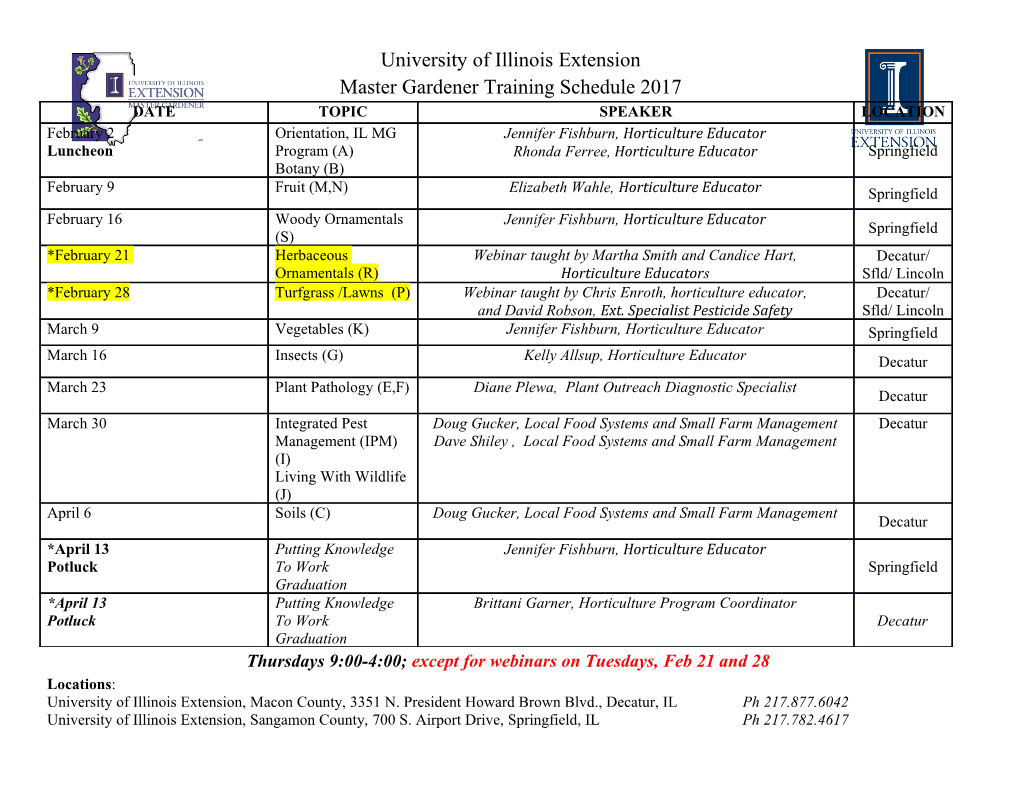
metals Article Synthesis of Magnesium Carbonate via Carbonation under High Pressure in an Autoclave Srecko Stopic 1,*, Christian Dertmann 1, Giuseppe Modolo 2, Philip Kegler 2 , Stefan Neumeier 2, Dario Kremer 3, Hermann Wotruba 3, Simon Etzold 4, Rainer Telle 4, Diego Rosani 5, Pol Knops 6 and Bernd Friedrich 1 1 IME Process Metallurgy and Metal Recycling, RWTH Aachen University, Intzestrasse 3, 52056 Aachen, Germany; [email protected] (C.D.); [email protected] (B.F.) 2 Forschungszentrum Jülich GmbH, Wilhelm Johnen Strasse, 52428 Jülich, Germany; [email protected] (G.M.); [email protected] (P.K.); [email protected] (S.N.) 3 AMR Unit of Mineral Processing, RWTH Aachen University, Lochnerstrasse 4-20, 52064 Aachen, Germany; [email protected] (D.K.); [email protected] (H.W.) 4 Department of Ceramics and Refractory Materials, GHI-Institute of Mineral Engineering, Mauerstrasse 5, 52064 Aachen, Germany; [email protected] (S.E.); [email protected] (R.T.) 5 HeidelbergCement Technology Center–Global R&D, Oberklamweg 2-4, 69181 Leimen, Germany; [email protected] 6 Green Minerals, Rijksstraatweg 128, NL 7391 MG Twello, The Netherlands; [email protected] * Correspondence: [email protected]; Tel.: +49-241-80-95-860 Received: 5 November 2018; Accepted: 23 November 2018; Published: 27 November 2018 Abstract: Magnesium carbonate powders are essential in the manufacture of basic refractories capable of withstanding extremely high temperatures and for special types of cement and powders used in the paper, rubber, and pharmaceutical industries. A novel synthesis route is based on CO2 absorption/sequestration by minerals. This combines the global challenge of climate change with materials development. Carbon dioxide has the fourth highest composition in earth’s atmosphere next to nitrogen, oxygen and argon and plays a big role in global warming due to the greenhouse effect. Because of the significant increase of CO2 emissions, mineral carbonation is a promising process in which carbon oxide reacts with materials with high metal oxide composition to form chemically stable and insoluble metal carbonate. The formed carbonate has long-term stability and does not influence the earth’s atmosphere. Therefore, it is a feasible and safe method to bind carbon dioxide in carbonate compounds such as magnesite. The subject of this work is the carbonation of an olivine (Mg2SiO4) and synthetic magnesia sample (>97 wt% MgO) under high pressure and temperature in an autoclave. Early experiments have studied the influence of some additives such as sodium bicarbonate, oxalic acid and ascorbic acid, solid/liquid ratio, and particle size on the carbonation efficiency. The obtained results for carbonation of olivine have confirmed the formation of magnesium carbonate in the presence of additives and complete carbonation of the MgO sample in the absence of additives. Keywords: MgCO3-powder; synthesis; CO2- absorption; olivine carbonation; autoclave; thermal decomposition; CO2 utilization 1. Introduction The significance of the results coming from greenhouse gas (GHG) emissions to both the atmosphere and our lives has already been urged and is nowadays well-known. Because of the continuous increase of CO2 concentration in the atmosphere since the industrial revolution, various Metals 2018, 8, 993; doi:10.3390/met8120993 www.mdpi.com/journal/metals Metals 2018, 8, 993 2 of 15 techniques are proposed. Carbon capture and utilization (CCU) is considered as the most promising technique in order to use the product in cement, transforming it into insoluble carbonate (mainly calcite and magnesite), that is able to remain stable in a geological timeframe [1]. In order to accelerate mineral carbonation, some pretreatment processes are required (microwave heating, grinding, sieving, separation, thermal decomposition, and chemical treatment). The main goal of pre-treatment processes is to increase the carbonation rate and improve the process kinetics. Typical pre-treatment methods are particle size reduction, magnetic separation and thermal treatment. Particle size reduction incorporates various grinding methods for an increase of specific surface area. In magnetic separation, undesired ferrous particles are separated from the rest of the feedstock. Thermal treatment is necessary for hydrated minerals, such as serpentine that contains H2O molecules in the mineral structure. Pre-treatment is usually required in direct carbonation processes [2]. However, one must consider the balance between increase of reaction rate and additional energy costs, possible CO2-production related to energy supply and the influence on the beneficial utilization of the final products. The major problem of pre-treatment is its high energy input, i.e., thermal treatment should be avoided due to the high energy demand and CO2-emissions (depending on the energy source). Overall, the most potentially economical pre-treatment proved to be size reduction [3]. Although there are large resources, it is not a feasible feedstock material because of its crystallographic stability and thus the necessary step of thermal pre-treatment. Industrially produced by-products containing alkaline metals are also feasible for mineral carbonation, such as numerous types of slags, scraps, red gypsum, combustion residues, fly ashes and other forms of metal oxide materials such as red mud [4]. Unlike natural feasible materials, industrial by-products usually do not require mining and pretreatment processes for utilization because they already have high alkaline metal contents which are sufficient for mineral carbonation [5]. Because of high availability in minerals and secondary materials among all of the possible materials selections, calcium oxide and magnesium oxide are the most favorable options, as shown in Equations (1) and (2) [6,7]. CaO(s) + CO2(g) = CaCO3(S) + 179kJ/mol (1) MgO(s) + CO2(g) = MgCO3(s) + 118kJ/mol (2) Although the carbonation process is an exothermic reaction, it requires an additional heat for better dissolution of carbon dioxide in water in order to form magnesium carbonate. The benefits of exothermic mineral carbonation may result in a positive net energy balance, which improves the net efficiency of a combined cycle power plant [8]. Calculating energy balances of the process is essential for the determination of the process’ profitability which might be influenced by high energy costs. Furthermore, the overall reduction of carbon dioxide emissions has to be considered due to further emissions in the mineral carbonation process resulting from, e.g., transportation, grinding and processing of by-products. Furthermore, the potential use of the formed products should also be taken into consideration. There are abundant calcium and magnesium rich minerals available in the earth’s crust. Although MgO and CaO are the most abundant alkali and alkaline metal oxides, they cannot be found as binary oxides in nature. Usually, they exist as hydroxides or silicate minerals. In a mineral carbonation process, these can also be used as feedstock to form carbonates that are chemically stable in a geological timeframe. Silicate minerals usually are richer in alkaline metal content such as magnesium, sodium, and calcium. Common silicate minerals suitable for carbonation are forsterite (Mg2SiO4), antigorite (Mg3Si2O5(OH)4) and wollastonite (CaSiO3) and their overall reaction conversions are given in Equations (3) to (5). Mg2SiO4(s) + 2CO2(g) + H2O(l) = 2MgCO3(s) + H4SiO4(aq) + 89kJ/mol (3) Mg3Si2O5(OH)4(s) + 3CO2(g) + 2H2O(l) = 3MgCO3(s) + 2H4SiO4(aq) + 64kJ/mol (4) Metals 2018, 8, 993 3 of 15 CaSiO3(s) + CO2(g) + 2H2O(l) = CaCO3(s) + H4SiO4(aq) + 90kJ/mol (5) The aforementioned mineral carbonation using slags as reactant also have the chance to be profitable if they are built closely to the steel production site in order to reduce production Metals 2018, 8, x FOR PEER REVIEW 3 of 14 costs [9]. Furthermore, heat integration with the steel production plant can reduce overall energy significantlycosts significantly [9]. Carbonation [9]. Carbonation of different of different type typess of slags of slags are are widely widely studied, studied, one one study study by Georgakopoulos [[4]4] suggestssuggests that that blended blended hydraulic hydraulic cement cement BHC BHC slag slag has has the the highest highest conversion conversion rate ratewhich which is 68.3%. is 68.3%. · Red gypsum usually exists in the form of calcium calcium sulfate dihydrate (CaSO 4·2H2H22O).O). Typically, Typically, red gypsum has a purity of 95% and has large large resources in Malaysia [10]. [10]. Due to the the large large calcium calcium content content its carbonation isis alsoalso aa promisingpromising CCS CCS option, option, i.e., i.e., one one ton ton of of red red gypsum gypsum can can stably stably bind bind 0.26 0.26 tons tons of ofgaseous gaseous CO CO2.2 A. A big big advantage advantage of of red red gypsum gypsum as as carbonation carbonation resourceresource isis nono miningmining cost is required since it exists in the form of finefine powder which favors the carbonation reaction.reaction. Figure 1. ReactionReaction path of direct forsteri forsteritete carbonation in aqueous solution. Generally, the reaction path for the indirect carbonationcarbonation of forsterite in an aqueous solution can be described by Equations (6) to (12) which which is also also illustrated illustrated in in Figu Figurere 11[ [11,12].11,12]. For For simplicity, simplicity,
Details
-
File Typepdf
-
Upload Time-
-
Content LanguagesEnglish
-
Upload UserAnonymous/Not logged-in
-
File Pages15 Page
-
File Size-