Non-Flammable Containment Bag and Enclosure Development for International Space Station Use
Total Page:16
File Type:pdf, Size:1020Kb
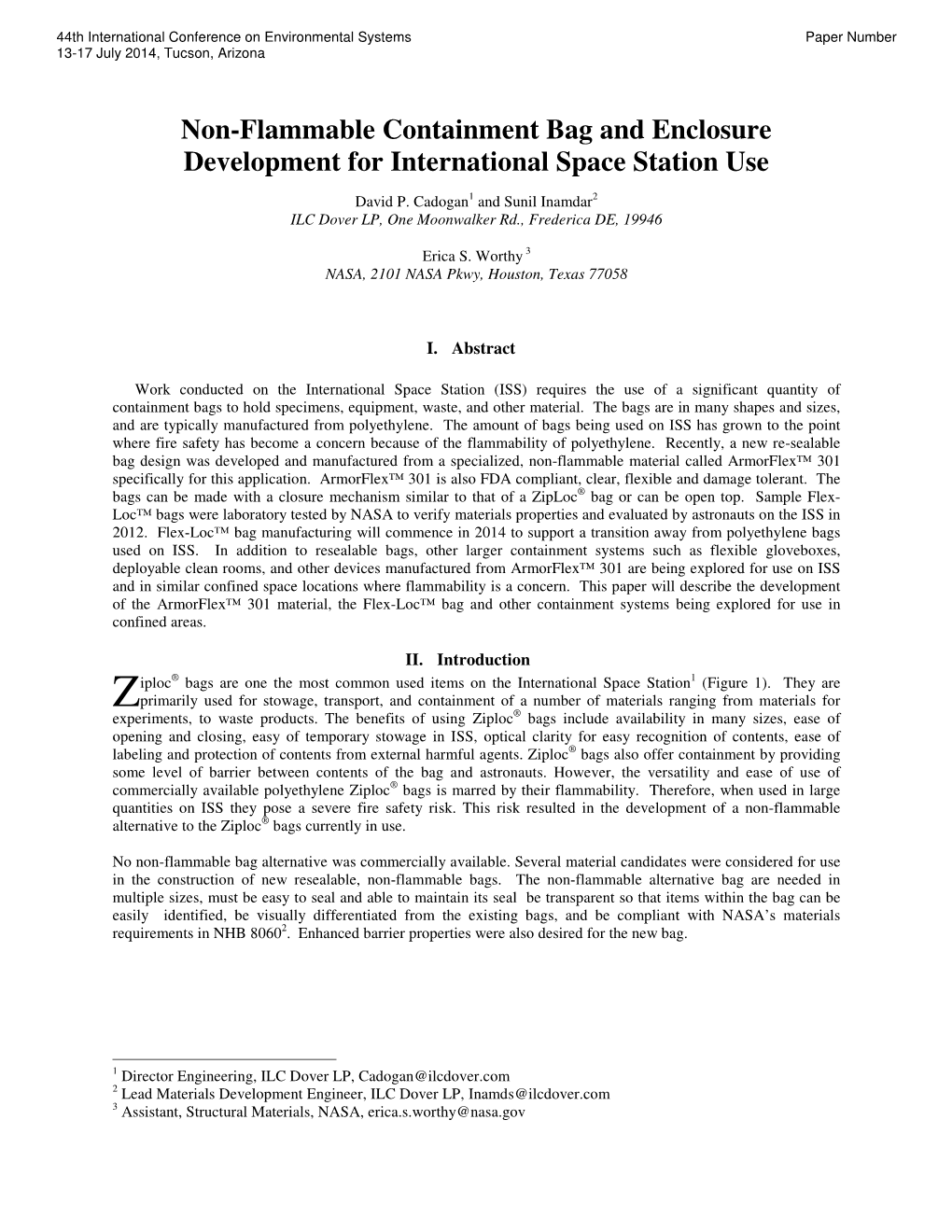
Load more
Recommended publications
-
The Facts About Plastic Bags: Recyclable, Affordable, and Convenient
THE FACTS ABOUT PLASTIC BAGS: RECYCLABLE, AFFORDABLE, AND CONVENIENT Plastic bags are 100% recyclable, reusable, made from natural gas, not oil, and a sustainable choice for consumers, communities and businesses. What’s more, the plastic bag manufacturing and recycling industry is a uniquely American industry that employs more than 30,000 Americans in 349 plants across the country, including more than 1,000 people in Washington state. Bans and taxes on plastic bags are misguided policies that don’t make sense. They don’t help the environment, force less sustainable options, threaten local manufacturing jobs and raise grocery costs for consumers. Instead of banning a reusable, 100% recyclable, American-made product, recycling solutions can help reduce litter, give consumers a choice, and protect American jobs. Plastic grocery bags are the best checkout option for our environment On a per bag basis, plastic bags are more resource efficient, reduce landfill waste and generate fewer greenhouse gas emissions. o They take up a lot less space in a landfill: 1,000 plastic bags weigh 13 pounds; 1,000 paper bags weigh 114 pounds.i o They generate 80 % less waste than paper bags.ii American plastic bags are made from natural gas, NOT oil. In the U.S., 85 percent of the raw material used to make plastic bags is produced from natural gas.iii Recycled plastic bags are used to make new plastic bags and building products, such as backyard decks, playground equipment, and fences. Bans haven’t worked in other places, and don’t protect the environment A ban would make no difference in litter reduction since plastic bags only make up a tiny fraction (less than 0.5 %) of the U.S. -
Boil in Bag Meals a Burner's Laziest and Easiest Option
Boil In Bag Meals A Burner’s laziest and easiest option. Boil‐in‐bag meals are a fantastic option for those of us that want a quick, nutritious home‐made meal on the playa with little‐to‐no waste. Here’s a quick run down of the boil‐in‐bag meal plan I executed in 2009 on the playa. The possibilities are limitless on these and you can tailor them to any diet, taste or hunger level. The basic boil‐in‐bag meal consists of 4 components… 1) A starch‐ rice, couscous or noodles 2) A protein‐ beef, chicken, meatballs, or tofu 3) An accompaniment‐ Veggies, “flavor profile items” (bacon, cherries, mint) and such 4) A sauce There are very specific ways to prepare each of these components so that they (and in turn, the dish) turn out as tasty and appetizing as possible… I will go into these in detail over the next few pages. First there are a few things you will need… a) Vacuum sealer with appropriate bags‐ I’m pretty sure this is the one I got for last year‐> http://www.amazon.com/Seal‐A‐Meal‐VS107‐Vacuum‐Food‐ Sealer/dp/B000KL5IJM/ref=sr_1_5?ie=UTF8&s=kitchen&qid=1279311399&sr= 1‐5 As far as bags go, there are individual 1‐quart bags that work well for single and double serving meals, and larger rolls of bags that you can cut to size and seal for larger meals or fruit/berries b) Large flat trays (aluminum disposable turkey roasting trays or flatter serving pans work best) to freeze the components and a fair amount of freezer space (Chest freezer works great) c) 2 gallon ziplock bags for freezing components d) A LOT of ice trays e) Coolers, dry ice and newspaper. -
Sack the Bag!
BAG RECYCLING INFO Phone: 617-654-6580 Boston, MA02108 1 Winter Street What Happens to Plastic Bags? Most plastic bags and plastic films SACK are recycled into outdoor furniture, decking and railing materials for homes and THE businesses. Approximately 2,250 plastic bags go into one typical 16-foot decking board! BAG! What About Paper Bags? Paper shopping bags are recycled and used in the manufacturing of new grocery bags and cardboard boxes. MASSACHUSETTS RESOURCES CONSUMERS: Find a Plastic Bag Recycling USE FEWER Drop-Off Location DISPOSABLE www.plasticbagrecycling.org SHOPPING BAGS! Massachusetts Department of DISTRIBUTED BY Environmental Protection www.mass.gov/dep/recycle Massachusetts Food Association MASSACHUSETTS FOOD ASSOCIATION www.mafood.com DISPOSABLE SHOPPING BAGS: PROBLEMS & SOLUTIONS In MarchWHAT’S 2009, the BEING Department DONE of HOW YOU CAN HELP REFUSE! In March 2009, the Department of First things first: Do you even need a Environmental Protection (MassDEP) bag? Tell the clerk that you'll carry out and Massachusetts Food Association your handful of items. Be sure to keep (MFA) set a mutual goal of reducing by your receipt handy! one-third the number of paper and plastic shopping bags distributed by MFA’s REDUCE! 500+ member grocery stores and Use disposable shopping bags only supermarkets by the year 2013. when necessary: to keep household soaps and cleaners separate from To achieve this goal, MFA members have foodstuffs, for example. committed to: REUSE! • Promoting the use of reusable bags Bring your own canvas, cloth or Disposable shopping bags contribute • Providing in store plastic bag durable plastic bags. Many grocery to a variety of economic, recycling bins for customers stores offer 5¢ or 10¢ off your order • Offering reusable shopping bags for when you “bring back the sack.” environmental, health and safety problems. -
Inspiredspring 2020 Inspired Living Classy, Fun and Fabulous
front cover LIVE inspiredSPRING 2020 Inspired living Classy, fun and fabulous. Just like you. Inspired home Add a little extra personality to every room. Inspired travel Good things come to those who wander. 2 Thirty-One • Live Inspired Spring 2020 3 Currently Terrazzo The Terrazzo trend has exploded in the last two years, making the leap from floors to fashion prints. Solid backgrounds speckled with colorful “chips” are popping up everywhere like couture confetti. 4 Our Inspired Crossbody Ltd. Get to know the five hottest trends for the season. and Around Town® Tote are just two of the items available in our Terrazzo Pebble. trending Rose Gold Rounded Bags What's old is new again. First used in Fabergé eggs in the 1800s, Rose Gold Circular and half-moon handbags is now associated with spring romances are a huge trend in fashion right and elegant summer weddings. now – like our Half Moon Crossbody shown here. We love their unique A new desire for iridescent fabrics, along shape and how great they look with the Rose Gold trend, inspired our with personalization. new Spring print, Rose Blush Metallic. Like this style? You'll love our Round 3 Utility Tote, too! You can find it on 1 pg. 36 of the Spring Catalog. 5Switching Straps Handbags with interchangeable straps are a new trend offering convenience and affordability. Why buy a whole new bag when you don't have to? Our Wristlet & Crossbody Straps now Shibori come in thin pebble and wide woven Borrowing from ancient textiles is options to create even more looks. -
One Less Bag: Issaquah's Rules
One Less Bag: Issaquah’s Rules 5 cents One Less Bag: FAQ When do the rules go into effect? The rules went into effect July 1, 2014. Why do these rules exist? Using durable, reusable bags on a regular basis has the greatest environmental benefit. What do these rules mean? Disposable plastic bags are no longer allowed for use at retail check-out. Paper bags are allowed, but retailers are required to charge customers a minimum 5 cent charge per bag for larger bags. Retailers may charge a higher amount. Smaller paper bags may be provided for free. Who is affected? All retail establishments, grocery stores, hardware stores, clothing stores, Any retail business that provides retail carryout bags are required to follow this law. Paper bags must be made with a minimum of 40% post consumer recycled material and labeled accordingly. All Are there exemptions? charges for paper bags must be itemized on customer receipts. Food banks and services for low-income households are exempt. Businesses may also apply for temporary Customers using vouchers or electronic benefits from waivers to address unusual circumstances. state or federal food assistance programs are exempt from the 5 cent charge. Bags used within stores, such as bags for produce, bulk foods, meat and seafood, flowers and other similar uses where health, safety and moisture may be a concern, are Where can I learn more? exempt. In addition, bags for newspapers, dry cleaning and plastic bags sold in packages (for garbage or pet Go to issaquahwa.gov/bags or call 425-837-3420. waste, for example) are also exempt. -
3 Color Bag Printing Machine.Cdr
3 color Bag Printing Machine Salient Features Applications Solenoid controlled inking system Plate punch technology Invitation Cards Fully Automatic Wedding Cards Stationery Superior Technology Touch Screen Panel Letter Pads Perfect Registration Envelope Printing Vacuum Front Feeder Question Paper Pneumatic Control Sticker Sheet Instruction Manual Cut Off Valve System Leaets Front Loading System Calendars Short Changeover Time Magazines Tabloid Newspaper etc… Powder Spray D-cut Non-Woven Bags Exhaust Fan for Quick Drying Carry Bags Anti Static System U-cut bags with Side Gusset Shopping bags Centralised Lubrication System Promotional bags Pull Type Side Lay for Micro Adjustment Non-Woven Fabric Sheets Chain delivery System with Receeding Staker Laminated Non-Woven cut sheets 3 color Bag Printing Machine Fairprint 3 Color Sheet Fed Offset is a Break thru’ Innovative Design to deliver Latent needs of Global Consumers for three color printing at optimal investment.3 Color Sheet Fed Offset is compact design and consumes low power as well.This 3 Color Sheet Fed Offset is good for printing calendar, books, stationary, 3 Color Non-woven Bags, 3 Color Non-Woven Fabric sheets & similar applications. This gives good printing registration and printing appearance looks closer to 4 color results. This is easy to run & highly productive. This 3 color non woven bag printing machine is of great caliber and works on traditional effect technology with high-tech and unique features equipped by Fairprint. 3 color bag printing machine is a separate unit technology with 3 sets of plate, blanket and impression cylinder in each unit. in 3 color d cut bag printing machine there are special features like unique suction feeding technology specially designed for feeding non woven bags on offset, automatic impression technology, solenoid based inking control, 3 cylinder technology, transfer drum, pneumatic controls, touch interface and special plate punch technology. -
0.9% Sodium Chloride Injection, USP in MINI-BAG Plus Container VIAFLEX Plastic Container
0.9% Sodium Chloride Injection, USP in MINI-BAG Plus Container VIAFLEX Plastic Container DESCRIPTION 0.9% Sodium Chloride Injection, USP in the MINI-BAG Plus Container is a sterile, nonpyrogenic solution for intravenous administration after admixture with a single dose powdered drug. It contains no antimicrobial agents. The nominal pH is 5.0 (4.5 to 7.0). Each 100 mL contains 900 mg of Sodium Chloride, USP (NaCl). The osmolarity is 308 mOsmol/L (calculated). It contains 154 mEq/L sodium and 154 mEq/L chloride. The MINI-BAG Plus Container is a standard diluent container with an integral drug vial adaptor. It allows for drug admixture after connection to a single dose powdered drug vial having a 20 mm closure. A breakaway seal in the tube between the vial adaptor and the container is broken to allow transfer of the diluent into the vial and reconstitution of the drug. The reconstituted drug is then transferred from the vial into the container diluent and mixed to result in an admixture for delivery to the patient. The VIAFLEX Plastic Container is fabricated from a specially formulated polyvinyl chloride (PL 146 Plastic). Exposure to temperatures above 25°C/77°F during transport and storage will lead to minor losses in moisture content. Higher temperatures lead to greater losses. It is unlikely that these minor losses will lead to clinically significant changes within the expiration period. The amount of water that can permeate from inside the container into the overwrap is insufficient to affect the solution significantly. Solutions in contact with the plastic container can leach out certain chemical components from the plastic in very small amounts. -
Social Learning Experiment: Creating Reusable Bags from Recycled Plastic by Caitlin Prior, [email protected], (269)430-1226
Social Learning Experiment: Creating Reusable Bags from Recycled Plastic By Caitlin Prior, [email protected], (269)430-1226 Project Synopsis: The underlying goal of this project is to promote sustainable living practices in and around Western’s campus. The project itself was to come up with a method, that would be easy to duplicate for any student or faculty, of creating new reusable bags from plastic bags that people have lying around. Attached on the second sheet is a basic how-to-guide to create a grocery tote bag. A workshop will take place on April 15 at the Gibbs Open House. During this workshop I shared the knowledge and taught people how to do the process themselves. Afterwards they will not only have the knowledge and skill to reuse plastic bags but will then be in a mindset of sustainability. From this I hope to create a campus of people that learn from each other and can soon be a sustainably aware campus. Reasons: Americans use around 1 billion shopping bags a year creating 300,000 tons of landfill waste ("Clean Air Council"). Now this number can drop as people slowly start using reusable groceries bags. However there are still the plastic bags people have already collected. Some people may not know where to recycle plastic or the area they are living in may not have a local place to recycle them. This project is designed to get the creative juices flowing and avoid the throwing out old plastic bags that may be slightly dirty or have holes. -
The International Space Station: Decision 2015
The International Space Station: DECISION 2015 Executive Summary The United States should continue its participation in the International Space Station (ISS) program until 2020 or beyond. The nation should support a comprehensive research agenda throughout this time, fully using the unique resources available aboard this orbiting national laboratory. 1. Continued use of the ISS will help the United States maintain its international leadership position in space activities. 2. The United States will demonstrate that it is a reliable collaborator for future international projects by continuing to work with its international partners to capitalize upon the unique, paid-for capabilities of this research platform. 3. The United States can continue to drive innovation by supporting a full research agenda on the ISS with participation from government agencies as well as academic and commercial enterprises. 4. The ISS provides unique facilities and opportunities to carry out research that will better prepare the United States for future long-term space exploration. 5. Education initiatives associated with the ISS, which have already reached more than 31 million students in the United States, will continue to inspire students and enhance U.S. competitiveness by providing hands-on opportunities to learn about math and science. 6. Utilization of the ISS can help the United States nurture its high-tech workforce, with thousands of people across 37 states currently associated with the ISS program, also contributing to global competitiveness. 7. NASA can continue to encourage commercial space development by providing opportunities for commercial operators to undertake ISS resupply missions and other tasks and operations. 8. ISS completion is scheduled for 2010, after which the cost of continuing operations will be relatively low, while the potential benefits to be gained from onboard research and development will be higher than at any previous time. -
Pack a Balanced Pantry Bag
Pack a Balanced Pantry Bag The chart below represents a pantry bag designed to follow MyPyramid nutrition recommendations. The chart shows approximate amounts of food needed to provide: 9 meals (breakfast, lunch and dinner for 3 days) for 1-2 people Food Group Food Type and Serving Size Recommended Quantity Grains Bread (loaf) Rolls/pita/English muffins/bagels/tortilla (bag) Oats, farina, grits (box) 2 items Ready-to-eat cereal (box) Pasta/noodles (1 lb box /bag) Rice (1 lb bag) Vegetables Fresh (one item, ex. carrot, potato, tomato) Can (16 oz) 5-8 items Sauce (jar/can) Frozen (10-16 oz) Choose vegetables high in Vitamin A and Vitamin C. Juice (varies) Fruits Fresh (bunch/bag) 2-3 items Can (29 oz) Frozen (16 oz) Choose fruits high in Vitamin A 100% Juice (46 oz) and Vitamin C. Meats, Poultry & Stews/chili/meatballs (16 oz can) Eggs Chicken-5 oz. (2 cans= 1 item) Frozen meats (1 lb package) 1 item Eggs (1 dozen) Fish, Beans, Tuna/sardines- 6 oz. (2 cans= 1 item) Peanut Butter, Nuts Salmon/mackerel (16 oz can) Dried beans/peas (1 lb bag) 1-2 items Canned beans- (2 cans= 1 item) Peanut butter (18 oz jar) Dairy OR Calcium- Powdered Milk (1 qt envelope) Rich Foods Liquid Milk 1% or non fat (32 oz box) Soy/Almond/Rice milk (1 qt container) 3-4 items Cheese (8 oz package) Sardines/Salmon/Almonds (varies) Collards/Mixed Greens/Broccoli (varies) Fruits and Vegetables High in Vitamins A & C High in Vitamin A High in Vitamin C Fruits Dried Apricots, Apricot, Mango, Orange, Mandarin Oranges, Grapefruit, Peaches, Pineapple, and Watermelon Tangerines, Apricots, Plums, and Raspberries Sweet Potato (Yams), Carrot, Squash, Broccoli, Bell Peppers, Brussels Sprouts, Greens, Spinach, Collards, Cabbage, Cauliflower, Greens, Potatoes, Vegetables Leaf/Romaine Lettuce, Asparagus, Tomatoes, Summer Squash, and Sweet Broccoli, and Tomato Potatoes (Yams) Food Bank For New York City 39 Broadway, 10th Floor, New York, NY 10006 (212) 566-7855 Pack a Balanced Pantry Bag The chart below represents a pantry bag designed to follow MyPyramid nutrition recommendations. -
C a L E N D a R International Space Station
For more information on the International Space Station, visit: www.nasa.gov/station visit: Station, Space International the on information more For www.nasa.gov National Aeronautics and Space Administration INTERNATIONAL SPACE STATION CALENDAR 2011 A MESSAGE FROM THE PROGRAM MANAGER The International Space Station (ISS) is one of the greatest technological, geopolitical and engineering accomplishments in human 2011 history. The completion of the ISS on-orbit assembly allows for a focus on the multifaceted purpose of the ISS, one of scientific research, technology development, exploration and education. As a National Laboratory, the ISS will provide opportunities beyond NASA to academia, commercial entities and other government agencies to pursue their research and development needs in science, technology development and education. With everyone working together, we look forward to extending human presence beyond and improving life here on Earth. This calendar is designed to show all facets of the ISS using displays of astounding imagery and providing significant historical events with the hope of inspiring the next generation. NASA is appreciative of the commitment that America’s educators demonstrate each and every day as they instruct and shape the young students who will be tomorrow’s explorers and leaders. I hope you enjoy the calendar and are encouraged to learn new and exciting aspects about NASA and the ISS throughout the year. Regards, MICHAEL T. SUFFREDINI ISS Program Manager 1 2 2 3 4 6 5 LOOK HOW FAR WE’VE COME 20 JANUARY NASA has powered us into the 21st century through signature 11 accomplishments that are enduring icons of human achievement. -
Polar 20Ltr Thermal Bag Specification 01-09
Polar Thermal Products Ltd Specification : 20 Ltr Thermal Carry Bag A very high quality, durable 20 litre capacity Product Code: P20CB01 thermal carry bag with extreamly high Specification: 001/09 thermal performance. Used for the delivery of temperature controlled product (hot or cold). Can be used with gel packs to extend thermal performace or if being opened and closed regularly. Often used by district medical staff when carrying out vaccinations within the community, or to courier pharmaceutical, medical, blood product or perishable samples between locations. Also used for hot food delivery. Able to keep products within, between within required temperature range for several hours depending on use and whether gel packs are used. All products are waterproof, anti fungal and have root proof stiching CanCbbddithitil be branded with organisation logo and dl colour. Can be supplied with trolley, shoulder strap or document wallet as options. Guarentee All Polartherm products carry a two year guarantee subject to normal wear and tear Specifications Weight empty 0.9297 kgs External surface material Cotton coated PVC Internal lining material Cotton coated PVC Insulation material Patented Polartherm material Insulation thickness 45mm External dimensions width: 400mm height: 330mm depth: 280mm Internal dimensions width: 350mm height: 280mm depth: 230mm Lid type and fixings Zip Number of icepacks supplied None Cold life without opening Over 24hrs, temperature increase at an approximate rate of 0.73°C/hr from 3.5°C at an ambinet temperature of 30°C. Please ask for copy of independent tests. Thermal Conductance (W/m².K) 1.01 ± 0.1 Thermal Conductivity (W/m.K) 0.05 ± 0.005 Made from Polartherm™ - a unique triple layer insulation developed from the NASA space programme.