History of Andrew Jordan Knives
Total Page:16
File Type:pdf, Size:1020Kb
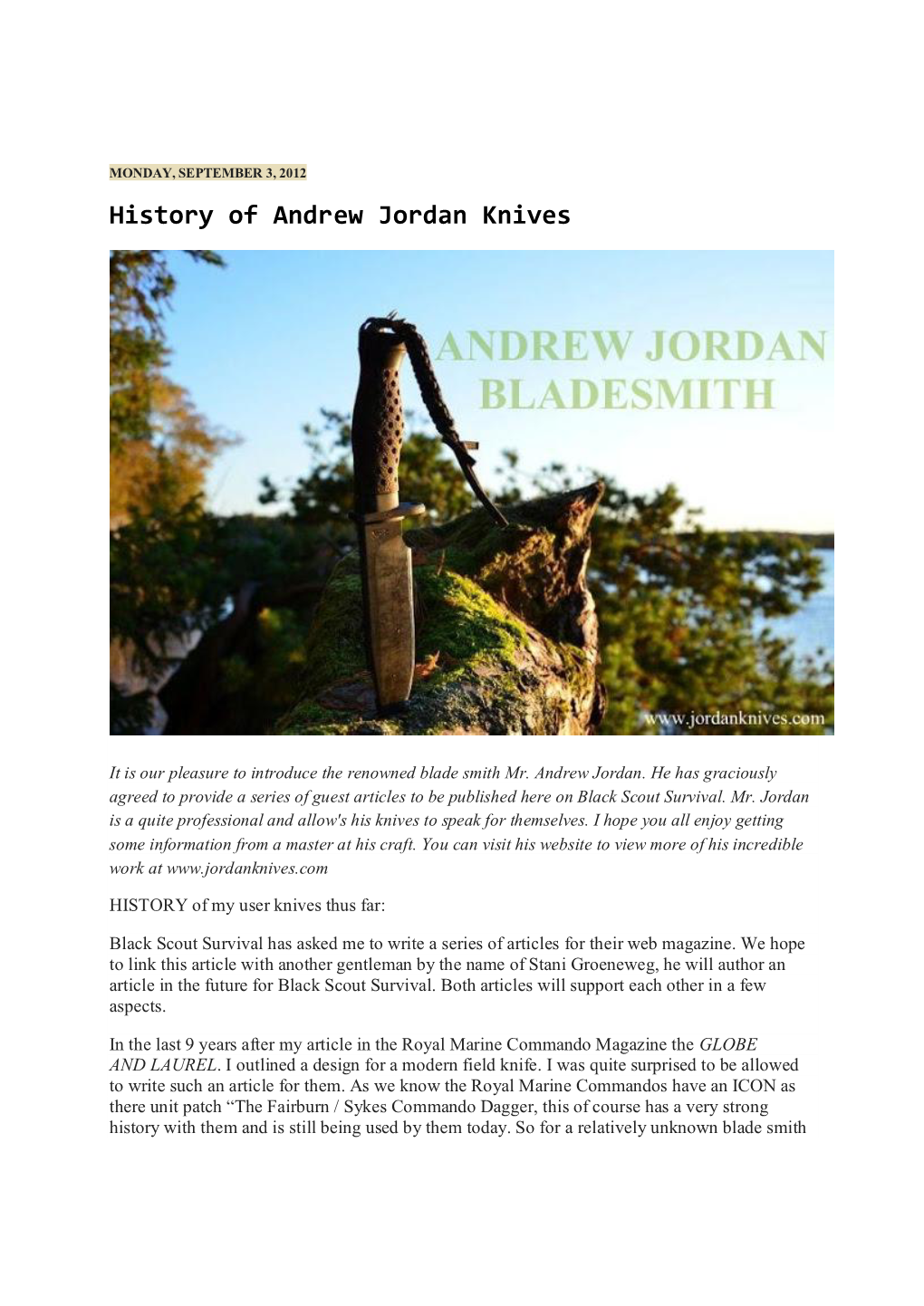
Load more
Recommended publications
-
Fairbairn-Sykes And
©Copyright 2014 by Bradley J. Steiner - ALL RIGHTS RESERVED. SWORD and PEN Official Newsletter of the International Combat Martial Arts Federation (ICMAF) and the Academy of Self-Defense AUGUST 2014 EDITION www.americancombato.com www.seattlecombatives.com www.prescottcombatives.com LISTEN TO OUR RADIO INTERVIEWS! Prof. Bryans and ourself each did 1-hour interviews on the Rick Barnabo Show in Phoenix, Arizona. If you go to prescottcombatives.com, click on “home”. When “news media” drops down, click on that —— and there’re the full interviews! E D I T O R I A L Violence Sometimes Is The Best — And Only Solution THE bromide sounds so good and comfy: “Violence never solves anything!”. That’s why so many people accept it. That’s why they unthinkingly pass it on. That’s why, despite it’s being bullshit, the damn catch phrase has become almost a guide for those poor saps who now live in a feral world and who feel helpless to deal with it. “Well,” they tell themselves, “violence certainly is no solution. We’ve just got to find ways to encourage dialog with troublemakers, and talk out our differences.” The truth is that while always regrettable, recourse to physical force is sometimes desperately necessary and completely justifiable. This fact —— this concept —— was once understood as being axiomatic. No sane person questioned, for example, that the absolute right to self-defense existed for everyone; everywhere, and at all times. Today, a great deal of confusion has been allowed to permeate the minds of formerly sensible people, and we observe such horse manure as “zero tolerance for violence” being announced as policy in the public schools —— making a bully’s victim as culpable as the bully if that victim defends himself. -
Royal Green Jackets (Rifles) Museum Peninsula Barracks, Romsey Road, Winchester
Royal Green Jackets (Rifles) Museum Peninsula Barracks, Romsey Road, Winchester Contact details: 01962 828549 [email protected] Website: https://www.rgjmuseum.co.uk Baggage and Belonging Catalogue 2020 Museum Royal Green Jackets (Rifles) Museum Accession Number 2007.1967 Categories Geological specimens Object name Stones Description Stones picked up by Colour Sergeant Gerald Meredith, King's Royal Rifle Corps, from various locations in Afghanistan, India and Africa Physical description Seven stones affixed to a piece of card titled 'Stones from Afar'. The stones are captioned with significant places including Wazir Akbar Khan's Tomb at Kabul; Jahangir's Tomb; the Bala Hissar, Kabul; and Colenso, Natal near where the son of Field Marshal Earl Roberts was killed. E judgement Meredith, Colour Sergeant Gerald King's Royal Rifle Corps Other associations Afghanistan AFRICA INDIA Research image Baggage and Belonging Catalogue 2020 Museum Royal Green Jackets (Rifles) Museum Accession Number 2008.4087 Categories Flags and banners Object name Standard Description Standard of Afghan origin, described as being ‘captured’ by the 1st Battalion, King's Royal Rifle Corps at the Battle of Kandahar, 1 September 1880, during the Second Anglo-Afghan War, 1878-80, Afghanistan Physical description Large textile comprising stitched panels of red and yellow (possibly faded green), with a red and gold embroidered edge. Names associated King's Royal Rifle Corps Other associations Afghanistan Second Anglo-Afghan War Research image (left) Baggage and Belonging Catalogue 2020 Museum Royal Green Jackets (Rifles) Museum Accession Number 2006.1150 Categories Arms and armour Object name Helmet Description Helmet, possibly of British origin, described as being ‘picked up on the Kandahar battlefield’, fought 1 September 1880, during the Second Anglo-Afghan War, 1878-80, Afghanistan Physical description Brass helmet ornately decorated with lion motif above a central badge featuring two artillery guns and script (possibly Pashto or Dari). -
2012 Gerber Product Reference Guide
2012 GERBER PRODUCT REFERENCE GUIDE TABLE OF CONTENTS PRODUCTS OUTDOOR .............................................................................................................................................. 4 SURVIVAL ......................................................................................................................................... 14 HUNTING .......................................................................................................................................... 35 ESSENTIALS ................................................................................................................................. 54 INDUSTRIAL ................................................................................................................................. 63 TACTICAL ......................................................................................................................................... 68 RETAIL DISPLAYS ..........................................................................................................................75 MERCHANDISE .................................................................................................................................. 77 www.gerbergear.com/germany OUTDOOR CLAM CLAM UPC BOX BOX UPC SPECIFICATIONS HIKING, BIKING, CAMPING, FISHING – WE HAVE A KNIFE OR TOOL FOR EVERY OUTDOOR ACTIVITY. WHEN TESTED IN THE ELEMENTS, GERBER’S OUTDOOR GEAR SHOWS ITS TRUE COLORS - SLEEK, SPORTY DESIGNS CONSTRUCTED WITH RUGGED MATERIALS. DESERTS, MOUNTAINS, FORESTS -
Knife, Combat, Utility the Next Military Issue Survival Knife
Knife, Combat, Utility The next military issue survival knife Standard Issue since World War II Most are familiar with the Air Force & Navy aircrew survival knife with 5 inch fixed blade from Camillus is now manufactured in accordance with U.S. Government specifications by the Ontario Knife Company. In addition, jet pilots and select crew members with ejection capability were issued the MC1 or M724 automatic rescue knife with 3 inch clip point blade and parachute shroud cutter. This knife was issued from 1957 until 1993. In lieu of the MC1, helicopter pilots and crew are issued the Camillus Model 1760 folding pocket knife with their survival vest. This stainless steel knife is equipped with 2.75 inch blade, can opener, cap opener, screw driver, and awl/punch. This folding knife is also standard issue with ground combat elements and has been around since 1945. It has been affectionately known by troops as the Demo Knife. Official Issue Swiss Army Knife The Swiss issued model 1961, a similar knife to the demo is named the Soldier by Victorinox and Standard Issue by Wenger. In 2003, Victorinox released a 111mm series of knifes known as the Trailmaster based on the German Army Knife. Not to be confused with Cold Steel’s Trail Master Bowie Knife, Victorinox renamed this knife Trekker. Offered with a one-handed open blade, the Trekker became very popular in the United States. In 2008 the Trailmaster/Trekker knife was officially adopted by the Swiss Government to replace the Soldier model 1961. The new Soldier features a one-handed serrated locking blade, Philips screwdriver, can opener, small screw driver, bottle opener, large locking screwdriver, wire striper, reamer, wood saw and key ring. -
Pointerview®
MAY 14, 2020 1 WWW.WESTPOINT.EDU THE MAY 14, 2020 VOL. 77, NO. 18 OINTER IEW® DUTY, HONOR, COUNTRY PSERVING THE U.S. MILITARY ACADEMY AND THE COMMUNITY V OF WEST POINT ® SEE INSIDE FOR MORE COVID-19 INFORMATION POINTER VIEW INSIDE & ONLINE WWW . WESTPOINT . EDU / NEWS WWW . POINTERVIEW . COM USMA PAO continues to provide comprehensive resources across the West Point community through the West Point Coronavirus FORSCOM commander webpage at www.westpoint. edu/coronavirus, and it has SEE PAGE 2 released external messages on visits West Point • • USMA social media platforms. (Above) Gen. Michael X. Garrett, commander of U.S. Army Forces Command, observes COVID-19 response training being conducted at Keller Army Community Hospital at West Point May 7. (Bottom right) Garrett toured the hospital’s For more information, contact COVID-19 ward to learn more about the preparations being made prior to the arrival of a task force from the 10th the West Point Public Affairs Mountain Division that will be conducting the U.S. Military Academy’s summer training. (Bottom left) Garrett speaks Office at paoinformation@ to Garrison West Point commander Col. Cecil Marson during his visit. Photos by Brandon O'Connor/PV and Tony Pride/PAO westpoint.edu. See page 3 for Keller Corner updates. See pages 2, 7-11 for Coronavirus-related stories, graphics, updates and activities. See pages 12-16 for Army West Point sports articles. 2 MAY 14, 2020 NEWS & FEATURES POINTER VIEW FORSCOM commander visits West Point, inspects COVID-19 preparations Story and photo by Brandon O’Connor PV Assistant Editor The U.S. -
Cold Steel 1998 Catalog
Performance Warranty We insist all of our knives deliver When it comes to the blade, these include construction. For handles, we strive to develop We stand behind our knives 100%. We extraordinary performance for their asking profile, thickness, blade geometry, edge the perfect mix of materials and ergonomics to subject them to the highest standards in price. In other words, “they must deliver their geometry, steel and heat treatment. Every one offer the most comfortable secure grip available. the industry and strive to make each one moneyʼs worth”. of these factors is studied in great detail to arrive Above all, we TEST what we make! Rigorous as perfect as possible. In order to achieve this goal, we are vitally at the optimum combination for a specific use. testing is the only way to ensure we get the level Our fixed blade sheath knives have a 5 interested in all the elements that are critical to If the knife is a folder, we concentrate on the of performance we demand. year warranty to the original owner against performance. locking mechanism to ensure the strongest, safest defects in materials or workmanship. Our folding knives are warranted for one year. Please remember ANY knife can be broken Tests of Strength & Sharpness or damaged if subjected to sufficient abuse and that all knives eventually wear out (just The Tanto perforating a steel drum. like your boots) and must be replaced. Critics say that practically any knife can Most of the tests shown here be stabbed through a steel drum... but (Right) Retaining a fine edge while are dangerous and they should unlike other knives, the Tantoʼs point is repeatedly cutting pine (wood) not be duplicated. -
2017 Mid-Crkt Catalog-High.Pdf
BREAKTHROUGH “FIELD STRIP” TECHNOLOGY LETS YOU EASILY DISASSEMBLE YOUR KNIFE FOR CLEANING WITHOUT TOOLS. HOMEFRONT™ Designed by Ken Onion in Kaneohe, Hawaii • Breakthrough “Field Strip” Technology Innovation • Field Strip Lets You Easily Disassemble Your Knife for Cleaning Without Tools • AUS 8 Blade Steel with 6061 Aluminum Handles It might look like your grandpa’s classic WWI folder, but it’s got an impressive secret. The new Homefront™ knife is the first in our fleet to feature “Field Strip” technology. This in-field, no-tool take apart capability lets you purge your most reliable companion of a hard day’s grime right where you are, without ever returning to your workbench. K270GKP MSRP: $150.00 Available: July 2016 Blade: Length: 3.502” (88.9 mm) Edge: Plain Steel: AUS 8, HRC 57-58 Finish: Brushed Steel Thickness: 0.133” (3.4 mm) Closed: 4.728” (120 mm) Open: 8.313” (211.1 mm) Weight: 4.8 oz. (136 g) Handle: 6061 Aluminum NEW Style: Folding Knife w/Locking Liner 2017 Field Strip Technology Patent Pending Slide Front Release 1 Lever Up to Disengage Rotate Release Wheel 2Clockwise to Loosen Handle Pull Knife Apart to 3 Easily Clean Simply Reverse the Process to Reassemble the Knife CRKT.COM 2017 PRODUCT PREVIEW JETTISON™ Designed by Robert Carter in Hillister, Texas A sleek and powerful knife with a mighty heritage. The designer of the Jettison™ comes from a • Frame Lock long line of knife craftsmen. With a razor-sharp blade and frame lock, this everyday carry knife • Stonewash Handle stands up to its lineage, and stands apart in a new league of its own. -
OKC Bushcraft Field Knife Updated
NEWS OF OUR CLIENTS 668 Flinn Ave Suite 28 Tel 805 529 3700 Contact: Jonina Costello / [email protected] Moorpark CA 93021 Fax 805 529 3701 Jason Bear / [email protected] Phone: (805) 529-3700 ONTARIO KNIFE COMPANY® INTRODUCES NEW-FOR-2014 BUSHCRAFT FIELD KNIFE™ Classic, Rugged Design Meets Superior Strength for the Ultimate Survival Knife The new-for-2014 Ontario Knife Company® Bushcraft Field Knife maximizes the value of minimalist design. Crafted with high- end carbon steel and a design that is sure to have survivalists, hunters and outdoor enthusiasts lining up to be the first to own one, the OKC Bushcraft Field Knife is the next must have knife — and more. A survival knife is a hunting companion, survival tool, and is at times used for field craft that no blade should ever be expected to perform. Requirements such as these demand a knife that was not just built for the bush, but built by a blademaster. Ontario Knife Company vetted their craftsman well and selected OKC Blademaster-in-Residence Dan Maragni to design the OKC Bushcraft Field Knife. Fans of survival knives are no strangers to Margani’s previous works including Ontario Knife’s SP43 and SP53. However, with the new OKC Bushcraft Field Knife, Maragni may have created his crowning work. The OKC Bushcraft Field Knife was hand-crafted with attention to detail and a focus on the key aspects the Bushcraft community demands in a survival blade, including a hardwood handle and carbon steel blade. Overall, the full-tang OKC Bushcraft Field Knife measures 10.12 inches of robust 5160 carbon steel. -
America's Knife Company
100% MADE IN THE USA AMERICA’S KNIFE COMPANYTM 2016 CATALOG WWW.EMERSONKNIVES.COM “You have committed every crime under the sun. Where you have been the least resisted you have been the most SHEEPDOG brutal. Details found on Page 9 We will have no truce or parley with you, or the grisly gang who work your wicked will. You do your worst and we will do our best.” -Winston Churchill America. Land of the free and the home of the brave. America, the beacon of hope to all those oppressed. Amer- ica, the last refuge of hope to rid the world of evil. You can dislike her. You can criticize her. You can even hate her, but when the time comes, when you are truly in need you know that she will be there for you. She will be the first to fight, the first to spend her most precious resource on your behalf. That call shall come again. And we will be ready. Like we always have. We must be ready. We must gird our loins for the upcoming struggle that we may face. We must be prepared to once again fight the good fight. The enemy will do his worst. America will do her best. I will do my best to help her every way I can. God Bless America, Ernest Emerson “A man who stands by his convictions, never stands alone” -Ernest Emerson WWW.EMERSONKNIVES.COM 310-539-5633 WWW.EMERSONKNIVES.COM 310-539-5633 “The process of evolution does not “When it comes to Tactical Folder Makers, TM none have moved the earth like Ernest Emerson” THE ETAK just apply to animals.” New! BULLDOGS TM Emerson Tactical Assault Knife -Ernest Emerson -Blade Magazine In terms of Tactical Assault Gear and Weaponry there is a long historical record, as old as man himself, of the continuous evolution of strategies, tactics, technology, and weaponry. -
Wilderness Edge Survival Knife
New Wilderness Edge Fighter Pilots' Survival Knife ─ Used by Military in Japan and Poland As seen on the Lost TV series. The Wilderness Edge™ version is the ultimate survival knife and kit. You'll never worry about getting lost in the woods again because the Wilderness Edge™ includes everything you need to catch and prepare food, start a fire, find your way, see in the dark and signal for help. Perfect for military, scouts, preppers, bush crafters, survivalists, or for anyone who wants to be prepared! It contains essential gear to save you from a disaster; it could save your life in an emergency. Knife includes Eagle Claw® split shot and Norwegian Mustad® fishhooks, US-made flies. This system is made from the finest rugged & corrosion-resistant materials. The components of this unique set of wilderness survival tools fit into either the handle or the sheath. It’s a 32-piece multi- functional survival system, including: SPECIFICATIONS: • Full tang 10.5" knife (6" blade) with ripsaw top, 420HC SS, with thumb guards & finger grip • LED splash-Lite submersible flashlight with 20 year lithium battery ꟷ stores in handle • Fast-release knife sheath; converts to fishing pole with reel • 17 pieces including fishing tackle, hooks, swivels, fly, and weights • Nail ─ for punching holes in leather and canvas for lacing • 2 safety pins • Thigh strap, doubles as gear strap • Signal mirror with sight • Small animal snare • Spearhead/arrowhead • Liquid filled compass with lanyard ability slot • Magnesium fire starter stick • Ceramic knife sharpener rod • Survival guide fan card (10 pages) • Drilling thumbscrew drills wood & light metal materials • SKUs: TTKWE01-BR, TTKWE01-BL, Model #’s: WE-1001-BR, WE-1001-BL ADDITIONAL FUNCTIONS: • Flashlight lens works as magnifier • Fishhook & line can be used as needle & thread • Thigh strap can be used as tourniquet • Full tang knife butt can be used for light hammering • Available in brown and black. -
Fallkniven 2012.Pdf
Krut, Jarl and Juni Prestige Knives What distinguishes a Swedish knife? Perhaps the apparently simple design or maybe providing The Volcano Knife is the prestige knife for the a good and safe function, all without frills. The really experienced outfitter. Only those who classic clean lines discern a philosophy that have got the experience from living outdoors honours the skill and experience of the mind, will understand how to use this exceptional where the tool is allowed to play its part but to knife. However, the knife is not only very strong outshine the one that holds the handle - the and holds an edge extremely well, it’s tremen- perfect combination. So it is with Krut, Jarl dously beautiful as well. Since the Volcano knife and Juni, our new sheath knives. Handle of is all handmade, very few Volcano knives will rich curly birch, solid nickel silver fittings and become available thru the coming years. Still, sharp blade of laminated cobalt steel on Krut it’s worth waiting for! Is delivered with a well and laminated powder steel (3G) for Jarl and made black leather sheath, all packed in a solid Juni. The world’s best, in our opinion. A black wood gift box. leather sheath is included. Krut – is an old Swedish soldier name, used around 200 years ago, and should be understood as Blackpowder. Sons of farmers took such names when they joined the Swedish Army around that time. Gentleman’s Pocket Knife appears to be a tra- ditional, slightly old-fashioned pocket knife but if you look at it closely you will find nothing but modern materials and hi-tech solutions. -
Watches Corporate Gifts 2020
WATCHES CORPORATE GIFTS 2020 A SUSTAINABLE SIGNATURE MORE THAN 130 YEARS OF TRADITION AND EXPERIENCE Victorinox creates products which are designed to be true companions for life. Precise and elegantly engineered, our company is proud to represent the distinguished characteristics of our country through the manufacturing of the Swiss Army Knife. They are one of the key symbols of excellent Swiss quality and ingenuity. Still today, the core values upon which our business and manufacturing is based, are as relevant as they were in 1897 when Karl Elsener created the Original Swiss Army Knife: Functionality, innovation, iconic design and uncompromising quality. Victorinox products have accompanied people through life’s adventures since 1884. They are the ambassadors of our timeless Swiss values – as timeless as the classics you will discover on the following pages. Today Victorinox produces more than 120’000 Pocket Tools, Household- and Professional Knives per day. We market our products in 125 countries on all five continents and a considerable part thereof is used as Promotional Gifts. The typical values such as quality, innovation, functionality and iconic design leave a lasting impression and guarantee an unmis- takable and lasting image transfer. Our products are the result of the dedicated work of 2100 individuals who are part of the Victorinox family from around the world. It is the culmination of their contributions which make Victorinox products what they are: unique. We are pleased to offer you in this catalog a carefully selected choice of favored promotional products. We are looking forward to writing the next chapter of our company history together.