Phase Evolution of Conversion-Type Electrode for Lithium Ion Batteries
Total Page:16
File Type:pdf, Size:1020Kb
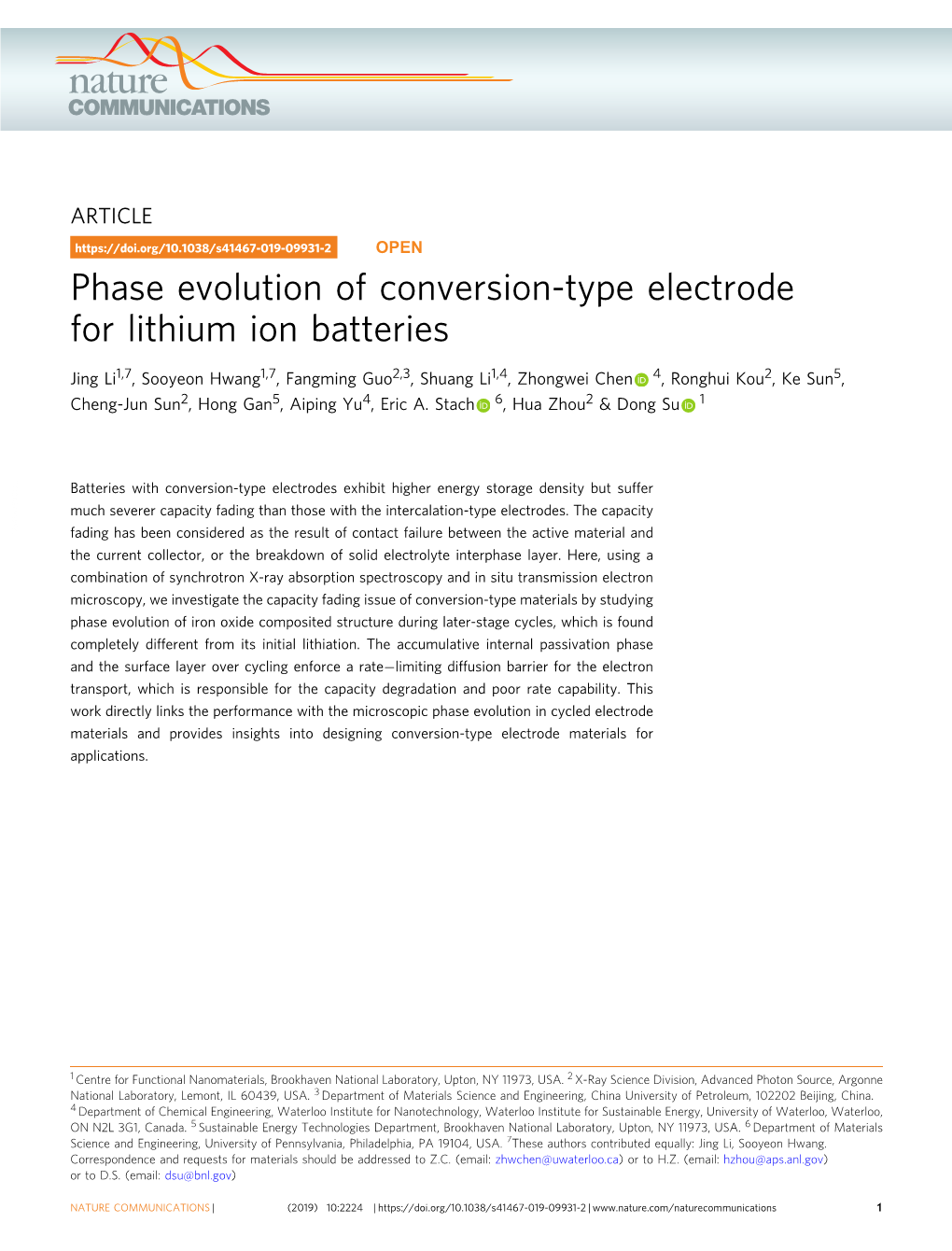
Load more
Recommended publications
-
Material - Safety - Data Sheet (MSDS) No.16 for Ansmann Zinc Carbon (Mercury Free Heavy Duty) Batteries Single Cells and Multi-Cell Battery Packs 1/6
Material - Safety - Data Sheet (MSDS) No.16 for Ansmann Zinc Carbon (Mercury Free Heavy Duty) Batteries single cells and multi-cell battery packs 1/6 Date of issue: 2015 - 02 - 23 The information contained within is provided as a service to our customers and Revision no: 1 for their information only. The information and recommendations set forth herein Revision date: 2016 - 10 - 07 are made in good faith and are believed to be accurate at the date of preparation. Editor: Ansmann AG ANSMANN AG makes no warranty expressed or implied. 1. Product and Supplier Identification Product name: ANSMANN (Super) Heavy Duty Battery Designation: Zinc Manganese Dioxide Battery Models / types: R3 (AAA); R6 (AA); R14 (C); R20 (D); 6F22 (9V E-Block); 3R12; 4R25 Electrochemical system: MnO2 (Manganese Dioxide) (positive electrode) Zn (negative electrode) NH4Cl, ZnCl2 (electrolyte) Supplier: Germany ANSMANN AG Address: Industriestraße 10; 97959 Assamstadt; Germany Phone / Fax: + 49 (0) 6294 42040 / + 49 (0) 6294 420444 Home / email: ansmann.de / [email protected] USA ANSMANN USA Corporation Address: 1001 Lower Landing Rd. Ste 101; Blackwood, NJ08012; USA Phone / Facsimile: +1 973 4395244 1012 / +1 973 2062006 email: [email protected] United Kingdom ANSMANN UK LTD. Address: Units 11-12, RO24, Harlow Business Park, Harlow, Essex. CM19 5QB. UK Phone / Facsimile: +44 (0) 870 609 2233 / +44 (0) 870609 2234 email: [email protected] Hong Kong ANSMANN Energy Int. LTD. Address: Unit 3117-18, 31/F; Tower 1; Millenium City 1; No. 388 Kwun Tong Road; Kwun Tong, kowloon; Hong-Kong -
PSDS Zinc Air Batteries MF
Primary Zinc-Air-Battery: Button Type Hearing Aid Batteries Product Safety Data Sheet This "Safety information" is provide as a service to our customers Disclaimer: (EU) These batteries are no "substances" nor "preparations"according to Regulation (EC) No 1907/2006 EC. Instead they have to be regarded as "articles", no substances are intended to be released during handling. Therefore there is no obligation to supply a MSDS according to Regulation (EC) 190'7/2006, Article 31. This PSDS is intended to be unsolicited information without any further legal commitment. The details presented are in accordance with our present knowledge and experiences. They are no contractual assurances of product attributes. (U.S.A.) Material Safety Data Sheets (MSDS) are a sub-requirement of the Occupational Safety and Health Administration (OSHA) Hazard Communication Standard, 29 CFR Subpart 1910.1200. This Hazard Communication Standard does not apply to various subcategories including anything defined by OSHA as an "article". OSHA has defined "article" as a manufactured item other than a fluid or particle; (i) which is formed to a specific shape or design during manufacture; ii) which has end use function(s) dependent in whole or in part upon its shape or design during end use; and (iii) which under normal conditions of use does not release more than very small quantities, e.g. minute or trace amounts of a hazardous chemical, and does not pose a physical hazard or health risk to employees. This sheet is provided as technical information only. The information contained in this Product Safety Data Sheet has been established to the best of RENATA SA's knowledge and belief. -
A Review of Cathode and Anode Materials for Lithium-Ion Batteries
A Review of Cathode and Anode Materials for Lithium-Ion Batteries Yemeserach Mekonnen Aditya Sundararajan Arif I. Sarwat IEEE Student Member IEEE Student Member IEEE Member Department of Electrical & Department of Electrical & Department of Electrical & Computer Engineering Computer Engineering Computer Engineering Florida International University Florida International University Florida International University Email: [email protected] Email: [email protected] Email: [email protected] Abstract—Lithium ion batteries are one of the most technologies such as plug-in HEVs. For greater application use, commercially sought after energy storages today. Their batteries are usually expensive and heavy. Li-ion and Li- based application widely spans from Electric Vehicle (EV) to portable batteries show promising advantages in creating smaller, devices. Their lightness and high energy density makes them lighter and cheaper battery storage for such high-end commercially viable. More research is being conducted to better applications [18]. As a result, these batteries are widely used in select the materials for the anode and cathode parts of Lithium (Li) ion cell. This paper presents a comprehensive review of the common consumer electronics and account for higher sale existing and potential developments in the materials used for the worldwide [2]. Lithium, as the most electropositive element making of the best cathodes, anodes and electrolytes for the Li- and the lightest metal, is a unique element for the design of ion batteries such that maximum efficiency can be tapped. higher density energy storage systems. The discovery of Observed challenges in selecting the right set of materials is also different inorganic compounds that react with alkali metals in a described in detail. -
Coal As Value-Added for Lithium Battery Anodes
Coal as Value-Added for Lithium Battery Anodes Project Review Award No. DE-FE0031879 November 6th 2020 1 Project Summary • Semplastics has begun development of a novel material based on our X-MAT® polymer-derived ceramic (PDC) technology for use as an anode material in lithium-ion batteries • The X-MAT anode material is a composite of chemically tailored silicon oxycarbide (SiOC) and domestically sourced coal powder, designed to be a drop- in replacement for graphite within lithium-ion batteries • Preliminary tests of this material have shown more than twice the reversible capacity of graphite anodes • Through this project, Semplastics proposes to complete development and begin commercialization of this material 2 Project Description and Objectives 3 What are X-MAT Coal-Core Composite Powders? • Raw coal powder mixed with our proprietary polymer derived ceramic (PDC)-forming resin to produce coal-core composite powder materials – Electrically conductive – Low cost – Coal is 1-5¢/lb – The raw coal will not be burned during materials processing, and the resulting powder composite will not burn – Easily manufactured compared to typical ceramics – no sintering needed – Capable of using a variety of coals including lignite, bituminous, and anthracite particles in an “as-is” state with our proprietary PDC technology 4 How is this different from other approaches? • Our PDCs can be tuned at the Atomic Level to contain varying amounts of silicon, oxygen and carbon • Uses a “green” low-energy method – does not involve high-energy processes including -
Batteries Information Received from EU, Canada, Japan, Indonesia, USA and Other Stakeholders (BAJ, IPEN, NRDC, ZMWG)
Batteries Information received from EU, Canada, Japan, Indonesia, USA and other stakeholders (BAJ, IPEN, NRDC, ZMWG) 1. Category of mercury-added product Batteries 2. Further description of the product Mercury-containing button cells 3. Information on the use of the Currently, there are three types of button cell batteries that contain mercury: zinc air, silver oxide and alkaline. product These batteries contain mercury in small amounts (typically 0.1-2%) and the purpose of mercury in the cell is to prevent the build-up of hydrogen gas. The mercury acts as a barrier to the production of hydrogen and as such prevents the cell swelling and becoming damaged. Figure 1 – Cross Section of Zinc Anode Button Cell and Zinc Air Button Cell (European Commission, 2014) Range of mercury content/consumption per unit product - 0.1 – 2 weight-% (button cells with intentionally added mercury) - 0.0005 weight-% (button cells without intentionally added mercury) Button batteries are used for powering high drain devices such as watches, calculators, and hearing aids. 4. Information on the availability of EU mercury-free (or less-mercury) Main alternatives: Mercury-free zinc air batteries alternatives Mercury free versions are commercially available for all applications of the main types of button cells (lithium, silver, oxide, alkaline and zinc air). The most frequently used types make use of zinc air technology (European Commission, 2014). Since October 2015, mercury-containing button cell batteries have been prohibited in the EU following the expiry of the exemption granted under the Batteries Directive. 1 Canada Alternatives: mercury-free silver oxide batteries, mercury-free zinc air batteries, lithium batteries Mercury-free alternatives have been available from major battery manufacturers since the late 1990s and early 2000s (e.g. -
Lithium Batteries
LITHIUM BATTERIES 1. Introduction Over the past 20 years, lithium battery technology has dramatically evolved, providing increasingly greater energy density, greater energy per volume, longer cycle life and improved reliability. Lithium is the lightest of all metals, has the greatest electrochemical potential and provides the largest specific energy per weight. Lithium batteries are now powering a wide range of electrical and electronical devices, including laptop computers, mobile phones, power tools, telecommunication systems and new generations of electric cars and vehicles. Next to advantages, new technologies often bring new challenges and risks. Reports on incidents with lithium batteries catching fire have made the public well aware of their flammability hazard and have triggered massive research on the mechanisms initiating such events and the ways to make operation, storage, transportation and recycling safer. This document covers some of the safety related issues of lithium batteries. 2. Types of Lithium Batteries 2.1 Cell or Battery? Although the word "battery" is a common term to describe an electrochemical storage system, international industry standards differentiate between a "cell" and a "battery". A cell is a single encased electrochemical unit (one positive and one negative electrode) with a voltage differential across its two terminals (Figure 1). Figure 1: Examples of cells A battery is two or more cells that are electrically connected together and fitted with devices such as a case, terminals, marking and protective devices that it needs to function properly (Figure 2). EHS-DOC-147 v.2 1 / 18 Figure 2: Examples of batteries However, in common usage, the terms "cell" and "battery" are used interchangeably. -
Characterization of Spent Household Zinc-Carbon Dry Cell Batteries in the Process of Recovery of Value Metals
Journal of Minerals & Materials Characterization & Engineering, Vol. 11, No.6, pp.641-651, 2012 jmmce.org Printed in the USA. All rights reserved Characterization of Spent Household Zinc-Carbon Dry Cell Batteries in the Process of Recovery of Value Metals Majharul Haque Khan and A.S.W Kurny* Materials and Metallurgical Engineering Department, Bangladesh University of Engineering and Technology, Dhaka, Bangladesh *Corresponding author: [email protected] ABSTRACT Spent zinc-carbon dry cell batteries were characterized to assess the environmental impacts and also, to identify the potentials of recovering the metal values from these batteries. Different component parts of both new and spent batteries of all the five types (AAA, AA, C, D and 9V) were examined. The outer steel casings were found to be tin plated. Steel, zinc and manganese constituted 63 percent of the total weight of the battery. Average zinc and manganese contents were about 22 and 24 percent of the total weight of spent batteries. The electrolyte paste of the spent batteries contained 22 wt. percent zinc and 60 wt. percent manganese. The rest was chlorine, carbon and small amounts of iron and other impurity elements. The major phases in the fresh batteries were carbon, MnO2 and NH4Cl, while Zn(NH3)2Cl2, ZnO.Mn2O3, Mn3O4 and Mn2O3 were the prominent phases in the spent batteries. Presence of mercury and cadmium were not detected and a small percentage of lead was found in both the zinc anode and in the electrolyte paste. Keywords: Zinc-carbon battery, Characterization, Spent batteries, Waste management 1. INTRODUCTION Zinc-carbon dry cell batteries are widely used in different household applications like toys, radios, recorders, watches, remote controls, cameras, torches etc. -
Higher Power Lithium Batteries
MIL -EMBEDDED .COM MilitaryLIDAR clears up helo landing brownouts VOLUME 4 NUMBER 4 EMBEDDED SYSTEMS JUNE 2 008 Is COTS in for a rough landing? Industry execs speak out on tech, trends, future Hardware: Portable power High-power lithium batteries: Providing more performance, life, and reliability By Sol Jacobs Batteries capable of delivering high-rate power to long-life single-use military applications have remained virtually unchanged for decades. Now, a new generation of high-power lithium batteries is available that offers unique performance and features, including higher capacity and energy density, reliability, instantaneous activation, and the COTS advantage. Driven largely by advancements in em- power, long-life batteries capable of to power long-term single-use military bedded computers and semiconductor providing reliable power for single-use applications; however, high-power lithium fabrication, long-life single-use military/ military applications as a “critical problem” batteries are now an option to consider, too: aerospace systems are rapidly evolving, to address. with new generation products offering Reserve and thermal batteries improved functionality, miniaturization, The search for solutions led to the develop- Silver-zinc batteries and enhanced product reliability, as well ment of new COTS high-power lithium Spin-activated batteries as higher performance expectations. This battery technology featuring exceptionally High-power lithium batteries applies to a wide variety of single-use long shelf life combined with powerful military products, including mortar-guidance performance capabilities previously available A brief review of these competing technologies systems, rockets, missiles, torpedoes, mines, only with reserve or thermal batteries. Design highlights the potential advantages and sonobuoys, unattended ground sensors, engineers are advised to perform appropriate disadvantages of each battery chemistry. -
Relating Catalysis Between Fuel Cell and Metal-Air Batteries
Perspective Relating Catalysis between Fuel Cell and Metal-Air Batteries Matthew Li,1,2 Xuanxuan Bi,1 Rongyue Wang,3 Yingbo Li,4,6 Gaopeng Jiang,2 Liang Li,5 Cheng Zhong,6,* Zhongwei Chen,2,* and Jun Lu1,* With the ever-increasing demand for higher-performing energy-storage sys- Progress and Potential tems, electrocatalysis has become a major topic of interest in an attempt to Catalyst research for fuel cells has enhance the electrochemical performance of many electrochemical technolo- led to much advancement in gies. Discoveries pertaining to the oxygen reduction reaction catalyst helped humanity’s understanding of the enable the commercialization of fuel-cell-based electric vehicles. However, a underlying physics of the process, closely related technology, the metal-air battery, has yet to find commercial significantly enhancing the application. Much like the Li-ion battery, metal-air batteries can potentially uti- performance of the technologies. lize the electrical grid network for charging, bypassing the need for establishing In contrast, metal-air batteries a hydrogen infrastructure. Among the metal-air batteries, Li-air and Zn-air bat- such as Li-air and Zn-air batteries teries have drawn much interest in the past decade. Unfortunately, state-of-the remain to be solved. Although the art metal-air batteries still produce performances that are well below practical metal anode used in this these levels. In this brief perspective, we hope to bridge some of the ideas from systems does play a large role in fuel cell to that of metal-air batteries with the aim of inspiring new ideas and di- limiting their commercial success, rections for future research. -
Effective Battery Energy Capacity As a Function of Temperature and Discharge Current
Effective Battery Energy Capacity as a Function of Temperature and Discharge Current Michael Ruscito, Mingshi Yang, Tomas Pavydis, Jinghan Huang University of Illinois at Urbana-Champaign PHYS 398DLP, Professor George Gollin 1 May 2020 Abstract The goal of this project is to analyze the effects of variable environmental temperatures and discharge currents on the effective energy capacity of common batteries. AAA batteries with different chemical compositions were considered including: alkaline, nickel-metal hydride, primary lithium, and lithium ion. Additionally, lithium coin cell batteries were tested to compare the results of different form factors. In theory, the chemical reactions and electrical processes within the batteries are optimized to perform at specific temperatures and current draws. These specifications are commonly provided by the manufacturer and give information on the “ideal” conditions for use. Operating outside of these optimal specifications could demonstrate a noticeable effect on battery life expectancy, and more specifically, lower the effective energy capacity. This project’s approach to measure these effects consisted of collecting information on battery voltages under specific temperatures and discharge currents. The results demonstrated that battery behavior is altered by these conditions. I Introduction Nearly all common electronics rely on battery power in order to run and the lifespan of these devices often seems strongly correlated with the temperature around them. For example, a phone battery may appear to drain much quicker during the winter or in colder environments and electric cars seem to lose a noticeable amount of range after being left out in the cold overnight. To combat this, Tesla car batteries will even drain some of their energy in order to heat themselves preventing damage to the energy cells. -