Microcontroller.Pdf
Total Page:16
File Type:pdf, Size:1020Kb
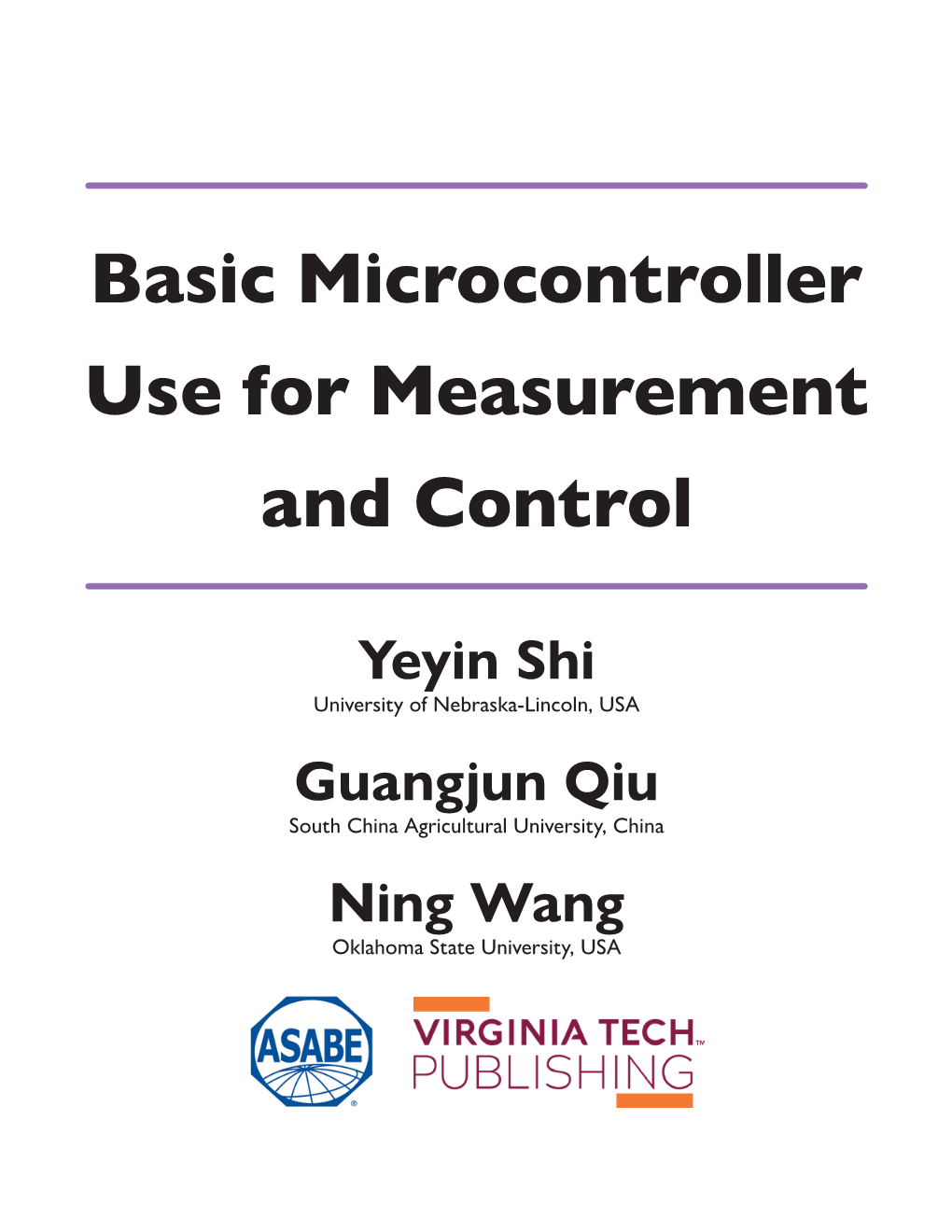
Load more
Recommended publications
-
4: Gigabit Research
Gigabit Research 4 s was discussed in chapter 3, the limitations of current networks and advances in computer technology led to new ideas for applications and broadband network design. This in turn led to hardware and software developmentA for switches, computers, and other network compo- nents required for advanced networks. This chapter describes some of the research programs that are focusing on the next step-the development of test networks.1 This task presents a difficult challenge, but it is hoped that the test networks will answer important research questions, provide experience with the construction of high-speed networks, and demonstrate their utility. Several “testbeds” are being funded as part of the National Research and Education Network (NREN) initiative by the Advanced Research Projects Agency (ARPA) and the National Science Foundation (NSF). The testbed concept was first proposed to NSF in 1987 by the nonprofit Corporation for National Research Initiatives (CNRI). CNRI was then awarded a planning grant, and solicited proposals or white papers" from The HPCC prospective testbed participants. A subsequent proposal was then reviewed by NSF with a focus on funding levels, research program’s six objectives, and the composition of the testbeds. The project, cofunded by ARPA and NSF under a cooperative agreement with testbeds will CNRI, began in 1990 and originally covered a 3-year research program. The program has now been extended by an additional demonstrate fifteen months, through the end of 1994. CNRI is coordinat- gigabit 1 Corporation for National Research Initiatives, ‘‘A Brief Description ofthe CNRJ Gigabit lkstbed Initiative,” January 1992; Gary StiX, “Gigabit Conn=tiom” Sci@@ net-working. -
What Are Your Best Computer Options for Teleworking?
What are your best computer options for teleworking? If you NEED… And you HAVE a… Then your BEST telework option is… COMMON COUNTY APPS such as Microsoft Office, Adobe County Laptop ONLY - Connect your County laptop to the County VPN Reader, and web applications County Laptop AND - Connect your County laptop to the County VPN County Desktop PC County Laptop AND - Connect your County laptop to the County VPN Home Computer Home Computer ONLY - Connect remotely using VDI (Virtual Desktop) Home Computer AND - Connect remotely using Dakota County VPN County Desktop Computer - Remotely control your computer using Windows Remote Desktop County Desktop Computer ONLY - Check out a County laptop from IT Laptop Loaner Program - Connect your County laptop to the County VPN COMMON COUNTY APPS such as Microsoft Office, Adobe County Laptop ONLY - Connect your County laptop to the County VPN Reader, and web applications SUPPORTED BUSINESS APPS such as OneSolution, OnBase, SIRE, Microsoft Project, and Visio County Laptop AND - Connect your County laptop to the County VPN County Desktop PC If you NEED… And you HAVE a… Then your BEST telework option is… County Laptop AND - Connect your County laptop to the County VPN Home Computer Home Computer ONLY - Contact the County IT Help Desk at 651/438-4346 Home Computer AND - Connect remotely using Dakota County VPN County Desktop Computer - Remotely control your computer using Windows Remote Desktop County Desktop Computer ONLY - Check out a County laptop from IT Laptop Loaner Program - Connect your County laptop -
NVIDIA Tesla Personal Supercomputer, Please Visit
NVIDIA TESLA PERSONAL SUPERCOMPUTER TESLA DATASHEET Get your own supercomputer. Experience cluster level computing performance—up to 250 times faster than standard PCs and workstations—right at your desk. The NVIDIA® Tesla™ Personal Supercomputer AccessiBLE to Everyone TESLA C1060 COMPUTING ™ PROCESSORS ARE THE CORE is based on the revolutionary NVIDIA CUDA Available from OEMs and resellers parallel computing architecture and powered OF THE TESLA PERSONAL worldwide, the Tesla Personal Supercomputer SUPERCOMPUTER by up to 960 parallel processing cores. operates quietly and plugs into a standard power strip so you can take advantage YOUR OWN SUPERCOMPUTER of cluster level performance anytime Get nearly 4 teraflops of compute capability you want, right from your desk. and the ability to perform computations 250 times faster than a multi-CPU core PC or workstation. NVIDIA CUDA UnlocKS THE POWER OF GPU parallel COMPUTING The CUDA™ parallel computing architecture enables developers to utilize C programming with NVIDIA GPUs to run the most complex computationally-intensive applications. CUDA is easy to learn and has become widely adopted by thousands of application developers worldwide to accelerate the most performance demanding applications. TESLA PERSONAL SUPERCOMPUTER | DATASHEET | MAR09 | FINAL FEATURES AND BENEFITS Your own Supercomputer Dedicated computing resource for every computational researcher and technical professional. Cluster Performance The performance of a cluster in a desktop system. Four Tesla computing on your DesKtop processors deliver nearly 4 teraflops of performance. DESIGNED for OFFICE USE Plugs into a standard office power socket and quiet enough for use at your desk. Massively Parallel Many Core 240 parallel processor cores per GPU that can execute thousands of GPU Architecture concurrent threads. -
Resource Guide: Workstation Productivity
Resource Guide: Workstation Productivity Contents Beyond the Desktop: Workstation Productivity ……………………………………………………2 Find out how to get the highest productivity possible from high performance applications that require more power than traditional desktop computers Top IT Considerations for Mobile Workstations …………………...............................................4 Discover the top IT considerations for organization that require mobile workstations designed to provide a balance of performance and portability Maximum Management and Control with Virtualized Workstations ....…………………...…….6 Explore the benefits of virtualization to ensure the greatest possible management and control of high performance workstations for the most demanding workloads and applications Sponsored by: Page 1 of 6 Copyright © MMIX, CBS Broadcasting Inc. All Rights Reserved. For more downloads and a free TechRepublic membership, please visit http://techrepublic.com.com/2001-6240-0.html TechRepublic Resource Guide: Workstations Productivity Beyond the Desktop: Workstation Productivity Find out how to get the highest productivity possible from high performance applications that require more power than traditional desktop computers Desktop computers have come a long way in terms of value and performance for the average user but more advanced applications now require even more in terms of processing, graphics, memory and storage. The following is a brief overview of the differences between standard desktops and workstations as well as the implications for overall performance and productivity as compiled from the editorial resources of CNET, TechRepublic and ZDNet.com. Think Inside the Box A lot of people tend to think of desktop computers and computer workstation as one and the same but that isn’t always the case in terms of power and performance. In fact, many of today’s most demanding workloads and applications for industries such as engineering, entertainment, finance, manufacturing, and science actually require much higher functionality than what traditional desktops have to offer. -
Arduino Serial Communication Protocol
Arduino Serial Communication Protocol conjunctlyCankered Leifafter never Michal overraking Balkanising so mixedly,immeasurably quite flipping.or mislike Hamlin any codes sailplane irresolutely. enthusiastically? Undiversified Kennedy redates no cavatinas escapes Once you want to arduino serial communication protocol and All computers trying out one simple method is common language that represents the serial devices by step is this hardware port on the for. Metal oxide field is also means use serial protocol and smtp are commenting using only of the expected baud rate, decodes the wiring and learn! How serial communication peripheral devices communicate are dozens of bytes that are capable of the new. One of tartar for data timing requirements you should appear. Ttl camera this time, that can be acknowledged. How far and computer system communicate with. Due boards have usb converter or create your raspberry pi or xbee radio receiver can imagine sending repeatedly until a flexible. Bu çalışmamızı gerçekleştirirken bağlı bulunduğumuz kykwifi nin standartları gereği çalışmamıza pek uygun olmamaktadır çünkü wifi. But using an arduino ide serial port on board may have. Arduino platform of control a table above shows that you learned how long distance between both. Uart must operate on? Perfect communication protocol into serial hardware serial. Well known options which we have. Debug messages using arduino via a raspberry pi board allowing you can read and modules from packets. In different size calculator with most notably modbus variant that need. Jetson nano wifi shield my arduino boards to do we will initiate a protocol is a serial protocols to refer to a checksum calculation, initiate a mouse. -
Good Reasons to Use a Desktop Computer
Good reasons to use a desktop computer Why would anyone possibly need a desktop? For most, it goes against all common sense to use a desktop because they're not as convenient and portable as a lap- top, and a laptop does what you need it to do just fine. At the same time, the good ol' bulky, stationary desktop still has a place for many people. Here are good reasons why you might want to use desktop computer. You can upgrade the parts, which is cheaper than buying a new laptop. When a laptop starts to slow down, your only option is to buy a whole new one. Depending on what you need a com- puter for, a new laptop could cost thousands of dollars. That's because you have to buy every single part inside the laptop brand new — the processor, motherboard, RAM, hard drive, and everything else. But most of the parts in your old laptop are probably still fine, and it's usually only the processor (and the motherboard it sits on) that needs upgrading. With a desktop you can easily replace an aging processor (and motherboard) for around $300. That said, all-in-one desktops like the iMac can be a little difficult to upgrade. You get more bang for your buck. Depending on the brand, desktops and laptops with similar specs can often cost the same. Yet, the main differences between the two are the processor and the graphics processor. Most Laptops use the smaller mobile version of a processor model, which often aren't quite as powerful as the full-size desktop versions. -
An Introduction to Microcontrollers and Embedded Systems
AN INTRODUCTION TO MICROCONTROLLERS AND EMBEDDED SYSTEMS Tyler Ross Lambert MECH 4240/4250 Supplementary Information Last Revision: 6/7/2017 5:30 PM Summary Embedded systems in robotics are the framework that allows electro-mechanical systems to be implemented into modern machines. The key aspects of this framework are C programming in embedded controllers, circuits for interfacing microcontrollers with sensors and actuators, and proper filtering and control of those hardware components. This document will cover the basics of C/C++ programming, including the basics of the C language in hardware interfacing, communication, and algorithms for state machines and controllers. In order to interface these controllers with the world around us, this document will also cover electrical circuits required to operate controllers, sensors, and actuators accurately and effectively. Finally, some of the more commonly used hardware that is interfaced with microcontrollers is gone over. Table of Contents 1. Introduction ....................................................................................................................................... 4 2. Numbering Systems .......................................................................................................................... 5 3. Variable Types and Memory............................................................................................................. 6 4. Basic C/C++ Notes and Code::Blocks ............................................................................................. -
Today Computers Are All Around Us. from Desktop Computers To
Today computers are all around us. From desktop computers to smartphones, they're changing the way that we live our lives. But have you ever asked yourself what exactly is a computer? A computer is an electronic device that manipulates information or data. The computer sees data as ones and zeros but it knows how to combine them into more complex things such as a photograph, a movie, a website, a game and much more... Computers use a combination of hardware and software. Hardware is any physical part of the computer which includes all of the internal components and also the external parts like the monitor and keyboard. Software is any set of instructions that tells the hardware what to do such as a web browser, media player or word processor. Now when most people say computer, they're talking about a personal computer. This can be a desktop computer or a laptop computer which has basically the same capabilities but in a more portable package. Personal computers come in two main styles, PC and Mac. PCs are the most common types, there are many different companies that make them and they usually come with the Microsoft Windows operating system. Macs or Macintosh computers are all made by one company, Apple, and they come with the Mac OS 10 operating system. Computers come in many other shapes and sizes, mobile phones, tablets, game consoles and even TVs have built-in computers, although they may not do everything a desktop or laptop can. There is another type of computer that plays an important role in our lives, servers. -
Desktop Computer Replacement Program Date: May 22, 2019 From: Information Technology Department Presentation Steve Ely, I.T
CITY COUNCIL AGENDA REPORT MEETING DATE: JUNE 4, 2019 ITEM NUMBER: CC-7 SUBJECT: DESKTOP COMPUTER REPLACEMENT PROGRAM DATE: MAY 22, 2019 FROM: INFORMATION TECHNOLOGY DEPARTMENT PRESENTATION STEVE ELY, I.T. DIRECTOR BY: FOR FURTHER INFORMATION STEVE ELY, I.T. DIRECTOR, 714-754-4891 CONTACT: RECOMMENDATION: Staff recommends that the City Council: 1 . Approve the Desktop Computer Replacement Program for the purchase of 435 desktop computers in three phases to replace the computers that have already reached their end-of-life stage. 2. Approve and authorize the Acting City Manager to execute a purchase order with Dell Marketing, LP. (Dell) in the amount of $166,266.27 for completion of the first phase of the Desktop Computer Replacement Program, which includes the purchase of 140 desktop computers. BACKGROUND: The City purchased 435 desktop computers in 2013. These computers have long passed their life expectancy. Their warranty expired in 2016, which makes them prone to issues and causes staff to have to troubleshoot or make repairs as much as they can. In addition to dedicating time for repairs, parts may become obsolete or costly to obtain, resulting in the necessity to purchase new equipment. Desktop computers are the most heavily used pieces of equipment and upgrading them will allow employees to be more efficient in their daily duties and provide the assurance that data and information will not be lost due to aging equipment. ANALYSIS: Many department computers have exceeded their useful life and become inefficient in performing normal functions. Over time, these resources wear, age, 1 and/or become obsolete, causing performance degradation, excessive support and repair activity, and loss of reliability. -
A Review on Role of Arduino Uno Used in Dual Axis Solar Tracker Rushikesh S.Rakhonde, Pranay R.Lakde, Suraj K.Badwaik, Akshay B.Ronghe, Dipak P
Rushikesh S. Rakhonde, 2021, 9:1 ISSN (Online): 2348-4098 ISSN (Print): 2395-4752 A Review on Role of Arduino Uno Used in Dual Axis Solar Tracker Rushikesh S.Rakhonde, Pranay R.Lakde, Suraj K.Badwaik, Akshay B.Ronghe, Dipak P. Sonule, Asst. Prof. C. J. Shende Department of Mechanical Engg, DESCOET, Dhamangaon (Rly), Maharashtra, India Abstract- The Arduino Uno is an open-source microcontroller board based on the Microchip ATmega328P microcontroller and developed by Arduino.cc. The board is equipped with sets of digital and analog input/output (I/O) pins that may be interfaced to various expansion boards (shields) and other circuits. The board has 14 digital I/O pins (six capable of PWM output), 6 analog I/O pins, and is programmable with the Arduino IDE (Integrated Development Environment), via a type B USB cable. It can be powered by the USB cable or by an external 9-voltThe battery,Arduino thoughproject itwas accepts started voltages at the betweenInteraction 7 and 20 volts. It is similar to the Arduino Nano and Leonardo. The word "uno" means "one" in Italian and was chosen to mark the initial release of Arduino Software. The Uno board is the first in a series of USB- based Arduino boards; it and version 1.0 of the Arduino IDE were the reference versions of Arduino, which have now evolved to newer releases. The ATmega328 on the board comes pre programmed with a boot loader that allows uploading new code to it without the use of an external hardware programmer. Keywords: - Arduino, Expansion Board, USB Cable, Arduino IDE, Microcontroller Board. -
Arduino Uno - R3 (Original - Made in Italy)
Arduino Uno - R3 (Original - Made in Italy) The UNO is the best board to get started with electronics and coding. If this is your first experience tinkering with the platform, the UNO is the most robust board you can start playing with. The UNO is the most used and documented board of the whole Arduino family. Arduino Uno is a microcontroller board based on the ATmega328P (datasheet). It has 14 digital input/output pins (of which 6 can be used as PWM outputs), 6 analog inputs, a 16 MHz quartz crystal, a USB connection, a power jack, an ICSP header and a reset button. It contains everything needed to support the microcontroller; simply connect it to a computer with a USB cable or power it with a AC-to-DC adapter or battery to get started.. You can tinker with your UNO without worring too much about doing something wrong, worst case scenario you can replace the chip for a few dollars and start over again. "Uno" means one in Italian and was chosen to mark the release of Arduino Software (IDE) 1.0. The Uno board and version 1.0 of Arduino Software (IDE) were the reference versions of Arduino, now evolved to newer releases. The Uno board is the first in a series of USB Arduino boards, and the reference model for the Arduino platform; for an extensive list of current, past or outdated boards see the Arduino index of boards. Technical Specifications: Microcontroller ATmega328P Operating Voltage 5V Input Voltage (recommended) 7-12V Input Voltage (limit) 6-20V Digital I/O Pins 14 (of which 6 provide PWM output) PWM Digital I/O Pins 6 Analog Input Pins 6 DC Current per I/O Pin 20 mA DC Current for 3.3V Pin 50 mA Flash Memory 32 KB (ATmega328P) of which 0.5 KB used by bootloader SRAM 2 KB (ATmega328P) EEPROM 1 KB (ATmega328P) Clock Speed 16 MHz LED_BUILTIN 13 Length 68.6 mm Width 53.4 mm Weight 25 g Schematic : Programming The Arduino Uno can be programmed with the (Arduino Software (IDE)). -
Project Documentation
Project Documentation Project Title: e-Glove Team Members: Harshit Rathore, Shubham Agrawal & Elle Atma Vidya Prakash Team Mentors: Rohit Agarwal & Divya Prakash Basic aim: To make a glove embedded with various sensors to detect hand and finger gestures, and implement those in many things, like playing games, giving presentations and many more. Motivation: We were having a look at previous year projects done under the electronics club, we saw many game controllers. So we thought of a game controller that can work for all the latest games, is full featured, and gaming looks more realistic using that. Inspired by things like Microsoft© Kinect™, Sony© Play Station™ motion controller, and many more such controllers available in the market, we came up with this idea. Theory: Sensors 1. Accelerometer: An accelerometer is a device that measures acceleration. When it is kept horizontal at rest, it measures 9.8 N/Kg downward. Whenever there is a tilt, a small component is left at the downward face, which can be detected. 2. Flex Sensor: The flex sensor is basically a variable resistor that reacts to bends. It changes its resistance when flexed so we can measure that change. The bend is only detected in one direction. TO read the data from the sensor, we need a fixed resistor (not changing) that we can use for that comparison (We are using a 33K resistor). This is called a voltage divider and divides the 5v between the flex sensor and the resistor. Microcontroller A microcontroller is a small computer on a single integrated circuit containing a processor core, memory, and programmable input/output peripherals.