Low-Cost Flood Sensors: Innovation for Dam Safety Monitoring
Total Page:16
File Type:pdf, Size:1020Kb
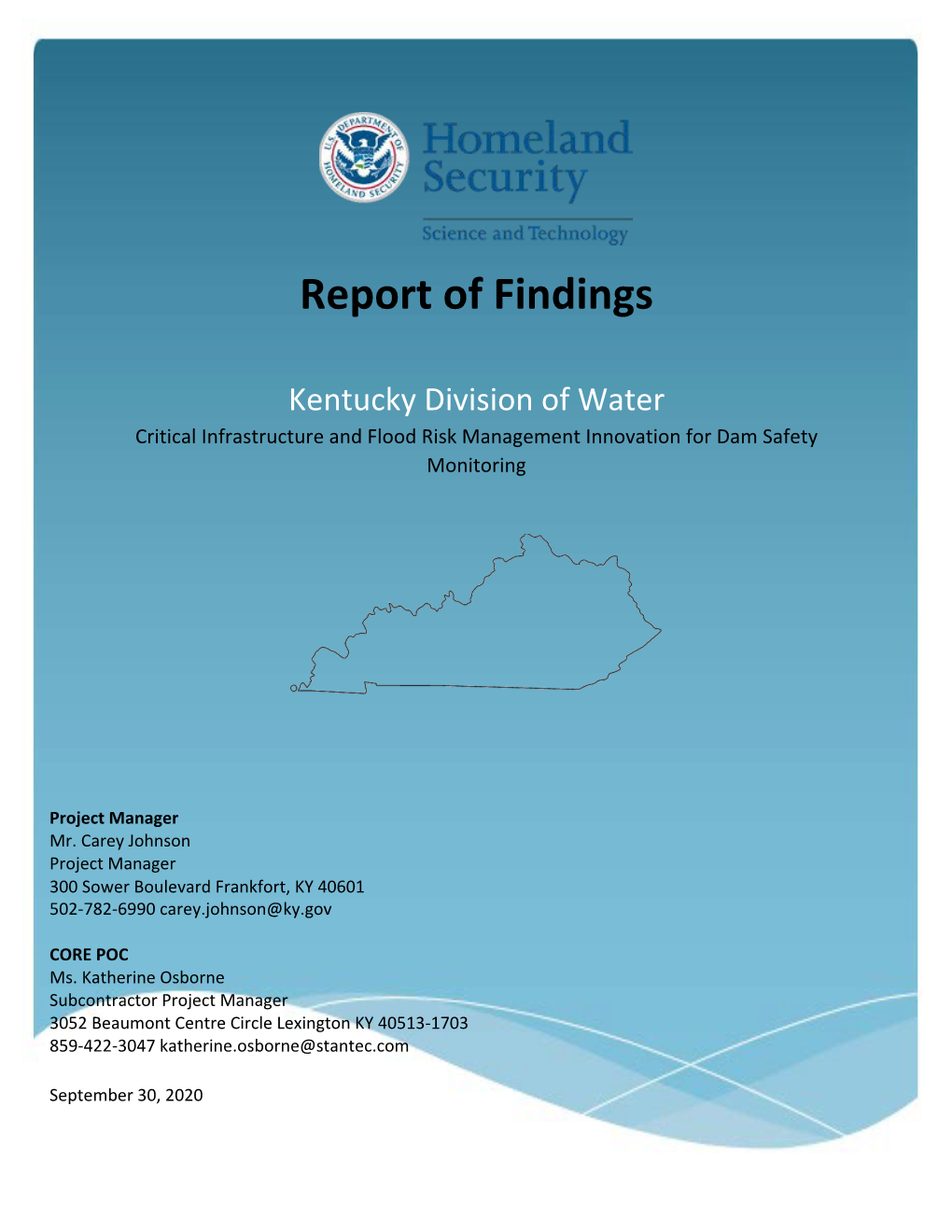
Load more
Recommended publications
-
Fishing Regula Tions Fishing Regulations
FISHING REGULATIONS FISHING REGULATIONS Dave Dreves photo NEW THIS YEAR The items highlighted here are a • Camp Ernst Lake in Boone County, quick overview of the changes to this Madisonville City Park Lake North NEED A PLACE TO FISH? year’s regulations. Changes from last in Hopkins County, Millennium Park season are printed in bright blue in Pond in Boyle County, Whitehall Find new fishing information on complete detail throughout this guide to Park Lake in Madison County, Way- Kentucky waterbodies by visiting assist you in noticing those changes. mond Morris Park Lake in Daviess fw.ky.gov. Click on the “Fishing” County, and Carlson and Dickerson tab, then on “Where to Fish” and FISHING lakes in Fort Knox in Meade County lastly “Find A Place to Fish.” An- • A 7-fish aggregate daily creel limit are now enrolled in the Fishing in glers may search lakes, rivers and on rainbow and brown trout on Dale Neighborhoods Program (FINs). creeks for boat ramps and access Hollow Lake. points, what species are available • Yellow bass on the Ohio River are BOATING and maps of how to get there plus now under the statewide daily creel • Below locks and dams on U.S. Army other useful information. lmit of 30 fish with no minimum size Corps of Engineers waterways and Also under the “Where to Fish” limit. the Kentucky River, boat occupants tab is the 2011 Fishing Forecast. • The special fishing regulations on must wear a personal floatation This report details the anticipated ponds on Taylorsville Lake WMA are device (lifejacket) upstream of danger fishing success for each species removed. -
Articles on Reservoirs in Kentucky, Including: List of Dams and Reservoirs Of
APM7V91KSUTO » Doc » Articles On Reservoirs In Kentucky, including: List Of Dams And Reservoirs Of... Read eBook ARTICLES ON RESERVOIRS IN KENTUCKY, INCLUDING: LIST OF DAMS AND RESERVOIRS OF THE TENNESSEE RIVER, LAKE CUMBERLAND, LAKE BARKLEY, NOLIN RIVER LAKE, DALE HOLLOW RESERVOIR, BARREN RIVER LAKE, BOLTZ LAKE To read Articles On Reservoirs In Kentucky, including: List Of Dams And Reservoirs Of The Tennessee River, Lake Cumberland, Lake Barkley, Nolin River Lake, Dale Hollow Reservoir, Barren River Lake, Boltz Lake eBook, you should access the link under and download the document or have accessibility to other information which might be in conjuction with ARTICLES ON RESERVOIRS IN KENTUCKY, INCLUDING: LIST OF DAMS AND RESERVOIRS OF THE TENNESSEE RIVER, LAKE CUMBERLAND, LAKE BARKLEY, NOLIN RIVER LAKE, DALE HOLLOW RESERVOIR, BARREN RIVER LAKE, BOLTZ LAKE ebook. Read PDF Articles On Reservoirs In Kentucky, including: List Of Dams And Reservoirs Of The Tennessee River, Lake Cumberland, Lake Barkley, Nolin River Lake, Dale Hollow Reservoir, Barren River Lake, Boltz Lake Authored by Books, Hephaestus Released at 2016 Filesize: 9.56 MB Reviews The publication is easy in read better to understand. It is writter in basic words and phrases rather than hard to understand. You wont truly feel monotony at anytime of your respective time (that's what catalogues are for about if you question me). -- Kaya Rippin Absolutely among the nest publication I actually have actually go through. It really is rally fascinating throgh reading time. I am easily could possibly get a pleasure of looking at a composed ebook. -- Prof. Rick Romaguera Extensive manual for publication fans. -
Water-Resource Development: a Strategic Plan
Appendix B -Northern Kentucky Area Development District • DRAFT Water-Resource Development: A Strategic Plan Summary of Water Systems Northern Kentucky Area Development District Water Resources Development Commission October, 1999 3:40 PM 1 10/13/99 Appendix B -Northern Kentucky Area Development District • DRAFT CONTENTS CONTENTS ......................................................................................................................................................... 2 MAP LISTING...................................................................................................................................................... 4 NORTHERN KENTUCKY AREA DEVELOPMENT DISTRICT..................................................................... 5 REGIONAL OVERVIEW .................................................................................................................................... 5 BOONE COUNTY ............................................................................................................................................... 9 PUBLIC WATER SYSTEMS ........................................................................................................................ 9 FLORENCE WATER AND SEWER COMMISSION........................................................................ 10 BOONE COUNTY WATER AND SEWER DISTRICT.................................................................... 10 WALTON WATERWORKS DEPARTMENT................................................................................... 11 OTHER -
Kentucky Boating and Fishing Access Sites Guide
22 O LAKE INSET Lake or Pond MAP National River, Stream See Wildlife or Creek See Reserve State Capitol BOAT RAMP LAKELAKE LOWER R 237 H LAKE Creek E or InsetInset or Rive V 8 r County Seat KY Dept. of Fish I O Wildlife R I FRANKFORT ACCESS SITE 33 POND Management NWR Area Inez State Road Alexandria 89 U.S. Highway 275 WMA TROUT 3D U.S. KENTUCKY Military 20 STREAM 420 20 71 Base U.S. Interstate 338 75 L Licking Big IC K I 1 N G Lower River Sandy 64 ek 471 Parkway re C 2 Burlington KY p.38+39 Woolper 236 Salt & RIVER Dinsmore 275 River PKWY 20 Woods 18 River Little SNP 18 Boone r State de State p.22+23 w Forest County o Nature National Sandy p p.18+19 n u Preserve Park Cliffs G VER 177 RI SNP Rivers Lock & Dam Belleview 3 237 State SF 17 Park SNP NP & Lower BASIN Woods SP Upper p.42+43 Site k e State USFS Wildlife Resources e r Green 338 C Resort SRP KY Proclamation BOONE Park Area See Basin Index on p.24 SNA River River O 536 71 State SHS Upper County or I 536 Natural p.8+9 p.26+27 State Line H 75 Area r O e Green d State Upper w Tennessee, o 536 p Historic 0 5 10 20 n u 42 Site River G 127 Lower Cumberland, Cumberland Big Bone KENTON p.12+13 Lick SP Tradewater & Mississippi p.30+31 A 338 338 16 Rivers p.2+3 Approximate Scale in Miles 4 050100 Approx. -
FISHING REGULATIONS This Guide Is Intended Solely for Informational Use
KENTUCKY FISHING & BOATING GUIDE MARCH 2021 - FEBRUARY 2022 Take Someone Fishing! FISH & WILDLIFE: 1-800-858-1549 • fw.ky.gov Report Game Violations and Fish Kills: Rick Hill illustration 1-800-25-ALERT Para Español KENTUCKY DEPARTMENT OF FISH & WILDLIFE RESOURCES #1 Sportsman’s Lane, Frankfort, KY 40601 Get a GEICO quote for your boat and, in just 15 minutes, you’ll know how much you could be saving. If you like what you hear, you can buy your policy right on the spot. Then let us do the rest while you enjoy your free time with peace of mind. geico.com/boat | 1-800-865-4846 Some discounts, coverages, payment plans, and features are not available in all states, in all GEICO companies, or in all situations. Boat and PWC coverages are underwritten by GEICO Marine Insurance Company. In the state of CA, program provided through Boat Association Insurance Services, license #0H87086. GEICO is a registered service mark of Government Employees Insurance Company, Washington, DC 20076; a Berkshire Hathaway Inc. subsidiary. © 2020 GEICO ® Big Names....Low Prices! 20% OFF * Regular Price Of Any One Item In Stock With Coupon *Exclusions may be mandated by the manufacturers. Excludes: Firearms, ammunition, licenses, Nike, Perception, select TaylorMade, select Callaway, Carhartt, Costa, Merrell footwear, Oakley, Ray-Ban, New Balance, Terrain Blinds, Under Armour, Yeti, Columbia, Garmin, Tennis balls, Titleist golf balls, GoPro, Nerf, Lego, Leupold, Fitbit, arcade cabinets, bats and ball gloves over $149.98, shanties, large bag deer corn, GPS/fish finders, motors, marine batteries, motorized vehicles and gift cards. Not valid for online purchases. -
Lake Cumberland
Lake or Pond LAKE INSET National River, Stream MAP Wildlife or Creek Reserve State Capitol BOAT RAMP See LAKE Creek LAKE or Rive or LAKE r County Seat Wildlife POND FRANKFORT ACCESS SITE 33 InsetInset Management NWR Area Inez State Road WMA 89 U.S. Highway U.S. Military 420 TROUT 3D Base Licking Big U.S. Interstate STREAM Lower River Sandy 64 Parkway KY p.38+39 & Salt PKWY River River Little State State p.22+23 Nature Forest National p.18+19 Sandy Preserve Park State SF Rivers Lock & Dam Park SNP NP SP Lower Upper p.42+43 State USFS Resort SRP Green KY Proclamation Park Area SNA River River State SHS Upper County or Natural p.8+9 p.26+27 State Line Area Green State Tennessee, Upper Historic Site Lower Cumberland, River Cumberland p.12+13 Tradewater & Mississippi p.30+31 Fort Boonesborough Rivers p.2+3 SP 0 50 100 Approx. Scale in Miles: LOCK & DAM #10 S t o n 75 e 627 y LOCK & DAM #9 Run White Hall TUCKY EN SHS K 169 388 RIVER 1156 r MADI e v i R 27 LOCK & 25 DAM #8 LAKE REBA Richmond k 876 e x HERRINGTON LAKE e Di r C r a g u S TAYLOR \FORK GARRARD 595 LAKE P ai nt L re ic ilver C ek 1295 k S C re e k 421 39 75 Lancaster 595 Big South Fork of the Cumberland River 1016 590 25 Upper areas of this river are within the Big South Fork National River and Recreation Area which is in both Kentucky and Tennessee. -
MINERAL and FUEL RESOURCES MAP of KENTUCKY Sg Alexandria 75 BOONE S Warren H
KENTUCKY GEOLOGICAL SURVEY MAP AND CHART SERIES 21 Donald C. Haney, State Geologist and Director Series XI, 1998 UNIVERSITY OF KENTUCKY, Lexington 89° 88° 87° 86° 85° 84° 83° 82° sg Newport 275 sg COVINGTON s 471 39° 39° sg sg Burlington s Licking MINERAL AND FUEL RESOURCES MAP OF KENTUCKY sg Alexandria 75 BOONE s Warren H. Anderson and Garland R. Dever Jr. s KENTON c 71 CAMPBELL With contributions by Brandon C. Nuttall, Gerald A. Weisenfluh, Terry D. Hounshell, Kx, Pb O H I O William M. Andrews Jr., and John K. Hiett ls River sg Bullock Pen * Lake 1998 ls ls sg Warsaw 71 75 GALLATIN * Kincaid Lake sg sg sg Eagle Creek sg PENDLETON s OHIO Williamstown Scale: 1:500,000 Boltz Lake Brooksville s RIVER CARROLL Lake Falmouth 1 inch equals approximately 8 miles Carrollton sg Zn GRANT BRACKEN Maysville K Zn ss e * * Williamstown n * d 30 t s 10 0 10 20 40 Miles N u * ss c ls Vanceburg ss k Area of narrow outcrops y Greenup of construction limestone Fork ts Zn ss ss along the Licking River MASON Bedford North Fn Kx, Ba, Zn and its forks ss GREENUP 10 0 10 20 30 40 50 Kilometers sg * TRIMBLE Kx, Zn, Pb OWEN Mt. Olivet Owenton South ss Greenbo r * Lake ive LEWIS R ROBERTSON Kx, Zn Fn Fn Ashland * ls Kx, Zn Fn © 1998 by Kentucky Geological Survey, sg Kx, Zn, Ba, Pb Fe s Fn University of Kentucky HENRY ls Fork Catlettsburg Kx, Ba, Zn ls River HARRISON Flemingsburg Fn New Castle Kx, Ba, F oc7 sg La Grange 64 d Cynthiana FLEMING H(u) BOYD Big OLDHAM ls F, Ba, Fe 71 y Grayson NICHOLAS d ss n Ballardsville a * 23 Sandy dol ls S (abandoned) ls CARTER B uc3 ss dol SCOTT ls Carlisle Licking 75 Phosphate sis ss Fe B area Tar sand sis R sg i v 264 Fe e W E S T dol FRANKLIN Grayson r Lake Fe SHELBY BOURBON Ri LOUISVILLE 64 Guist Creek Kx, F ve 64 65 Georgetown r ROWAN Fe d Shelbyville Lake Frankfort ls d ls Paris A sg BATH Morehead VIRGINIA RIVER 64 JEFFERSON Owingsville ss le ELLIOTT ls Kx, Zn, tt Louisa Li N 265 Kx, Cu, F, Ba Fe ss F Fn ss A s Phosphate Zn, Ba Fe LAWRENCE mines Po Cave Run Sandy Hook ls c dol ls Lake sis I Po B D Fork d LEXINGTON Fe N NA WOODFORD Mt. -
Regulatory Requirements All Silivicultural Operations, 401 KAR 5
Appendix A Regulatory Requirements All Silvicultural Operations, 401 KAR 5:026, 5:029, 5:030, and 5:031 All operations must meet Kentucky water quality standards. Activities Near High-quality Waters and Outstand- ing National Resources Waters, 401 KAR 5:029, 5:030, and 5:031. Kentucky water quality standards (401 KAR 5:029) require the use of BMPs to protect high-quality waters and outstanding national resources waters listed in 401 KAR 5:030. In addition, outstanding resource wa- ters that support federally listed threatened and endan- gered species require protection (see 401 KAR 5:031). Activities Near Wild Rivers, KRS 146.200 et seq. and 401 KAR 4:100-140. The Kentucky Wild Rivers Act and associated regulations give special protection to streams designated as “wild rivers,” including regulation of sil- vicultural activity. Before undertaking any silvicultural activity in a corridor of a designated wild river, the land- owner or logger should contact the Wild Rivers Program of the Kentucky Division of Water for applicable regula- tions and instructions. Debris in Floodplains, KRS 151.250. The Kentucky Division of Water has authority over the placement of debris (including logging slash) in floodplains of peren- nial streams that have a drainage area larger than one- square mile. The Division of Water advises that as long as the BMPs for Streamside Management Zones and log- ging debris are followed, landowners and loggers will be considered in compliance with floodplain regulations that address debris. If these BMPs are not followed, the Ken- tucky Division of Water can institute enforcement pro- ceedings. -
Kentucky Drought Mitigation and Response Plan
Kentucky Drought Mitigation and Response Plan Prepared by the Energy and Environment Cabinet in partnership with the Kentucky Drought Mitigation and Response Advisory Council In fulfillment of the directive of Senate Joint Resolution 109 December 31, 2008 Table of Contents 1. Purpose................................................................................................................................3 2. Defining Drought, Drought Response and Drought Mitigation ......................................4 3. The Kentucky Drought Mitigation Team ...........................................................................5 3.1 KDMT Membership .......................................................................................................5 3.3 KDMT Drought Assessment Teams..............................................................................8 4. Drought Monitoring...........................................................................................................13 4.1 Drought Management Regions ...................................................................................13 4.2 Drought Indicators.......................................................................................................14 5. State Drought Response ..................................................................................................19 5.1 General Drought Action Levels ...................................................................................19 5.2 Targeted Drought Declarations ...................................................................................25 -
Kentucky Trail Town Guide Kentucky Trail Town Guide 5 TRAIL TOWNS PUBLIC LANDS
VOLUME 1 KentuckyTRAIL TOWNS Where the Outdoors and Amenities Meet GETTING AWAY FROM IT ALL TABLE OF CONTENTS DOESN’T HAVE TO MEAN BEING 5 Kentucky Trail Towns 26 Jamestown Overview IN THE MIDDLE OF NOWHERE. 28 Manchester 6 Kentucky Trails State Map 30 Harlan Tri-Cities Kentucky’s designated Trail Towns put you near the best outdoor action in the 8 Explore More of the state – including hundreds of miles of trails, woods and waters – but keep you in Outdoors in Kentucky 32 Berea cities and towns offering hotels, restaurants, attractions, entertainment and other 34 Columbia conveniences to round out your stay. TRAIL TOWNS 36 Royalton To be a certified Kentucky Trail Town, these popular destinations have made a 12 Dawson Springs Slade commitment to share their area’s outdoor opportunities, culture, history and stories 38 to visitors hungry for adventure. Since its inception, this program under the state’s 14 Livingston 40 McKee Tourism, Arts & Heritage Cabinet has designated 20 communities across Kentucky 16 Morehead 42 Munfordville to serve as official gateways to the state’s great outdoors. 18 Olive Hill 44 Cave City/Horse Cave Here’s just a taste of what awaits! 20 London 46 Campbellsville 22 Stearns 48 Estill Twin Cities 24 Elkhorn City 50 Hazard Explore Kentucky’s Trail Towns! kentuckytourism.com/ky-outdoors/trail-towns Dawson Springs KENTUCKY TRAIL TOWNS OVERVIEW Located in Western Kentucky, Dawson Known as Harlan Tri-Cities, the towns of Springs was the state’s first official Trail Cumberland, Benham and Lynch combine Town and is home to scenic trails, a beautiful to deliver attractions like Pine Mountain lake and lots of adventure at Pennyrile Scenic Trail and Kingdom Come State Park, Forest State Resort Park. -
1 Region 1 – Western US
^ = Partial Bathymetric Coverage ! = New to/updated in 2011 blue = Vision Coverage * = Detailed Shoreline Only Region 1 – Western US Lake Name State County French Meadows Reservoir CA Placer Alamo Lake AZ La Paz Goose Lake CA Modoc * Bartlett Reservoir AZ Maricopa Harry L Englebright Lake CA Yuba Blue Ridge Reservoir AZ Coconino Hell Hole Reservoir CA Placer Horseshoe Reservoir AZ Yavapai Hensley Lake CA Madera Lake Havasu AZ/CA Various * Huntington Lake CA Fresno Lake Mohave AZ/NV Various Ice House Reservoir CA El Dorado Lake Pleasant AZ Yavapai/Maricopa Indian Valley Reservoir CA Lake Lower Lake Mary AZ Coconino * Jackson Meadow Reservoir CA Sierra San Carlos Reservoir AZ Various * Jenkinson Lake CA El Dorado Sunrise Lake AZ Apache Lake Almanor CA Plumas * Theodore Roosevelt Lake AZ Gila Lake Berryessa CA Napa Upper Lake Mary AZ Coconino Lake Britton CA Shasta Antelop Valley Reservoir CA Plumas ^ Lake Cachuma CA Santa Barbara Barrett Lake CA San Deigo Lake Casitas CA Ventura Beardsley Lake CA Tuolumne Lake Del Valle CA Alameda Black Butte Lake CA Glenn Lake Isabella CA Kern Briones Reservoir CA Contra Costa Lake Jennings CA San Deigo Bullards Bar Reservoir CA Yuba Lake Kaweah CA Tulare Camanche Reservoir CA Various Lake McClure CA Mariposa Caples Lake CA Alpine Lake Natoma CA Sacramento Castaic Lake CA Los Angeles Lake of the Pines CA Nevada Castle Lake CA Siskiyou Lake Oroville CA Butte ^ Clear Lake CA Lake Lake Piru CA Ventura ^ Clear Lake Reservoir CA Modoc * Lake Shasta CA Shasta Cogswell Reservoir CA Los Angeles Lake Sonoma CA -
IMPORTANT INFORMATION: Lakes with an Asterisk * Do Not Have Depth Information and Appear with Improvised Contour Lines County Information Is for Reference Only
IMPORTANT INFORMATION: Lakes with an asterisk * do not have depth information and appear with improvised contour lines County information is for reference only. Your lake will not be split up by county. The whole lake will be shown unless specified next to name eg (Northern Section) (Near Follette) etc. LAKE NAME COUNTY COUNTY COUNTY COUNTY COUNTY Great Lakes GL Lake Erie Great Lakes GL Lake Erie (Port of Toledo) Great Lakes GL Lake Erie (Western Basin) Great Lakes GL Lake Huron Great Lakes GL Lake Huron (w West Lake Erie) Great Lakes GL Lake Michigan Great Lakes GL Lake Michigan (Northeast) Great Lakes GL Lake Michigan (South) Great Lakes GL Lake Michigan (w Lake Erie and Lake Huron) Great Lakes GL Lake Ontario Great Lakes GL Lake Ontario (Rochester Area) Great Lakes GL Lake Ontario (Stoney Pt to Wolf Island) Great Lakes GL Lake Superior Great Lakes GL Lake Superior (w Lake Michigan and Lake Huron) Great Lakes GL Lake St Clair Great Lakes GL (MI) Great Lakes Cedar Creek Reservoir AL Deerwood Lake Franklin AL Dog River Shelby AL Gantt Lake Mobile AL Goat Rock Lake * Covington AL (GA) Guntersville Lake Lee Harris (GA) AL Highland Lake * Marshall Jackson AL Inland Lake * Blount AL Jordan Lake Blount AL Lake Gantt * Elmore AL Lake Jackson * Covington AL (FL) Lake Martin Covington Walton (FL) AL Lake Mitchell Coosa Elmore Tallapoosa AL Lake Tuscaloosa Chilton Coosa AL Lake Wedowee (RL Harris Reservoir) Tuscaloosa AL Lay Lake Clay Randolph AL Lewis Smith Lake * Shelby Talladega Chilton Coosa AL Logan Martin Lake Cullman Walker Winston AL Mobile Bay Saint Clair Talladega AL Ono Island Baldwin Mobile AL Open Pond * Baldwin AL Orange Beach East Covington AL Bon Secour River and Oyster Bay Baldwin AL Perdido Bay Baldwin AL (FL) Pickwick Lake Baldwin Escambia (FL) AL (TN) (MS) Pickwick Lake (Northern Section, Pickwick Dam to Waterloo) Colbert Lauderdale Tishomingo (MS) Hardin (TN) AL (TN) (MS) Shelby Lakes Colbert Lauderdale Tishomingo (MS) Hardin (TN) AL Tallapoosa River at Fort Toulouse * Baldwin AL Walter F.