Steel and Raw Materials
Total Page:16
File Type:pdf, Size:1020Kb
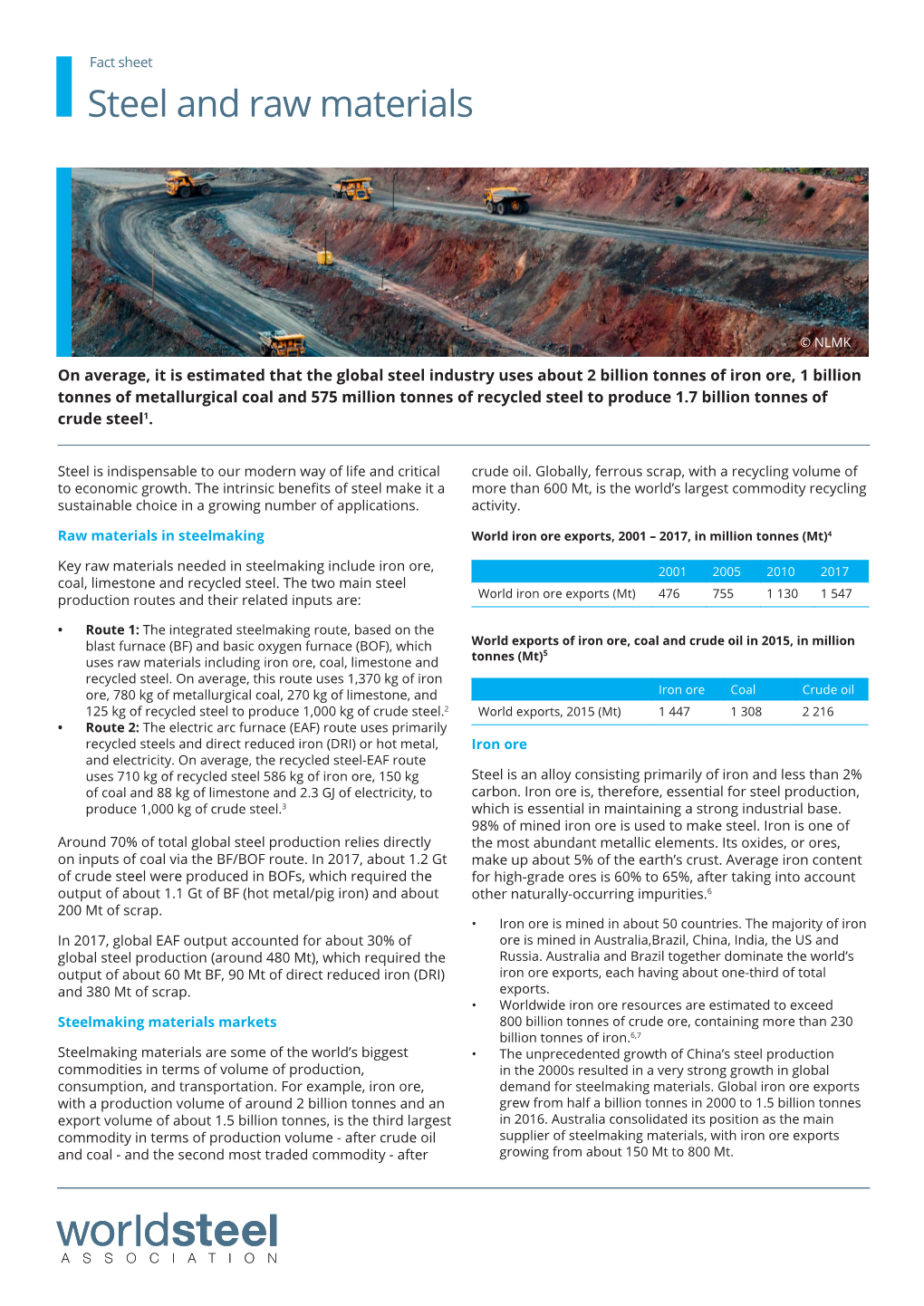
Load more
Recommended publications
-
Reduce Reuse Recycle Remanufacture
STEEL - THE PERMANENT MATERIAL IN THE CIRCULAR ECONOMY AR ECONOMY BEN CUL EFI CIR TS E R R C E a U U w n D S m io E E a t t c R e u r i d a e l r s s c n o o n i s s s e i r v m a e t i 2 o O n C E n o E R i f t f U a ic R v o ie T n E n c C In y C Y FA C U LE N MA RE ts Jo duc bs pro Durable 1 CONTENTS Steel in the circular economy 3 Steel is essential to our modern world 5 Reduce 7 Decreasing the amount of material, energy and other resources used to create steel and reducing the weight of steel used in products. Use and reuse 11 Reuse is using an object or material again, either for its original purpose or for a similar purpose, without significantly altering the physical form of the object or material. Remanufacture 15 The process of restoring durable used steel products to as-new condition. Recycle 19 Melting steel products at the end of their useful life to create new steels. Recycling alters the physical form of the steel object so that a new application can be created from the recycled material. End notes 22 2 STEEL IN THE CIRCULAR ECONOMY A sustainable circular economy is one in which steel is fundamental to the circular economy. society reduces the burden on nature by ensuring The industry is continuing to expand its offer resources remain in use for as long as possible. -
Society, Materials, and the Environment: the Case of Steel
metals Review Society, Materials, and the Environment: The Case of Steel Jean-Pierre Birat IF Steelman, Moselle, 57280 Semécourt, France; [email protected]; Tel.: +333-8751-1117 Received: 1 February 2020; Accepted: 25 February 2020; Published: 2 March 2020 Abstract: This paper reviews the relationship between the production of steel and the environment as it stands today. It deals with raw material issues (availability, scarcity), energy resources, and generation of by-products, i.e., the circular economy, the anthropogenic iron mine, and the energy transition. The paper also deals with emissions to air (dust, Particulate Matter, heavy metals, Persistant Organics Pollutants), water, and soil, i.e., with toxicity, ecotoxicity, epidemiology, and health issues, but also greenhouse gas emissions, i.e., climate change. The loss of biodiversity is also mentioned. All these topics are analyzed with historical hindsight and the present understanding of their physics and chemistry is discussed, stressing areas where knowledge is still lacking. In the face of all these issues, technological solutions were sought to alleviate their effects: many areas are presently satisfactorily handled (the circular economy—a historical’ practice in the case of steel, energy conservation, air/water/soil emissions) and in line with present environmental regulations; on the other hand, there are important hanging issues, such as the generation of mine tailings (and tailings dam failures), the emissions of greenhouse gases (the steel industry plans to become carbon-neutral by 2050, at least in the EU), and the emission of fine PM, which WHO correlates with premature deaths. Moreover, present regulatory levels of emissions will necessarily become much stricter. -
Schoolcraft Blast Furnace
Pictured Rocks National Lakeshore Schoolcraft National Park Service U.S. Department of the Interior Blast Furnace Schoolcraft furnace With surveyor William Burt’s discovery of iron ore near Teal Lake in Marquette County in 1844, Michigan’s Upper Peninsula suddenly became a hub of activity. The discovery led to construction of a vast mining and manufacturing industry using forges and blast furnaces. When the Civil War ended, many of the South’s furnaces had been destroyed by the war. Westward expansion was occurring across the plains and demand for iron boomed. It was during this era that many of the Upper Peninsula’s furnaces were constructed. There were advantages to smelting iron ore from charcoal fires. Iron produced in this manner was low in carbon content, making it highly fusable, strong, malleable and able to withstand shocks without cracking. The iron made fine wagon rims, horseshoes, and railroad wheels. Before the boom times were over, 29 separate furnaces were located on the Old Munising, ca. 1870 peninsula, though not all operated simultaneously. The business of iron making required more capital than was readily available in the area and financing and management of the operations was often complex. The first group of investors were from Philadelphia. They wished to develop a resort village on Munising Bay’s east shoreline in 1850. Some 87,000 acres of timber were purchased for $.85 an acre. A village was platted on the east shore of Munising Bay, lots were sold, and a dock was built. Henry Mather and Peter White acted as agents for the group of investors who created the Schoolcraft Iron Company in 1866. -
Higher-Quality Electric-Arc Furnace Steel
ACADEMIC PULSE Higher-Quality Electric-Arc Furnace Steel teelmakers have traditionally viewed Research Continues to Improve the electric arc furnaces (EAFs) as unsuitable Quality of Steel for producing steel with the highest- Even with continued improvements to the Squality surface finish because the process design of steelmaking processes, the steelmaking uses recycled steel instead of fresh iron. With over research community has focused their attention 100 years of processing improvements, however, on the fundamental materials used in steelmaking EAFs have become an efficient and reliable in order to improve the quality of steel. In my lab steelmaking alternative to integrated steelmaking. In at Carnegie Mellon University, we have several fact, steel produced in a modern-day EAF is often research projects that deal with controlling the DR. P. BILLCHRIS MAYER PISTORIUS indistinguishable from what is produced with the impurity concentration and chemical quality of POSCOManaging Professor Editorof Materials integrated blast-furnace/oxygen-steelmaking route. steel produced in EAFs. Science412-306-4350 and Engineering [email protected] Mellon University Improvements in design, coupled with research For example, we recently used mathematical developments in metallurgy, mean high-quality steel modeling to explore ways to control produced quickly and energy-efficiently. phosphorus. Careful regulation of temperature, slag and stirring are needed to produce low- Not Your (Great-) Grandparent’s EAF phosphorus steel. We analyzed data from Especially since the mid-1990s, there have been operating furnaces and found that, in many significant improvements in the design of EAFs, cases, the phosphorus removal reaction could which allow for better-functioning burners and a proceed further. -
5. Sirhowy Ironworks
Great Archaeological Sites in Blaenau Gwent 5. SIRHOWY IRONWORKS There were a number of ironworks in the area now covered by Blaenau Gwent County Borough, which provided all the raw materials they needed – iron ore, limestone and fuel, charcoal at first but later coal to make coke. The Sirhowy ironworks (SO14301010) are the only one where there is still something to see. The works were opened in 1778 with one blast furnace. Although it was originally blown by water power, in 1799 the owners invested in a Boulton and Watt steam engine. This gave them enough power to blow a second furnace, which started production in 1802. In the early years of the 19th century, the pig iron produced at Sirhowy was sent to the Tredegar works a little further down the valley where it was refined, until 1818 when the Sirhowy works were sold and started to send its pig iron to Ebbw Vale. A third furnace was added in 1826 and a fourth in 1839. But by the 1870s iron smelting at Sirhowy was no longer profitable, and the works finally closed in 1882. Like all ironworks in South Wales, the furnaces were built against a steep bank which enabled the ironworkers to load the charge of iron ore, limestone and coke or charcoal fuel more easily at the top of the furnace. All that is now left now are the remains of a bank of blast furnaces with the arches that would originally have linked them to the casting houses in front, and the building that originally housed the waterwheel. -
Update to the Developments of Hisarna an Ulcos Alternative Ironmaking Process Ir
Update to the Developments of Hisarna An Ulcos alternative ironmaking process Ir. Jan van der Stel , ir. Koen Meijer, ing. Cornelis Teerhuis, dr. Christiaan Zeijlstra, ir. Guus Keilman and ing. Maarten Ouwehand Tata Steel IJmuiden, The Netherlands Research, Development & Technology IEAGHG/IETS Iron and steel Industry CCUS and Process Integration Workshop Tokyo, Japan 4 – 7 November 2013 Confidential Content 1. HIsarna technology 2. HIsarna and CCS 3. HIsarna pilot plant 4. Campaign results 5. Conclusions 6. Forward plan 2 IEAGHG/IETS Iron and steel Industry CCUS and Process Integration Workshop , Tokyo, Japan, 4 – 7 November 2013. Confidential Ulcos IEAGHG/IETS Iron and steel Industry CCUS and Process Integration Workshop , Tokyo, Japan, 4 – 7 November 2013. Confidential 1. HIsarna technology Comparison with the BF route Blast furnace sinter Iron ore coke Liquid iron coal 4 IEAGHG/IETS Iron and steel Industry CCUS and Process Integration Workshop , Tokyo, Japan, 4 – 7 November 2013. Confidential 1. HIsarna technology Comparison with the BF route Blast furnace sinter Iron ore coke coal Direct use of coal and ore Liquid iron No coking and agglomeration 5 IEAGHG/IETS Iron and steel Industry CCUS and Process Integration Workshop , Tokyo, Japan, 4 – 7 November 2013. Confidential 1. HIsarna technology Top gas Oxygen Ore Oxygen Coal Slag Hot metal 6 IEAGHG/IETS Iron and steel Industry CCUS and Process Integration Workshop , Tokyo, Japan, 4 – 7 November 2013. Confidential 1.1. HIsarna technology Melting cyclone technology Melting and partial reduction of fine iron ores “2 Fe 2O3(s) + 2 CO(g) → 4 FeO(l) + 2 CO 2(g) ” • The cyclone product is a molten mixture of Fe 3O4 and FeO (~ 20 % reduced) • Pure oxygen is injected to generate the required melting temperature • The fines are separated from the gas by centrifugal flow of the gas IEAGHG/IETS Iron and steel Industry CCUS and Process Integration Workshop , Tokyo, Japan, 4 – 7 November 2013. -
Studying and Improving Blast Furnace Cast Iron Quality
Т. К. BALGABEKOV, D. K. ISSIN, B. M. KIMANOV, A. Z. ISSAGULOV, ISSN 0543-5846 ZH. D. ZHOLDUBAYEVA, А. Z. AKASHEV, B. D. ISSIN METABK 53(4) 556-558 (2014) UDC – UDK 669.162.2:669.1:669.13=111 STUDYING AND IMPROVING BLAST FURNACE CAST IRON QUALITY Received – Prispjelo: 2013-11-09 Accepted – Prihvaćeno: 2014-04-30 Preliminary Note – Prethodno priopćenje In the article there are presented the results of studies to improve the quality of blast furnace cast iron. It was estab- lished that using fire clay suspension for increasing the mould covering heat conductivity improves significantly pig iron salable condition and filtration refining method decreases iron contamination by nonmetallic inclusions by 50 – 70 %. Key words: blast furnace, cast iron, fire clay, filter, filtering elements INTRODUCTION tically contain water after mould drying with coke gas. Therefore, pig iron salable condition improves signifi- With the development of motor transport industry, cantly. machine-tool building and other machine building Besides, the use of fire clay for mould coverings ex- branches there increased the requirements to the quality cludes claps in dissolution and prevents the lime solu- of blast furnace cast iron. With the use in the cupola tion corroding action when split on the open parts of the mixture of cast iron melted in large-volume furnaces worker’s body, increases the culture of production and with the melting progressive parameters, at machine decreases labor intensity when making solution, as there building plants there became often defective castings is excluded the waste presence up to 30 – 40 % in the with shrinkage defects, friability, cracks. -
STEEL in the CIRCULAR ECONOMY a Life Cycle Perspective CONTENTS
STEEL IN THE CIRCULAR ECONOMY A life cycle perspective CONTENTS Foreword 3 The circular economy 4 Life cycle thinking 6 The life cycle assessment (LCA) approach 8 worldsteel’s LCA methodology and life cycle inventory (LCI) database 10 Sustainability and life cycle assessment 12 LCA in the steel industry 14 LCA by life cycle phase 15 Raw materials and steel production 15 Markets for by-products 16 Manufacturing and use 16 Reuse and remanufacturing 18 Recycling 19 LCA initiatives 20 Regional and global initiatives 21 Market sector initiatives 22 Construction 22 Automotive 24 Packaging 25 End notes 28 Glossary 29 Cover image: Steel staircase, office building, Prague, Czech Republic Design: double-id.com FOREWORD We live in a rapidly changing world with finite resources. Too many legislative bodies around the world At the same time, improvements in standards of living still enact regulations which only affect the “use and eradication of poverty, combined with global phase” of a product’s life, for example water and population growth, exert pressure on our ecosystems. energy consumption for washing machines, energy consumption for a fridge or CO2 emissions whilst As steel is everywhere in our lives and is at the heart driving a vehicle. This focus on the “use phase” can of our sustainable future, our industry is an integral part lead to more expensive alternative lower density of the global circular economy. The circular economy materials being employed but which typically have a promotes zero waste, reduces the amount of materials higher environmental burden when the whole life cycle used, and encourages the reuse and recycling of is considered. -
Pig Iron Sub-Committee, Chaired by Rodrigo Valladares, CEO of Viena Siderúrgica S/A, for Preparing and Editing the Information Presented in This Guide
Copyright © 2014 by International Iron Metallics Association Ltd. This guide published by International Iron Metallics Association Ltd. All rights reserved. This guide may be used or reproduced in any manner whatsoever providing it includes full acknowledgement to the IIMA. 2011 International Iron Metallics Association (IIMA) Printed and bound in the United Kingdom Disclaimer This guide is intended for information purposes only and is not intended as commercial material in any respect. The material is not intended as an offer or solicitation for the purposes of sale of any financial instrument, is not intended to provide an investment recommendation and should not be relied upon for such. The material is derived from published sources, together with personal research. No responsibility or liability is accepted for any such information of opinions or for any errors, omissions, misstatements, negligence, or otherwise for any further communication, written or otherwise. ii ACKNOWLEDGEMENT The International Iron Metallics Association (IIMA) wishes to thank Dr. Oscar Dam, Chief Technical Advisor, and the Pig Iron Sub-Committee, chaired by Rodrigo Valladares, CEO of Viena Siderúrgica S/A, for preparing and editing the information presented in this guide. FOREWORD The International Iron Metallics Association was created to promote the use of ore-based metallics (pig iron, HBI, DRI, and iron nuggets) as value-adding raw materials for the iron and steel and ferrous casting industries. Safe and efficient handling and shipping of merchant ore-based metallics are vital to the commercial trade and use of these materials. Therefore, we are continuing the series of guides begun by IIMA co-founder, HBI Association (HBIA), with this guide which addresses the methods, techniques, and procedures for handling and transferring merchant pig iron at dry bulk terminals. -
Distortion in Case Carburized Components- the Steelmakers View
Heat Treating: Proceedings of the 18th Conference Copyright © 1999 ASM International® Ronald A. Wallis, Harry W. Walton, editors, p 5-11 All rights reserved. DOI: 10.1361/cp1998ht005 www.asminternational.org Distortion in Case Carburized Components The Steel makers View M. Cristinacce British Steel Engineering Steels Rotherham, United Kingdom 1. Abstract NVH (noise, vibration and harshness) is becoming of increasing importance in the automotive industry. The control Distortion of components during heat treatment has a of distortion to give correct mating of rotating components significant effect upon final component costs. The factors such as gears and shafts has a major influence upon NVH which influence distortion behaviour occur during the performance. machining and heat treatment processes and are therefore Most of the examples given in this paper are automotive outside the control of the steelmaker. One important factor transmission components which are carburised. which is under the control of the steelmaker is hardenability A wide variety of factors influence distortion behaviour Consistent hardenability performance can have a significant and can be broadly summarised as follows: effect in reducing the variability in distortion. In a number of Component shape. instances it has been shown that the macrostructure and Steel type. as-cast shape of the steel can also influence distortion. Other Microstructure and residual stresses prior to heat downstream processing effects such as forging may also be treatment. influential in these circumstances. Reheating and carburising conditions. This paper gives examples of some of the experiences of Stacking and support in furnace. British Steel Engineering Steels with customers and end users, Quenching - Medium, temperature, flow, jigging, etc. -
The Stainless Steel Family
The Stainless Steel Family A short description of the various grades of stainless steel and how they fit into distinct metallurgical families. It has been written primarily from a European perspective and may not fully reflect the practice in other regions. Stainless steel is the term used to describe an extremely versatile family of engineering materials, which are selected primarily for their corrosion and heat resistant properties. All stainless steels contain principally iron and a minimum of 10.5% chromium. At this level, chromium reacts with oxygen and moisture in the environment to form a protective, adherent and coherent, oxide film that envelops the entire surface of the material. This oxide film (known as the passive or boundary layer) is very thin (2-3 namometres). [1nanometre = 10-9 m]. The passive layer on stainless steels exhibits a truly remarkable property: when damaged (e.g. abraded), it self-repairs as chromium in the steel reacts rapidly with oxygen and moisture in the environment to reform the oxide layer. Increasing the chromium content beyond the minimum of 10.5% confers still greater corrosion resistance. Corrosion resistance may be further improved, and a wide range of properties provided, by the addition of 8% or more nickel. The addition of molybdenum further increases corrosion resistance (in particular, resistance to pitting corrosion), while nitrogen increases mechanical strength and enhances resistance to pitting. Categories of Stainless Steels The stainless steel family tree has several branches, which may be differentiated in a variety of ways e.g. in terms of their areas of application, by the alloying elements used in their production, or, perhaps the most accurate way, by the metallurgical phases present in their microscopic structures: . -
Master's Thesis
MASTER'S THESIS Energy System Analysis in the Swedish Iron and Steel Industry Ernesto Ubieto Master of Science (120 credits) Mechanical Engineering Luleå University of Technology Department of Engineering Sciences and Mathematics Energy System Analysis of the Swedish Iron and Steel Industry Ernesto Ubieto Udina Table of contents 1 INTRODUCTION ................................................................................................................. 7 2 OBJECTIVES ....................................................................................................................... 8 3 METHODOLOGY ................................................................................................................ 9 3.1 Methodology of System Analysis ............................................................................... 9 3.1.1 Scope of the Analysis ....................................................................................... 10 3.1.2 Boundaries of the Analysis ............................................................................... 11 3.1.3 Time frames ..................................................................................................... 11 3.1.4 Components of the System .............................................................................. 12 3.1.5 Connections within the system ........................................................................ 13 3.1.6 Limitations of the study ................................................................................... 15 3.1.7 Tracking CO2