PROPULSION SYSTEMS for HYPERSONIC FLIGHT 1. Introduction
Total Page:16
File Type:pdf, Size:1020Kb
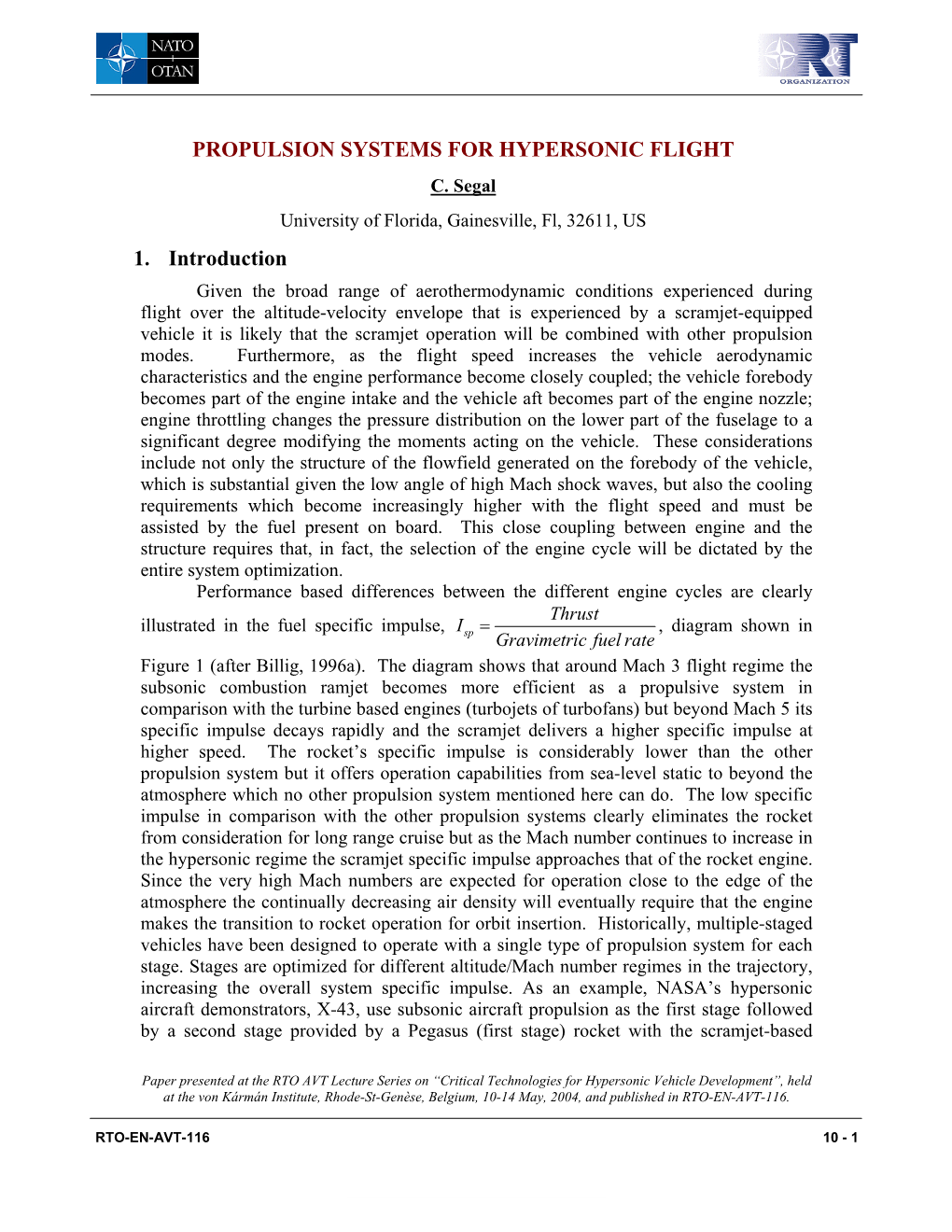
Load more
Recommended publications
-
Aircraft Engine Performance Study Using Flight Data Recorder Archives
Aircraft Engine Performance Study Using Flight Data Recorder Archives Yashovardhan S. Chati∗ and Hamsa Balakrishnan y Massachusetts Institute of Technology, Cambridge, Massachusetts, 02139, USA Aircraft emissions are a significant source of pollution and are closely related to engine fuel burn. The onboard Flight Data Recorder (FDR) is an accurate source of information as it logs operational aircraft data in situ. The main objective of this paper is the visualization and exploration of data from the FDR. The Airbus A330 - 223 is used to study the variation of normalized engine performance parameters with the altitude profile in all the phases of flight. A turbofan performance analysis model is employed to calculate the theoretical thrust and it is shown to be a good qualitative match to the FDR reported thrust. The operational thrust settings and the times in mode are found to differ significantly from the ICAO standard values in the LTO cycle. This difference can lead to errors in the calculation of aircraft emission inventories. This paper is the first step towards the accurate estimation of engine performance and emissions for different aircraft and engine types, given the trajectory of an aircraft. I. Introduction Aircraft emissions depend on engine characteristics, particularly on the fuel flow rate and the thrust. It is therefore, important to accurately assess engine performance and operational fuel burn. Traditionally, the estimation of fuel burn and emissions has been done using the ICAO Aircraft Engine Emissions Databank1. However, this method is approximate and the results have been shown to deviate from the measured values of emissions from aircraft in operation2,3. -
Module 1: Hypersonic Atmosphere Lecture1: Characteristics of Hypersonic Atmosphere
NPTEL –Aerospace Module 1: Hypersonic Atmosphere Lecture1: Characteristics of Hypersonic Atmosphere 1.1 Introduction Hypersonic flight has special traits, some of which are seen in every hypersonic flight. Presence of these particular features during a flight is highly dependant on type of trajectory, configuration etc. In short it is the mission requirement which decides the nature of hypersonic atmosphere encountered by the flight vehicle. Some missions are designed for high deceleration in outer atmosphere during reentry. Hence, those flight vehicles experience longer flight duration at high angle of attacks due to which blunt nosed configuration are generally preferred for such aircrafts. On the contrary, some missions are centered on low flight duration with major deceleration closer to earth surface hence these vehicles have sharp nose and low angle of attack flights. Reentry flight path of hypersonic vehicle is thus governed by the parameters called as ballistic parameter and lifting parameter. These parameters are obtained by applying momentum conservation equation in the direction of the flight path and normal to it. Velocity-altitude map of the flight is thus made from the knowledge of these governing flight parameters, weight and surface area. Ballistic parameter is considered for non lifting reentry flights like flight path of Apollo capsule, however lifting parameter is considered for lifting reentry trajectories like that of space shuttle. Therefore hypersonic flight vehicles are classified in four different types based on the design constraints imposed from mission specifications. 1. Reentry Vehicles (RV): These vehicles are typically launched using rocket propulsion system. Reentry of these vehicles is controlled by control surfaces. -
Notes on Earth Atmospheric Entry for Mars Sample Return Missions
NASA/TP–2006-213486 Notes on Earth Atmospheric Entry for Mars Sample Return Missions Thomas Rivell Ames Research Center, Moffett Field, California September 2006 The NASA STI Program Office . in Profile Since its founding, NASA has been dedicated to the • CONFERENCE PUBLICATION. Collected advancement of aeronautics and space science. The papers from scientific and technical confer- NASA Scientific and Technical Information (STI) ences, symposia, seminars, or other meetings Program Office plays a key part in helping NASA sponsored or cosponsored by NASA. maintain this important role. • SPECIAL PUBLICATION. Scientific, technical, The NASA STI Program Office is operated by or historical information from NASA programs, Langley Research Center, the Lead Center for projects, and missions, often concerned with NASA’s scientific and technical information. The subjects having substantial public interest. NASA STI Program Office provides access to the NASA STI Database, the largest collection of • TECHNICAL TRANSLATION. English- aeronautical and space science STI in the world. language translations of foreign scientific and The Program Office is also NASA’s institutional technical material pertinent to NASA’s mission. mechanism for disseminating the results of its research and development activities. These results Specialized services that complement the STI are published by NASA in the NASA STI Report Program Office’s diverse offerings include creating Series, which includes the following report types: custom thesauri, building customized databases, organizing and publishing research results . even • TECHNICAL PUBLICATION. Reports of providing videos. completed research or a major significant phase of research that present the results of NASA For more information about the NASA STI programs and include extensive data or theoreti- Program Office, see the following: cal analysis. -
Propulsion Controls at NASA Lewis
Aircraft Turbine Engine Control Research at NASA Glenn Research Center Dr. Sanjay Garg Chief, Intelligent Control and Autonomy Branch Ph: (216) 433-2685 FAX: (216) 433-8990 email: [email protected] http://www.grc.nasa.gov/WWW/cdtb Glenn Research Center Intelligent Control and Autonomy Branch at Lewis Field Outline – The Engine Control Problem • Safety and Operational Limits • State-of-the-Art Engine Control Logic Architecture – Historical Glenn Research Center Contributions • Early Stages of Turbine Engine Control (1945-1960s) • Maturation of Turbine Engine Control (1970-1990) – Advanced Engine Control Research • Recent Significant Accomplishments (1990- 2004) • Current Research (2004 onwards) – Conclusion Glenn Research Center Intelligent Control and Autonomy Branch at Lewis Field Basic Engine Control Concept • Objective: Provide smooth, stable, and stall free operation of the engine via single input (PLA) with no throttle restrictions • Reliable and predictable throttle movement to thrust response • Issues: • Thrust cannot be measured • Changes in ambient condition and aircraft maneuvers cause distortion into the fan/compressor • Harsh operating environment – high temperatures and large vibrations • Safe operation – avoid stall, combustor blow out etc. • Need to provide long operating life – 20,000 hours • Engine components degrade with usage – need to have reliable performance throughout the operating life Glenn Research Center Intelligent Control and Autonomy Branch at Lewis Field Basic Engine Control Concept • Since Thrust (T) -
Aerospace Engine Data
AEROSPACE ENGINE DATA Data for some concrete aerospace engines and their craft ................................................................................. 1 Data on rocket-engine types and comparison with large turbofans ................................................................... 1 Data on some large airliner engines ................................................................................................................... 2 Data on other aircraft engines and manufacturers .......................................................................................... 3 In this Appendix common to Aircraft propulsion and Space propulsion, data for thrust, weight, and specific fuel consumption, are presented for some different types of engines (Table 1), with some values of specific impulse and exit speed (Table 2), a plot of Mach number and specific impulse characteristic of different engine types (Fig. 1), and detailed characteristics of some modern turbofan engines, used in large airplanes (Table 3). DATA FOR SOME CONCRETE AEROSPACE ENGINES AND THEIR CRAFT Table 1. Thrust to weight ratio (F/W), for engines and their crafts, at take-off*, specific fuel consumption (TSFC), and initial and final mass of craft (intermediate values appear in [kN] when forces, and in tonnes [t] when masses). Engine Engine TSFC Whole craft Whole craft Whole craft mass, type thrust/weight (g/s)/kN type thrust/weight mini/mfin Trent 900 350/63=5.5 15.5 A380 4×350/5600=0.25 560/330=1.8 cruise 90/63=1.4 cruise 4×90/5000=0.1 CFM56-5A 110/23=4.8 16 -
The Propulsion of Sea Ships – in the Past, Present and Future –
The Propulsion of Sea Ships – in the Past, Present and Future – (Speech by Bernd Röder on the occasion of the VHT General Meeting on 11.12.2008) To prepare for today’s topic, more specifically for the topic: ship propulsion of the future, I did what every reasonable person would have done in my situation if he should have a look into the future – I dug out our VHT crystal ball. As you know, our crystal ball is a reliable and cost-efficient resource which we have been using for a long time with great suc- cess. Among other things, we’ve been using it to provide you with the repair costs or their duration or the probable claims experience of a policy, etc. or to create short-term damage statistics, as well. So, I asked the crystal ball: What does ship propulsion of the future look like? Every future and all statistics lie in the crystal ball I must, however, admit that what I saw there was somewhat irritating, and it led me to only the one conclusion – namely, that we’re taking a look into the very distant future at a time in which humanity has not only used up all of the oil reserves but also the entire wind. This time, we’re not really going to get any further with the crystal ball. Ship propulsion of the future or 'back to the roots'? But, sometimes it helps to have a look into the past to be able to say something about the fu- ture. According to the principle, draw a line connecting the distant past to today and simply extend it into the future. -
Rocket Nozzles: 75 Years of Research and Development
Sådhanå Ó (2021) 46:76 Indian Academy of Sciences https://doi.org/10.1007/s12046-021-01584-6Sadhana(0123456789().,-volV)FT3](0123456789().,-volV) Rocket nozzles: 75 years of research and development SHIVANG KHARE1 and UJJWAL K SAHA2,* 1 Department of Energy and Process Engineering, Norwegian University of Science and Technology, 7491 Trondheim, Norway 2 Department of Mechanical Engineering, Indian Institute of Technology Guwahati, Guwahati 781039, India e-mail: [email protected]; [email protected] MS received 28 August 2020; revised 20 December 2020; accepted 28 January 2021 Abstract. The nozzle forms a large segment of the rocket engine structure, and as a whole, the performance of a rocket largely depends upon its aerodynamic design. The principal parameters in this context are the shape of the nozzle contour and the nozzle area expansion ratio. A careful shaping of the nozzle contour can lead to a high gain in its performance. As a consequence of intensive research, the design and the shape of rocket nozzles have undergone a series of development over the last several decades. The notable among them are conical, bell, plug, expansion-deflection and dual bell nozzles, besides the recently developed multi nozzle grid. However, to the best of authors’ knowledge, no article has reviewed the entire group of nozzles in a systematic and comprehensive manner. This paper aims to review and bring all such development in one single frame. The article mainly focuses on the aerodynamic aspects of all the rocket nozzles developed till date and summarizes the major findings covering their design, development, utilization, benefits and limitations. -
Propulsion Systems for Aircraft. Aerospace Education II
. DOCUMENT RESUME ED 111 621 SE 017 458 AUTHOR Mackin, T. E. TITLE Propulsion Systems for Aircraft. Aerospace Education II. INSTITUTION 'Air Univ., Maxwell AFB, Ala. Junior Reserve Office Training Corps.- PUB.DATE 73 NOTE 136p.; Colored drawings may not reproduce clearly. For the accompanying Instructor Handbook, see SE 017 459. This is a revised text for ED 068 292 EDRS PRICE, -MF-$0.76 HC.I$6.97 Plus' Postage DESCRIPTORS *Aerospace 'Education; *Aerospace Technology;'Aviation technology; Energy; *Engines; *Instructional-. Materials; *Physical. Sciences; Science Education: Secondary Education; Textbooks IDENTIFIERS *Air Force Junior ROTC ABSTRACT This is a revised text used for the Air Force ROTC _:_progralit._The main part of the book centers on the discussion -of the . engines in an airplane. After describing the terms and concepts of power, jets, and4rockets, the author describes reciprocating engines. The description of diesel engines helps to explain why theseare not used in airplanes. The discussion of the carburetor is followed byan explanation of the lubrication system. The chapter on reaction engines describes the operation of,jets, with examples of different types of jet engines.(PS) . 4,,!It********************************************************************* * Documents acquired by, ERIC include many informal unpublished * materials not available from other souxces. ERIC makes every effort * * to obtain the best copravailable. nevertheless, items of marginal * * reproducibility are often encountered and this affects the quality * * of the microfiche and hardcopy reproductions ERIC makes available * * via the ERIC Document" Reproduction Service (EDRS). EDRS is not * responsible for the quality of the original document. Reproductions * * supplied by EDRS are the best that can be made from the original. -
The SKYLON Spaceplane
The SKYLON Spaceplane Borg K.⇤ and Matula E.⇤ University of Colorado, Boulder, CO, 80309, USA This report outlines the major technical aspects of the SKYLON spaceplane as a final project for the ASEN 5053 class. The SKYLON spaceplane is designed as a single stage to orbit vehicle capable of lifting 15 mT to LEO from a 5.5 km runway and returning to land at the same location. It is powered by a unique engine design that combines an air- breathing and rocket mode into a single engine. This is achieved through the use of a novel lightweight heat exchanger that has been demonstrated on a reduced scale. The program has received funding from the UK government and ESA to build a full scale prototype of the engine as it’s next step. The project is technically feasible but will need to overcome some manufacturing issues and high start-up costs. This report is not intended for publication or commercial use. Nomenclature SSTO Single Stage To Orbit REL Reaction Engines Ltd UK United Kingdom LEO Low Earth Orbit SABRE Synergetic Air-Breathing Rocket Engine SOMA SKYLON Orbital Maneuvering Assembly HOTOL Horizontal Take-O↵and Landing NASP National Aerospace Program GT OW Gross Take-O↵Weight MECO Main Engine Cut-O↵ LACE Liquid Air Cooled Engine RCS Reaction Control System MLI Multi-Layer Insulation mT Tonne I. Introduction The SKYLON spaceplane is a single stage to orbit concept vehicle being developed by Reaction Engines Ltd in the United Kingdom. It is designed to take o↵and land on a runway delivering 15 mT of payload into LEO, in the current D-1 configuration. -
Nasa X-15 Program
5 24,132 6 9 NASA X-15 PROGRAM By: T.D. Barnes - NASA Contractor - 1960s NASA contractors for the X-15 program were Bendix Field Engineering followed by Unitec, Inc. The NASA High Range Tracking stations were located at Ely and Beatty Nevada with main control being at Dryden/Edwards AFB in California. Personnel at the tracking stations consisted of a Station Manager, a Technical Advisor, and field engineers for the Mod-2 Radar, Data Transmission System, Communications, Telemetry, and Plant Maintenance/Generators. NASA had a site monitor at each tracking station to monitor our contractor operations. Though supporting flights of the X-15 was their main objective, they also participated in flights of the XB-70, the three Lifting Bodies, experimental Lunar Landing vehicles, and an occasional A-12/YF-12/SR-71 Blackbird flight. On mission days a NASA van picked up each member of the crew at their residence for the 4:20 a.m. trip to the tracking station 18 miles North of Beatty on the Tonopah Highway. Upon arrival each performed preflight calibrations and setup of their various systems. The liftoff of the B-52, with the X-15 tucked beneath its wing, seldom occurred after 9:00 a.m. due to the heat effect of the Mojave Desert making it difficult for the planes to acquire altitude. At approximately 0800 hours two pilots from Dryden would proceed uprange to evaluate the condition of the dry lake beds in the event of an emergency landing of the X-15 (always buzzing our station on the way up and back). -
Comparison of Helicopter Turboshaft Engines
Comparison of Helicopter Turboshaft Engines John Schenderlein1, and Tyler Clayton2 University of Colorado, Boulder, CO, 80304 Although they garnish less attention than their flashy jet cousins, turboshaft engines hold a specialized niche in the aviation industry. Built to be compact, efficient, and powerful, turboshafts have made modern helicopters and the feats they accomplish possible. First implemented in the 1950s, turboshaft geometry has gone largely unchanged, but advances in materials and axial flow technology have continued to drive higher power and efficiency from today's turboshafts. Similarly to the turbojet and fan industry, there are only a handful of big players in the market. The usual suspects - Pratt & Whitney, General Electric, and Rolls-Royce - have taken over most of the industry, but lesser known companies like Lycoming and Turbomeca still hold a footing in the Turboshaft world. Nomenclature shp = Shaft Horsepower SFC = Specific Fuel Consumption FPT = Free Power Turbine HPT = High Power Turbine Introduction & Background Turboshaft engines are very similar to a turboprop engine; in fact many turboshaft engines were created by modifying existing turboprop engines to fit the needs of the rotorcraft they propel. The most common use of turboshaft engines is in scenarios where high power and reliability are required within a small envelope of requirements for size and weight. Most helicopter, marine, and auxiliary power units applications take advantage of turboshaft configurations. In fact, the turboshaft plays a workhorse role in the aviation industry as much as it is does for industrial power generation. While conventional turbine jet propulsion is achieved through thrust generated by a hot and fast exhaust stream, turboshaft engines creates shaft power that drives one or more rotors on the vehicle. -
Modelling a Hypersonic Single Expansion Ramp Nozzle of a Hypersonic Aircraft Through Parametric Studies
energies Article Modelling a Hypersonic Single Expansion Ramp Nozzle of a Hypersonic Aircraft through Parametric Studies Andrew Ridgway, Ashish Alex Sam * and Apostolos Pesyridis College of Engineering, Design and Physical Sciences, Brunel University London, London UB8 3PH, UK; [email protected] (A.R.); [email protected] (A.P.) * Correspondence: [email protected]; Tel.: +44-1895-267-901 Received: 26 September 2018; Accepted: 7 December 2018; Published: 10 December 2018 Abstract: This paper aims to contribute to developing a potential combined cycle air-breathing engine integrated into an aircraft design, capable of performing flight profiles on a commercial scale. This study specifically focuses on the single expansion ramp nozzle (SERN) and aircraft-engine integration with an emphasis on the combined cycle engine integration into the conceptual aircraft design. A parametric study using computational fluid dynamics (CFD) have been employed to analyze the sensitivity of the SERN’s performance parameters with changing geometry and operating conditions. The SERN adapted to the different operating conditions and was able to retain its performance throughout the altitude simulated. The expansion ramp shape, angle, exit area, and cowl shape influenced the thrust substantially. The internal nozzle expansion and expansion ramp had a significant effect on the lift and moment performance. An optimized SERN was assembled into a scramjet and was subject to various nozzle inflow conditions, to which combustion flow from twin strut injectors produced the best thrust performance. Side fence studies observed longer and diverging side fences to produce extra thrust compared to small and straight fences. Keywords: scramjet; single expansion ramp nozzle; hypersonic aircraft; combined cycle engines 1.