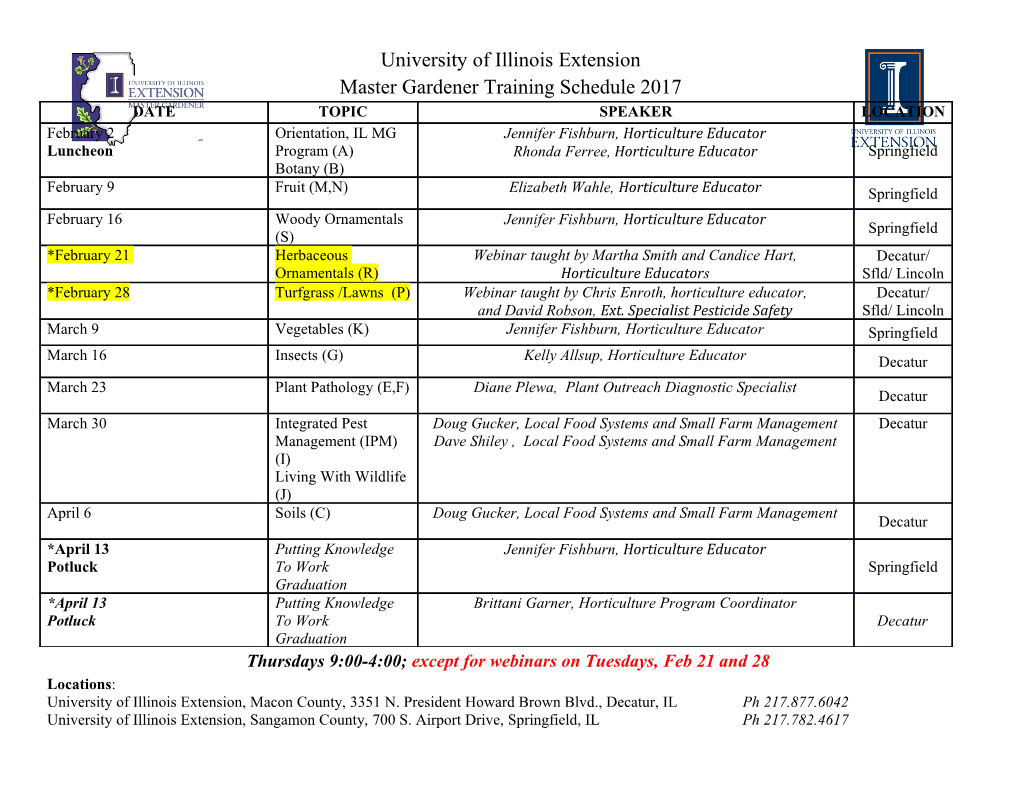
Mullite Ceramics: Its Properties, Structure, and Synthesis (Juliana Anggono) Mullite Ceramics: Its Properties, Structure, and Synthesis Juliana Anggono Lecturer, Faculty of Industrial Engineering, Mechanical Engineering Department - Petra Christian University Email: [email protected] Abstract Besides its importance for conventional ceramics, mullite has become a choice of material for advanced structural and functional ceramics due to its favourable properties. Some outstanding properties of mullite are low thermal expansion, low thermal conductivity, excellent creep resistance, high-temperature strength, and good chemical stability. The mechanism of mullite formation depends upon the method of combining the alumina- and silica-containing reactants. It is also related to the temperature at which the reaction leads to the formation of mullite (mullitisation temperature). Mullitisation temperatures have been reported to differ by up to several hundred degrees Celsius depending on the synthesis method used. The three synthesis methods used to prepare mullite are discussed in this paper together with an overview of mullite, its properties and the current application of mullite. Keywords: mullite, mullitisation, glassy phase, sol-gel, spray pyrolysis, chemical vapour deposi- tion Abstrak Keramik mullite tidak hanya penting dalam penggunaan konvensional, tetapi juga sudah menjadi bahan pilihan untuk aplikasi struktural dan fungsional karena sifat-sifatnya yang menguntungkan. Beberapa keunggulan sifat mullite adalah sifat muai dan konduktivitas panasnya rendah, ketahanan mulur yang tinggi, kekuatan yang terjaga pada temperatur tinggi, dan sifat korosinya yang baik. Mekanisme pembentukan mullite bergantung pada bagaimana proses menggabungkan reaktan yang mengandung alumina dan silika. Mekanisme tersebut juga bergantung pada temperatur reaksi awal yang akan mengarah pada pembentukan mullite (mullitisation). Beberapa penelitian melaporkan terjadinya temperatur mullitisation yang bervariasi hingga beberapa ratus derajat Celsius bergantung pada proses sintesa yang digunakan. Artikel ini menjelaskan tiga proses sintesa yang menghasilkan mullite yang dibahas bersama dengan sifat-sifat dan aplikasi mullite saat ini. Kata kunci: mullite, mullitisation, fasa glassy, sol-gel, spray pyrolysis, chemical vapour deposi- tion. 1. Introduction temperature mullite phase. (Bowen, Greig et al., 1924) It was not until the 1970s that the signi- Mullite is an alumino-silicate compound that is ficance of the inherently favourable properties of used extensively in traditional refractory applica- mullite was recognised, when the mechanical tions. Most traditional ceramic products have behaviour in compression of mullite specimens, free mullite as part of their final phase composition since or nearly free of a glassy phase, was first studied. they usually contain some clay and silicon as Mullite is becoming increasingly important in starting materials. The microstructures of the electronic, optical, and high temperature structural materials also contain a relatively low melting glass. applications, because of its low dielectric constant, Natural mullite is rare in nature; it is named good transparency for mid-infrared light and after one of the few known deposits on the Isle of excellent creep resistance. Classical uses of mullite Mull, United Kingdom. (Bowen and Greig, 1924) include refractories in the metallurgical industries The occurrence of this compound on the Isle of Mull for electric-furnace roofs, hot metal mixers and low- is thought to be a result of post-Caledonian volcanic frequency induction furnaces. In the glass Indus- activities in which clay mineral deposits, heated tries, these refractories are employed in the upper through contact with magma, produced a high structure of the tank in which the glass is melted st and for constructing the drawing chambers. Mullite Note: Discussion is expected before July, 1 2005. The proper is frequently used as kiln setting slabs and posts for discussion will be published in “Jurnal Teknik Mesin” volume 7, number 2, October 2005. firing ceramic ware as well as for the linings of high- Jurusan Teknik Mesin, Fakultas Teknologi Industri, Universitas Kristen Petra 1 http://puslit.petra.ac.id/journals/mechanical/ JURNAL TEKNIK MESIN Vol. 7, No. 1, April 2005: 1 – 10 temperature reactors. However, during the last goal of high temperature stability requires the grain decade, the spectrum of actual or potential employ- boundary to be free from glass. This is particularly ment of mullite now includes its use as a matrix difficult to achieve in mullite ceramics because of its material for high-temperature composite develop- low bulk and surface diffusivities, which are the ment, a substrate in multilayer packaging, reason for its high temperature stability. The protective coatings, turbine engine components, and processing of mullite is therefore especially impor- an infrared-transparent window especially for high- tant if a dense ceramic capable of fulfilling its high- temperature application. (Tummala, 1991; Prochaz- temperature potential is to be achieved. Table 1 ka and Klug, 1983) One approach to improve the summarises the range of characteristic properties environmental durability of silicon-based ceramics now being achieved in dense mullite ceramics. is to apply refractory oxide coatings containing no silica or those with a lower silica activity. Mullite is Table 1. Typical Properties of Mullite Ceramics. most promising because of its environmental durability, chemical compatibility, and coefficient of (Lee and Rainforth, 1994) thermal expansion (CTE) similar to that of SiC. Density (g cm-3) 3.16-3.22 Coatings of mullite applied by atmospheric plasma Hardness (GPa) spraying (APS) to SiC ceramic matrix composites At RT 13-15 provides some degree of corrosion resistance to At 1000 oC 10 corrosive industrial environments. (Van Roode, RT fracture toughness KIc (MPam1/2) 1.5-3 Price et al., 1988) Young’s Modulus (GPa) 140-250 These new interests have sparked extensive Bend strength (MPa) 150-500 studies on the synthesis and processing of mullite Thermal expansion coefficient (x106 K) 3.1-4.1 //a and mullite-based composites by molecular and/or 300-900 oC 5.6-7.0 //b colloidal methods and also on techniques for 5.6-6.1 //c producing mullite protective layers. Thermal conductivity (Wm-1K-1) Mullite rarely occurs in nature, so it is usually At 100oC 6.07 synthesised, rather than mined. Various prepara- At 600oC 4.31 tion methods and starting materials are used for the At 1000oC 3.98 synthesis of mullite ceramics. The preparation At 1400oC 3.89 methods can be classified into three different preparation routes as follows: (1) sinter-mullite, (2) The slow diffusion kinetics which make the fused-mullite (3) chemical-mullite (high-purity material so difficult to sinter also impart excellent mullite). The synthesis of mullite ceramics together with important processing routes to fabricate high temperature microstructural stability. This monolithic mullite ceramics are described in this behaviour is in marked contrast to some other paper. ceramics such as hot pressed silicon nitride (HPSN) which contains sufficient glassy phase at the grain 2. Properties of Mullite Ceramics boundaries. The grain boundary glass has a critical effect on high-temperature properties. Rapid soften- Mullite has been used for high-temperature ing of the glass and microcracking can occur as the exposed parts because of its good creep resistance test temperature is raised, degrading high-tempera- and high compressive strength at elevated tempera- ture strength loss. In contrast, mullite usually only ture. Flexural strength and creep resistance at has a minimal grain boundary glassy phase, if any, elevated temperatures are significantly affected by reducing the damaging effects of grain boundary the presence of glassy boundary inclusions; in the sliding and micro- cracking. Bend strength values absence of grain boundary glassy phase, polycrys- can vary from as low as 120 MPa to over 400 MPa. talline mullite retains > 90% of its room-tempera- ture strength to 1500oC, (Mah and Mazdiyasni, The differences can be partly explained in terms of 1983; Kanzaki, Tabata et al., 1985; Ismail, Nakai et the density achieved, the morphology of the grains al., 1986; Ismail, Nakai et al., 1987; Kumazawa, and the presence of additional crystalline and Ohta et al., 1990; Kumazawa, Kanzaki et al., 1988; amorphous phases. Ohnishi, Kawanami et al., 1990) with excellent In the polycrystalline form, the most essential thermal shock resistance, and low thermal requirement for retaining the strength of mullite at conductivity. (Becher, 1991; Somiya and Hirata, elevated temperatures appears to be the elimination 1991; Nixon, Chevacharoenkul et al., 1990) of glassy boundaries. As shown in Fig. 1, two typical Depending on the microstructural features, the low curves are observed. The first type shows a signify- fracture toughness of mullite, typically of the order cant increase in strength at about 1300oC. The of 2 MPam1/2 is regarded as a significant factor in limiting the potential applications. Moreover, the second shows no distinct maxima and decrease 2 Jurusan Teknik Mesin, Fakultas Teknologi Industri, Universitas Kristen Petra http://puslit.petra.ac.id/journals/mechanical/ Mullite Ceramics: Its Properties, Structure, and Synthesis (Juliana Anggono) slightly with increasing temperature. When poly- 3. Structure of Mullite crystalline mullite contains a small amount of
Details
-
File Typepdf
-
Upload Time-
-
Content LanguagesEnglish
-
Upload UserAnonymous/Not logged-in
-
File Pages10 Page
-
File Size-