A Hybrid Peridynamics and Physics Engine Approach
Total Page:16
File Type:pdf, Size:1020Kb
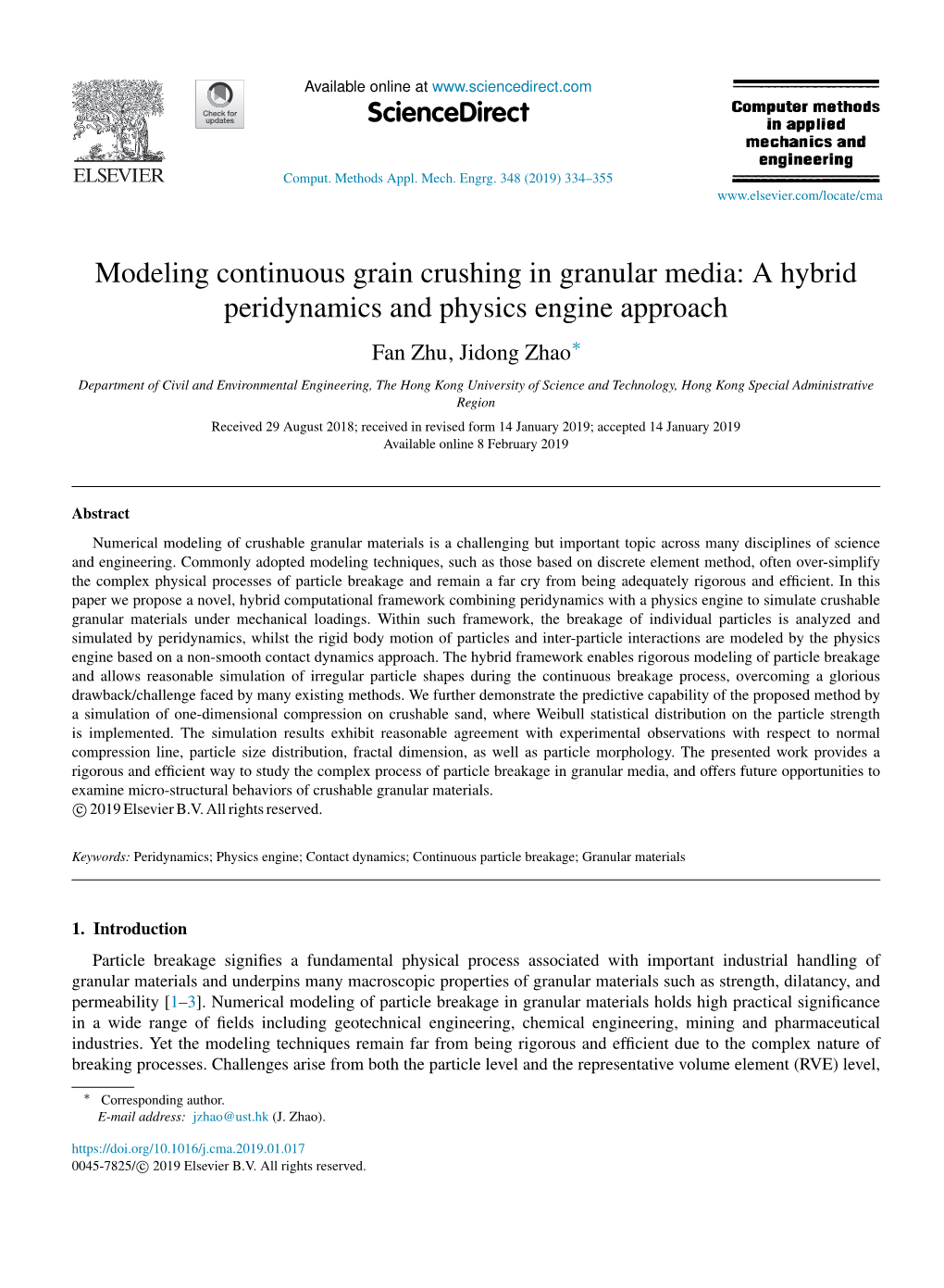
Load more
Recommended publications
-
An Optimal Solution for Implementing a Specific 3D Web Application
IT 16 060 Examensarbete 30 hp Augusti 2016 An optimal solution for implementing a specific 3D web application Mathias Nordin Institutionen för informationsteknologi Department of Information Technology Abstract An optimal solution for implementing a specific 3D web application Mathias Nordin Teknisk- naturvetenskaplig fakultet UTH-enheten WebGL equips web browsers with the ability to access graphic cards for extra processing Besöksadress: power. WebGL uses GLSL ES to communicate with graphics cards, which uses Ångströmlaboratoriet Lägerhyddsvägen 1 different Hus 4, Plan 0 instructions compared with common web development languages. In order to simplify the development process there are JavaScript libraries handles the Postadress: Box 536 751 21 Uppsala communication with WebGL. On the Khronos website there is a listing of 35 different Telefon: JavaScript libraries that access WebGL. 018 – 471 30 03 It is time consuming for developers to compare the benefits and disadvantages of all Telefax: these 018 – 471 30 00 libraries to find the best WebGL library for their need. This thesis sets up requirements of a Hemsida: specific WebGL application and investigates which libraries that are best for http://www.teknat.uu.se/student implmeneting its requirements. The procedure is done in different steps. Firstly is the requirements for the 3D web application defined. Then are all the libraries analyzed and mapped against these requirements. The two libraries that best fulfilled the requirments is Three.js with Physi.js and Babylon.js. The libraries is used in two seperate implementations of the intitial game. Three.js with Physi.js is the best libraries for implementig the requirements of the game. -
Geometry & Computation for Interactive Simulation
Geometry & Computation for Interactive Simulation Jorg Peters (CISE University of Florida, USA), Dinesh Pai (University of British Columbia), Ulrich Reif (Technische Universitaet Darmstadt) Sep 24 – Sep 29, 2017 1 Overview The workshop advanced the state of the art in geometry and computation for interactive simulation by in- troducing to each other researchers from different branches of academia, research labs and industry. These researchers share the common goal of improving the interface between geometry and computation for physi- cal simulation – but approach it with differing emphasis, techniques and toolkits. A key issue for all partici- pants is to shorten process times and to improve the outcomes of the design-analysis cycle. That is, to more quickly optimize shape, structure and properties to achieve one or multiple design goals. Correspondingly, the challenges laid out covered a wide spectrum from hierarchical design and prediction of novel 3D printed materials, to multi-objective optimization minimizing fuel consumption of commercial airplanes, to creating training scenarios for minimally invasive surgery, to multi-point interactive force feedback for virtually plac- ing an engine into a restricted cavity. These challenges map to challenges in the underlying areas of geometry processing, computational geometry, geometric design, formulation of simulation models, isogeometric and higher-order isoparametric design with splines and meshingless approaches, to real-time computation for interactive surgical force-feedback simulation. The workshop was highly succesful in presenting and con- trasting this rich set of techniques. And it generated recommendations for educating future generation of researchers in geometry and computation for interactive simulation (see outcomes). The lower than usual number of participants (due to a second series of earth quakes just before the meeting) allowed for increased length of individual presentations, so as to discuss topics and ideas at length, and to address basics theory. -
Physics Editor Mac Crack Appl
1 / 2 Physics Editor Mac Crack Appl This is a list of software packages that implement the finite element method for solving partial differential equations. Software, Features, Developer, Version, Released, License, Price, Platform. Agros2D, Multiplatform open source application for the solution of physical ... Yves Renard, Julien Pommier, 5.0, 2015-07, LGPL, Free, Unix, Mac OS X, .... For those who prefer to run Origin as an application on your Mac desktop without a reboot of the Mac OS, we suggest the following virtualization software:.. While having the same core (Unigine Engine), there are 3 SDK editions for ... Turnkey interactive 3D app development; Consulting; Software development; 3D .... Top Design Engineering Software: The 50 Best Design Tools and Apps for ... design with the intelligence of 3D direct modeling,” for Windows, Linux, and Mac users. ... COMSOL is a platform for physics-based modeling and simulation that serves as ... and tools for electrical, mechanical, fluid flow, and chemical applications .... Experience the world's most realistic and professional digital art & painting software for Mac and Windows, featuring ... Your original serial number will be required. ... Easy-access panels let you instantly adjust how paint is applied to the brush and how the paint ... 4 physical cores/8 logical cores or higher (recommended).. A dynamic soft-body physics vehicle simulator capable of doing just about anything. ... Popular user-defined tags for this product: Simulation .... Easy-to-Use, Powerful Tools for 3D Animation, GPU Rendering, VFX and Motion Design. ... Trapcode Suite 16 With New Physics, Magic Bullet Suite 14 With New Color Workflows Now ... Maxon Cinema 4D Immediately Available for M1-Powered Macs image .. -
Physics Simulation Game Engine Benchmark Student: Marek Papinčák Supervisor: Doc
ASSIGNMENT OF BACHELOR’S THESIS Title: Physics Simulation Game Engine Benchmark Student: Marek Papinčák Supervisor: doc. Ing. Jiří Bittner, Ph.D. Study Programme: Informatics Study Branch: Web and Software Engineering Department: Department of Software Engineering Validity: Until the end of summer semester 2018/19 Instructions Review the existing tools and methods used for physics simulation in contemporary game engines. In the review, cover also the existing benchmarks created for evaluation of physics simulation performance. Identify parts of physics simulation with the highest computational overhead. Design at least three test scenarios that will allow to evaluate the dependence of the simulation on carefully selected parameters (e.g. number of colliding objects, number of simulated projectiles). Implement the designed simulation scenarios within Unity game engine and conduct a series of measurements that will analyze the behavior of the physics simulation. Finally, create a simple game that will make use of the tested scenarios. References [1] Jason Gregory. Game Engine Architecture, 2nd edition. CRC Press, 2014. [2] Ian Millington. Game Physics Engine Development, 2nd edition. CRC Press, 2010. [3] Unity User Manual. Unity Technologies, 2017. Available at https://docs.unity3d.com/Manual/index.html [4] Antonín Šmíd. Comparison of the Unity and Unreal Engines. Bachelor Thesis, CTU FEE, 2017. Ing. Michal Valenta, Ph.D. doc. RNDr. Ing. Marcel Jiřina, Ph.D. Head of Department Dean Prague February 8, 2018 Bachelor’s thesis Physics Simulation Game Engine Benchmark Marek Papinˇc´ak Department of Software Engineering Supervisor: doc. Ing. Jiˇr´ıBittner, Ph.D. May 15, 2018 Acknowledgements I am thankful to Jiri Bittner, an associate professor at the Department of Computer Graphics and Interaction, for sharing his expertise and helping me with this thesis. -
Locotest: Deploying and Evaluating Physics-Based Locomotion on Multiple Simulation Platforms
LocoTest: Deploying and Evaluating Physics-based Locomotion on Multiple Simulation Platforms Stevie Giovanni and KangKang Yin National University of Singapore fstevie,[email protected] Abstract. In the pursuit of pushing active character control into games, we have deployed a generalized physics-based locomotion control scheme to multiple simulation platforms, including ODE, PhysX, Bullet, and Vortex. We first overview the main characteristics of these physics engines. Then we illustrate the major steps of integrating active character controllers with physics SDKs, together with necessary implementation details. We also evaluate and compare the performance of the locomotion control on different simulation platforms. Note that our work only represents an initial attempt at doing such evaluation, and additional refine- ment of the methodology and results can still be expected. We release our code online to encourage more follow-up works, as well as more interactions between the research community and the game development community. Keywords: physics-based animation, simulation, locomotion, motion control 1 Introduction Developing biped locomotion controllers has been a long-time research interest in the Robotics community [3]. In the Computer Animation community, Hodgins and her col- leagues [12, 7] started the many efforts on locomotion control of simulated characters. Among these efforts, the simplest class of locomotion control methods employs re- altime feedback laws for robust balance recovery [12, 7, 14, 9, 4]. Optimization-based control methods, on the other hand, are more mathematically involved, but can incor- porate more motion objectives automatically [10, 8]. Recently, data-driven approaches have become quite common, where motion capture trajectories are referenced to further improve the naturalness of simulated motions [14, 10, 9]. -
Physics Engine Design and Implementation Physics Engine • a Component of the Game Engine
Physics engine design and implementation Physics Engine • A component of the game engine. • Separates reusable features and specific game logic. • basically software components (physics, graphics, input, network, etc.) • Handles the simulation of the world • physical behavior, collisions, terrain changes, ragdoll and active characters, explosions, object breaking and destruction, liquids and soft bodies, ... Game Physics 2 Physics engine • Example SDKs: – Open Source • Bullet, Open Dynamics Engine (ODE), Tokamak, Newton Game Dynamics, PhysBam, Box2D – Closed source • Havok Physics • Nvidia PhysX PhysX (Mafia II) ODE (Call of Juarez) Havok (Diablo 3) Game Physics 3 Case study: Bullet • Bullet Physics Library is an open source game physics engine. • http://bulletphysics.org • open source under ZLib license. • Provides collision detection, soft body and rigid body solvers. • Used by many movie and game companies in AAA titles on PC, consoles and mobile devices. • A modular extendible C++ design. • Used for the practical assignment. • User manual and numerous demos (e.g. CCD Physics, Collision and SoftBody Demo). Game Physics 4 Features • Bullet Collision Detection can be used on its own as a separate SDK without Bullet Dynamics • Discrete and continuous collision detection. • Swept collision queries. • Generic convex support (using GJK), capsule, cylinder, cone, sphere, box and non-convex triangle meshes. • Support for dynamic deformation of nonconvex triangle meshes. • Multi-physics Library includes: • Rigid-body dynamics including constraint solvers. • Support for constraint limits and motors. • Soft-body support including cloth and rope. Game Physics 5 Design • The main components are organized as follows Soft Body Dynamics Bullet Multi Threaded Extras: Maya Plugin, Rigid Body Dynamics etc. Collision Detection Linear Math, Memory, Containers Game Physics 6 Overview • High level simulation manager: btDiscreteDynamicsWorld or btSoftRigidDynamicsWorld. -
On the Use of Simulation in Robotics
PERSPECTIVE On the use of simulation in robotics: Opportunities, challenges, and suggestions for moving forward PERSPECTIVE HeeSun Choia, Cindy Crumpb, Christian Duriezc, Asher Elmquistd, Gregory Hagere, David Hanf,1, Frank Hearlg, Jessica Hodginsh, Abhinandan Jaini, Frederick Levej, Chen Lik, Franziska Meierl, Dan Negrutd,2, Ludovic Righettim,n, Alberto Rodriguezo, Jie Tanp, and Jeff Trinkleq Edited by Nabil Simaan, Vanderbilt University, Nashville, TN, and accepted by Editorial Board Member John A. Rogers September 30, 2020 (received for review November 16, 2019) The last five years marked a surge in interest for and use of smart robots, which operate in dynamic and unstructured environments and might interact with humans. We posit that well-validated computer simulation can provide a virtual proving ground that in many cases is instrumental in understanding safely, faster, at lower costs, and more thoroughly how the robots of the future should be designed and controlled for safe operation and improved performance. Against this backdrop, we discuss how simulation can help in robotics, barriers that currently prevent its broad adoption, and potential steps that can eliminate some of these barriers. The points and recommendations made concern the following simulation-in-robotics aspects: simulation of the dynamics of the robot; simulation of the virtual world; simulation of the sensing of this virtual world; simulation of the interaction between the human and the robot; and, in less depth, simulation of the communication between robots. This Perspectives contribution summarizes the points of view that coalesced during a 2018 National Science Foundation/Department of Defense/National Institute for Standards and Technology workshop dedicated to the topic at hand. -
(Eg Phd, Mphil, Dclinpsychol) at Th
This thesis has been submitted in fulfilment of the requirements for a postgraduate degree (e.g. PhD, MPhil, DClinPsychol) at the University of Edinburgh. Please note the following terms and conditions of use: This work is protected by copyright and other intellectual property rights, which are retained by the thesis author, unless otherwise stated. A copy can be downloaded for personal non-commercial research or study, without prior permission or charge. This thesis cannot be reproduced or quoted extensively from without first obtaining permission in writing from the author. The content must not be changed in any way or sold commercially in any format or medium without the formal permission of the author. When referring to this work, full bibliographic details including the author, title, awarding institution and date of the thesis must be given. A NUMERICAL MODELLING TOOL FOR MULTIBODY WAVE ENERGY CONVERTERS Engineering Doctorate (EngD) Thesis David OGDEN Innosea Ltd. ii Declaration I confirm that this thesis, presented for the degree of Engineering Doctorate, has: i. Been composed entirely by myself ii. Been solely the result of my own work except where explicitly stated otherwise by reference or acknowledgment iii. Not been submitted for any other degree or professional qualification ................... David Ogden Date: . iii iv Abstract Numerical models of wave energy converters (WECs) have been successfully used since the 1970s to understand a device’s characteristics and improve its performance before advancing to costlier, higher-risk stages of development such as tank testing and sea trials. In the last decade several software packages have become available to the industry specifically for time-domain multibody WEC modelling using potential flow theory. -
Numerical Methods for Large Scale Non-Smooth Multibody Problems
Politecnico di Milano 6/11/2014 Numerical Methods for Large Scale Non-Smooth Multibody Problems Ing. Alessandro Tasora Dipartimento di Ingegneria Industriale Università di Parma, Italy [email protected] http://ied.unipr.it/tasora Numerical Methods for Large-Scale Multibody Problems Politecnico di Milano, November 2014 A.Tasora, Dipartimento di Ingegneria Industriale, Università di Parma, Italy slide n. 2 Let us go on and win glory for ourselves, or yield it to others Homer, Iliad ΑΧΙΛΛΕΥΣ 1 Numerical Methods for Large-Scale Multibody Problems Politecnico di Milano, November 2014 A.Tasora, Dipartimento di Ingegneria Industriale, Università di Parma, Italy slide n. 3 Multibody simulation today MultibodyOutlook simulation tomorrow THE COMPLEXITY CHALLENGE Numerical Methods for Large-Scale Multibody Problems Politecnico di Milano, November 2014 A.Tasora, Dipartimento di Ingegneria Industriale, Università di Parma, Italy slide n. 4 Background Joint work in the multibody field with - M.Anitescu (ARGONNE National Labs, Chicago University) - D.Negrut & al. (University of Wisconsin – Madison) - J.Kleinert & al. (Fraunhofer ITWM, Germany) - F.Pulvirenti & al. (Ferrari Auto, Italy) - NVidia Corporation (USA) - A.Jain (NASA – JPL) - S.Negrini & al. (Politecnico di Milano, Italy) - ENSAM Labs (France) - Realsoft OY (Finland) - Cineca supercomputing (Italy) 2 Numerical Methods for Large-Scale Multibody Problems Politecnico di Milano, November 2014 A.Tasora, Dipartimento di Ingegneria Industriale, Università di Parma, Italy slide n. 5 Structure of this lecture Sections • Concepts and applications • Coordinate transformations • Dynamics: a theoretical background • A typical direct solver for classical MB problems • Iterative method for nonsmooth dynamics • Software implementation • C++ implementation of the HyperOCTANT solver in Chrono::Engine • Examples • Future challenges Numerical Methods for Large-Scale Multibody Problems Politecnico di Milano, November 2014 A.Tasora, Dipartimento di Ingegneria Industriale, Università di Parma, Italy slide n. -
Systematic Literature Review of Realistic Simulators Applied in Educational Robotics Context
sensors Systematic Review Systematic Literature Review of Realistic Simulators Applied in Educational Robotics Context Caio Camargo 1, José Gonçalves 1,2,3 , Miguel Á. Conde 4,* , Francisco J. Rodríguez-Sedano 4, Paulo Costa 3,5 and Francisco J. García-Peñalvo 6 1 Instituto Politécnico de Bragança, 5300-253 Bragança, Portugal; [email protected] (C.C.); [email protected] (J.G.) 2 CeDRI—Research Centre in Digitalization and Intelligent Robotics, 5300-253 Bragança, Portugal 3 INESC TEC—Institute for Systems and Computer Engineering, 4200-465 Porto, Portugal; [email protected] 4 Robotics Group, Engineering School, University of León, Campus de Vegazana s/n, 24071 León, Spain; [email protected] 5 Universidade do Porto, 4200-465 Porto, Portugal 6 GRIAL Research Group, Computer Science Department, University of Salamanca, 37008 Salamanca, Spain; [email protected] * Correspondence: [email protected] Abstract: This paper presents a systematic literature review (SLR) about realistic simulators that can be applied in an educational robotics context. These simulators must include the simulation of actuators and sensors, the ability to simulate robots and their environment. During this systematic review of the literature, 559 articles were extracted from six different databases using the Population, Intervention, Comparison, Outcomes, Context (PICOC) method. After the selection process, 50 selected articles were included in this review. Several simulators were found and their features were also Citation: Camargo, C.; Gonçalves, J.; analyzed. As a result of this process, four realistic simulators were applied in the review’s referred Conde, M.Á.; Rodríguez-Sedano, F.J.; context for two main reasons. The first reason is that these simulators have high fidelity in the robots’ Costa, P.; García-Peñalvo, F.J. -
Initial Steps for the Coupling of Javascript Physics Engines with X3DOM
Workshop on Virtual Reality Interaction and Physical Simulation VRIPHYS (2013) J. Bender, J. Dequidt, C. Duriez, and G. Zachmann (Editors) Initial Steps for the Coupling of JavaScript Physics Engines with X3DOM L. Huber1 1Fraunhofer IGD, Germany Abstract During the past years, first physics engines based on JavaScript have been developed for web applications. These are capable of displaying virtual scenes much more realistically. Thus, new application areas can be opened up, particularly with regard to the coupling of X3DOM-based 3D models. The advantage is that web-based applica- tions are easily accessible to all users. Furthermore, such engines allow popularizing and presenting simulation results without having to compile large simulation software. This paper provides an overview and a comparison of existing JavaScript physics engines. It also introduces a guideline for the derivation of a physical model based on a 3D model in X3DOM. The aim of using JavaScript physics engines is not only to virtually visualize designed products but to simulate them as well. The user is able to check and test an individual product virtually and interactively in a browser according to physically correct behavior regarding gravity, friction or collision. It can be used for verification in the design phase or web-based training purposes. Categories and Subject Descriptors (according to ACM CCS): I.3.5 [Computer Graphics]: Computational Geometry and Object Modeling—Physically based modeling I.3.7 [Computer Graphics]: Three-Dimensional Graphics and Realism—Virtual reality I.6.4 [Computer Graphics]: Model Validation and Analysis— 1. Introduction of water or particle systems, e.g. the visualization of gas dis- persion, are to be described. -
Physics-Based Simula1on
Physics-based Simula1on • simple (independent par1cles), or complex (robust colliding, stacking, sliding 3D rigid bodies) • many many simulators! – PhysX (Unity, Unreal), Bullet, Open Dynamics Engine, MuJoCo, Havok, Box2D, Chipmunk, OpenSim, RBDL, Simulink (MATLAB), ADAMS, SD/FAST, DART, Vortex, SOFA, Avatar, Project Chrono, Cannon.js, … – many course projects, theses, abandon-ware Resources • hUps://processing.org/examples/ see “Simulate”; 2D par1cle systems • Non-convex rigid bodies with stacking 3D collision processing and stacking hUp://www.cs.ubc.ca/~rbridson/docs/rigid_bodies.pdf • Physically-based Modeling, course notes, SIGGRAPH 2001, Baraff & Witkin hUp://www.pixar.com/companyinfo/research/pbm2001/ • Doug James CS 5643 course notes hUp://www.cs.cornell.edu/courses/cs5643/2015sp/ • Rigid Body Dynamics, Chris Hecker hUp://chrishecker.com/Rigid_Body_Dynamics • Video game physics tutorial hUps://www.toptal.com/game/video-game-physics-part-i-an-introduc1on-to-rigid-body-dynamics • Box2D javascript live demos hUp://heikobehrens.net/misc/box2d.js/examples/ • Rigid body collisions javascript demo hUps://www.myphysicslab.com/engine2D/collision-en.html • Rigid Body Collision Reponse, Michael Manzke, course slides hUps://www.scss.tcd.ie/Michael.Manzke/CS7057/cs7057-1516-09-CollisionResponse-mm.pdf • Rigid Body Dynamics Algorithms. Roy Featherstone, 2008 • Par1cle-based Fluid Simula1on for Interac1ve Applica1ons, SCA 2003, PDF • Stable Fluids, Jos Stam, SIGGRAPH 1999. interac1ve demo: hUps://29a.ch/2012/12/16/webgl-fluid-simula1on Simula1on