Design Methodology for Heavy-Lifting Uavs with Co-Axial Rotors
Total Page:16
File Type:pdf, Size:1020Kb
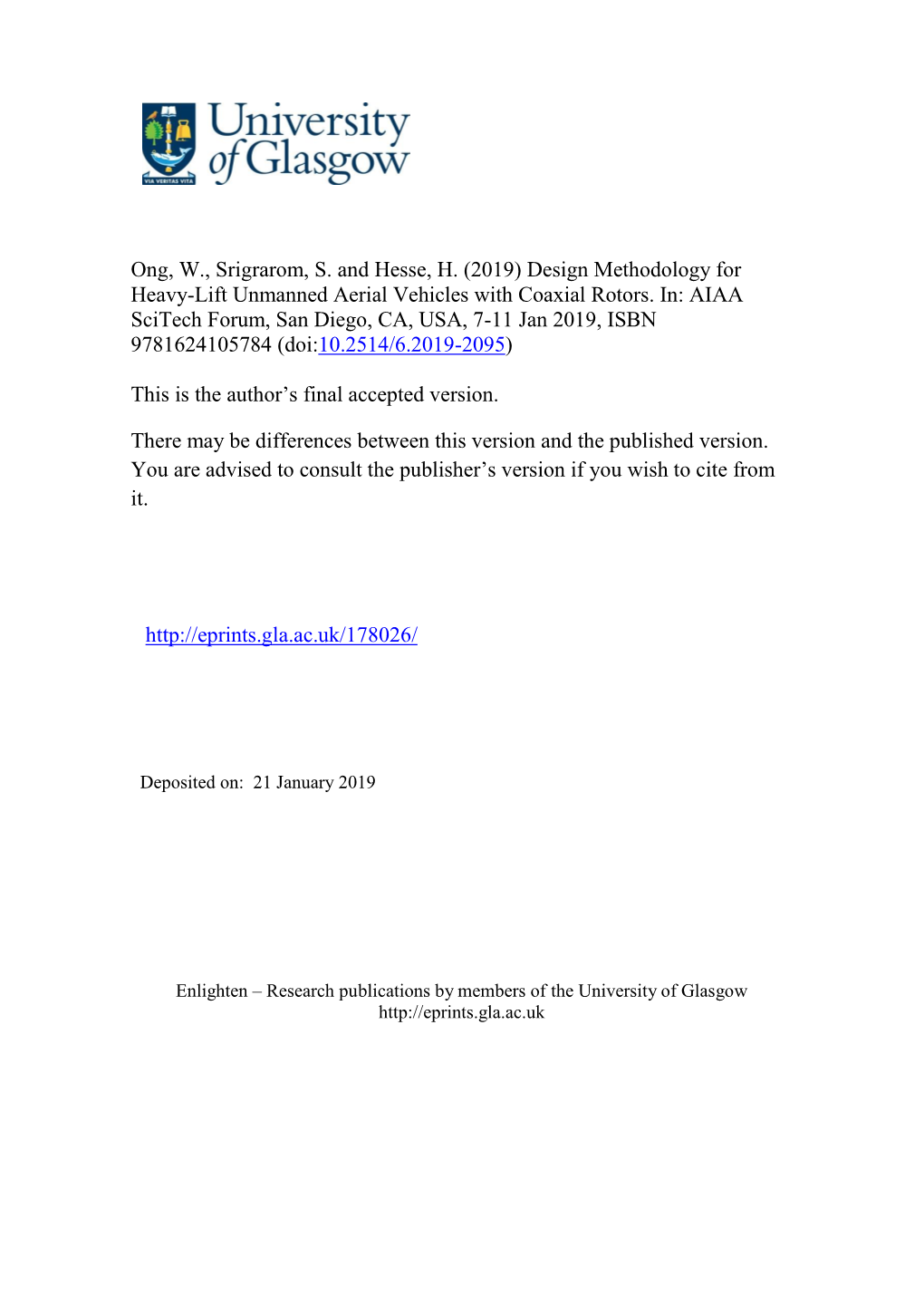
Load more
Recommended publications
-
Effectiveness of the Compound Helicopter Configuration in Rotorcraft Performance Increase
transactions on aerospace research 4(261) 2020, pp.81-106 DOI: 10.2478/tar-2020-0023 eISSN 2545-2835 effectiveness of the compound helicopter configuration in rotorcraft performance increase Jarosław stanisławski Retired doctor of technical sciences [email protected] • ORCID: 0000-0003-1629-4632 abstract The article presents the results of calculations applied to compare flight envelopes of varying helicopter configurations. Performance of conventional helicopter with the main and tail rotors, in the case of compound helicopter, can be improved by applying wings and pusher propellers which generate an additional lift and horizontal thrust. The simplified model of a helicopter structure, consisting of a stiff fuselage and the main rotor treated as a stiff disk, is applied for evaluation of the rotorcraft performance and the required range of control system deflections. The more detailed model of deformable main rotor blades, applying the Galerkin method, is used to calculate rotor loads and blade deformations in defined flight states. The calculations of simulated flight states are performed considering data of a hypothetical medium class helicopter with the take-off mass of 6,000kg. In the case of both of the helicopter configurations, the articulated main rotor hub is taken under consideration. According to the Galerkin method, the elastic blade model allows to compute blade deformations as a combination of the blade bending and torsional eigen modes. Introduction of additional wing and pusher propellers allows to increase the range of operational speed over 300 km/h. Results of the simulation are presented as time- runs of rotor loads and blade deformations and in a form of disk distribution plots of rotor parameters. -
Design and Development of Unmanned Aerial Vehicle (Drone
Design and Development of Unmanned Aerial Vehicle (Drone) for Civil Applications Thesis Project A Thesis submitted to the Dept. of Electrical & Electronic Engineering, BRAC University in partial fulfillment of the requirements for the Bachelor of Science degree in Electrical & Electronic Engineering Project Supervisor Dr. Pran Kanai Saha Project Group A.M. Reasad Azim Bappy - 10110017 MD. Asfak-Ur-Rafi -10321005 MD. Saddamul Islam –11321030 Ali Sajjad - 10321007 Khan Nafis Imran – 10321011 DECLARATION We hereby declare that the thesis titled “Design and Development of Unmanned Aerial Vehicle (Drone) for Civil Applications” is submitted to the Department of Electrical and Electronics Engineering of BRAC University in partial fulfillment of the Bachelor of Science in Electrical and Electronics Engineering. This is work was not submitted elsewhere for the award of any other degree or any other publication. ________________________ ________________________ A.M. Reasad Azim Bappy MD. Asfak-Ur-Rafi-Anonno Student ID : 10110017 Student ID : 10321005 ________________________ ________________________ MD. Saddamul Islam Ali Sajjad Student ID : 11321030 Student ID : 10321007 ________________________ Khan Nafis Imran Student ID : 10321011 Supervisor: _____________________ Dr. Pran Kanai Saha Professor, Department of Electrical and Electronic Engineering, BUET, Dhaka-1000, Bangladesh. i Acknowledgement Foremost, we would like to express our sincere gratitude to our advisor, Dr. Pran Kanai Saha, Professor, Department of Electrical and Electronic Engineering, -
Micro Coaxial Helicopter Controller Design
Micro Coaxial Helicopter Controller Design A Thesis Submitted to the Faculty of Drexel University by Zelimir Husnic in partial fulfillment of the requirements for the degree of Doctor of Philosophy December 2014 c Copyright 2014 Zelimir Husnic. All Rights Reserved. ii Dedications To my parents and family. iii Acknowledgments There are many people who need to be acknowledged for their involvement in this research and their support for many years. I would like to dedicate my thankfulness to Dr. Bor-Chin Chang, without whom this work would not have started. As an excellent academic advisor, he has always been a helpful and inspiring mentor. Dr. B. C. Chang provided me with guidance and direction. Special thanks goes to Dr. Mishah Salman and Dr. Humayun Kabir for their mentorship and help. I would like to convey thanks to my entire thesis committee: Dr. Chang, Dr. Kwatny, Dr. Yousuff, Dr. Zhou and Dr. Kabir. Above all, I express my sincere thanks to my family for their unconditional love and support. iv v Table of Contents List of Tables ........................................... viii List of Figures .......................................... ix Abstract .............................................. xiii 1. Introduction .......................................... 1 1.1 Vehicles to be Discussed................................... 1 1.2 Coaxial Benefits ....................................... 2 1.3 Motivation .......................................... 3 2. Helicopter Flight Dynamics ................................ 4 2.1 Introduction ........................................ -
Open Walsh Thesis.Pdf
The Pennsylvania State University The Graduate School College of Engineering A PRELIMINARY ACOUSTIC INVESTIGATION OF A COAXIAL HELICOPTER IN HIGH-SPEED FLIGHT A Thesis in Aerospace Engineering by Gregory Walsh c 2016 Gregory Walsh Submitted in Partial Fulfillment of the Requirements for the Degree of Master of Science August 2016 The thesis of Gregory Walsh was reviewed and approved∗ by the following: Kenneth S. Brentner Professor of Aerospace Engineering Thesis Advisor Jacob W. Langelaan Associate Professor of Aerospace Engineering George A. Lesieutre Professor of Aerospace Engineering Head of the Department of Aerospace Engineering ∗Signatures are on file in the Graduate School. Abstract The desire for a vertical takeoff and landing (VTOL) aircraft capable of high forward flight speeds is very strong. Compound lift-offset coaxial helicopter designs have been proposed and have demonstrated the ability to fulfill this desire. However, with high forward speeds, noise is an important concern that has yet to be thoroughly addressed with this rotorcraft configuration. This work utilizes a coupling between the Rotorcraft Comprehensive Analysis System (RCAS) and PSU-WOPWOP, to computationally explore the acoustics of a lift-offset coaxial rotor sys- tem. Specifically, unique characteristics of lift-offset coaxial rotor system noise are identified, and design features and trim settings specific to a compound lift-offset coaxial helicopter are considered for noise reduction. At some observer locations, there is constructive interference of the coaxial acoustic pressure pulses, such that the two signals add completely. The locations of these constructive interferences can be altered by modifying the upper-lower rotor blade phasing, providing an overall acoustic benefit. -
Ka-50 Attack Helicopter Acrobatic Flight
24 EUROPEAL'J ROTORCRAFT FORUM Marseilles, France -15th_l i 11 September 1998 ADOS Ka-50 Attack Helicopter Acrobatic Flight Serguey V. Mikheyev, Boris N. Bourtsev, Serguey V. Selemenev Kamov Company, Moscow Region, Russia I. Introduction The Ka-50 attack helicopter is intended to act against both ground and air targets. High maneuverability of the Ka-50 helicopter provides lower own vulnerability in combat. Aerobatic t1ight demonstrates maneuverability of the helicopter. This is effected by validity of the key solution in the helicopter designing. KAMOV Company helicopter experience concentrates in the Ka-50 attack helicopter. The Table No.1 lists basic types of the serial and experimental helicopters which have been developed by K.AJ\10V Company within the 50 years period. This paper consists of presentations on the following subjects: basic technical solutions and aeroelastic phenomena; examination of test t1ight results; maneuverability features; means of aerobatic t1ight monitoring and analysis. 2.Basic technical solutions and aeroelastic phenomena It is very important to have a substantiation of aeromechanical phenomena. This is feasible given adequate mathematical models making possible to explain and forecast : natural frequencies of structures; loads; aeroelastic stability limits ; helicopter performance . KAL'v!OV Company has developed software to simulate a coaxial rotor aeroelasticity [1,2,4,5]. Aeroelastic phenomena to be simulated are shown in the Fig.2 as ( 1-7) lines in the following way: ( 1) - system of equations of rotor blades motion ; (2) - elastic model of coaxial rotor control linkage ; (3) - model of coaxial rotor vortex wake; (4,5,6)- unsteady aerodynamic data of airfoils; (7) - elastic /mass I geometry data of the upper/lower rotor blades and of the hubs. -
Wake Interactions of a Tetrahedron Quadcopter
Wake Interactions Of A Tetrahedron Quadcopter Item Type Conference Paper Authors Epps, Jeremy; Garanger, Kevin; Feron, Eric Citation Epps, J., Garanger, K., & Feron, E. (2020). Wake Interactions Of A Tetrahedron Quadcopter. 2020 International Conference on Unmanned Aircraft Systems (ICUAS). doi:10.1109/ icuas48674.2020.9214004 Eprint version Pre-print DOI 10.1109/icuas48674.2020.9214004 Publisher Institute of Electrical and Electronics Engineers (IEEE) Rights Archived with thanks to IEEE Download date 07/10/2021 07:44:05 Link to Item http://hdl.handle.net/10754/667639 Wake Interactions Of A Tetrahedron Quadcopter Jeremy Epps1, Kévin Garanger1;2, Eric Feron1;2 Abstract— This paper studies the influence of the place- tetrahedron structure was chosen as the airframe of the ment of a quadcopter’s rotors with a tetrahedron shape on vehicle because of its known structural strength and its produced thrust. A tetrahedron quadcopter is a rotorcraft rigidity [4], allowing it to be used as the building block of with four horizontal rotors, including an upper rotor and three lower rotors placed equidistant around the upper rotor a self-similar assembly inspired by fractals. Fig. 1 shows on a lower plane. The goal of this aircraft design is to create the prototype of the module, named Tetracopter, as built an airframe that is structurally rigid in 3-dimensions while by the authors. being as efficient as an aircraft that has its rotors onthe same vertical plane. Due to the wake interaction between the top and bottom propellers, a reduction of thrust is expected compared to a placement of the rotors on the same plane when rotors are close enough. -
Graduation Project September 2020
ISTANBUL TECHNICAL UNIVERSITY FACULTY OF AERONAUTICS AND ASTRONAUTICS PERFORMANCE CALCULATION FOR HELICOPTER BLADE UNDER HOVER CONDITION GRADUATION PROJECT Hüseyin DİKEL Department of Aeronautical Engineering Thesis Advisor: Assis. Prof. Dr. Özge ÖZDEMİR SEPTEMBER 2020 i ISTANBUL TECHNICAL UNIVERSITY FACULTY OF AERONAUTICS AND ASTRONAUTICS PERFORMANCE CALCULATION FOR HELICOPTER BLADE UNDER HOVER CONDITION GRADUATION PROJECT Hüseyin DİKEL (110150005) Department of Aeronautıcal Engineering Thesis Advisor: Assis. Prof. Dr. Özge ÖZDEMİR SEPTEMBER 2020 iii Hüseyin DİKEL, student of ITU Faculty of Aeronautics and Astronautics student ID 110150005, successfully defended the graduation entitled “PERFORMANCE CALCULATION FOR HELICOPTER BLADE UNDER HOVER CONDITION” which he prepared after fulfilling the requirements specified in the associated legislations, before the jury whose signatures are below. Thesis Advisor: Assis. Prof. Dr. Özge ÖZDEMİR .............................. İstanbul Technical University Jury Members: Prof. Dr. Metin Orhan KAYA ............................... İstanbul Technical University Prof. Dr. Zahit MECİTOĞLU ............................... İstanbul Technical University Date of Submission : 07 September 2020 Date of Defense : 14 September 2020 v To my big family, iii iv FOREWORD Önsöz bölümünün içerisindeki metinler 1 satır aralıklı yazılır. Tezin ilk sayfası niteliğinde yazılan önsöz ikisayfayı geçmez. Tezi destekleyen kurumlara ve yardımcı olan kişilere bu kısımdateşekkür edilir. Önsöz metninin altında sağa dayalı olarak -
Identification of Coaxial-Rotors Dynamic Wake Inflow for Flight Dynamics and Aeroelastic Applications
42st European Rotorcraft Forum 2016 IDENTIFICATION OF COAXIAL-ROTORS DYNAMIC WAKE INFLOW FOR FLIGHT DYNAMICS AND AEROELASTIC APPLICATIONS Felice Cardito, Riccardo Gori, Giovanni Bernardini Jacopo Serafini, Massimo Gennaretti Department of Engineering, University Roma Tre, Rome, Italy Abstract This paper presents the development of a linear, finite-state, dynamic perturbation model for wake inflow of coaxial rotors in arbitrary steady flight, based on high-accuracy radial and azimuthal representations. It might conveniently applied in combination with blade element formulations for rotor aeroelastic mod- elling, where three-dimensional, unsteady multiharmonic and localized aerodynamic effects may play a crucial role. The proposed model is extracted from responses provided by an arbitrary high-fidelity CFD solver to perturbations of rotor degrees of freedom and controls. The transfer functions of the multihar- monic responses are then approximated through a rational-matrix approach, which returns a constant coefficient differential operator relating the inflow multiharmonic coefficients to the inputs. The accuracy of the model is tested both for hovering and forward flight by comparison with the wake inflow directly evaluated by the high-fidelity CFD tool for arbitrary inputs. 1. INTRODUCTION ing the need for a tail rotor and its associated shafting and gearboxes. Due to the improved performance they may provide, coaxial rotors are expected to become a common solu- While coaxial rotors have been investigated since the tion for next-generation rotorcraft. -
High-Fidelity Modeling of Multirotor Aerodynamic Interactions for Aircraft Design
Brigham Young University BYU ScholarsArchive Faculty Publications 2020-8 High-Fidelity Modeling of Multirotor Aerodynamic Interactions for Aircraft Design Eduardo Alvarez Brigham Young University, [email protected] Andrew Ning Brigham Young University, [email protected] Follow this and additional works at: https://scholarsarchive.byu.edu/facpub Part of the Mechanical Engineering Commons BYU ScholarsArchive Citation Alvarez, Eduardo and Ning, Andrew, "High-Fidelity Modeling of Multirotor Aerodynamic Interactions for Aircraft Design" (2020). Faculty Publications. 4179. https://scholarsarchive.byu.edu/facpub/4179 This Peer-Reviewed Article is brought to you for free and open access by BYU ScholarsArchive. It has been accepted for inclusion in Faculty Publications by an authorized administrator of BYU ScholarsArchive. For more information, please contact [email protected], [email protected]. Postprint version of the article published by AIAA Journal, Aug 2020, DOI: 10.2514/1.J059178. The content of this paper may differ from the final publisher version. The code used in this study is available at github.com/byuflowlab/FLOWUnsteady. High-fidelity Modeling of Multirotor Aerodynamic Interactions for Aircraft Design Eduardo J. Alvarez ∗ and Andrew Ning.† Brigham Young University, Provo, Utah, 84602 Electric aircraft technology has enabled the use of multiple rotors in novel concepts for urban air mobility. However, multirotor configurations introduce strong aerodynamic and aeroacoustic interactions that are not captured through conventional aircraft design tools. In this paper we explore the capability of the viscous vortex particle method (VPM) to model multirotor aerodynamic interactions at a computational cost suitable for conceptual design. A VPM-based rotor model is introduced along with recommendations for numerical stability and computational efficiency. -
Rotor Diameter
Scaling Up Success The SB>1 Defiant Joint Multi-Role Technology Demonstrator challenges Sikorsky and Boeing to grow the integrated X2 technologies By Frank Colucci peed and range improvements The SB>1 Defiant JMR Technology Demonstrator scales up Sikorsky X2 rigid coaxial rotor sought by US Army Aviation drove compound helicopter technologies to achieve speed, range and agility far better than SSikorsky, Boeing and their Defiant conventional helicopters. (Sikorsky graphic) team to scale up technologies flown on the 6,000 lb (3 t) X2 and 11,400 lb The MPS summary of FVL-M teams, Sikorsky Innovations vice (5.2 t) S-97 to the 30,000 lb (14 t) class performance includes cruising president Chris Van Buiten previously SB>1 Joint Multi-Role Technology speeds greater than 230 kt (426 stated, “Raider is risk-reduction for JMR.” Demonstrator (JMR-TD). A Systems km/h), vertical takeoff at 6,000 ft/95˚F Sikorsky and Boeing teamed Integration Laboratory (SIL) for Defiant (1,800 m/35˚C) density altitude and up on the SB>1 Defiant in January came on line in December and a a combat radius of 229 nm (424 km) 2013. Boeing program co-director Transmission System Test Bed will run with four crew and 12 troops. The 250 Pat Donnelly said, “When we put in 2016. The JMR-TD due to fly in 2017 is kt (463 km/h) Defiant answers the this together, we were certainly very based on a 2013 Mission Performance specification with rigid coaxial rotors, sensitive to the scaling issues of the Specification (MPS) for a medium-size an integrated tail propeller, optimized X2 technology. -
Bandwidth Assessment for Multirotor Uavs
Gastone Ferrarese DOI 10.1515/ama-2017-0023 Bandwidth Assessment for MultiRotor UAVs BANDWIDTH ASSESSMENT FOR MULTIROTOR UAVs Gastone FERRARESE* *Faculty of Engineering, Department of Industrial Engineering, University of Bologna, Via Risorgimento 2, 40136, Bologna, Italy [email protected] received 14 July 2016, revised 29 May 2017, accepted 31 May 2017 Abstract: This paper is a technical note about the theoretical evaluation of the bandwidth of multirotor helicopters. Starting from a mathematical linear model of the dynamics of a multirotor aircraft, the transfer functions of the state variables that deeply affect the stability characteristics of the aircraft are obtained. From these transfer functions, the frequency response analysis of the system is effected. After this analysis, the bandwidth of the system is defined. This result is immediately utilized for the design of discrete PID controllers for hovering flight stabilization. Numeric simulations are shown to demonstrate that the knowledge of the bandwidth is a valid aid in the design of flight control systems of these machines. Key words: Multirotor, PID, Attitude Stabilization, Flight Control, Bandwidth 1. INTRODUCTION as Padfield (1996) clearly stated in his capital book. Unfortunately, a rigorous study of this parameter for multi--rotor aircraft is not yet available in literature. Multirotor helicopters are Vertical Take Off and Landing This technical note is the first attempt to fill this void. An ana- (VTOL) flying vehicles that have gained, in the very last years, the lytic method to find the bandwidth of a multirotor helicopter is de- attention of both academic research institutions and commercial scribed. This result is based on the study of the frequency re- companies. -
Optimal-Time Quadcopter Descent Trajectories Avoiding the Vortex Ring and Autorotation States
1 Optimal-time Quadcopter Descent Trajectories Avoiding the Vortex Ring and Autorotation States Amin Talaeizadeha, Duarte Antunesb;∗, Hossein Nejat Pishkenaria;∗ and Aria Alastya Abstract—It is well-known that helicopters descending fast attention in the context of quadcopters, despite the fact that may enter the so-called Vortex Ring State (VRS), a region they can play a very important role due to their agility. Some in the velocity space where the blades lift differs significantly exceptions are [8]–[16]. from regular regions. This may lead to instability and therefore this region is avoided, typically by increasing the horizontal In [8] it is reported that for descending trajectories and for speed. This paper researches this phenomenon in the context of some velocity state space regions a quadcopter can become small-scale quadcopters. The region corresponding to the VRS unstable. Other studies show that these instabilities are due is identified by combining first-principles modeling and wind- to the VRS effects, see [9]–[11], where simple models are tunnel experiments. Moreover, we propose that the so called defined for explaining the boundary of these regions. These Windmill-Brake State (WBS) or autorotation region should also be avoided for quadcopters, which is not necessarily the case simple models are similar to helicopter models and are used for helicopters. A model is proposed for the velocity constraints in some works to design controllers that avoid entering the that the quadcopter must meet to avoid these regions. Then, VRS [12]–[16]. In fact, these studies are similar to helicopter the problem of designing optimal time descend trajectories that VRS avoiding controllers introduced in [17], [18].