SAMI Editor Redesign
Total Page:16
File Type:pdf, Size:1020Kb
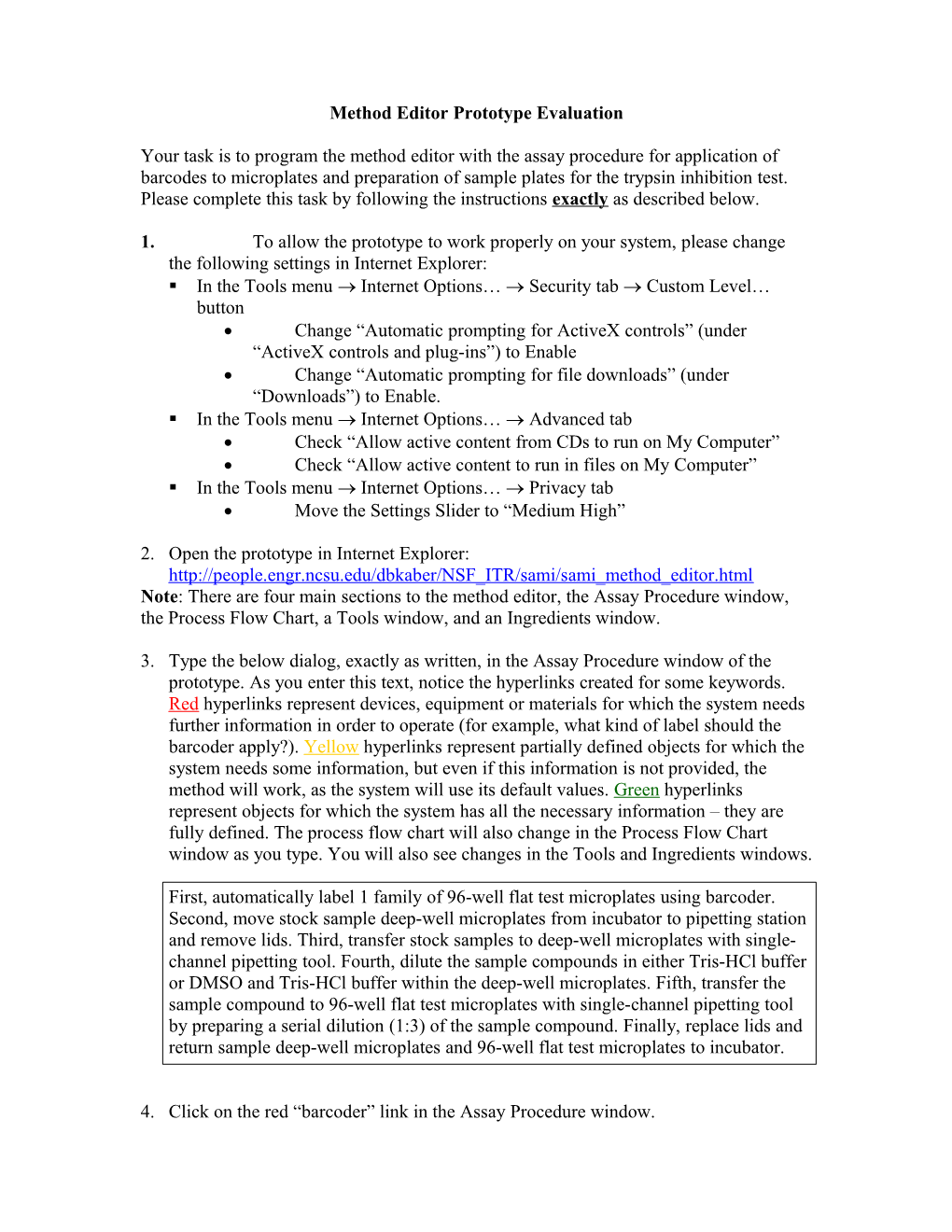
Method Editor Prototype Evaluation
Your task is to program the method editor with the assay procedure for application of barcodes to microplates and preparation of sample plates for the trypsin inhibition test. Please complete this task by following the instructions exactly as described below.
1. To allow the prototype to work properly on your system, please change the following settings in Internet Explorer: . In the Tools menu Internet Options… Security tab Custom Level… button Change “Automatic prompting for ActiveX controls” (under “ActiveX controls and plug-ins”) to Enable Change “Automatic prompting for file downloads” (under “Downloads”) to Enable. . In the Tools menu Internet Options… Advanced tab Check “Allow active content from CDs to run on My Computer” Check “Allow active content to run in files on My Computer” . In the Tools menu Internet Options… Privacy tab Move the Settings Slider to “Medium High”
2. Open the prototype in Internet Explorer: http://people.engr.ncsu.edu/dbkaber/NSF_ITR/sami/sami_method_editor.html Note: There are four main sections to the method editor, the Assay Procedure window, the Process Flow Chart, a Tools window, and an Ingredients window.
3. Type the below dialog, exactly as written, in the Assay Procedure window of the prototype. As you enter this text, notice the hyperlinks created for some keywords. Red hyperlinks represent devices, equipment or materials for which the system needs further information in order to operate (for example, what kind of label should the barcoder apply?). Yellow hyperlinks represent partially defined objects for which the system needs some information, but even if this information is not provided, the method will work, as the system will use its default values. Green hyperlinks represent objects for which the system has all the necessary information – they are fully defined. The process flow chart will also change in the Process Flow Chart window as you type. You will also see changes in the Tools and Ingredients windows.
First, automatically label 1 family of 96-well flat test microplates using barcoder. Second, move stock sample deep-well microplates from incubator to pipetting station and remove lids. Third, transfer stock samples to deep-well microplates with single- channel pipetting tool. Fourth, dilute the sample compounds in either Tris-HCl buffer or DMSO and Tris-HCl buffer within the deep-well microplates. Fifth, transfer the sample compound to 96-well flat test microplates with single-channel pipetting tool by preparing a serial dilution (1:3) of the sample compound. Finally, replace lids and return sample deep-well microplates and 96-well flat test microplates to incubator.
4. Click on the red “barcoder” link in the Assay Procedure window. Note: This opens an action/configuration dialog for the barcoder. There are similar functional links in the Process Flow Chart and the Tools windows for the barcoder dialog; however, please do not use these links.
5. Click on the Rotate icon in the lower right corner of the microplate image. Note: The microplate image rotates to show the left side of the plate.
6. Click on the Indexed label image on the right side of the window.
7. Click on the microplate image in the middle, in the top row of the grid.
8. In the new label information window, change the prefix of the label to EZ4Me.
9. Click OK. Note: The image of the label will appear on the microplate in the location you selected.
10. Click Apply. Note: Notice the changes in the color of the barcoder links. The barcoder is now fully defined: the system has all the necessary information to print and apply a barcode label.
11. Click on any yellow “incubator” link in the Assay Procedure window. Note: This opens an action/configuration dialog for the incubator. There are similar functional links in the Tools windows for the incubator dialog; however, please do not use these links.
12. Change the Minimum time in the Incubation Time section to 5 Minutes. Note: The time can be changed by clicking on the down arrow next to the Minutes box or clicking inside of the Minutes box, using backspace to delete the current time, and typing the new time.
13. Deactivate the Maximum time by clicking to unselect the checkbox. Note: When the checkbox is unchecked, the Maximum time will be deactivated in the dialog.
14. Click on the temperature knob near 37°C. Note: You can click on the rules between 35° and 40°. Notice the change in the window next to the knob.
15. Click Apply. Note: Notice that the color of the incubator links has changed from yellow (partially defined) to green (fully defined) in the Assay Procedure and Tools windows.
16. Click any yellow "deep-well microplates" link in the Assay Procedure window. Note: This opens a configuration window.
17. Select the radio button next to "96 Well - Deep (1 ml)".
18. Click OK. Note: Notice the changes in the wording of the assay procedure and the color of the microplate links in the Assay Procedure window and in the Tools window (Microplates tab).
19. Click Delete Device in the Tools window.
20. Click on the checkbox next to Liquid Pipettor – Biomek FX.
21. Click Delete Device. Note: Notice the removal of the Pipettor in the Devices tab of the Tools window.
22. Click Add Device in the Tools window.
23. Select Liquid Pipettor in the Device Type drop-down menu. Note: Notice the next menu is activated with this menu selection.
24. Select Biomek in the Manufacturer drop-down menu.
25. Select EL405 in the Model Type drop-down menu.
26. Click Add Device. Note: Notice the addition of the Pipettor in the Devices tab of the Tools window.
27. Click Run in the Menu bar at the top of the prototype.
28. Select Debug from the drop-down menu. Note: Notice the message in the window that pops up.
29. Click OK to dismiss the pop-up window. Do Not Close the final page. Follow the final instructions below.
You are currently viewing the Usability Data page. It is very important that you do not close this page until you have completed the appropriate steps to save this information. If you plan to FAX the evaluation materials, follow the steps for “Print for Fax”. If you plan to EMAIL the evaluation materials, follow the steps for “Save to File”.
Print for Fax: 1. In Internet Explorer, go to File and select Print. 2. Follow the same printing steps you would use to print a Microsoft Word document.
Save to File: 1. In Internet Explorer, go to File and select Save As… 2. Change Save As type from “Web Page, complete” to “Text file”. 3. Make sure that you are saving the file in a location that you will be able to find upon exiting Internet Explorer. 4. Click Save.