Module 6 Engineering Fabrication, Construction, and Architectural Drawings
Total Page:16
File Type:pdf, Size:1020Kb
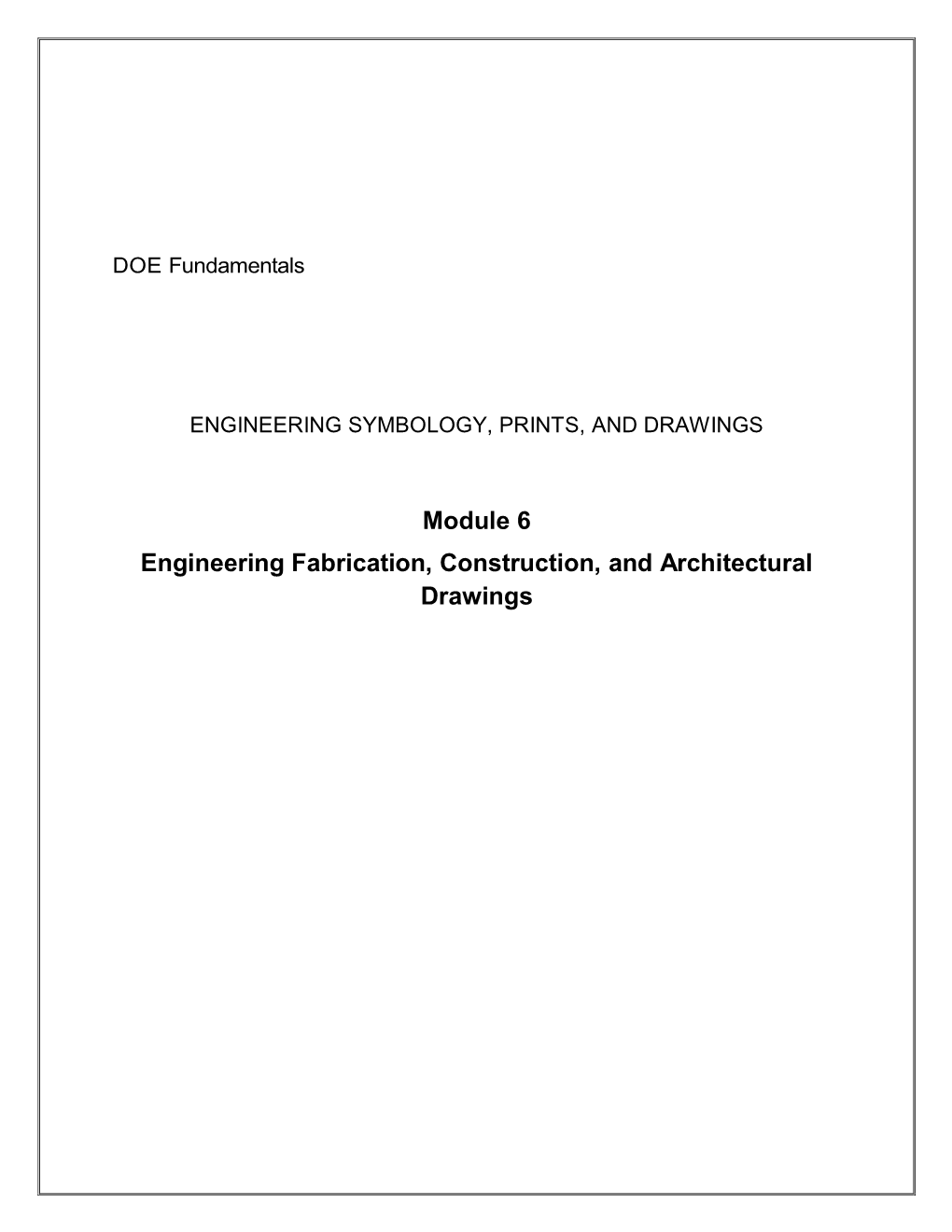
Load more
Recommended publications
-
Architecture's Cartographic Turn
Edinburgh Research Explorer Architecture’s Cartographic Turn Citation for published version: Dorrian, M 2005, Architecture’s Cartographic Turn. in F Pousin (ed.), Figures de la Ville et Construction des Savoirs: Architecture, Urbanisme, Geographie. CNRS Editions, Paris, pp. 61-72. <http://books.openedition.org/editionscnrs/4291> Link: Link to publication record in Edinburgh Research Explorer Document Version: Early version, also known as pre-print Published In: Figures de la Ville et Construction des Savoirs Publisher Rights Statement: Dorrian, M. (2005). Architecture’s Cartographic Turn. In F. Pousin (Ed.), Figures de la Ville et Construction des Savoirs. (pp. 61-72). Paris: CNRS Editions. General rights Copyright for the publications made accessible via the Edinburgh Research Explorer is retained by the author(s) and / or other copyright owners and it is a condition of accessing these publications that users recognise and abide by the legal requirements associated with these rights. Take down policy The University of Edinburgh has made every reasonable effort to ensure that Edinburgh Research Explorer content complies with UK legislation. If you believe that the public display of this file breaches copyright please contact [email protected] providing details, and we will remove access to the work immediately and investigate your claim. Download date: 28. Sep. 2021 1 Architecture’s ‘Cartographic Turn’ Mark Dorrian (Architecture, School of Arts, Culture and Environment, Univ. Of Edinburgh) Over the past thirty years something of a ‘cartographic turn’ has taken place in key areas of architectural theory and practice.1 What I mean by this is that there has been an increasing use of mapping as a generative – that is as a formal, formative, and not simply analytical – process within architectural projects. -
1938-1939 Undergraduate Catalogue
^ BULLETIN OF THE ^ UNIVERSITY OF VERMONT AND STATE AGRICULTURAL COLLEGE BURLINGTON ------- VERMONT VOLUME XXXVI — MARCH, 1939 — NUMBER 3 sofias 17SI THE CATALOGUE 19 3 8 -1 9 3 9 ANNOUNCEMENTS 19 3 9 -1 9 40 Published by the University of Vermont and State Agricultural College, Burlington, Vermont, four times a year; in January, February, March and October, and entered as second-class matter under Act of Congress of August 24, 1912 r 1 L Contents PAGE CALENDAR 5 UNIVERSITY CALENDAR 6-7 ADMINISTRATION 8-3 8 Board of Trustees 8—10 Office Hours 10 Officers of Instruction and Administration; Employees 11—27 Committees of the University Senate 27—28 Experiment Station Staff 28—30 Extension Service Staff 30—3 3 Summer School Faculty, 1938 34—3 8 GENERAL INFORMATION 39-98 Location 39 Charters, Corporations, History of the Colleges 39-44 Buildings and Grounds 44—5 6 Fees and Expenses 5 6-61 Employment, Loan Funds and Scholarships 61-73 Prizes 74-79 Honors 79-80 Degrees , 81 Graduate Study 82—86 University Extension 87-88 The Summer Session 8 8—89 Educational Conferences 89 Military Training 90 Physical Education and Athletics 90—92 Religious Life 92—93 Organizations 93—95 University Lectures 96 Publications 96 Regulations 97-98 ADMISSION 99-126 The Academic Colleges . 99—107 Methods of Admission . 107—110 Entrance Subjects 111—123 Special and Unclassified Students 123 Admission to Advanced Standing 123—124 Preliminary Registration and Enrollment 124 The College of Medicine, Requirements for Admission 125—126 COURSES OF INSTRUCTION 127-222 The -
The Computer's Role in Sketch Design: a Transparent Sketching
The Computer’s Role in Sketch Design: A Transparent Sketching Medium Michael Trinder The Martin Centre for Architectural and Urban Studies, University of Cambridge Department of Architecture Key words: sketching, sketch design, user-interface, transparency, immersion, computer- aided design Abstract: Starting from an analysis of the current unsuitability of computers for sketching, three key requirements are identified, in particular the notion that re-drawing or over-drawing are more important than editing and tweaking. These requirements are encapsulated in the broad concept of Transparency, understood both literally and metaphorically. Two experiments in implementing aspects of Transparency are described. One subverts the Macintosh window manager to provide windows with variable transparency, so that tracing between applications becomes a practical possibility. The other implements a graphical interface that requires no on-screen palettes or sliders to control it, allowing uninterrupted concentration on the design in hand. User tests show that the tool can be learnt quickly, is engaging to use, and most importantly, has character. 1. INTRODUCTION Computers are being used by architects almost exclusively for the later stages of design: one UK practice has been quoted as using CAAD for upwards of 90% of their issued drawings while early presentation work and sketches are made with pencil and paper. Under the temporal, financial and aesthetic pressures of the design office any tool will be used only for tasks that designers perceive are within its capability. Whether their current perception is based in prejudice, preference or past experience, designers avoid using computers for sketching. The software currently available for sketch design is plainly not working. -
Architectural Drawing (TE 8437) Grades 10 - 12 One Credit, One Year Counselors Are Available to Assist Parents and Students with Course Selections and Career Planning
Department of Teaching & Learning Parent/Student Course Information Technical Design and Illustration Program Architectural Drawing (TE 8437) Grades 10 - 12 One Credit, One Year Counselors are available to assist parents and students with course selections and career planning. Parents may arrange to meet with the counselor by calling the school's guidance department. COURSE DESCRIPTION The courses in engineering and technology provide opportunities for students to acquire skills and knowledge necessary for technological literacy, entry-level careers, and lifelong learning. Students learn Virginia’s 21 Workplace Readiness Skills within the content area. Those who are completing a two-year sequence have the opportunity to verify their knowledge of the workplace readiness skills through an industry assessment. This course provides students with the opportunity to learn more about the principles of architecture and related drafting practices and techniques. It provides helpful information for the homeowner and is beneficial to the future architect, interior designer, or homebuilder. Students use resource materials, standard books, and computers as they learn the general principles, practices and techniques of architectural drawing. The course includes designing residential structures and drawing plot plans, elevations, schedules and renderings. PREREQUISITE Basic Technical Drawing CERTIFICATION Students successfully completing the Technical Design and Illustration Program of Study will be prepared for the AutoCAD REVIT and or AutoCAD Architecture industry credential. STUDENT ORGANIZATION Technology Student Association (TSA) is a co-curricular organization for all students enrolled in engineering and technology courses. Students are encouraged to be active members of their youth organization to develop leadership and teamwork skills and to receive recognition for their participation in local, regional, state and national activities. -
Arch-Architecture 1
ARCH-ARCHITECTURE 1 ARCH 1110. Architectural Drawing ARCH-ARCHITECTURE 4 Credits (2+4P) This course is designed as an introduction to architectural drawing and ARCH 1105. Orientation and Mentoring in Architecture-Construction- design for students without prior experience in the fine arts. Students Engineering (ACE) are guided through a series of spatial and analytical exercises that 1-6 Credits (1-6) focus attention on not only how architects draw, but also the reasoning This course is intended for high school dual credit students and and processes embedded within the technique. Students are provided college/university students wishing to explore careers in Architecture, exposure to a wide range of interconnected architectural concepts Construction, and Engineering (ACE), which includes the specific fields and to manual and digital drawing, as well as modeling techniques for of Architectural, Civil, Mechanical, Structural, Interior, Landscape, architectural and interior design. Students will learn how to represent Sustainability, and Environmental. Students receive one-on-one composition, form, and space by orthographic drawing, paraline and mentoring, attend field trips, and engage in hands-on activities. May be perspective views, and freehand sketching. Three-dimensional model repeated up to 6 credits. Restricted to Community Colleges campuses building techniques will also be introduced. Learning Outcomes Learning Outcomes 1. Career opportunities related to ‘ACE’ 1. Gain understanding of basic methods of architectural drawing 2. Career requirements: Education 2. Explore and gain understanding of concepts of spatial design and its 3. Career requirements: Experience and/or examination(s) representation through exercises 4. Overview of construction/management 3. That stress analytical ability and an awareness of rational design 5. -
Commercial Drafting and Detailing 3Rd Edition Ebook, Epub
COMMERCIAL DRAFTING AND DETAILING 3RD EDITION PDF, EPUB, EBOOK Alan Jefferis | 9781435425972 | | | | | Commercial Drafting and Detailing 3rd edition PDF Book Internet a. Generally, an eBook can be downloaded in five minutes or less Dennis K. Common Office Practice A. This bestseller complements informational content with practical, hands-on material, including step-by-step instructions for the design and layout of each type of drawing associated with a complete set of architectural plans--all presented via projects that can be completed using CAD drawing methods. The text opens with information on architectural styles that have dominated the field over the last four centuries, followed by basic design components related to site and structure. Traditional drafting techniques used 30—60 and 45 degree set squares , and that determined the angles used in these views. Updates throughout this new edition introduce key principles of responsive design while integrating mobile design and testing. Worldwide in scope, it combines a clear historical outline with masterly analysis and interpretation. Tendency of material to: i. We use your LinkedIn profile and activity data to personalize ads and to show you more relevant ads. The author, an experienced design professional and award-winning educator, also emphasizes fundamental web design principles, helping readers develop knowledge and skills that go beyond a specific software package and can serve them well throughout their careers. Electrical Drawings 1. Embeds 0 No embeds. From Wikipedia, the free encyclopedia. Using online project files, students are encouraged to practice what they have learned by tackling design projects throughout the text from concept to completion. Show level of detail beyond working drawings b. -
1931–32 General Catalog
`University ' of California Bulletin THIRD SERIES, Vol. XXV, No. 4 CIRCULAR OF INFORMATION UNIVERSITYOF CALIFORNIA AT LOS ANGELES SEPTEMBER, 1931 UNIVERSITY OF CALIFORNIAPRESS BERKELEY, CALIFORNIA For Sale by the Students' Cooperative Book Store, 405 Hilgard Avenue, Los Angeles Price Five Cents Administrative Bulletins of the University of California 1931-32. No.4 The bulletins concerning the colleges , schools, and departments of the University are listed below. For copies of these circulars, and for further. information, address the University of California Press, Berkeley, except in those cases where Los Angeles and San Francisco are indicated. The circulars are sent free except those for which a price (which includes postage) isgiven. The Circular of Information, with reference primarily to the Under- graduate Division at Berkeley: containing general information about the University, its organization , requirements for admission to under- graduate status, and for the bachelor's degree in the colleges of Letters and Science, Agriculture, Commerce, and Engineering; students' fees and expenses. Sent free by mail by the University Press on request. A charge of 5 cents is made for copies distributed on the University Campus. The Annual Announcement of Courses of Instruction in the Departments at Berkeley. Price, 30 cents. The Circular of Information of the University of California at Los Angeles: containing general information about the University, requirements for admission to undergraduate status, and for the bachelor' s degree in the College of Letters and Science, in the Teachers College, and in the Branch of the College of Agriculture in Southern California; students' fees and expenses. Sent free by mail by the University Press on request. -
Abstract - Sketch Diagramming – a Contemporary Approach to Architectural Drawing
Anna Katrine Hougaard - The Royal Danish Academy of Fine Arts (KADK), School of Architecture - Philip de Langes Allé 10 - DK - 1435 Copenhagen K Mail: [email protected] Abstract - Sketch Diagramming – a contemporary approach to architectural drawing I would like to contribute a series of drawings for the exhibition and/or a paper for the group session discussions. In my Ph.D. project I approach architectural drawing as a notational system with the main capacity of orchestrating things and thoughts rather than depicting them. Drawing’s oper- ational capacity as a notational system (usually translating between drawing and building) operates both through iconic likeness, indexical impact and symbolic specification1. Archi- tectural drawing employs both digital and analogue notational systems2 and can be con- ducted with hand, manually by software, or by writing algorithms that produce drawings. Here I will elaborate the notion of sketch diagramming. Sketch indicates a loose, searching and developing process, and diagram indicates more rigor; maybe even a set of rules or a logic of reasoning. Nevertheless, diagrams can be both graphical - amounting in graphical works or paintings3 - as well as digital4. Sketch diagramming in the creative process can be thought of as a generative drawing game where rules can be employed, changed or invented as one draws, unspecific of drawing tool. When the rule-set of a sketch diagram becomes clear, it starts being a digital diagram and stops being a sketch diagram. Architectural drawing as sketch diagramming is an intermediary and responsive link which can be used to direct and negotiate a span from graphical intuitions to strict rules towards basically any chosen situation. -
Features and Design Intent in Engineering Sketches
View metadata, citation and similar papers at core.ac.uk brought to you by CORE provided by Repositori Institucional de la Universitat Jaume I Features and Design Intent in Engineering Sketches Raquel Plumed1, Peter Varley2, Pedro Company2 1 Department of Mechanical Engineering and Construction [email protected] 2 Institute of New Imaging Technologies [email protected], [email protected] Universitat Jaume I, Castellón de la Plana, Spain Abstract We investigate the problem of determining design intent from engineering sketches: what did the designer have in mind when sketching a component? Specifically, we consider the unidirectional reverse mapping from form features, as determined from an input sketch, to design features, representing the design intent present in the designer’s mind. We introduce a list of com- mon engineering form features. For each, we list which geometrical cues may be helpful in identifying these features in design sketches, and we list the design features which such form features commonly imply. We show that a reductionist approach which decomposes a diagram into form features can be used to deduce the design intent of the object portrayed in a drawing. We supply experimental results in support of this idea. 1 Introduction We aim to provide tools for design engineers who are already familiar with (and make good use of) the various features of state- of-the-art CAD packages, but who want the additional freedom offered by sketching when in the creative phase of designing a new product. Hence, we are interested in the interpretation of sketches of engineering components, both singly and in assemblies. -
Maps and Meanings: Urban Cartography and Urban Design
Maps and Meanings: Urban Cartography and Urban Design Julie Nichols A thesis submitted in fulfilment of the requirements of the degree of Doctor of Philosophy The University of Adelaide School of Architecture, Landscape Architecture and Urban Design Centre for Asian and Middle Eastern Architecture (CAMEA) Adelaide, 20 December 2012 1 CONTENTS CONTENTS.............................................................................................................................. 2 ABSTRACT .............................................................................................................................. 4 ACKNOWLEDGEMENT ....................................................................................................... 6 LIST OF FIGURES ................................................................................................................. 7 INTRODUCTION: AIMS AND METHOD ........................................................................ 11 Aims and Definitions ............................................................................................ 12 Research Parameters: Space and Time ................................................................. 17 Method .................................................................................................................. 21 Limitations and Contributions .............................................................................. 26 Thesis Layout ....................................................................................................... 28 -
CIJE1978 ABSTRACT: the MAIN POINT of THIS ESSAY IS TN§ 1Hr ACCESSION NUMBER;` 1J112249 SOUND ENERGY and Environmentalfolicy Is ONE THAT Erves NEEDS of LABOR
%I- I , AVAILABILITY.; -REPRINT AVAILABLE (SEE P. VII): UMI DESCRIPTOR: iicoNomIcsi 4.EMPtovolENTI ENERGY; mEtIVIRONMENTI * LABOR UNIONS; LABOR EC0NOMICs; POLIGY1 UNEMPLOYMENT JOGRNAL CITATION:. SCIENCE NEWS; 113; 16; 255 ISSUE; CIJE1978 ABSTRACT: THE MAIN POINT OF THIS ESSAY IS TN§ 1hr ACCESSION NUMBER;` 1J112249 SOUND ENERGY AND ENVIRONMENTALfOLICY is ONE THAT ERves NEEDS OF LABOR. 'THE ROLE OF LABOR /1,4 THE CONFLIC S BETH fN CLEARINGHOUSE ACCESSION NUMBER: 4E521937 ENERGY, ENVIRONMENT, ANO EMPLOYMENT IS DISCUSSED. NDR1 PUBLICATION ATE1 APR 78 AVAILABILITY: REPRINT AVAILABLE (SEE P..V111: UMI TITLE: THE SOL TRANSITION JOURNAL CITATION: ALTERNATIVES; 7; 3; 4 -13:16 P ER1ONAL AUTHOR: MMORIR, BARRY ApToet: .Ecomomicsi *ENERGY; *FEDERAL GOVERNMENTI' fACCESSION,NUIBER: EJ182600 IgrATIINIMAATAFIRItIMI WITATRIW2211 CCEARINGHOUSE ACCESSION NUMBER: AA528218 . ISSUE:, CIJEI97e . PUBLICATION FEB 78 :::// A gRwITEANET:11/ TITLE: 1977 MAJOR EOUCATION EVENT C FACIfill4LVESF141141111A2N111 Iga, NERGY PRE EN ED., IMR1 PERSONAL! AUTHOK: BROOINSKY, BEN e - 'AVilLASILITT.i REPRINT AVAILABLE (SEE P. VIII: UMI DEICRITON: *EDUCATIONAL TIEVEOPmENTi oMANDICAWED CH LOR *SUPREME COuR LITIGATI0N; *ENERGY CONSERVATIDN1 JOURNAL C)TATION: ENVIRONMENT; 20; 3,; 6- 10,13, op REN , REACTION; . GRAMiNG IBROAOCA5T11 CORPORAL PUNISHMENT ISSUE: C1JE1978 ACCESSION NUMBER; EJI82250 i, ABSTRACT: OESCRIBES THE EFFORT TO HANDICAPPED CLEAINGHOUSE ACCESSION NUMBER: 5E521938 CHILDREN UNDER PUBLIC 94-1421 DISCUSSDISCUSSES ESLUPREME CO T ACTION ON THE BAKKE CASE ANO ON CORPORAL -
REVOLUTIONS in PARALLEL: the RISE and FALL of DRAWING in ARCHITECTURAL DESIGN by Kristina M. Luce a Dissertation Submitted in Pa
REVOLUTIONS IN PARALLEL: THE RISE AND FALL OF DRAWING IN ARCHITECTURAL DESIGN by Kristina M. Luce A dissertation submitted in partial fulfillment of the requirements for the degree of Doctor of Philosophy (Architecture) in The University of Michigan 2009 Doctoral Committee: Professor Daniel Alan Herwitz, Co-Chair Associate Professor Malcolm McCullough, Co-Chair Professor Celeste A. Brusati Associate Professor Lydia M. Soo © Kristina M. Luce ____________________________ 2009 ACKNOWLEDGEMENTS The dissertation is more of a collaborative effort then an individual one. I am certainly responsible for the words on these pages, and I am, of course, solely responsible for any errors, but the thinking I cannot claim as mine alone. In this brief moment when one can acknowledge the contributions so generously provided by others, I find myself overwhelmed by the size of my indebtedness and by my gratitude for all scholars who brave criticism, and even ridicule, to share their thinking. One simply cannot make a contribution to any field without the first being inspired by the work that has come before, and the works of James Ackerman, James Elkins, Hans Belting, Mario Carpo, Wolfgang Lefèvre, Herbert Simon and John Harwood, among many others, were of enormous help in forming my own thoughts. More personally, this dissertation would not have the shape it does today had Greg Lynn, Neil Thelen, Evan Douglis and Richard Sarrach not given generously of their time, energy and expertise to share their thinking with me through a series of interviews. In some cases their words have found a place within my own, but they all have helped shape my understanding of the current state of design and practice within architecture.