Processing PDMS Gecko Tape Using Isopore Filters and Silicon Wafer Templates
Total Page:16
File Type:pdf, Size:1020Kb
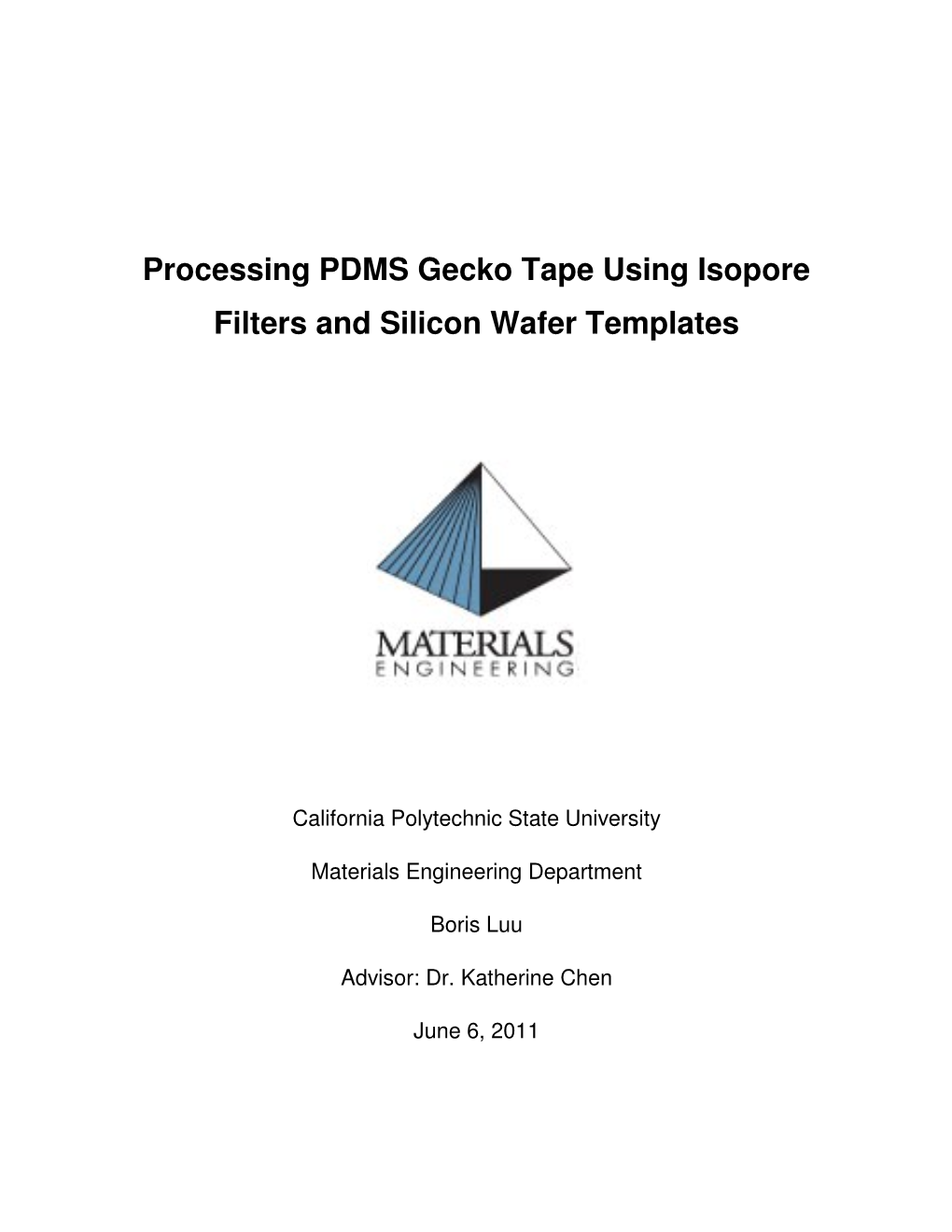
Load more
Recommended publications
-
Honors Thesis
Surface Construction and Mechanisms of Adhesion in Tokay Gecko Feet and Characterization of a Bio-Inspired Reversible Adhesive Tape Honors Undergraduate Thesis Submitted to: The College of Engineering Honors Committee College of Engineering 122 Hitchcock Hall The Ohio State University By: Robert A. Sayer Department of Mechanical Engineering Spring 2006 Approved by: Professor Bharat Bhushan, Advisor Department of Mechanical Engineering Acknowledgements I would like to thank Professor Bharat Bhushan for providing me the opportunity to work in the NLIM and the many hours that he spent helping revise the literature review. I also greatly appreciate the help that I received from Dr. Zhenhua Tao with the AFM and from Yong Chae Jung with the optical profiler and the contact angle measurements and Dr. Manuel Palacio for obtaining the SEM images. Without the aforementioned people, this project would not have been possible. i Abstract Several creatures including insects, spiders, and lizards, have developed a unique clinging ability that utilizes dry adhesion. Geckos, in particular, have developed the most complex adhesive structures capable of smart adhesion—the ability to cling on different smooth and rough surfaces and detach at will. These animals make use of on the order of a million microscale hairs (setae) (about 14000/mm2) that branch off into hundreds of nanoscale spatulae. This hierarchical surface construction gives the gecko the adaptability to create a large real area of contact with surfaces. van der Waals forces are the primary mechanism utilized to adhere to surfaces and capillary forces are a secondary effect that can further increase adhesive force. Although a gecko is capable of producing on the order of 20 N of adhesive force, it retains the ability to remove its feet from an attachment surface at will. -
Enhanced Friction and Adhesion with Biologically Inspired Fiber Arrays
Enhanced Friction and Adhesion with Biologically Inspired Fiber Arrays Carmel Majidi Electrical Engineering and Computer Sciences University of California at Berkeley Technical Report No. UCB/EECS-2007-55 http://www.eecs.berkeley.edu/Pubs/TechRpts/2007/EECS-2007-55.html May 15, 2007 Copyright © 2007, by the author(s). All rights reserved. Permission to make digital or hard copies of all or part of this work for personal or classroom use is granted without fee provided that copies are not made or distributed for profit or commercial advantage and that copies bear this notice and the full citation on the first page. To copy otherwise, to republish, to post on servers or to redistribute to lists, requires prior specific permission. Enhanced Friction and Adhesion with Biologically Inspired Fiber Arrays by Carmel Shamim Majidi B.S. (Cornell University) 2001 M.S. (University of California, Berkeley) 2004 A thesis submitted in partial satisfaction of the requirements for the degree of Doctor of Philosophy in Engineering - Electrical Engineering and Computer Science in the GRADUATE DIVISION of the UNIVERSITY OF CALIFORNIA, BERKELEY Committee in charge: Professor Ronald S. Fearing, Chair Professor Kyriakos Komvopoulos Professor Ali Javey Spring 2007 The thesis of Carmel Shamim Majidi is approved. Chair Date Date Date University of California, Berkeley Spring 2007 Enhanced Friction and Adhesion with Biologically Inspired Fiber Arrays Copyright c 2007 by Carmel Shamim Majidi Abstract Enhanced Friction and Adhesion with Biologically Inspired Fiber Arrays by Carmel Shamim Majidi Doctor of Philosophy in Engineering - Electrical Engineering and Computer Science University of California, Berkeley Professor Ronald S. Fearing, Chair Controlling surface forces through nano/microstructure represents an important advance- ment in tribology. -
Surface Wettability Plays a Significant Role in Gecko Adhesion Underwater
Surface wettability plays a significant role in gecko adhesion underwater Alyssa Y. Starka,1, Ila Badgeb, Nicholas A. Wucinicha, Timothy W. Sullivana, Peter H. Niewiarowskia, and Ali Dhinojwalab aIntegrated Bioscience Program, and bDepartment of Polymer Science, The University of Akron, Akron, OH 44325 Edited by David B. Wake, University of California, Berkeley, CA, and approved February 13, 2013 (received for review November 8, 2012) Although we now have thousands of studies focused on the nano-, in water (33). At face value, this is perplexing: many geckos live in micro-, and whole-animal mechanics of gecko adhesion on clean, dry tropical habitats where surface wetting from rain and humidity is substrates, we know relatively little about the effects of water on expected to be common. However, arboreal geckos likely use plant gecko adhesion. For many gecko species, however, rainfall fre- surfaces more than other substrates, such as dirt, sand, or man- quently wets the natural surfaces they navigate. In an effort to begin made glass and plastics, and many plant surfaces are hydrophobic closing this gap, we tested the adhesion of geckos on submerged (24). This begs the obvious question: Can geckos stick to wet substrates that vary in their wettability. When tested on a wet hydrophobic surfaces? Unfortunately, data necessary to answer hydrophilic surface, geckos produced a significantly lower shear this question are very limited. Early experiments by Hiller (35) adhesive force (5.4 ± 1.33 N) compared with a dry hydrophilic sur- tested for the effect of surface wettability on adhesion using sur- face (17.1 ± 3.93 N). -
ADHESIVE FORCE of a SINGLE GECKO SETA a Thesis Presented
ADHESIVE FORCE OF A SINGLE GECKO SETA A Thesis Presented to The Graduate Faculty of The University of Akron In Partial Fulfillment of the Requirements for the Degree Master of Science Lan Yu May, 2018 ADHESIVE FORCE OF A SINGLE GECKO SETA Lan Yu Thesis Approved: Accepted: Advisor Dean of College Dr. Ali Dhinojwala Dr. Eric J. Amis Committee Member Dean of the Graduate School Dr. Hunter King Dr. Chand K. Midha Department Chair Date Dr. Coleen Pugh ii ABSTRACT The gecko’s adhesion system uses arrays of setae to achieve strong and repeatable adhesion. Observation of the toe pad structure shows that shorter setae are generally proximal while longer ones distal [39]. We hypothesized that a seta of longer length would generate higher adhesive force, as long and slender setae have lower bending modulus, and therefore making it easier to contact spatulae with the surface. By following previous single seta experiments [11], we first measured the shear force generated by an isolated gecko seta using Nano Bionix. We also tested the length hypothesis by measuring the shear adhesion ability of single seta of varying lengths ranging from 80 to 140µm, which was taken from different parts of the gecko toe pad from distal to proximal. Measurements gave the result of shear forces of a single seta in the range of 80 to 250µN and an average of 136.81µN. This number is lower than the average value 194µN in previous studies, which is tested under a preload of 15µN [11]. In addition, results from 12 individual setae suggested that shear adhesion force of a single seta is independent of setal length and dependent on setal diameter. -
Chapter 2 the Design and Fabrication
Abstract There has been significant interest in developing dry adhesives mimicking the gecko adhesive system, which offers several advantages compared to conventional pressure sensitive adhesives. Specifically, gecko adhesive pads have anisotropic adhesion properties: the adhesive pads (spatulae) stick strongly when sheared in one direction but are non-adherent when sheared in the opposite direction. This anisotropy property is attributed to the complex topography of the array of fine tilted and curved columnar structures (setae) that bear the spatulae. In this thesis, easy, scalable methods, relying on conventional and unconventional techniques are presented to incorporate tilt in the fabrication of synthetic polymer-based dry adhesives mimicking the gecko adhesive system, which provide anisotropic adhesion properties. In the first part of the study, the anisotropic adhesion and friction properties of samples with various tilt angles to test the validity of a nanoscale tape-peeling model of spatular function are measured. Consistent with the Peel Zone model, samples with lower tilt angles yielded larger adhesion forces. Contact mechanics of the synthetic array were highly anisotropic, consistent with the frictional adhesion model and gecko-like. Based on the original design, a new design of gecko-like dry adhesives was developed which showed superior tribological properties and furthermore showed anisotropic adhesive properties without the need for tilt in the structures. These adhesives can be used to reversibly suspend weights from vertical surfaces (e.g., walls) and, for the first time to our knowledge, horizontal surfaces (e.g., ceilings) by simultaneously and judiciously activating anisotropic friction and adhesion forces. Furthermore, adhesion properties between artificial gecko-inspired dry adhesives and rough substrates with varying roughness are studied. -
Nano-Hairs: Dry Adhesives
Geckos: From climbing up walls, trees to being upside-down. The gecko has mastered the skill of climbing and sticking to any surface at any angle. The ability to scurry up and down surfaces at blistering pace is what has allowed the gecko to escape predators and catch its own prey. The most crucial ability to the survival of this species. But how are these animals able to defy gravity? The answer; Nanohairs. Nano-Hairs: These hairs on the pads of their toes are called setae, and they pos- ses about two million of them.(lerch) But how do microscopic sized hairs allow a gecko to not only stick but climb up walls? These hairs are spread out when pushed against a surface. This drastically in- creases the surface area a gecko has on a surface. A gecko can simply relax the force it has against the surface causing less hairs to be spread out leading to a smaller surface area and van der waals forces, allowing it to lift its foot off. Dry Adhesives: Comparing a gecko to our adhesive technologies, there is clear superiorities that the gecko’s feet posses. Suc- tions adhesives are expensive and costly, while ones that rely on chemical bonds are sticky and permanent. Using inspiration from geckos nanohairs though, these flaws have been eliminated. Creating synthetic setae with nanotechnology, adhesives have been able to be made that have incredible adhesive capacities, howev- er like the gecko are not sticky nor are permanent. . -
Modeling Fabrication and Testing of Artificial Gecko Adhesion Using Multi Layer Fbrillar Structure
International Journal of Latest Technology in Engineering, Management & Applied Science (IJLTEMAS) Volume VI, Issue VIIIS, August 2017 | ISSN 2278-2540 Modeling Fabrication and Testing of Artificial Gecko Adhesion using Multi Layer Fbrillar Structure Ameya P. Nijasure, Priam V. Pillai Department of Mechanical Engineering, Pillai Collage of Engineering, New Panvel, Raigad, India. Abstract- The idea of designing a micro level artificial gecko deform independently, which makes sure that each fiber adhesive structure is inspired from ability of geckos to climb any reaches deeper in case of rough surface to achieve clean surface. Gecko can climb any rough or smooth surface because contact [8]. The key parameter that plays important role in of its hierarchical structure present on feet which functions as a gecko adhesion are pattern periodicity of a synthetic setae, smart adhesive [1]. The key parameter that affects gecko hierarchical structure, length, diameter, angle, size, stiffness of adhesion are pattern periodicity of a synthetic setae, hierarchical end tips and flexibility of a base. structure, length, diameter, angle, size, stiffness of end tips and flexibility of a base [2]. The design and fabrication of number of Each five-toed foot of the gecko has about 500,000 foot- single and multi-level hierarchical pattern were performed. CO2 hairs called setae a uniformly distributed array each about LASER cutting machine having power of 60 W is used to 110µm in length and 4.2µm diameter. Further it is divided in manufacture moulds. The mould is fabricated from methyl to spatulae a thin stalk with triangular shape tiny end of 0.2µm methacrylate sheets of different thickness 3 mm to 10 mm. -
The Effect of Substrate Wettability and Modulus on Gecko and Gecko-Inspired Synthetic Adhesion in Variable Temperature and Humid
www.nature.com/scientificreports OPEN The efect of substrate wettability and modulus on gecko and gecko‑inspired synthetic adhesion in variable temperature and humidity Christopher T. Mitchell1,3, Cem Balda Dayan2,3, Dirk‑M. Drotlef2, Metin Sitti2 & Alyssa Y. Stark1* Gecko adhesive performance increases as relative humidity increases. Two primary mechanisms can explain this result: capillary adhesion and increased contact area via material softening. Both hypotheses consider variable relative humidity, but neither fully explains the interactive efects of temperature and relative humidity on live gecko adhesion. In this study, we used live tokay geckos (Gekko gecko) and a gecko‑inspired synthetic adhesive to investigate the roles of capillary adhesion and material softening on gecko adhesive performance. The results of our study suggest that both capillary adhesion and material softening contribute to overall gecko adhesion, but the relative contribution of each depends on the environmental context. Specifcally, capillary adhesion dominates on hydrophilic substrates, and material softening dominates on hydrophobic substrates. At low temperature (12 °C), both capillary adhesion and material softening likely produce high adhesion across a range of relative humidity values. At high temperature (32 °C), material softening plays a dominant role in adhesive performance at an intermediate relative humidity (i.e., 70% RH). Te gecko adhesive system has sparked intense research and innovation for more than two decades 1–15. However, despite signifcant interest in the morphology, evolutionary history, and biomechanical principles of the gecko adhesive system, there is still uncertainty about the governing mechanisms of gecko adhesion. Specifcally, the potential roles of capillary adhesion and material sofening on gecko adhesive performance in humid environ- ments have ofen been debated 16–20. -
Properties, Principles, and Parameters of the Gecko Adhesive System
Preprint: Autumn, K. 2006. Properties, principles, and parameters of the gecko adhesive system. In Smith, A. and J. Callow, Biological Adhesives. SpringerKellar Verlag. Autumn The Gecko Adhesive System 1 of 39 Do not copy or distribute without permission of the author ([email protected]). Copyright (c) 2005 Kellar Autumn. Properties, Principles, and Parameters of the Gecko Adhesive System Kellar Autumn Department of Biology Lewis & Clark College Portland, OR 97219-7899 [email protected] 10156 words + 130 references. 6 figures, 2 tables. “The designers of the future will have smarter adhesives that do considerably more than just stick” –Fakley 2001 1. Summary Gecko toe pads are sticky because they feature an extraordinary hierarchy of structure that functions as a smart adhesive. Gecko toe pads (Russell 1975) operate under perhaps the most severe conditions of any adhesives application. Geckos are capable of attaching and detaching their adhesive toes in milliseconds (Autumn et al. 2005 (in press)) while running with seeming reckless abandon on vertical and inverted surfaces, a challenge no conventional adhesive is capable of meeting. Structurally, the adhesive on gecko toes differs dramatically from that of conventional adhesives. Conventional pressure sensitive adhesives (PSAs) such as those used in adhesive tapes are fabricated from materials that are sufficiently soft and sticky to flow and make intimate and continuous surface contact (Pocius 2002). Because they are soft and sticky, PSAs also tend to degrade, foul, self- adhere, and attach accidentally to inappropriate surfaces. Gecko toes typically bear a series of scansors covered with uniform microarrays of hair-like setae formed from !- keratin (Russell 1986; Wainwright et al. -
Nanoapplications – from Geckos to Human Health Correspondence To
Nanoapplications – From geckos to human health Correspondence to: Simone Lerch Simone Lerch nspm ltd, Luzernerstr. 36 nspm ltd, Meggen, Switzerland 6045 Meggen Switzerland [email protected] Abstract Nanotechnology, the manipulation of matter on a bundles as synthetic setae (see Figure 1C and D), molecular scale, is all around us in our everyday and possesses adhesive capacities nearly four lives. Chocolate, non-dairy creamer, and sunscreen times higher than that of gecko feet. It even sticks are examples of consumer products with a high to Teflon. content of nanoparticles. Nanotechnology holds great potential for environmental applications like What is nanotechnology? wastewater treatment and nanobionic engineering Nanotechnology is generally defined as the manipu- of plants. Due to their unique and adaptable lation of matter on a molecular scale, typically in the properties for targeted therapeutic payload delivery, − range of nanometres (1 nm = 10 9 m). Nanomatter nanoparticles are also emerging as promising is typically smaller than a cell, but bigger than a tools for innovative pharmaceutical treatment. small molecule (see Figure 2). The European Union Nevertheless, licensing regulations specifically for (EU) defines nanomaterials as ‘natural, incidental nanomaterials are lacking, and the long-term or manufactured material containing particles, in effects of nanoparticles on both the environment an unbound state or as an aggregate or as an and human health need to be further clarified. agglomerate and where, for 50% or more of -
Gecko-Inspired Carbon Nanotube-Based Self-Cleaning
NANO LETTERS 2008 Gecko-Inspired Carbon Nanotube-Based Vol. 8, No. 3 Self-Cleaning Adhesives 822-825 Sunny Sethi,† Liehui Ge,† Lijie Ci,‡ P. M. Ajayan,‡ and Ali Dhinojwala*,† Department of Polymer Science, The UniVersity of Akron, Akron, Ohio 44325, Department of Materials Science and Engineering, Rensselaer Polytechnic Institute, Troy, New York 12180-3590 Received October 26, 2007 ABSTRACT The design of reversible adhesives requires both stickiness and the ability to remain clean from dust and other contaminants. Inspired by gecko feet, we demonstrate the self-cleaning ability of carbon nanotube-based flexible gecko tapes. A gecko has the unique ability to reversibly stick and unstick to a variety of smooth and rough surfaces. The gecko’s wall climbing ability, without the use of vis- coelastic glue, has attracted significant attention.1–11 Although the gecko does not groom its feet, its stickiness remains for months between molts.12 The gecko’s dirty feet can recover its ability to climb vertical walls only after a few steps.12 Our daily experience with sticky tapes has been the opposite. The stickier the adhesive, the more difficult it is to keep it clean from dust and other contaminants. Synthetic self-cleaning adhesives, inspired by the gecko’s feet, could be used for many applications including wall climbing robots and microelectronics. The secret of the gecko’s adhesive properties lies in the Figure 1. Natural and synthetic structures showing self-cleaning 1,13–15 microstructure of gecko feet. Microscopy shows that abilities. (A) SEM image of natural gecko setae. (B) Surface of a gecko feet are covered with millions of small hairs called lotus leaf with hierarchical roughness.16 (C) Hairy structure of lady’s setae, which further divide into hundreds of smaller spatulas mantle leaf.17 (D-E) SEM images of synthetic setae made of (Figure 1A). -
The Research of Adsorption Mechanism in Space Crawling
The Research of Adsorption Mechanism in Space Crawling Robot On- orbit Servicing for Cooperative Spacecraft Yilin Su1, Xuyan Hou1*, Kailiang Zhang 1 , Tao Chen 2, Zongquan Deng 1,Lining Sun 2 , 1 School of Mechatronics Engineering, Harbin Institute of Technology, Harbin 150001, P.R. China E-mail: [email protected] 2 School of Mechatronics Engineering, Soochow University, Suzhou 215000, P.R. China etc [5-7]. Nowadays, many countries have ABSTRACT developed for the robot, and obtained certain According to the on-orbit servicing requirements of research results [8-14], as figure 1. space cooperative spacecraft, in order to expanded existing manipulator work space and its task function and provided support for the on-orbit control of space Cooperative spacecraft, a new type of space crawling robot was designed. The space robot system was consisted of legs driven by piezoelectric, micro adhesive feet and other parts. The space robot was composed of eight legs driven by piezoelectric which has three joints and five degrees of freedom. It can extend crossing obstacle a) Alicia Robot b) REST I Robot ability by somersault based on the traditional way of crawling.The robot feet were designed into micro array structure that based on the bionics principle and reference the micro structure on feet of Gecko, insects or other creatures. Based on the theory of interface micro mechanics and tribology, the contact mechanics model between micro structure of the adhesive feet and the surface of spacecraft was established. Then analyzed its adhesive properties based on Discrete Element Method. The simulation results shown that in the space environment with c) Sky cleaner 3 Robot d) Miniwalker Robot zero gravity, the robot feet with micro array structure has the function of adsorption.