Faster Than the Wind: the Optimization Experience in the America's CUP Challenge
Total Page:16
File Type:pdf, Size:1020Kb
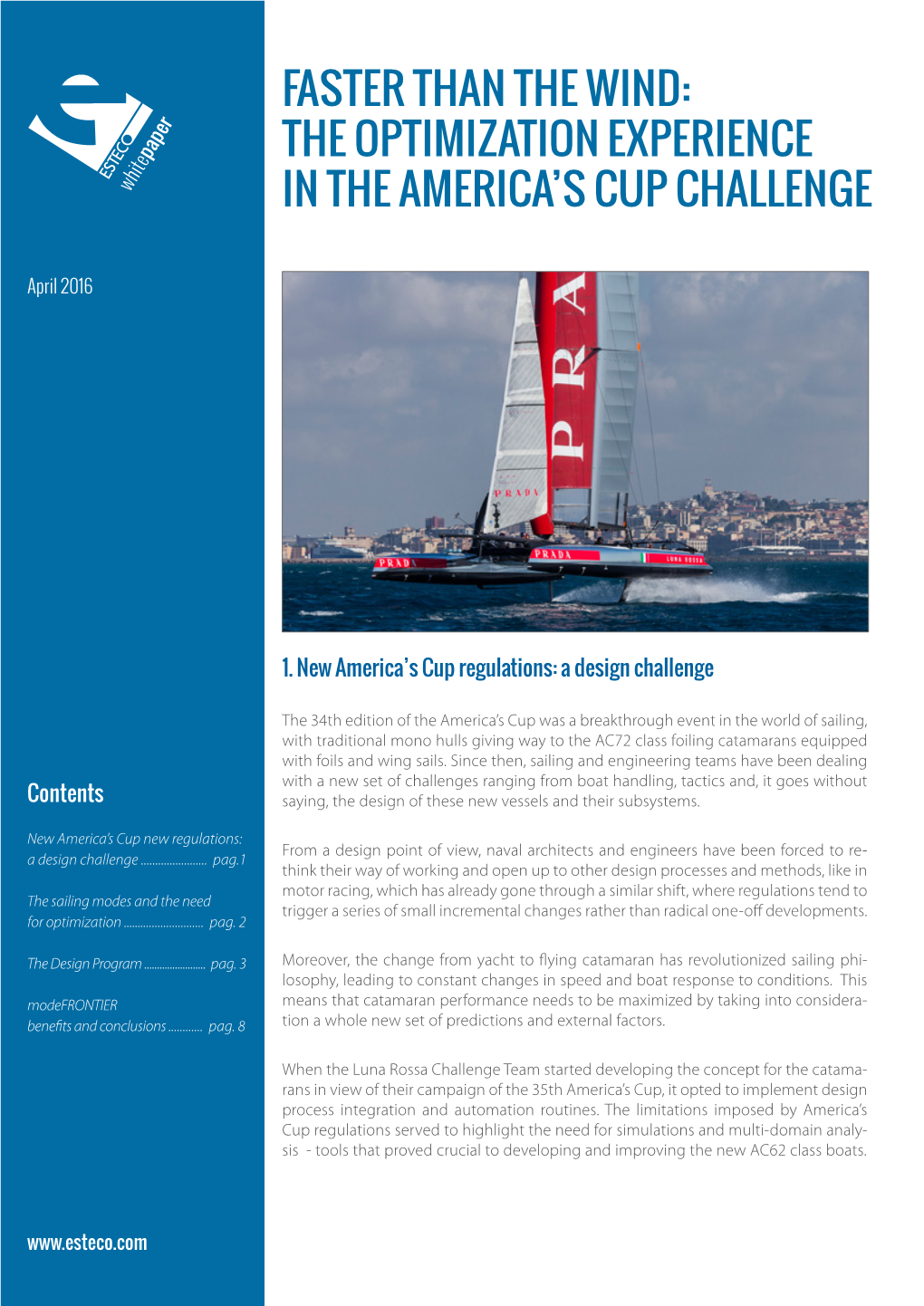
Load more
Recommended publications
-
A Preview of the 35Th America's Cup Races
The BUZZ - Oracle Team USA is a two-time winner of the America’s Cup (2010 and 2013). It is aiming for a three- peat with the upcoming races in Bermuda. Photo,left page: Sam Greenfield /Oracle Team USA, courtesy of Ber Team /Oracle page: Sam Greenfield Photo,left muda Tourism Authority. Vuitton courtesy of Louis Pinto, 2015 / Ricardo Photo, inset right: © ACEA 76 NY_Buzz Event_America’s CupSCCS46.indd 76 4/17/17 10:11 AM IN FULL What you aneed to know to take in the 35th Louis Vuitton America’s Cup races THE NEW YORK i CONNECTION starting in Above: Last year, New York hosted May off the the Louis Vuitton S l America’s Cup coast of World Series, a pre- liminary face off - Bermuda. where competitors earned points for BY ROBERTA NAAS the final races. HOW THE RACES STARTED: In a race GET READY: Beginning in late May, yacht THE SCHEDULE: The action in Bermuda around England’s Isle of Wight in August lovers are in for a spectacular treat: the kick- this summer represents the climax of a com- 1851, an upstart schooner named America off of the 35th America’s Cup presented by petition that started two years ago in Ports- sailed past the Royal Yacht to win the 100 Louis Vuitton in Bermuda. Defending the mouth, England. The first of the final series Pound Cup. More than a simple boating com- America’s Cup, the competition for the oldest of races, Louis Vuitton America’s Cup Quali- petition, this triumph of the New York Yacht trophy in international sports (dating back to fiers, begins in Bermuda on May 26 and runs Club (NYYC) over the Royal Yacht Squadron 1851), will be Oracle Team USA, representing through June 3. -
Team Portraits Emirates Team New Zealand - Defender
TEAM PORTRAITS EMIRATES TEAM NEW ZEALAND - DEFENDER PETER BURLING - SKIPPER AND BLAIR TUKE - FLIGHT CONTROL NATIONALITY New Zealand HELMSMAN HOME TOWN Kerikeri NATIONALITY New Zealand AGE 31 HOME TOWN Tauranga HEIGHT 181cm AGE 29 WEIGHT 78kg HEIGHT 187cm WEIGHT 82kg CAREER HIGHLIGHTS − 2012 Olympics, London- Silver medal 49er CAREER HIGHLIGHTS − 2016 Olympics, Rio- Gold medal 49er − 2012 Olympics, London- Silver medal 49er − 6x 49er World Champions − 2016 Olympics, Rio- Gold medal 49er − America’s Cup winner 2017 with ETNZ − 6x 49er World Champions − 2nd- 2017/18 Volvo Ocean Race − America’s Cup winner 2017 with ETNZ − 2nd- 2014 A class World Champs − 3rd- 2018 A class World Champs PATHWAY TO AMERICA’S CUP Red Bull Youth America’s Cup winner with NZL Sailing Team and 49er Sailing pre 2013. PATHWAY TO AMERICA’S CUP Red Bull Youth America’s Cup winner with NZL AMERICA’S CUP CAREER Sailing Team and 49er Sailing pre 2013. Joined team in 2013. AMERICA’S CUP CAREER DEFINING MOMENT IN CAREER Joined ETNZ at the end of 2013 after the America’s Cup in San Francisco. Flight controller and Cyclor Olympic success. at the 35th America’s Cup in Bermuda. PEOPLE WHO HAVE INFLUENCED YOU DEFINING MOMENT IN CAREER Too hard to name one, and Kiwi excelling on the Silver medal at the 2012 Summer Olympics in world stage. London. PERSONAL INTERESTS PEOPLE WHO HAVE INFLUENCED YOU Diving, surfing , mountain biking, conservation, etc. Family, friends and anyone who pushes them- selves/the boundaries in their given field. INSTAGRAM PROFILE NAME @peteburling Especially Kiwis who represent NZ and excel on the world stage. -
Latitude 38 October 2013
Latitude 38 Latitude VOLUME 436 O 3 WE GO WHERE THE WIND BLOWS OCTOBER 2013 VOLUME 436 AMERICA'S CUP 34 — There is a new gold standard at the highest level of yacht racing. It's AC72s on San Francisco Bay. Like the America's Cup itself, there is no second place. The transformation brought about by the creation of the AC72s has been no less than that of biplanes to passenger jets, Model Ts to F1 cars, or snail mail to high-speed Internet. Since this sailing show of a lifetime happened on our home waters, we hope you didn't miss it. Having already made an improb- didn't come as a complete shock. After clear, the result was not. "The obvious ably spectacular comeback from an falling behind by seven races, OTUSA difference was Oracle's ability to foil 8-to-1 deficit in the improbably exciting was on a roll, having roared back to an upwind," said Kiwi helmsman Dean 34th America's Cup on San Francisco 8-to-8 tie. Barker. "Oracle's boat systems or [sail- Bay, Oracle Team USA came from behind But there was more to it than that. ing] technique were better suited for in the 19th and final Kiwi head Grant foiling upwind for sustained periods." race to defeat Emir- Dalton said he'd Dalton said that by the end of the ates Team New Zea- "slept the best I have Cup, Oracle had made a 90-second im- land and retain the in a week" because provement between the two boats on the oldest trophy — 162 he was confident weather legs. -
Latitude 38 August 2012
Latitude 38 Latitude VOLUME 422 Augu 012 WE GO WHERE THE WIND BLOWS AUGUST 2012 VOLUME 422 AMERICA'S CUP WORLD SERIES — At last. On August 22, two dozen years since the legendary Tom Blackaller touted the potential excitement of sailing a year ago in Cascais, Portugal, and fender (Oracle Team USA) to race against big fast cats in the America's Cup, a gun hit Plymouth, UK, San Diego, and both all the other challengers. will sound starting the fi rst offi cial match Naples and Venice, Italy, before conclud- This means eleven crews represent- race in catamarans between America's ing July 1 in Newport, R.I. ing eight teams and eight countries were Cup teams on San Francisco Bay. The 2012-2013 series starts fresh this gearing up at bases in San Francisco and "What? I thought the Cup was next month with a three-city, four-regatta, Alameda as Latitude went to press. year?" It is. But if you missed the memo circuit kicking off in San Francisco. Starting with practice racing on Tues- — and we know many sailors who are We get two regattas here — August day, August 21, through a fi nal race and just starting to catch up — the America's and October — followed by a return to celebrity pro-am contest on Sunday, Cup World Series arrives on our doorstep Venice and Naples this month. in April and May 2013. We hear one Multi-City Circuit or two more cities The San Francisco event begins the may be added. second year of a two-year Cup ramp-up U n l i k e t h e that features the AC World Series as an challenger elimi- annual multi-city race circuit. -
Annual Report 2018
Annual Report 2018 PRADA spa (Hong Kong Stock code: 1913) ANNUAL REPORT 2018 TABLE OF CONTENTS The PRADA Group 3 Financial Review 55 Directors and Senior Management 77 Directors’ Report 93 Corporate Governance 115 Consolidated Financial Statements 137 PRADA spa Separate Financial Statements 143 Notes to the Consolidated Financial Statements 149 Independent Auditors’ Reports 231 The first Prada store Galleria Vittorio Emanuele II, Milan THE PRADA GROUP PRADA Group Annual Report 2018 - The PRADA Group 3 Miuccia Prada and Patrizio Bertelli PRESENTATION Pioneer of a vision that transcends fashion, the Prada Group inquisitively observes contemporary society and its interactions with very diverse and apparently distant cultural spheres. A fluid perspective that becomes the Group’s manifesto, suggesting a unique approach to doing business by placing at the core of ethical and action principles essential values such as freedom of creative expression, reinterpretation of what already exists, preservation of know-how and enhancement of people’s work. The Prada Group is a contemporary interpreter of changing scenarios. In a three- dimensional temporal dialogue that combines the identity heritage of the past with demands and dynamics of the present and future perspectives, creativity molds ideas that transcend the boundaries of the ordinary and create an innovative vision of tomorrow. “Thorough observation and curiosity for the world around us have always been at the heart of the creativity and modernity of the Prada Group. In society, and thus in fashion, which is somehow a reflection of it, the only constant is change. The transformation and innovation of references, at the core of any evolution, has led us to interact with different cultural disciplines, at times apparently far from our own, allowing us to capture and anticipate the spirit of the times. -
Oracle Team Usa
MARINE & OFFSHORE CASE STUDY ORACLE TEAM USA © ORACLE TEAM USA / Photo: Guilain Grenier Challenge: ORACLE TEAM USA needed to design, build and test two boats based on entirely new, untested design specifi cations in less than three years to Teams were allowed to build two versions of the AC72. Each defend the 34th America’s Cup. team had to design and build its own AC72, based on what it had learned from sailing the smaller AC45, which ORACLE Solution: TEAM USA designed on behalf of the America’s Cup community. The team chose Dassault Systèmes’ “It became clear that the complexity of the AC72 was far 3DEXPERIENCE® platform, including CATIA for beyond what we had seen previously with older America’s virtual product design, ENOVIA for collaborative Cup boats,” explained Christoph Erbelding, senior structural innovation, and SIMULIA for realistic simulation engineer with the team, who previously worked in the to develop boats for the most technologically automotive and aerospace industries. “That complexity was advanced America’s Cup ever. what led us to 3DEXPERIENCE.” Benefi ts: CHOOSING THE 3DEXPERIENCE PLATFORM The 3DEXPERIENCE platform enabled ORACLE TEAM USA to rapidly develop, test and perfect “In America’s Cup racing, it has been typical for designers to its cutting-edge boat designs in a collaborative use their own favorite software,” Russell Coutts, CEO of rd virtual environment that fostered sharing and ORACLE TEAM USA, said. “After we won the 33 Cup, we leveraged the skills of its global teams. In a chose Dassault Systèmes because we wanted to have a fully miraculous comeback, ORACLE TEAM USA won integrated design program. -
CONTINUING CONNECTED TRANSACTION Sponsorship Of
Hong Kong Exchanges and Clearing Limited and The Stock Exchange of Hong Kong Limited take no responsibility for the contents of this announcement, make no representation as to its accuracy or completeness and expressly disclaim any liability whatsoever for any loss howsoever arising from or in reliance upon the whole or any part of the contents of this announcement. Via A. Fogazzaro n. 28, Milan, Italy Registry of Companies of Milan, Italy: No. 10115350158 (Incorporated under the laws of Italy as a joint-stock company) (Stock Code: 1913) CONTINUING CONNECTED TRANSACTION Sponsorship of Luna Rossa Challenge S.r.l. for its participation in the XXXVI America’s Cup The Board of Directors of PRADA S.p.A. is pleased to announce that on December 1st, 2017 (European time) the Company, entered into a sponsorship agreement with Luna Rossa Challenge S.r.l. for i t s participation in the XXXVI edition of the America’s Cup. Luna Rossa Challenge S.r.l. is a company indirectly controlled by Mr. Patrizio Bertelli, who is a Chief Executive Officer, an Executive Director and a substantial shareholder (as defined in the Listing Rules) of the Company. Therefore Luna Rossa Challenge S.r.l. is a connected person (as defined in the Listing Rules) of the Company. As such, the sponsorship agreement with Luna Rossa Challenge S.r.l. constitutes a continuing connected transaction of the Company under Chapter 14A of the Listing Rules. Since the relevant applicable percentage ratios (as defined in the Listing Rules) in respect of the sponsorship agreement with Luna Rossa Challenge S.r.l. -
LVC Semi Final a Day for the Tacticians
0515_27 x marte:Layout 1 14-05-2007 22:34 Pagina 1 w QUOTES OF THE DAY w w . l SEMI FINALS RACE 2 u n a r “ROMEO” RACE COMMITTEE o s s A Day for the Tacticians a FIRST WARNING SIGNAL 14:50 c h a l The wind came from everywhere, in gusts, from the land, shifts from the left, shifts from the right and then finally the sea l e n breeze filled in. The tacticians and navigators explained how they coped with some of Valencia’s MATCH 1 g e . c toughest conditions to date in two races showing two very different styles of match racing out on the racecourse EMIRATES TEAM NEW ZEALAND, NZL 92 VS DESAFIO ESPANOL 2007, ESP 97 o m Ray Davies, Strategist Matt Wachowicz, Navigator Peter Isler, Navigator Torben Grael, Tactician MATCH 2 Emirates Team New Zealand Desafio Espanol 2007 BMW Oracle Racing Luna Rossa Challenge LUNA ROSSA CHALLENGE, ITA 94 VS BMW ORACLE RACING, USA 98 SOPRA, I QUATTRO SEMIFINALISTI PRIMA DELLA PARTENZA “SI ANNUSANO” VICINO ALLA BARCA GIURIA It was certainly a tough day on There weren’t too many opportunities The thing that was clear going You never know what is going the water yesterday, you had to keep to split, they established a controlling into the pre-start, it was to happen on a day like yesterday, it close and take a bit of a risk, position and although we were going to be a very shifty day. normal match race style can L defend and back yourself. -
Separate Financial Statements 2020 Separate Financial Statements
Separate Financial Statements Financial Separate 2020 Separate Financial Statements 2020 PRADA spa (Hong Kong Stock code: 1913) SEPARATE FINANCIAL STATEMENTS 2020 SFS 2020-19apr 2021.indd 2 19/04/21 14:48 SFS 2020-19apr 2021.indd 3 19/04/21 14:48 TABLE OF CONTENTS Corporate Information 3 Financial Review 7 Corporate Governance 19 Financial Statements 39 Notes to the Financial Statements 45 Independent Auditors’ Report 117 Board of Statutory Auditors’ Report 127 SFS 2020-19apr 2021.indd 1 19/04/21 14:48 Miuccia Prada and Patrizio Bertelli SFS 2020-19apr 2021.indd 2 19/04/21 14:48 CORPORATE INFORMATION PRADA spa Separate Financial Statements 2020 - Corporate Information 3 SFS 2020-19apr 2021.indd 3 19/04/21 14:48 PRADA S.P.A. CORPORATE INFORMATION Registered Office Via A. Fogazzaro, 28 20135 Milan, Italy Head Office Via A. Fogazzaro, 28 20135 Milan, Italy Place of business in Hong Kong 8th Floor, One Taikoo Place registered under Part 16 979 King’s Road of the Hong Kong Companies Quarry Bay, Hong Kong S.A.R. (P.R.C.) Ordinance Company Corporate web site www.pradagroup.com Hong Kong Stock Exchange 1913 Identification Number Share Capital Euro 255,882,400 (represented by 2,558,824,000 shares of Euro 0.10 each) Board of Directors Carlo Mazzi (Chairman & Executive Director) Miuccia Prada Bianchi (Chief Executive Officer & Executive Director) Patrizio Bertelli (Chief Executive Officer & Executive Director) Alessandra Cozzani (Chief Financial Officer & Executive Director) Stefano Simontacchi (Non-Executive Director) Maurizio Cereda (Independent -
Un Catamarano Per La Coppa Di America
Alba rusata, vela abbagnata Nella foto sopra si può notare che la parte poppiera dell’ala Un catamarano è ruotata rispetto all’elemento prodiero per la Coppa © ACEA / Gilles Martin-Raget Foto sotto, l’AC72 di Luna Rossa Challenge 2013, in navigazione sulle acque di America di Auckland (Nuova Zelanda) © Luna Rossa / Nigel Marpel Stéphan Jules Buchet Socio del Gruppo di Roma daggerboard (deriva retrattile a lamina). Ciascuno scafo ha un timone e un dag- gerboard. Non possono esistere altre appendici. Ciascun timone può avere un’estensione massima di 5 m, mentre 7 m è quella mas- sima per ciascuna deriva retrattile. Il peso complessivo dell’equipaggio, di 11 elementi, deve essere compreso fra 957 e 1012 kg; qualora non fosse raggiunto il peso minimo, dovranno essere posti dei pesi correttori in piombo. Inizialmente era previsto l’imbarco anche di un ospite, non regatante, e di operato- ri video, non regatanti, ma le raccoman- dazioni fatte dopo l’incidente di maggio, hanno escluso la presenza di altro perso- Vista d’insieme di un catamarano AC72 nale oltre a quello dell’equipaggio attivo. © Guilain Grenier Fra le varie regole di classe previste, una prevede che il consorzio proprietario del- l’imbarcazione sia capace di disassem- blare e assemblare un AC72 come segue: a prossima sfida per la conquista Si tratta di un catamarano simmetrico dell’America’s Cup sarà combattu- con la randa rigida, chiamata comune- (a) in 24 ore smontare e rimpacchettare L ta utilizzando i catamarani tecnolo- mente ala, che ingloba l’albero. AC72 l’ala in contenitori da trasporto con le gici a vela rigida di 72 piedi, ideati per Queste imbarcazioni assicurano velocità seguenti dimensioni: questa manifestazione e che prendono il elevate anche con pochissimo vento. -
2013 Sustainability Report Introduction
2013 sustainability report introduction our vision for the 34th america’s cup was to deliver a model sustainable sporting event. The America’s Cup is the world’s premier sailing race, and the oldest trophy in international sport, predating the modern Olympic Games by 45 years. The America’s Cup is named after the schooner America, which won a race around the Isle of Wight on August 22, 1851, against a fleet of British yachts. Four nations have won the America’s Cup in its 162-year history: the United States, Australia, New Zealand and Switzerland. ORACLE TEAM USA won the 33RD America’s Cup in Valencia, Spain, in February 2010, and selected San Francisco as the host city for the 34TH America’s Cup. ORACLE TEAM USA, representing the Golden Gate Yacht Club, won the 33RD America’s Cup in Valencia, Spain, in February 2010, and the Golden Gate Yacht Club selected San Francisco as the host city for the 34TH America’s Cup. The America’s Cup Event Authority (“ACEA”) aspired to implement best practice standards in delivering a sustainable 34TH America’s Cup event in San Francisco. Our vision was to deliver a model sustainable sporting event and to leave a positive legacy in the community and on the sport of sailing. ACEA published the 34TH America’s Cup Sustainability Plan 1 (“Sustainability Plan”) in March 2012, outlining our approach to delivering sustainable event activities in San Francisco. We pledged to understand our impacts, reduce potentially negative impacts as far as possible, and maximize legacy benefits. Since that time, ACEA has monitored and tracked the event’s performance and progress in order to inform stakeholders and the public about activities and achievements, and provide transparent reporting on event activities in San Francisco. -
The 36Th America's
He Waka Eke Noa We are all paddling in the same waka Published: October 2019 *All dates and information correct at time of publication The America’s Cup has a special place in And it provides a stage for us to tell our stories; New Zealand’s recent history, and not just including our unique, shared voyaging history, from a sporting point of view. our deep connection with the sea (reflected in our sailing successes) and the expertise of our world Whether hosting it here or competing for it class marine industry. The event will profile New overseas, moments from the America’s Cup - Zealand technology and innovation while providing celebration and heartbreak - are seared into our a significant economic boost to many sectors. collective memory. The Auld Mug has captured our imaginations and provided an opportunity to It will also be a lot of fun. The Event Village in take our skills, culture and innovation to the world. the heart of Auckland will create a wonderful hub where visitors and locals can experience So it is with great pleasure that I welcome the the vibrancy of the Cup and the best hospitality, release of this Event Concept for the 36th America’s which New Zealand is famed for. It will provide Cup, setting out the important vision and principles a world class venue for the bases, which we to ensure the event delivers for us all. achieved while minimising any new intrusions New Zealand knows how to host major global into the harbour. Negotiating to remove the events. Whether it’s the World Masters Games, tank farm off Wynyard has helped revitalise the the Rugby World Cup or of course previous waterfront space that will enable events of this America’s Cups, Kiwis come together in scale to be hosted well into the future.