Zno As a Functional Material, a Review
Total Page:16
File Type:pdf, Size:1020Kb
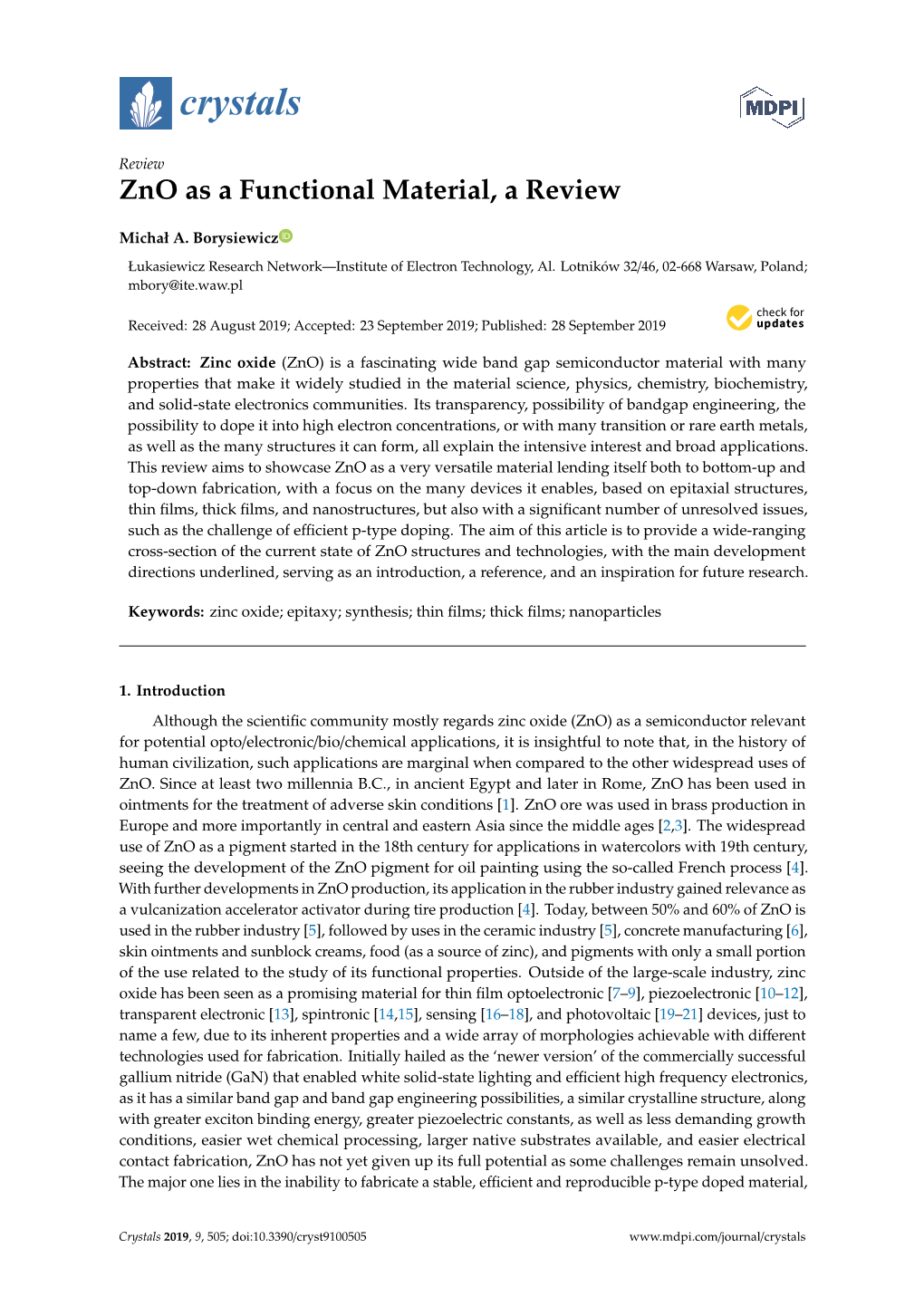
Load more
Recommended publications
-
Toward the Growth of Self-Catalyzed Zno Nanowires Perpendicular to the Surface of Silicon and Glass Substrates, by Pulsed Laser Deposition
materials Article Toward the Growth of Self-Catalyzed ZnO Nanowires Perpendicular to the Surface of Silicon and Glass Substrates, by Pulsed Laser Deposition Basma ElZein 1,2,* , Yingbang Yao 3 , Ahmad S. Barham 4 , Elhadj Dogheche 5 and Ghassan E. Jabbour 6 1 Electrical Engineering Department, College of Engineering, University of Business and Technology (UBT), Jeddah 21361, Saudi Arabia 2 Institute of Electronics, Microelectronics and Nanotechnology, CNRS and University Lille Nord de France- Avenue Poincaré, CEDEX, 59652 Villeneuve d’Ascq, France 3 Faculty of Materials and Energy, Guangdong University of Technology, Guangzhou 510006, China; [email protected] 4 General Subjects Department, College of Engineering, University of Business and Technology (UBT), Jeddah 21361, Saudi Arabia; [email protected] 5 Campus Le Mont Houy, IEMN CNRS, Polytechnic University Hauts de France, CEDEX, 59309 Valenciennes, France; [email protected] 6 Canada Research Chair in Engineered Advanced Materials and Devices, Faculty of Engineering, University of Ottawa, Ottawa, ON K1N 6N5, Canada; [email protected] * Correspondence: [email protected] Received: 7 September 2020; Accepted: 29 September 2020; Published: 5 October 2020 Abstract: Vertically-oriented zinc oxide (ZnO) nanowires were synthesized on glass and silicon substrates by Pulsed Laser Deposition and without the use of a catalyst. An intermediate c-axis oriented nanotextured ZnO seed layer in the form of nanowall network with honey comb structure allows the growth of high quality, self-forming, and vertically-oriented nanowires at relatively low temperature (<400 ◦C) and under argon atmosphere at high pressure (>5 Torr). Many parameters were shown to affect the growth of the ZnO nanowires such as gas pressure, substrate–target distance, and laser energy. -
Catalytic Asymmetric Addition of Diorganozinc Reagents to N
Catalytic asymmetric addition of diorganozinc SPECIAL FEATURE reagents to N-phosphinoylalkylimines Alexandre Coˆ te´ , Alessandro A. Boezio, and Andre´ B. Charette* Department of Chemistry, University of Montreal, P.O. Box 6128, Station Downtown, Montreal, QC, Canada H3C 3J7 Edited by Jack Halpern, University of Chicago, Chicago, IL, and approved February 4, 2004 (received for review October 31, 2003) The synthesis of ␣-chiral amines bearing two alkyl groups has been hampered by the accessibility and stability of the alkylimine precursor. Herein, we report an efficient strategy to generate the alkyl-substituted imine in situ that is compatible with the Me- DuPHOS monoxide⅐Cu(I) catalyzed addition of diorganozinc re- agents. The sulfinic acid adduct of the imine is readily prepared by mixing diphenylphosphinic amide, the aldehyde, and sulfinic acid. The sulfinic acid adduct is generally isolated by filtration. The addition of diorganozinc reagents in the presence of Me-DuPHOS monoxide⅐Cu(I) and the in situ-generated imines affords the cor- Fig. 1. Bioactive ␣-chiral amines. responding ␣-chiral amines in high yields and enantiomeric excesses. sensitive imines from stable precursors has been a strategy that he synthesis of ␣-chiral amines using the catalytic asymmetric has been quite successful in a number of cases. Typically, a stable Taddition of diorganozinc reagents has produced very exciting imine adduct is used as a precursor and is converted to the imine results in recent years (1–3). This very important subunit is in situ (Scheme 2). The method involves the use of a leaving ␣ CHEMISTRY commonly found in many pharmaceuticals and other biologically group (LG) on the -carbon of the N-protected amine. -
Pyrophoric Materials
Appendix A PYROPHORIC MATERIALS Pyrophoric materials react with air, or with moisture in air. Typical reactions which occur are oxidation and hydrolysis, and the heat generated by the reactions may ignite the chemical. In some cases, these reactions liberate flammable gases which makes ignition a certainty and explosion a real possibility. Examples of pyrophoric materials are shown below. (List may not be complete) (a) Pyrophoric alkyl metals and derivatives Groups Dodecacarbonyltetracobalt Silver sulphide Dialkytzincs Dodecacarbonyltriiron Sodium disulphide Diplumbanes Hexacarbonylchromium Sodium polysulphide Trialkylaluminiums Hexacarbonylmolybdenum Sodium sulphide Trialkylbismuths Hexacarbonyltungsten Tin (II) sulphide Nonacarbonyldiiron Tin (IV) sulphide Compounds Octacarbonyldicobalt Titanium (IV) sulphide Bis-dimethylstibinyl oxide Pentacarbonyliron Uranium (IV) sulphide Bis(dimethylthallium) acetylide Tetracarbonylnickel Butyllithium (e) Pyrophoric alkyl non-metals Diethylberyllium (c) Pyrophoric metals (finely divided state) Bis-(dibutylborino) acetylene Bis-dimethylarsinyl oxide Diethylcadmium Caesium Rubidium Bis-dimethylarsinyl sulphide Diethylmagnesium Calcium Sodium Bis-trimethylsilyl oxide Diethylzinc Cerium Tantalum Dibutyl-3-methyl-3-buten-1-Yniborane Diisopropylberyllium Chromium Thorium Diethoxydimethylsilane Dimethylberyllium Cobalt Titanium Diethylmethylphosphine Dimethylbismuth chloride Hafnium Uranium Ethyldimthylphosphine Dimethylcadmium Iridium Zirconium Tetraethyldiarsine Dimethylmagnesium Iron Tetramethyldiarsine -
Chemical List
1 EXHIBIT 1 2 CHEMICAL CLASSIFICATION LIST 3 4 1. Pyrophoric Chemicals 5 1.1. Aluminum alkyls: R3Al, R2AlCl, RAlCl2 6 Examples: Et3Al, Et2AlCl, EtAlCl2, Me3Al, Diethylethoxyaluminium 7 1.2. Grignard Reagents: RMgX (R=alkyl, aryl, vinyl X=halogen) 8 1.3. Lithium Reagents: RLi (R = alkyls, aryls, vinyls) 9 Examples: Butyllithium, Isobutyllithium, sec-Butyllithium, tert-Butyllithium, 10 Ethyllithium, Isopropyllithium, Methyllithium, (Trimethylsilyl)methyllithium, 11 Phenyllithium, 2-Thienyllithium, Vinyllithium, Lithium acetylide ethylenediamine 12 complex, Lithium (trimethylsilyl)acetylide, Lithium phenylacetylide 13 1.4. Zinc Alkyl Reagents: RZnX, R2Zn 14 Examples: Et2Zn 15 1.5. Metal carbonyls: Lithium carbonyl, Nickel tetracarbonyl, Dicobalt octacarbonyl 16 1.6. Metal powders (finely divided): Bismuth, Calcium, Cobalt, Hafnium, Iron, 17 Magnesium, Titanium, Uranium, Zinc, Zirconium 18 1.7. Low Valent Metals: Titanium dichloride 19 1.8. Metal hydrides: Potassium Hydride, Sodium hydride, Lithium Aluminum Hydride, 20 Diethylaluminium hydride, Diisobutylaluminum hydride 21 1.9. Nonmetal hydrides: Arsine, Boranes, Diethylarsine, diethylphosphine, Germane, 22 Phosphine, phenylphosphine, Silane, Methanetellurol (CH3TeH) 23 1.10. Non-metal alkyls: R3B, R3P, R3As; Tributylphosphine, Dichloro(methyl)silane 24 1.11. Used hydrogenation catalysts: Raney nickel, Palladium, Platinum 25 1.12. Activated Copper fuel cell catalysts, e.g. Cu/ZnO/Al2O3 26 1.13. Finely Divided Sulfides: Iron Sulfides (FeS, FeS2, Fe3S4), and Potassium Sulfide 27 (K2S) 28 REFERRAL -
Grown and Characterization of Zno Aligned Nanorod Arrays for Sensor Applications
energies Article Grown and Characterization of ZnO Aligned Nanorod Arrays for Sensor Applications Arkady N. Redkin, Eugene E. Yakimov, Maria V. Evstafieva and Eugene B. Yakimov * Institute of Microelectronics Technology RAS, 6 Academician Ossipyan str., 142432 Chernogolovka, Russia; [email protected] (A.N.R.); [email protected] (E.E.Y.); [email protected] (M.V.E.) * Correspondence: [email protected] Abstract: ZnO nanorods are promising materials for many applications, in particular for UV de- tectors. In the present paper, the properties of high crystal quality individual ZnO nanorods and nanorod arrays grown by the self-catalytic CVD method have been investigated to assess their possible applicationsfor UV photodetectors. X-ray diffraction, Raman spectroscopy and cathodolu- minescence investigations demonstrate the high quality of nanorods. The nanorod resistivity and carrier concentration in dark is estimated. The transient photocurrent response of both as grown and annealed at 550 ◦C nanorod array under UV illumination pulses is studied. It is shown that annealing increases the sensitivity and decreases the responsivity that is explained by oxygen out-diffusion and the formation of near surface layer enriched with oxygen vacancies. Oxygen vacancy formation due to annealing is confirmed by an increase of green emission band intensity. Keywords: ZnO nanorod; self-catalytic CVD method; photoresponse; cathodoluminescence Citation: Redkin, A.N.; Yakimov, E.E.; Evstafieva, M.V.; Yakimov, E.B. Grown and Characterization of ZnO 1. Introduction Aligned Nanorod Arrays for Sensor Zinc oxide, a well-known direct bandgap II–VI semiconductor, is a material with Applications. Energies 2021, 14, 3750. large exciton binding energy (60 meV) and a wide bandgap (Eg ~ 3.37 eV) [1], suitable for https://doi.org/10.3390/en14133750 short wavelength optoelectronic applications [2]. -
Title Exploration of Dimethylzinc-Mediated Radical Reactions
Title Exploration of Dimethylzinc-Mediated Radical Reactions. Author(s) Yamada, Ken-Ichi; Tomioka, Kiyoshi Citation The Chemical Record (2015), 15(5): 854-871 Issue Date 2015-10 URL http://hdl.handle.net/2433/203021 This is the peer reviewed version of the following article: Yamada, K.-i. and Tomioka, K. (2015), Exploration of Dimethylzinc-Mediated Radical Reactions. Chem. Rec., 15: 854‒871, which has been published in final form at http://dx.doi.org/10.1002/tcr.201500017. This article may be used for non-commercial purposes in accordance with Wiley Right Terms and Conditions for Self-Archiving.; The full-text file will be made open to the public on 17 JUL 2016 in accordance with publisher's 'Terms and Conditions for Self-Archiving'.; This is not the published version. Please cite only the published version.; この論文は出版社版でありません。引用の際に は出版社版をご確認ご利用ください。 Type Journal Article Textversion author Kyoto University PersonalPersonal AccountAccount THE CHEMICAL Exploration of Dimethylzinc- RECORD Mediated Radical Reactions THE CHEMICAL RECORD Ken-ichi Yamada,[a] and Kiyoshi Tomioka[b] [a] Graduate School of Pharmaceutical Sciences, Kyoto University E-mail: [email protected] [b] Department of Medicinal Chemistry, Faculty of Pharmaceutical Sciences, Doshisha Women's College of Liberal Arts E-mail: [email protected] Received: [will be filled in by the editorial staff] Published online: [will be filled in by the editorial staff] ABSTRACT: In this account, our studies on radical reactions that are promoted by dimethylzinc and air are described. Advantages of this reagent and differences from conventional radical initiators, such as triethylborane, are discussed. Keywords: radical reaction, dimethylzinc, C(sp3)–H bond functionalization, C–C bond formation, Umpolung Introduction It has been long time since the word "radical" changed its useful functional group transformations via a radical meaning in chemistry. -
Studies on Group Ii Metal Alkyls Particularly Those of Beryllium
Durham E-Theses Studies on group ii metal alkyls particularly those of beryllium Robert, P.D. How to cite: Robert, P.D. (1968) Studies on group ii metal alkyls particularly those of beryllium, Durham theses, Durham University. Available at Durham E-Theses Online: http://etheses.dur.ac.uk/8717/ Use policy The full-text may be used and/or reproduced, and given to third parties in any format or medium, without prior permission or charge, for personal research or study, educational, or not-for-prot purposes provided that: • a full bibliographic reference is made to the original source • a link is made to the metadata record in Durham E-Theses • the full-text is not changed in any way The full-text must not be sold in any format or medium without the formal permission of the copyright holders. Please consult the full Durham E-Theses policy for further details. Academic Support Oce, Durham University, University Oce, Old Elvet, Durham DH1 3HP e-mail: [email protected] Tel: +44 0191 334 6107 http://etheses.dur.ac.uk STUDIES ON GROUP II METAL ALKYLS PARTICULARLY THOSE OF BERYLLIUM by P.D. ROBERTS, B.Sc. A thesis submitted for the Degree of Doctor of Philosophy in the University of Durham JULY 1968 Acknowledgements The author wishes to thank Professor G.E. Coates, M.A. , D.Sc, F.R.I.C., under whose supervision this research was carried out, for his constant encouragement and valuable advice. Thanks are also given to Dr. A.J. Downs, formerly of the University of Newcastle upon Tyne, for his help with vibrational spectroscopy and to members of this department, especially Dr. -
Heterojunctions Between Zinc Oxide Nanostructures and Organic Semiconductor
Heterojunctions between zinc oxide nanostructures and organic semiconductor Amal Wadeasa Norrköping 2011 Heterojunctions between zinc oxide nanostructures and organic semiconductor Amal Wadeasa Linköping Studies in Science and Technology. Dissertations, No. 1405 Copyright, 2011, Amal Wadeasa, unless otherwise noted ISBN: 978-91-7393-046-8 ISSN: 0345-7524 Abstract Lighting is a big business, lighting consumes considerable amount of the electricity. These facts motivate for the search of new illumination technologies that are efficient. Semiconductor light emitting diodes (LEDs) have huge potential to replace the traditional primary incandescent lighting sources. They are two basic types of semiconductor LEDs being explored: inorganic and organic semiconductor light emitting diodes. While electroluminescence from p-n junctions was discovered more than a century ago, it is only from the 1960s that their development has accelerated as indicated by an exponential increase of their efficiency and light output, with a doubling occurring about every 36 months, in a similar way to Moore's law in electronics. These advances are generally attributed to the parallel de velopment o f semiconductor te chnologies, optics a nd m aterial science. Organic light emitting diodes (OLEDs) have rapidly matured during the last 30 years driven by the possibility to create large area light-emitting diodes and displays. Another driving force to specifically use semiconducting polymers is the possibility to build the OLED on conventional flexible substrates via low-cost manufacturing techniques such as printing techniques, which open the way for large area productions. This thesis deals with the demonstration and investigation of heterojunction LEDs ba sed o n p-organic semiconductor and n-ZnO nanostructures. -
Zno and Zncdo Metal Organic Vapor Phase Epitaxy: Epitaxy, Defects and Band Gap Engineering
ZnO and ZnCdO metal organic vapor phase epitaxy: epitaxy, defects and band gap engineering By Vishnukanthan Venkatachalapathy Submitted in partial fulfillment of the requirements for the degree of Philosophiae Doctor Department of Physics/Centre for Materials science and Nanotechnology Faculty of Mathematics and Natural Sciences University of Oslo Dedicated to my father Abstract Zinc oxide (ZnO) and its ternary alloys have high potential to compete with III-V nitrides for optoelectronic applications. Furthermore, oxide semiconductors receive considerable attention due to their low cost of fabrication, chemical robustness and high thermal conductance. The goal of this work was (i) to explore manufacturing route of ZnO and ZnCdO films using metal organic vapor phase epitaxy (MOVPE) in vector flow epitaxy mode and (ii) to master structural/optical properties of these films for preparing such as components in electronics, optoelectronics and solar energy conversion. Our starting point was to study the influence of basic synthesis parameters on the structural and luminescence properties of pure ZnO films on c-axis oriented sapphire substrates. The samples were synthesized using previously unexplored for ZnO vector flow epitaxy mode of MOVPE employing systematic variations of fundamental synthesis parameters such as temperature, pressure, II/VI molar ratio, total carrier gas flow ratio, susceptor rotation rate, etc. It was concluded that the growth temperature affects the precursor pyrolysis and in these terms pre-determines the actual II/VI molar ratio available at the reaction zone. Concurrently, direct II/VI molar ratio variations by supplying different amount of precursors influences the properties too, for example, changing intrinsic defect balance in the films. -
Comparison of Photocatalytic and Transport Properties of Tio2 and Zno Nanostructures for Solar-Driven Water Splitting
PCCP View Article Online PAPER View Journal | View Issue Comparison of photocatalytic and transport properties of TiO2 and ZnO nanostructures Cite this: Phys. Chem. Chem. Phys., 2015, 17, 7775 for solar-driven water splitting† ab ab a a Simelys Herna´ndez,* Diana Hidalgo, Adriano Sacco, Angelica Chiodoni, Andrea Lamberti,ab Valentina Cauda,a Elena Tressoab and Guido Saraccob Titanium dioxide (TiO2) and zinc oxide (ZnO) nanostructures have been widely used as photo-catalysts due to their low-cost, high surface area, robustness, abundance and non-toxicity. In this work, four TiO2 and ZnO-based nanostructures, i.e. TiO2 nanoparticles (TiO2 NPs), TiO2 nanotubes (TiO2 NTs), ZnO nanowires (ZnO NWs) and ZnO@TiO2 core–shell structures, specifically prepared with a fixed thickness of about 1.5 mm, are compared for the solar-driven water splitting reaction, under AM1.5G simulated sunlight. Complete characterization of these photo-electrodes in their structural and photo-electrochemical properties was carried out. Both TiO2 NPs and NTs showed photo-current saturation reaching 0.02 and Creative Commons Attribution-NonCommercial 3.0 Unported Licence. 0.12 mA cmÀ2, respectively, for potential values of about 0.3 and 0.6 V vs. RHE. In contrast, the ZnO NWs and the ZnO@TiO2 core–shell samples evidence a linear increase of the photocurrent with the applied potential, reaching 0.45 and 0.63 mA cmÀ2 at 1.7 V vs. RHE, respectively. However, under concen- trated light conditions, the TiO2 NTs demonstrate a higher increase of the performance with respect to the ZnO@TiO2 core–shells. Such material-dependent behaviours are discussed in relation with the different Received 15th December 2014, charge transport mechanisms and interfacial reaction kinetics, which were investigated through electro- Accepted 11th February 2015 chemical impedance spectroscopy. -
Nano-Materials Employment in Energy Harvesting and Storage Devices
Politecnico di Torino Porto Institutional Repository [Doctoral thesis] Nano-materials employment in energy harvesting and storage devices Original Citation: Dimitrios Tamvakos (2015). Nano-materials employment in energy harvesting and storage devices. PhD thesis Availability: This version is available at : http://porto.polito.it/2598393/ since: March 2015 Published version: DOI:10.6092/polito/porto/2598393 Terms of use: This article is made available under terms and conditions applicable to Open Access Policy Arti- cle ("Creative Commons: Attribution 3.0") , as described at http://porto.polito.it/terms_and_ conditions.html Porto, the institutional repository of the Politecnico di Torino, is provided by the University Library and the IT-Services. The aim is to enable open access to all the world. Please share with us how this access benefits you. Your story matters. (Article begins on next page) POLITECNICO DI TORINO DEPARTMENT OF APPLIED SCIENCES AND TECHNOLOGY Doctorate in electronic devices (ciclo XXVII) Nano-materials employment in energy harvesting and storage devices. Scientific supervisor: Dr. Daniele Pullini (Fiat research centre) Academic advisor: Prof. Giancarlo Cicero (Politecnico di Torino) Candidate: Dimitrios Tamvakos ii Contents List of Figures vii List of Tables xi Abstact…..................................................................................................................................................................1 Chapter 1 ..................................................................................................................................................................4 -
Titanium Dioxide-Coated Zinc Oxide Nanorods As an Efficient
nanomaterials Article Titanium Dioxide-Coated Zinc Oxide Nanorods as an Efficient Photoelectrode in Dye-Sensitized Solar Cells Qiang Zhang 1 , Shengwen Hou 2 and Chaoyang Li 1,2,* 1 School of Systems Engineering, Kochi University of Technology, Kami, Kochi 782-8502, Japan; [email protected] 2 Center for Nanotechnology, Kochi University of Technology, Kami, Kochi 782-8502, Japan; [email protected] * Correspondence: [email protected]; Tel.: +81-887-57-2106 Received: 14 July 2020; Accepted: 12 August 2020; Published: 14 August 2020 Abstract: Well-arrayed zinc oxide nanorods applied as photoelectrodes for dye-sensitized solar cells were synthesized on an aluminum-doped zinc oxide substrate by the multi-annealing method. In order to improve the chemical stability and surface-to-volume ratio of photoanodes in dye-sensitized solar cells, the synthesized zinc oxide nanorods were coated with pure anatase phase titanium dioxide film using a novel mist chemical vapor deposition method. The effects of the titanium dioxide film on the morphological, structural, optical, and photovoltaic properties of zinc oxide–titanium dioxide core–shell nanorods were investigated. It was found that the diameter and surface-to-volume ratio of zinc oxide nanorods were significantly increased by coating them with titanium dioxide thin film. The power conversion efficiency of dye-sensitized solar cells was improved from 1.31% to 2.68% by coating titanium dioxide film onto the surface of zinc oxide nanorods. Keywords: titanium dioxide; zinc oxide; core–shell nanorods; mist chemical vapor deposition; dye-sensitized solar cell 1. Introduction Since Grätzel et al.