of degraded chill-down cases marked in 2014 the first milestone for the industrial application of the code [R11]. 3 NUMERICAL SIMULATION TOOLS In order to further increase the capabilities of the code and to improve the simulation 3.1 Basis principles of COMETE methodology and the flight prediction The coupling strategy of the COMETE reliability an additional effort has been software is based on the coupling of two undertaken focusing on the specific problem of independent softwares : the flow solver the chill-down under 0-g conditions [R7-R8]. CATHARE developed by CEA and the In the past fundamental research activities have conduction solver Samcef-Thermal developed been carried out to study the heat transfer by LMS-SAMTECH/Siemens (Liège, correlations and closure equations in Belgium) controlled by a Master process called microgravity to be later implemented in the Supervisor. The Supervisor, also developed by numerical tool COMETE [R6]. Nevertheless LMS-SAMTECH/Siemens using the MPI the limited data available in terms of message-passing library, allows data reproducibility (the duration experiments is exchanges between the codes. The Supervisor relatively short due to technical constraints sets the duration of the
Details
-
File Typepdf
-
Upload Time-
-
Content LanguagesEnglish
-
Upload UserAnonymous/Not logged-in
-
File Pages12 Page
-
File Size-