Heat Transfer
Total Page:16
File Type:pdf, Size:1020Kb
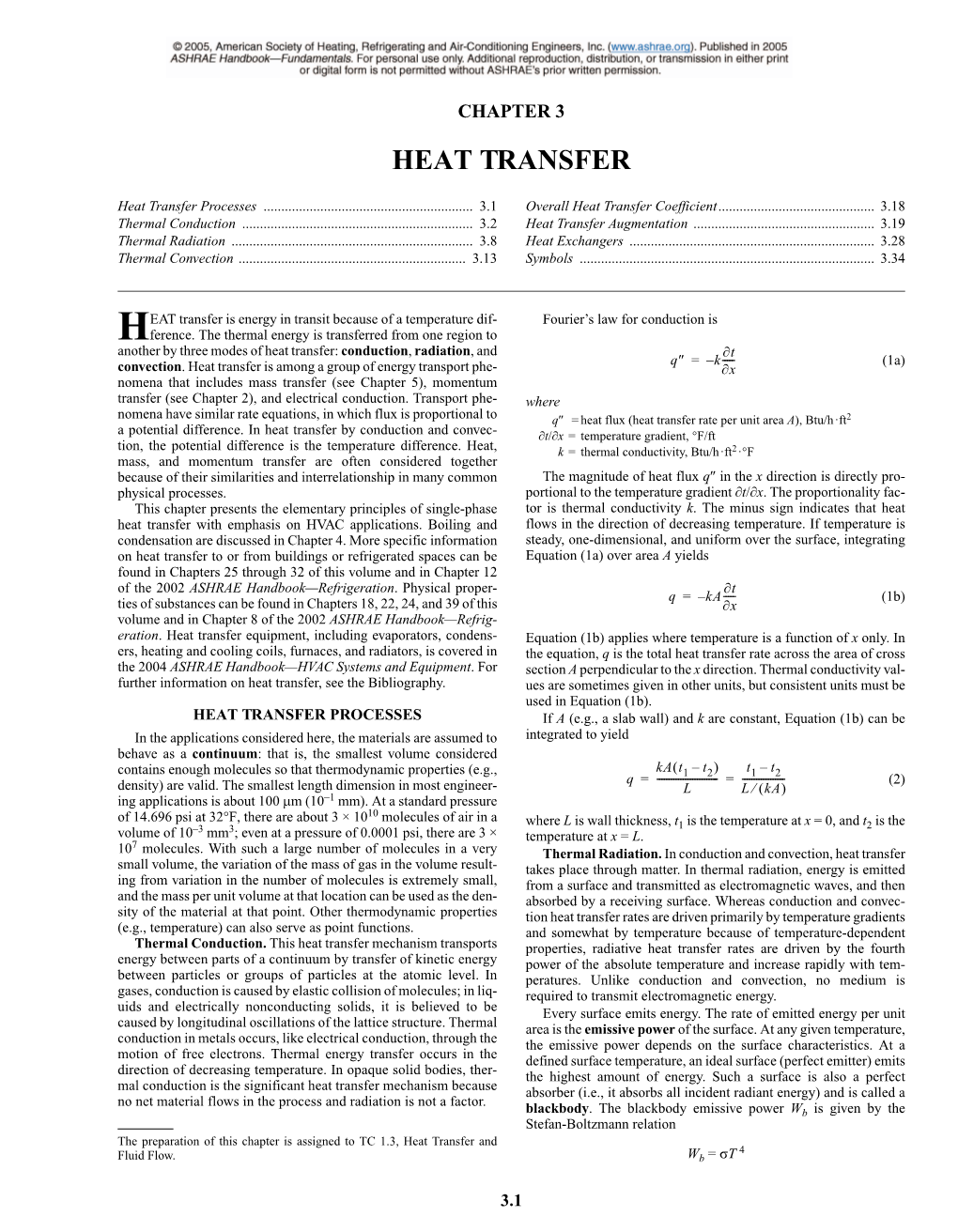
Load more
Recommended publications
-
Separation Points of Magnetohydrodynamic Boundary
Journal of Naval Architecture and Marine Engineering June,2018 http://dx.doi.org/10.3329/jname.v15i2.29966 http://www.banglajol.info MATHEMATICAL ANALYSIS OF NON-NEWTONIAN NANOFLUID TRANSPORT PHENOMENA PAST A TRUNCATED CONE WITH NEWTONIAN HEATING N. Nagendra1*, C. H. Amanulla2 and M. Suryanarayana Reddy3 1Department of Mathematics, Madanapalle Institute of Technology and Science, Madanapalle-517325, India. *Email: [email protected] 2Department of Mathematics, Jawaharlal Nehru Technological University, Anantapur, Anantapuramu-515002, India. Email: [email protected] 3Department of Mathematics, JNTUA College of Engineering, Pulivendula-516390, India. Email: [email protected] Abstract: In the present study, we analyze the heat, momentum and mass (species) transfer in external boundary layer flow of Casson nanofluid past a truncated cone surface with Biot Number effect is studied theoretically. The effects of Brownian motion and thermophoresis are incorporated in the model in the presence of both heat and nanoparticle mass transfer Biot Number effect. The governing partial differential equations (PDEs) are transformed into highly nonlinear, coupled, multi-degree non-similar partial differential equations consisting of the momentum, energy and concentration equations via appropriate non-similarity transformations. These transformed conservation equations are solved subject to appropriate boundary conditions with a second order accurate finite difference method of the implicit type. The influences of the emerging parameters i.e. Casson fluid parameter (β)(≥ 1), Brownian motion parameter (Nb) thermophoresis parameter (Nt), Lewis number (Le)(≥ 5), Buoyancy ratio parameter (N )( ≥ 0) Prandtl number (Pr) (7≤ Pr ≤ 100) and Biot number (Bi) (0.25 ≤ Bi ≤ 1)on velocity, temperature and nano-particle concentration distributions is illustrated graphically and interpreted at length. -
HEAT TRANSFER and the SECOND LAW Thus Far We’Ve Used the First Law of Thermodynamics: Energy Is Conserved
HEAT TRANSFER AND THE SECOND LAW Thus far we’ve used the first law of thermodynamics: Energy is conserved. Where does the second law come in? One way is when heat flows. Heat flows in response to a temperature gradient. If two points are in thermal contact and at different temperatures, T1 and T2 then energy is transferred between the two in the form of heat, Q. Heat Transfer and The Second Law page 1 © Neville Hogan The rate of heat flow from point 1 to point 2 depends on the two temperatures. Q˙ = f(T1,T2) If heat flows from hot to cold, (the standard convention) this function must be such that Q˙ > 0 iff T1 > T2 Q˙ < 0 iff T1 < T2 Q˙ = 0 iff T1 = T2 Heat Transfer and The Second Law page 2 © Neville Hogan In other words, the relation must be restricted to 1st and 3rd quadrants of the Q˙ vs. T1 – T2 plane. Q T1-T2 NOTE IN PASSING: It is not necessary for heat flow to be a function of temperature difference alone. —see example later. Heat Transfer and The Second Law page 3 © Neville Hogan HEAT FLOW GENERATES ENTROPY. FROM THE DEFINITION OF ENTROPY: dQ = TdS Therefore Q˙ = TS˙ IDEALIZE THE HEAT TRANSFER PROCESS: Assume no heat energy is stored between points 1 and 2. Therefore Q˙ = T1S˙ 1 = T2S˙ 2 Heat Transfer and The Second Law page 4 © Neville Hogan NET RATE OF ENTROPY PRODUCTION: entropy flow rate out minus entropy flow rate in. S˙ 2 - S˙ 1 = Q˙ /T2 - Q˙ /T1 = Q(T˙ 1 - T2) /T1T2 Absolute temperatures are never negative (by definition). -
An Experimental Approach to Determine the Heat Transfer Coefficient in Directional Solidification Furnaces
Journal of Crystal Growth 113 (1991) 557-565 PRECEDING p_GE B,LA(]'_,,_O'_7FILMED North-Holland N9 Y. An experimental approach to determine the heat transfer coefficient in directional solidification furnaces Mohsen Banan, Ross T. Gray and William R. Wilcox Center for Co,stal Growth in Space and School of Engineering, Clarkson University, Potsdam, New York 13699, USA Received 13 November 1990; manuscript received in final form 22 April 1991 f : The heat transfer coefficient between a molten charge and its surroundings in a Bridgman furnace was experimentally determined using m-sttu temperature measurement. The ampoule containing an isothermal melt was suddenly moved from a higher temperature ' zone to a lower temperature zone. The temperature-time history was used in a lumped-capacity cooling model to evaluate the heat i transfer coefficient between the charge and the furnace. The experimentally determined heat transfer coefficient was of the same i order of magnitude as the theoretical value estimated by standard heat transfer calculations. 1. Introduction Chang and Wilcox [1] showed that increasing the Biot number in Bridgman growth affects the A variety of directional solidification tech- position and shape of the isotherms in the furnace. niques are used for preparation of materials, espe- The sensitivity of interface position to the hot and cially for growth of single crystals. These tech- cold zone temperatures is greater for small Blot niques include the vertical Bridgman-Stockbarger, number. horizontal Bridgman, zone-melting, and gradient Fu and Wilcox [2] showed that decreasing the freeze methods. It is time consuming and costly to Biot numbers in the hot and cold zones of a experimentally determine the optimal thermal vertical Bridgman-Stockbarger system results in conditions of a furnace utifized to grow a specific isotherms becoming less curved. -
Chemically Reactive MHD Micropolar Nanofluid Flow with Velocity Slips
www.nature.com/scientificreports OPEN Chemically reactive MHD micropolar nanofuid fow with velocity slips and variable heat source/sink Abdullah Dawar1, Zahir Shah 2,3*, Poom Kumam 4,5*, Hussam Alrabaiah 6,7, Waris Khan 8, Saeed Islam1,9,10 & Nusrat Shaheen11 The two-dimensional electrically conducting magnetohydrodynamic fow of micropolar nanofuid over an extending surface with chemical reaction and secondary slips conditions is deliberated in this article. The fow of nanofuid is treated with heat source/sink and nonlinear thermal radiation impacts. The system of equations is solved analytically and numerically. Both analytical and numerical approaches are compared with the help of fgures and tables. In order to improve the validity of the solutions and the method convergence, a descriptive demonstration of residual errors for various factors is presented. Also the convergence of an analytical approach is shown. The impacts of relevance parameters on velocity, micro-rotation, thermal, and concentration felds for frst- and second-order velocity slips are accessible through fgures. The velocity feld heightens with the rise in micropolar, micro-rotation, and primary order velocity parameters, while other parameters have reducing impact on the velocity feld. The micro-rotation feld reduces with micro-rotation, secondary order velocity slip, and micropolar parameters but escalates with the primary order velocity slip parameter. The thermal feld heightens with escalating non-uniform heat sink/source, Biot number, temperature ratio factor, and thermal radiation factor. The concentration feld escalates with the increasing Biot number, while reduces with heightening chemical reaction and Schmidt number. The assessment of skin factor, thermal transfer, and mass transfer are calculated through tables. -
A Homemade 2 Dimensional Thermal Conduction Apparatus Designed As
AC 2008-292: A HOMEMADE 2-DIMENSIONAL THERMAL CONDUCTION APPARATUS DESIGNED AS A STUDENT PROJECT Robert Edwards, Pennsylvania State University-Erie Robert Edwards is currently a Lecturer in Engineering at The Penn State Erie, The Behrend College where he teaches Statics, Dynamics, and Fluid and Thermal Science courses. He earned a BS degree in Mechanical Engineering from Rochester Institute of Technology and an MS degree in Mechanical Engineering from Gannon University. Page 13.49.1 Page © American Society for Engineering Education, 2008 A Homemade 2-Dimensional Thermal Conduction Apparatus Designed as a Student Project Abstract: It can be fairly expensive to equip a heat transfer lab with commercially available devices. It is always nice to be able to make a device that provides an effective lab experience for the students. It is an extra bonus if the device can be designed as a student project, giving the students working on the device both a real design experience and a better understanding of the principles involved with the device and the associated lab exercise. One example of such a device is a 2-dimensional heat conduction device which was designed and built as a student senior design project by mechanical engineering technology students at Penn State Erie, The Behrend College. The device described in this paper allows the students to determine the thermal conductivity of several different materials, and to graphically see the effect of contact resistance in the heat conduction path. The students use the conductivity information to try to determine what material the test samples are made of. This paper describes the design of the device and the basic theory including a description of how it applies to this particular device. -
Introduction to Thermal Transport
Introduction to Thermal Transport Simon Phillpot Department of Materials Science and Engineering University of Florida Gainesville FL 32611 [email protected] Objectives •Identify reasons that heat transport is important •Describe fundamental processes of heat transport, particularly conduction •Apply fundamental ideas and computer simulation methods to address significant issues in thermal conduction in solids Many Thanks to … •Patrick Schelling (Argonne National Lab Æ U. Central Florida) •Pawel Keblinski (Rensselaer Polytechnic Institute) •Robin Grimes (Imperial College London) •Taku Watanabe (University of Florida) •Priyank Shukla (U. Florida) •Marina Yao (Dalian University / U. Florida) Part 1: Fundamentals Thermal Transport: Why Do We Care? Heat Shield: Disposable space vehicles Cross-section of Mercury Heat Shield Apollo 10 Heat Shield Ablation of polymeric system Heat Shield: Space Shuttle Thermal Barrier Coatings for Turbines http://www.mse.eng.ohio-state.edu/fac_staff/faculty/padture/padturewebpage/padture/turbine_blade.jpg Heat Generation in NanoFETs SOURCE ELECTRON 20 nm FINS RELAXATION G A D ~ 20 nm 10 3 T Q”’ ~ 10 eV/nm /s E DRAIN HOTSPOT EDGE Y-K. Choi et al., EECS, U.C. Berkeley BALLISTIC DRAIN TRANSPORT • Scaling → Localized heating → Phonon hotspot • Impact on ESD, parasitic resistances ? Thermoelectrics cold junction n-type p-type hot junctions Heat Transfer Mechanisms Three fundamental mechanisms of heat transfer: • Convection • Conduction •Radiation ¾ Convection is a mass movement of fluids (liquid or gas) rather than -
Strongly-Coupled Conjugate Heat Transfer Investigation of Internal Cooling of Turbine Blades Using the Immersed Boundary Method
Strongly-Coupled Conjugate Heat Transfer Investigation of Internal Cooling of Turbine Blades using the Immersed Boundary Method Tae Kyung Oh Thesis submitted to the faculty of the Virginia Polytechnic Institute and State University in partial fulfillment of the requirements for the degree of Master of Science In Mechanical Engineering Danesh K. Tafti – Chair Roop L. Mahajan Wing F. Ng May 13th 2019 Blacksburg, Virginia, USA Keywords: Conjugate heat transfer, immersed boundary method, internal cooling, fully developed assumption Strongly-Coupled Conjugate Heat Transfer Investigation of Internal Cooling of Turbine Blades using the Immersed Boundary Method Tae Kyung Oh ABSTRACT The present thesis focuses on evaluating a conjugate heat transfer (CHT) simulation in a ribbed cooling passage with a fully developed flow assumption using LES with the immersed boundary method (IBM-LES-CHT). The IBM with the LES model (IBM-LES) and the IBM with CHT boundary condition (IBM-CHT) frameworks are validated prior to the main simulations by simulating purely convective heat transfer (iso-flux) in the ribbed duct, and a developing laminar boundary layer flow over a two dimensional flat plate with heat conduction, respectively. For the main conjugate simulations, a ribbed duct geometry with a blockage ratio of 0.3 is simulated at a bulk Reynolds number of 10,000 with a conjugate boundary condition applied to the rib surface. The nominal Biot number is kept at 1, which is similar to the comparative experiment. As a means to overcome a large time scale disparity between the fluid and the solid regions, the use of a high artificial solid thermal diffusivity is compared to the physical diffusivity. -
Heat Transfer and Thermal Modelling
H0B EAT TRANSFER AND THERMAL RADIATION MODELLING HEAT TRANSFER AND THERMAL MODELLING ................................................................................ 2 Thermal modelling approaches ................................................................................................................. 2 Heat transfer modes and the heat equation ............................................................................................... 3 MODELLING THERMAL CONDUCTION ............................................................................................... 5 Thermal conductivities and other thermo-physical properties of materials .............................................. 5 Thermal inertia and energy storage ....................................................................................................... 7 Numerical discretization. Nodal elements ............................................................................................ 7 Thermal conduction averaging .................................................................................................................. 9 Multilayer plate ..................................................................................................................................... 9 Non-uniform thickness ........................................................................................................................ 11 Honeycomb panels ............................................................................................................................. -
Lecture 2. BASICS of HEAT TRANSFER ( )
Lecture 2. BASICS OF HEAT TRANSFER 2.1 SUMMARY OF LAST WEEK LECTURE There are three modes of heat transfer: conduction, convection and radiation. We can use the analogy between Electrical and Thermal Conduction processes to simplify the representation of heat flows and thermal resistances. T q R Fourier’s law relates heat flow to local temperature gradient. T qx Axk x Convection heat transfer arises when heat is lost/gained by a fluid in contact with a solid surface at a different temperature. TW Ts TW Ts q hAs TW Ts [Watts] or q 1/ hAs Rconv 1 Where: Rconv hAs Radiation heat transfer is dependent on absolute temperature of surfaces, surface properties and geometry. For case of small object in a large enclosure. 4 4 q s As Ts Tsurr Kosasih 2012 Lecture 2 Basics of Heat Transfer 1 2.2 CONTACT RESISTANCE In practice materials in thermal contact may not be perfectly bonded and voids at their interface occur. Even a flat surfaces that appear smooth turn out to be rough when examined under microscope with numerous peaks and valleys. Figure 1. Comparison of temperature distribution and heat flow along two plates pressed against each other for the case of perfect and imperfect contact. In imperfect contact, the “contact resistance”, Ri causes an additional temperature drop at the interface Ti Ri qx (1) Ri is very difficult to predict but one should be aware of its effect. Some order‐ of‐magnitude values for metal‐to‐metal contact are as follows. Material 2 Contact Resistance Ri [m W/K] ‐5 Aluminum 5 x 10 Copper 1 x 10‐5 Stainless steel 3 x 10‐4 Kosasih 2012 Lecture 2 Basics of Heat Transfer 2 We use grease or soft metal foil to improve contact resistance e.g. -
Causal Heat Conduction Contravening the Fading Memory Paradigm
entropy Article Causal Heat Conduction Contravening the Fading Memory Paradigm Luis Herrera Instituto Universitario de Física Fundamental y Matematicas, Universidad de Salamanca, 37007 Salamanca, Spain; [email protected] Received: 1 September 2019; Accepted: 26 September 2019; Published: 28 September 2019 Abstract: We propose a causal heat conduction model based on a heat kernel violating the fading memory paradigm. The resulting transport equation produces an equation for the temperature. The model is applied to the discussion of two important issues such as the thermohaline convection and the nuclear burning (in)stability. In both cases, the behaviour of the system appears to be strongly dependent on the transport equation assumed, bringing out the effects of our specific kernel on the final description of these problems. A possible relativistic version of the obtained transport equation is presented. Keywords: causal dissipative theories; fading memory paradigm; relativistic dissipative theories 1. Introduction In the study of dissipative processes, the order of magnitude of relevant time scales of the system (in particular the thermal relaxation time) play a major role, due to the fact that the interplay between this latter time scale and the time scale of observation, critically affects the obtained pattern of evolution. This applies not only for dissipative processes out of the steady–state regime but also when the observation time is of the order of (or shorter than) the characteristic time of the system under consideration. Besides, as has been stressed before [1], for time scales larger than the relaxation time, transient phenomena affect the future of the system, even for time scales much larger than the relaxation time. -
FHF02SC Heat Flux Sensor User Manual
Hukseflux Thermal Sensors USER MANUAL FHF02SC Self-calibrating foil heat flux sensor with thermal spreaders and heater Copyright by Hukseflux | manual v1803 | www.hukseflux.com | [email protected] Warning statements Putting more than 24 Volt across the heater wiring can lead to permanent damage to the sensor. Do not use “open circuit detection” when measuring the sensor output. FHF02SC manual v1803 2/41 Contents Warning statements 2 Contents 3 List of symbols 4 Introduction 5 1 Ordering and checking at delivery 8 1.1 Ordering FHF02SC 8 1.2 Included items 8 1.3 Quick instrument check 9 2 Instrument principle and theory 10 2.1 Theory of operation 10 2.2 The self-test 12 2.3 Calibration 12 2.4 Application example: in situ stability check 14 2.5 Application example: non-invasive core temperature measurement 16 3 Specifications of FHF02SC 17 3.1 Specifications of FHF02SC 17 3.2 Dimensions of FHF02SC 20 4 Standards and recommended practices for use 21 4.1 Heat flux measurement in industry 21 5 Installation of FHF02SC 23 5.1 Site selection and installation 23 5.2 Electrical connection 25 5.3 Requirements for data acquisition / amplification 30 6 Maintenance and trouble shooting 31 6.1 Recommended maintenance and quality assurance 31 6.2 Trouble shooting 32 6.3 Calibration and checks in the field 33 7 Appendices 35 7.1 Appendix on wire extension 35 7.2 Appendix on standards for calibration 36 7.3 Appendix on calibration hierarchy 36 7.4 Appendix on correction for temperature dependence 37 7.5 Appendix on measurement range for different temperatures -
Convective Heat Flux Explained.Indd
Convective heat flux explained Theory Thermal convection is one of the three mechanisms of heat transfer, besides conduction and thermal radia- tion. The heat is transferred by a moving fluid (e.g. wind or water), and is usually the dominant form of heat transfer in liquids and gases. Convection can be divided into natural convection and forced convection. Generally, when a hot body is placed in a cold envi- rameters like velocity of the fluid, material proper- ronment, the heat will flow from the hot body to the ties etc. For example, if one blows air over the tea cup, cold surrounding until an equilibrium is reached. the speed of the fluid is increased and thus the heat Close to the surface of the hot body, the surrounding transfer coefficient becomes larger. This means, that air will expand due to the higher temperature. There- the water cools down faster. fore, the hot air is lighter than the cold air and moves upwards. These differences in density create a flow, Application which transports the heat away from the hot surface To demonstrate the phenomenon of convection, the to the cold environment. This process is called natu- heat flux of a tea cup with hot water was measured ral convection. with the gSKIN® heat flux sensor. In one case, air was When the movement of the fluid is enhanced, we talk blown towards the cup by a fan. The profile of the about forced convection: An example is the cooling of a hot body with a fan: The fluid velocity is increased and thus the device is cooled faster, because the heat transfer is higher.