Cryocoolers Part 1: Fundamentals the INTERNATIONAL CRYOGENICS MONOGRAPH SERIES
Total Page:16
File Type:pdf, Size:1020Kb
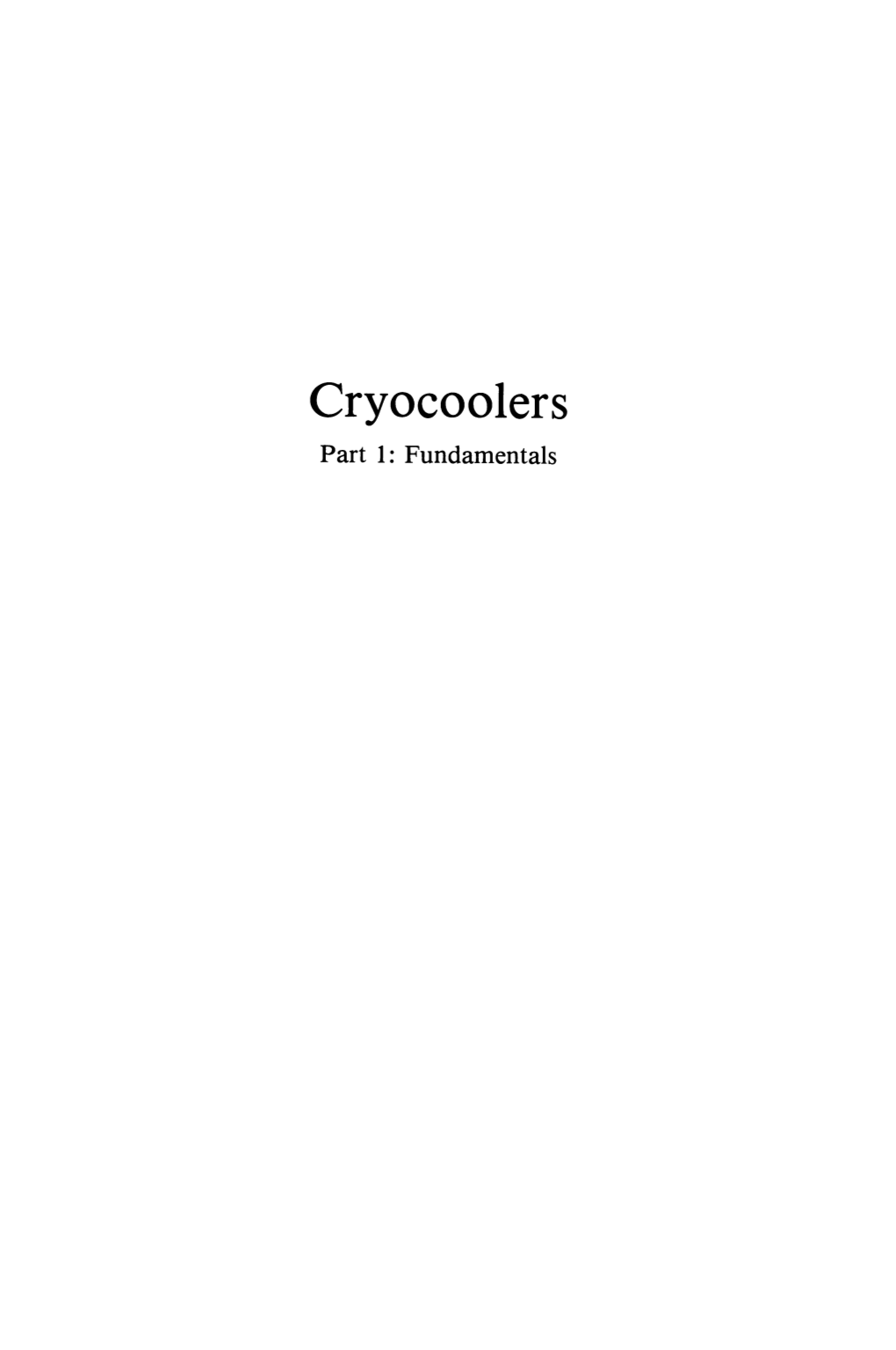
Load more
Recommended publications
-
Stirling Refrigerator
Stirling Refrigerator Mid-Point Report Luis Gardetto Ahmad Althomali Abdulrahman Alazemi Faiez Alazmi John Wiley 2017-2018 Project Sponsor: Dr. David Trevas Faculty Advisor: Mr. David Willy Instructor: Dr. Sarah Oman DISCLAIMER This report was prepared by students as part of a university course requirement. While considerable effort has been put into the project, it is not the work of licensed engineers and has not undergone the extensive verification that is common in the profession. The information, data, conclusions, and content of this report should not be relied on or utilized without thorough, independent testing and verification. University faculty members may have been associated with this project as advisors, sponsors, or course instructors, but as such they are not responsible for the accuracy of results or conclusions. i Executive Summary Refrigeration is a ubiquitous application of engineering concepts, with implications like food preservation techniques, superconducting-magnet involving techniques and crystal harvesting techniques. The refrigeration process involves the removal of excess heat from specified objects, thereby enhancing the cooling or the chilling effect. Refrigerators come in many sizes and shapes, according to the available expertise, materials, and applications. With the advancement of technology and the emergence of various contemporary issues such as cost, size, and dangerous chemicals among others, researchers are embarking on studies, which can facilitate the design and development of a more efficient refrigerator, capable of performing the desired work as presupposed with minimal problems. The current proposal focuses on Stirling cryocoolers, which have been recognized as one of the most efficient coolers of the current era. The key advantages of these chillers include low power consumption rates as well as the use of non-hazardous refrigerants. -
Thermodynamic Analysis of a Waste Heat Driven Vuilleumier Cycle Heat Pump
Entropy 2015, 17, 1452-1465; doi:10.3390/e17031452 OPEN ACCESS entropy ISSN 1099-4300 www.mdpi.com/journal/entropy Article Thermodynamic Analysis of a Waste Heat Driven Vuilleumier Cycle Heat Pump Yingbai Xie * and Xuejie Sun Department of Power Engineering, North China Electric Power University, Baoding 07100, China; E-Mail: [email protected] * Author to whom correspondence should be addressed; E-Mail: [email protected]; Tel.: +86-312-752-2706; Fax: +86-312-752-2440. Academic Editor: Marc A. Rosen Received: 29 January 2015 / Accepted: 17 March 2015 / Published: 20 March 2015 Abstract: A Vuilleumier (VM) cycle heat pump is a closed gas cycle driven by heat energy. It has the highest performance among all known heat driven technologies. In this paper, two thermodynamic analyses, including energy and exergy analysis, are carried out to evaluate the application of a VM cycle heat pump for waste heat utilization. For a prototype VM cycle heat pump, equations for theoretical and actual cycles are established. Under the given conditions, the exergy efficiency for the theoretical cycle is 0.23 compared to 0.15 for the actual cycle. This is due to losses taking place in the actual cycle. Reheat losses and flow friction losses account for almost 83% of the total losses. Investigation of the effect of heat source temperature, cycle pressure and speed on the exergy efficiency indicate that the low temperature waste heat is a suitable heat source for a VM cycle heat pump. The selected cycle pressure should be higher than 100 MPa, and 200–300 rpm is the optimum speed. -
Performance Evaluation of the Thermolift Natural Gas Fired Air Conditioner and Cold-Climate Heat Pump
NOTICE: This document contains information of a preliminary nature and is not intended for release. It is subject to revision or correction and therefore does not represent a final report. ORNL/LTR-2019/1288 Performance Evaluation of the ThermoLift Natural Gas Fired Air Conditioner and Cold-Climate Heat Pump Peter Hofbauer Paul Schwartz Vishaldeep Sharma Approved for public release. Distribution is unlimited September 2019 DOCUMENT AVAILABILITY Reports produced after January 1, 1996, are generally available free via US Department of Energy (DOE) SciTech Connect. Website www.osti.gov Reports produced before January 1, 1996, may be purchased by members of the public from the following source: National Technical Information Service 5285 Port Royal Road Springfield, VA 22161 Telephone 703-605-6000 (1-800-553-6847) TDD 703-487-4639 Fax 703-605-6900 E-mail [email protected] Website http://classic.ntis.gov/ Reports are available to DOE employees, DOE contractors, Energy Technology Data Exchange representatives, and International Nuclear Information System representatives from the following source: Office of Scientific and Technical Information PO Box 62 Oak Ridge, TN 37831 Telephone 865-576-8401 Fax 865-576-5728 E-mail [email protected] Website http://www.osti.gov/contact.html This report was prepared as an account of work sponsored by an agency of the United States Government. Neither the United States Government nor any agency thereof, nor any of their employees, makes any warranty, express or implied, or assumes any legal liability or responsibility for the accuracy, completeness, or usefulness of any information, apparatus, product, or process disclosed, or represents that its use would not infringe privately owned rights. -
1998 Report of the RTOC
MONTREAL PROTOCOL ON SUBSTANCES THAT DEPLETE THE OZONE LAYER UNEP 1998 REPORT OF THE REFRIGERATION, AIR CONDITIONING AND HEAT PUMPS TECHNICAL OPTIONS COMMITTEE 1998 Assessment UNEP 1998 REPORT OF THE REFRIGERATION, AIR CONDITIONING AND HEAT PUMPS TECHNICAL OPTIONS COMMITTEE 1998 ASSESSMENT 1998 TOC Refrigeration, A/C and Heat Pumps Assessment Report 1 Montreal Protocol On Substances that Deplete the Ozone Layer UNEP 1998 REPORT OF THE REFRIGERATION, AIR CONDITIONING AND HEAT PUMPS TECHNICAL OPTIONS COMMITTEE 1998 ASSESSMENT The text of this report is composed in Times New Roman. Co-ordination: Refrigeration, Air Conditioning and Heat Pumps Technical Options Committee Composition: Lambert Kuijpers (Co-chair) Layout: Dawn Lindon Reproduction: UNEP Nairobi, Ozone Secretariat Date: October 1998 No copyright involved Printed in Kenya; 1998. ISBN 92-807-1731-6 2 1998 TOC Refrigeration, A/C and Heat Pumps Assessment Report UNEP 1998 REPORT OF THE REFRIGERATION, AIR CONDITIONING AND HEAT PUMPS TECHNICAL OPTIONS COMMITTEE 1998 ASSESSMENT 1998 TOC Refrigeration, A/C and Heat Pumps Assessment Report 3 DISCLAIMER The United Nations Environment Programme (UNEP), the Technology and Economic Assessment Panel (TEAP) co-chairs and members, the Technical and Economic Options Committee, chairs, co-chairs and members, the TEAP Task Forces co-chairs and members, and the companies and organisations that employ them do not endorse the performance, worker safety, or environmental acceptability of any of the technical options discussed. Every industrial operation requires consideration of worker safety and proper disposal of contaminants and waste products. Moreover, as work continues - including additional toxicity evaluation - more information on health, environmental and safety effects of alternatives and replacements will become available for use in selecting among the options discussed in this document. -
Progress of Pulse Tube Cryocooler
Superconductivity and Cryogenics Vol.12, No.4, (2010), pp.1~7 Progress of Pulse Tube Cryocooler Yoichi Matsubara1,* and Deuk-Yong Koh2 1Former Professor of Nihon University, 763 Kotto Chikura minamiboso Chiba 295-0022, Japan 2KIMM, 171 Jang-dong Yuseong-ku Daejeon 305-343, Korea Received 7 September 2010; accepted 15 October 2010 ``` Abstract-- The pulse tube cooler as an alternative of of future development of the cooling system for each Stirling, G-M or VM cooler to overcome the requirement application fields. from the various application fields is described. The necessity of the object oriented cooler development is explained to realize the cryocooler of more energy-efficient, more reliable, 2. CLASSIFICATION OF PTC more compact and less expensive than what is currently available commercially. 2.1. Critical components of PTC Most characteristic merit of the pulse tube cooler is that it 1. INTRODUCTION has no mechanical moving components at the cold part of the cooling device without the sacrifice of thermodynamic Cryogenic technology, including cryocoolers, is a efficiency. From the view point of thermodynamic aspect, crucial supporting technology for superconductor pulse tube cooler will be divided into five critical applications, without exception. In general, if the existing components. room temperature technology is replaced with the Fig. 1 shows the basic arrangement of each component; superconducting technology, the extra work required for pressure wave generator, regenerator, pulse tube, heat the cooling system becomes a sort of penalty. Therefore the exchanger and the work receiver section. The simplest development of efficient cryocooler becomes essential configuration of the pressure wave generator will be issue. -
Mathematical and Optimization Analysis of a Miniature Stirling Cryocooler
View metadata, citation and similar papers at core.ac.uk brought to you by CORE provided by ethesis@nitr MATHEMATICAL AND OPTIMIZATION ANALYSIS OF A MINIATURE STIRLING CRYOCOOLER Thesis submitted in partial fulfillment of the requirements for the degree of Bachelor of Technology (B. Tech) In Mechanical Engineering By Yatin Chhabra (107ME025) Devaraj. V (107ME015) Under the guidance of Prof. R.K. Sahoo NATIONAL INSTITUTE OF TECHNOLOGY ROURKELA Page | i Certificate of Approval This is to certify that the thesis entitled Mathematical and Optimization Analysis of a Miniature Stirling Cryo-cooler submitted by Mr. Yatin Chhabra and Mr. Devaraj. V has been carried out under my supervision in partial fulfillment of the requirements for the Degree of Bachelors of Technology (B. Tech) in Mechanical Engineering at National Institute of Technology Rourkela, and this work has not been submitted elsewhere before for any other academic degree/diploma. .................................................. Dr. R. K. Sahoo Professor Department of Mechanical Engineering National Institute of Technology, Rourkela Page | ii Abstract In the given report, a comprehensive analytical model of the working of a miniature Stirling Cyo-cooler is presented. The motivation of the study is to determine the optimum geometrical parameters of a cryo-cooler such as compressor length, regenerator diameter, expander diameter, and expander stroke. In the first part of the study, an ideal analysis is carried out using the Stirling Cycle and basic thermodynamics equations. Using these equations, rough geometrical parameters are found out. In the second part of the study, a more comprehensive Schmidt’s analysis is carried out. In this analysis, pressure and volume variations are considered sinusoidal and based on these, various equations regarding efficiency and COP are derived. -
Review of Research, Development, and Deployment of Gas Heat Pumps in North America
Authors: Paul Glanville, R&D Manager, Gas Technology Institute; Patricia Rowley, Senior Engineer, Gas Technology Institute Session Title: Utilization: Innovations In Residential and Commercial Gas Technologies Title: Review of Research, Development, and Deployment of Gas Heat Pumps in North America Abstract In North America, natural gas is the predominant fuel for providing heat and hot water to residential and commercial buildings. In the U.S., the majority of homes and businesses use natural gas for heating and collectively consume 65 billion therms overall for space heating and hot water, equal to 23% of national natural gas consumption. In Canada, half of homes heat and 65% generate hot water with natural gas and a greater fraction of business, 80%, use natural gas for the same. Additionally, where available, consumer surveys indicate that natural gas is a preferred fuel for thermal comfort over alternatives. Despite its status as the predominant domestic and commercial fuel for heating and service hot water, direct use of natural gas for thermal comfort in North America is declining and may be undergoing a nascent transformation towards the expanded use of gas heat pumps (GHP). GHPs are at a cost premium over conventional, and even high-efficiency gas-fired heating equipment (e.g. furnaces, boilers.) While in many cases GHP products remain at the pre-commercial stage, they are receiving renewed attention due to potentially significant increases in delivered efficiency and the ability to provide seasonal comfort through some combination of heating, cooling, and hot water outputs. Market trends and pressures driving this interest include: (a) GHP technologies that may offer improved reliability, efficiency, financial payback, and end user comfort, (b) regulatory pressures concerning energy efficiency and both criteria and greenhouse gas (GHG) emissions, and (c) other environmental drivers concerning the primary energy budget of residential/commercial buildings, including pursuit of “Zero Net Energy” buildings. -
Nasa Cr-145078 Study of a Vuilleumier Cycle
NASA CR-145078 STUDY OF A VUILLEUMIER CYCLE CRYOGENIC REFRIGERATOR FOR DETECTOR COOLING ON THE LIMB SCANNING INFRARED RADIOMETER by Samuel C. Russo JULY 1976 Prepared under Contract NAS 1-14337 by HUGHES AIRCRAFT CpMPANY x Culver City, California ^^ for National Aeronautics and Space Administration NASA CR-145078 STUDY OF A VUILLEU.MIER CYCLE CRYOGENIC REFRIGERATOR FOR DETECTOR COOLING ON THE LIMB SCANNING. INFRARED RADIOMETER July 1976 Samuel C. Russo Prepared under Contract NAS 1-14337 by ;.! . HUGHES AIRCRAFT COMPANY • ' Culver City, California !„,.'•..•, '• for NASA National Aeronautics and Space Administration IY CONTENTS I INTRODUCTION AND SUMMARY 1 II VM CYCLE THEORY OF OPERATION. 5 in DETERMINATION OF CRYOGENIC COOLING REQUIREMENTS ... 9 IV THERMODYNAMIC DESIGN AND PARAMETRIC PERFORMANCE ANALYSIS 16 Thermodynamic Design Analysis 16 Parametric Performance Analysis 20 Calculations of Transient Performance 29 V CONCEPTUAL MECHANICAL DESIGN 32 Dynamic Balance 32 Description of Refrigerator 35 Interfaces 43 Electronic Interface Unit . 47 VI IMPLEMENTATION PLAN . 53 General Tasks 54 Test Plans 55 Schedule 57 VII RELIABILITY AND LIFE STUDIES 58 VIII CONCLUSIONS 61 APPENDIX A DESIGN SPECIFICATION 63 APPENDIX B INHERENT THERMODYNAMIC AND HEAT TRANSFER LOSSES OF VM REFRIGERATOR 82 APPENDIX C DESCRIPTION OF INPUT COMMANDS 87 EFERENCES.......................................... "M 111 LIST OF ILLUSTRATIONS Figure Page 1 Schematic of basic two-stage VM cryogenic refrigerator 6 2 Indicator diagrams of first- and second-stage expansion volumes 7 3 Indicator diagrams of expansion hot volume and crankcase volume 8 4 Typical small VM cooler (71-7244) .~77TT. 10 5 Thermal loads from detector support 13 6 Effect of ground operation on wear rate of hot rider ring ..... -
Cryocooler Fundamentals and Space Applications
Cryocooler Fundamentals and Space Applications Ray Radebaugh R. G. Ross, Jr. National Institute of Standards and Technology Jet Propulsion Laboratory Boulder, Colorado 80305 California Institute of Technology (303) 497-3710; [email protected] Pasadena, California 91109 [email protected] Sponsored by Short Course Lecturers: Cryogenic Engineering Conference Ray Radebaugh, NIST Tucson, Arizona R. G. Ross, Jr., JPL June 28, 2015 CSA-CEC2015.ppt Cryocooler Fundamentals and Space Applications Contents Morning (8:00 – 12:00): One 15 min. break Session 1: Information sources, definitions, history, applications, thermodynamics, cryocooler types, Joule-Thomson (JT) coolers, Brayton cryocoolers, Claude systems, heat exchangers Session 2: Regenerative cycles, Stirling cryocoolers, Gifford-McMahon (GM) cryocoolers, 4 K regenerators, pulse tube cryocoolers, types, examples, modeling, cryocooler comparisons, new research Afternoon (1:00 – 5:00): One 15 min. break Session 3: Space cryocoolers, history, applications, long life, Stirling coolers, Ron Ross pulse tube coolers, JT systems, Brayton coolers, system design, qualification, vacuum, conduction and radiation thermal loads Session 4: Performance requirements, thermal measurements, orientation, Ron Ross generated vibration and supression, launch vibration, EMI, AIRS example, sizing, temperature stability, integration 6/28/2015 CSA Short Course, Cryocoolers and Space Applications 2 Course Goals • Provide information to a variety of students • Learn about various types of cryocoolers • -
The Research Commercialisation Office of the University of Oxford, Previously Called Isis Innovation, Has Been Renamed Oxford University Innovation
The research commercialisation office of the University of Oxford, previously called Isis Innovation, has been renamed Oxford University Innovation All documents and other materials will be updated accordingly. In the meantime the remaining content of this Isis Innovation document is still valid. URLs beginning www.isis-innovation.com/... are automatically redirected to our new domain, www.innovation.ox.ac.uk/... Phone numbers and email addresses for individual members of staff are unchanged Email : [email protected] Isis insights ARE YOU AWAKE? Ii 2 Issue Summer Anaesthetic and vaccine innovations from Isis’ network, odafone dialling recise p elping SEs for consultancy 18 sensing 26 in Australia The latest innovations, collaborations and technology transfer Issue 76 Summer 2 Anaesthetic vaccine focus Ii Contents Vaccine Catalysing Are you renaissance ollaborations awake? rofessor Adrian ill on ohnson and ohnson easuring consciousness 8 new targets 10 Innovation 12 during anaesthesia Information Invention Inspiration 03: News 12: Are you awake Soware as a serice The latest from Isis Safeguarding surgery A fresh model for sharing academic soware 04. Enterprising Consultancy estational Consultancy for odafone and diabetes management 26: Taking Australian niversity of Iceland spin-out A remote monitoring and innoations to the world communication prototype ow Isis Enterprise is helping SEs . The orolio down under ‘ynamic’ tissue donation 16: Improved ltrasond antication Innovation uantifying organ sie 06: Milton Park 18: Precise pH sensing Oxford Innovation Society OIS arnessing an unbreakable electrode member prole: ilton ark 20: Ultra-high bandwidth 08: Vaccine Renaissance Enabling ‘i-fi’ technology OIS speaker rofessor Adrian ill on vaccine technology for new targets Stirling cycle eoltion A package of atalysing ollaborations complementary innovations A write-up of the key note talk from our arch OIS sponsors ohnson ohnson Innovation Ii is produced by Isis Innovation td, the technology transfer company owned by the niversity of Oxford. -
Experimental Investigation of Displacer Seal Geometry Effects In
energies Article Experimental Investigation of Displacer Seal Geometry Effects in Stirling Cycle Machines Jan Sauer and Hans-Detlev Kühl * TU Dortmund University, Lehrstuhl für Thermodynamik (BCI), Emil-Figge-Straße 70, 44227 Dortmund, Germany; [email protected] * Correspondence: [email protected]; Tel.: +49-231-755-2674 Received: 22 August 2019; Accepted: 30 October 2019; Published: 5 November 2019 Abstract: This contribution deals with an experimental investigation of the optimization potential of Stirling engines and similar regenerative machines by an enhanced design of the cylinder liner and the seal. The latter is mounted at the bottom end of the gap surrounding pistons and displacers that separate cylinder volumes at different temperature levels. The thermal loss associated with this gap may amount to more than 10% of the heat input into these machines. Mostly, its design is reduced to an estimation of the optimum width by analytical models, which usually do not account for further relevant optimization parameters, such as a step in the cylinder wall. However, a recently developed, enhanced analytical model predicts that this loss may be significantly reduced by such a step. In this work, this design was realized and investigated experimentally according to this prediction by modification of the cylinder liner and the seal of an extensively tested laboratory-scale machine. The results confirm that such a design actually reduces the thermal loss substantially, presumably by reducing the cyclic mass flows through the open end of the gap. Additionally, it even improves the net power output due to a reduced volumetric displacement by the piston or displacer, resulting in smaller flow losses and thermal regenerator losses, whereas the pressure amplitude remains virtually unchanged, contrary to initial expectations. -
Cryogenic Refrigeration Methods for Low and Ultra-Low Temperatures - a Review
Sddhand, Vol. 9, Part 3, November 1986, pp. 191-232. ~ Printed in India. Cryogenic refrigeration methods for low and ultra-low temperatures - a review M THIRUMALESHWAR* and S V SUBRAMANYAM** * Cryogenics Section, Technical Physics and Prototype Engineering Division, BARC, Bombay 400 085, India ** Department of Physics, Indian Institute of Science, Bangalore 560 012, India MS received 2 September 1985; revised 4 April 1986 Abstract. In this review, various cryogenic refrigeration methods to obtain temperatures extending down to the milliKelvin/microKelvin range are described after first explaining the concepts of a "thermo- dynamically ideal cycle" and the "figure of merit". The various cycles are compared with each other. Data about some of the commercially available refrigerators/cryogenerators have also been included in this review. Keywords. Cryogenics; ultra-low temperatures; refrigeration methods. I. Introduction Cryogenics literally means "icy cold". However, generally this word connotes temperatures below 120 K (Barron 1966). A review of the history of the development of cryogenics is given by Mendelssohn (1966). Cryogenic technology implies the science and techniques of liquefaction, transportation and usage of cryogenic fluids such as liquid nitrogen (LN2), liquid hydrogen (LH2), liquid helium (LHe) etc. Developments of this technology from both the commercial and laboratory points of view are described in standard references (e.g., Mendelssohn 1966; Hoare et al 1961; Scott 1959; Croft 1976; Kurti 1971). Cryogenic refrigeration methods cover a wide spectrum from large industrial plants for production of cryogenic liquids to closed cycle helium refrigerators handling only a few watts at very low temperatures. Daniels and du Pre (1971) give specifically the require- ments of such small refrigerators for cooling some electronic devices.