The Shotgun Pellets Interior Ballistics Analysis by Discrete Element Method (DEM) of LS-DYNA®
Total Page:16
File Type:pdf, Size:1020Kb
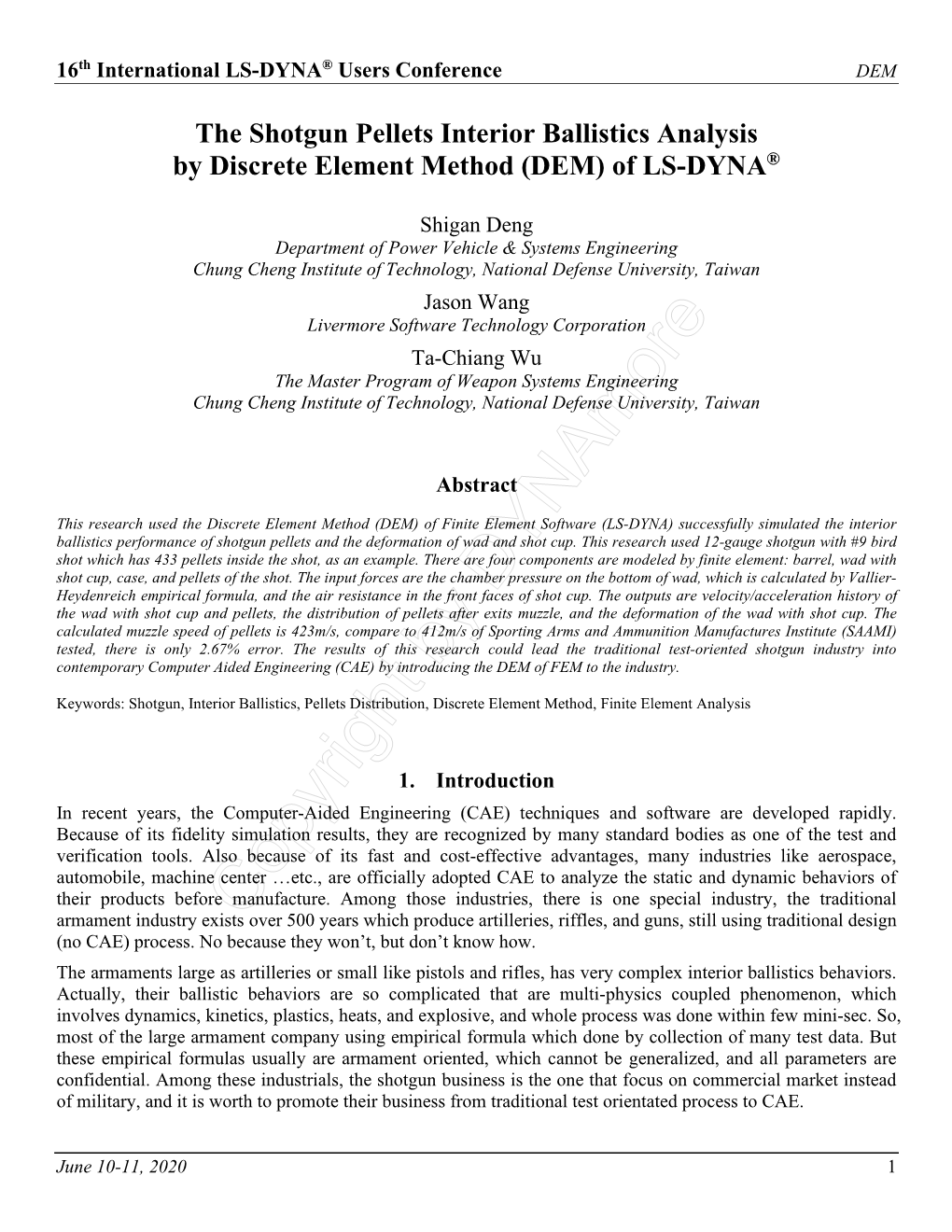
Load more
Recommended publications
-
The Interaction Between Clothing and Air Weapon Pellets Graham Wightman, K
CORE Metadata, citation and similar papers at core.ac.uk Provided by Abertay Research Portal The interaction between clothing and air weapon pellets Graham Wightman, K. Wark and J. Thomson This is the accepted manuscript © 2014, Elsevier Licensed under the Creative Commons Attribution-NonCommercial- NoDerivatives 4.0 International http://creativecommons.org/licenses/by-nc-nd/4.0/ The published article is available from doi: 10.1016/j.forsciint.2014.10.039 The interaction between clothing and air weapon pellets G.Wightman a, K. Wark, J Thomson a(Corresponding Author) School of Science Engineering and Technology, Abertay University, Bell Street, Dundee, DD1 1HG, Scotland. [email protected] Telephone: +44 1382 308659 Highlights • The effect of clothing on air weapon pellet penetration into ballistic gel has been examined. • Damage to the clothing depends on pellet shape and fabric weave. • Penetration depends: on range, pellet shape, the fabric weave, and how the clothing is in contact with the gel. • With loosely draped clothing at 20 yards range few pellets penetrated the gel. • Estimates suggest that these pellets stop in 75 microseconds, requiring a force of 1700 N. Abstract Comparatively few studies have been carried out on air weapon injuries yet there are significant number of injuries and fatalities caused by these low power weapons because of their availability and the public perception that because they need no licence they are assumed to be safe. In this study ballistic gel was tested by Bloom and rupture tests to check on consistency of production. Two series of tests were carried out firing into unclothed gel blocks and blocks loosely covered by different items of clothing to simulate attire (tee shirt, jeans, fleece, and jacket). -
About Pellet Numbers and Pellet Testing
AroundtheRange By Scott Pilkington About Pellet Numbers and Pellet Testing The first thing you need to know is ent head sizes. that competition airguns used in the Head sizes Olympic disciplines are .177 caliber, start at 4.48 which is equal to 177 thousandths of mm and con- an inch. The metric equivalent to .177 tinue through inch is 4.50 millimeters, therefore the 4.49, 4.50, 4.51 European caliber designation is 4.5 and 4.52 mm. mm. These sizes Here is a sampling of lot numbers on different packaging. are determined Next, you should know that the small- by the various est quantity of match pellets are typi- pellet (H & N, RWS, JSB, or Vogel) and size molds used to create the pellets cally packaged as 500 pellets and are a head size diameter (4.48, 4.9, 4.50, in the manufacturing process. But, you in containers called tins. When ten tins etc). It is a profound misunderstand- ask, isn’t one .177 barrel the same size are packaged together, they are called ing of this test target which causes so as another .177 barrel? No, not really. a sleeve. A sleeve contains 5,000 much confusion for parents, athletes pellets and weighs a little more than In the barrel manufacturing process, and coaches. six pounds. Five sleeves packaged the tolerances are such that the fin- Unfortunately, the conclusion of proper together are called a case. A case ished size of the lands and grooves of head size pellets for this particular contains 25,000 pellets and weighs the rifling will vary enough from one airgun is drawn when the new owner about 32 pounds. -
Analysis As Enacted (10/6/2016)
Legislative Analysis FIREARM DEFINITION/PNEUMATIC GUNS Phone: (517) 373-8080 http://www.house.mi.gov/hfa House Bill 4151 as enacted Analysis available at Public Act 21 of 2015 http://www.legislature.mi.gov Sponsor: Rep. Peter Pettalia House Bill 4152 as enacted House Bill 4155 as enacted Public Act 22 of 2015 Public Act 26 of 2015 Sponsor: Rep. Jason M. Sheppard Sponsor: Rep. Triston Cole House Bill 4153 as enacted House Bill 4156 without amendment Public Act 23 of 2015 Public Act 25 of 2015 Sponsor: Rep. Ray A. Franz Sponsor: Rep. Tom Barrett House Bill 4154 as enacted Senate Bill 85 as enacted Public Act 24 of 2015 Public Act 29 of 2015 Sponsor: Rep. Brett Roberts Sponsor: Sen. Dave Hildenbrand House Committee: Judiciary Senate Committee: Judiciary Complete to 10-6-16 BRIEF SUMMARY: Prior to the enactment of these bills, the definition of "firearm" differed somewhat among several statutes. The bill package aligns the definition of "firearm" in these statutes with the federal definition and no longer treats pneumatic guns (also known as "air-soft guns") and pellet guns as firearms, with some exceptions. With one exception, the bills took effect July 1, 2015; House Bill 4151 took effect May 12, 2015. The bills revise the definition of "firearm" to mean, unless otherwise specifically defined in statute, any weapon which will, is designed to, or may readily be converted to expel a projectile by action of an explosive. In addition, House Bill 4151 repeals an act that prohibited unaccompanied minors from using or possessing certain BB guns outside of their property. -
Typhoon F12 Owners Manual
TYPHOON DEFENCE INDUSTRIES F12 SEMI AUTOMATIC MAGAZINE FED FULL METAL SHOTGUN INSTRUCTION MANUAL READ THE INSTRUCTIONS AND WARNINGS IN THIS MANUAL BEFORE USING THIS FIREARM!!! INTRODUCTION TO TYPHOON DEFENCE INDUSTRIES For a long time Typhoon Defence Industries LLC. has been associated with the firearms industry in best way.The company has been manufacturing and exporting huge amount type of firearms to more than 28 countries ,where has C.I.P , SAAMI and TSE Test procedures by harmonizing the best modern technology and traditional craftmanship in manufacturing process. Typhoon Defence Industries LLC. has builded the company’s main philosophy and distinctive feature on Research&Development from the begining.This vision provided the company always putting signature to patented systems and inovative designs in Turkish market and International market with a lot of projects. Typhoon Defence Industries LLC. has these quality certificates : ISO 9001:2008 Certificate European Quality Assurance Certificate Turkish Standarts Institution Certificate Use your Typhoon Defence product for many years with high pleasure and feel yourself special by quality of your product!!! GENERAL INFORMATION This semi automatic shotgun (F12) uses gas pressure from the discharged shell in a precision,spring-loaded mechanism to eject empty shell, and load a new cartridge into the chamber(each time the trigger pulled).The system reduces recoil , and allows the shooter to concentrate on target. This technologically advanced gas metering system allows you to shot 2 ¾’’ and 3’’ shells interchangeably with ammunition of the proper gauge for your shotgun with flawless performance.This and other fine features ensure that your shotgun will be a source of pride and pleasure for many years in forward.For 3 ½’’ models the metering system allows you to shot heavy 2 ¾’’ , 3’’ , 3 ½’’ shells interchangeably. -
Air Gun Shooting Sports Safety Guide
AIR GUN SHOOTING SPORTS SAFETY GUIDE Developed by the Education & Training and Competitive Shooting Divisions A Publication of the National Rifle Association of America First Edition – January, 2006 Copyright, 2006, National Rifle Association All rights reserved. Printed in the United States of America. This book may not be reprinted or reproduced in whole or in part by mechanical means, photocopying, electronic reproduction, scanning, or any other means without prior written permission. For information, write to: Training Department, Education & Training Division, National Rifle Association, 11250 Waples Mill Road, Fairfax, Virginia 22030 01-06 AIR GUN SHOOTING SPORTS SAFETY GUIDE TABLE OF CONTENTS INTRODUCTION .............................................................................................................. 1 BASIC AIR GUN SAFETY............................................................................................... 3 Safety .............................................................................................................................. 3 The Safe Gun Handling Rules ........................................................................................ 3 SAFETY PRECAUTIONS AND PROCEDURES ........................................................ 6 Mechanical Safety....................................................................................................... 6 Safety Enhancers............................................................................................................. 7 Safety Rod.................................................................................................................. -
Firearms 101
Firearms 101 Shotgun Course and Rifle Muzzleloader Course have been combined into one all inclusive Firearms Course. Firearms Course now covers - Shotgun shooting - Rifle shooting - Airguns - Muzzleloaders Live Fire will only be done with the shotgun. New Course Completion Cards say “Firearm” - Will allow you to buy both a firearms hunting license and a rifle permit 1 Treat Every Firearm as if it were Loaded Treat every firearm as if it were loaded - Never accept a firearm from someone until they have proven it is unloaded - Safety is always ON. When does it come off? – When firearm is mounted on your shoulder and you know your target and what is beyond. - Do I use the scope as binoculars? No 2 Keep Muzzle in a Safe Direction Keep Muzzle pointed in a safe direction - What is a safe direction? A safe direction is always changing. - Need to be very aware of your surroundings anytime you have a firearm in your hand. - Two Hand Ready Position gives you best control of the muzzle 3 Be Sure of Your Target and Behind Know your target and beyond - .22 ammo = 1 mile - Shotgun slug = about 3600 ft - 00 Buckshot = about 1800 ft - Fine shot 500 – 900 ft - Distances above are with firearm pointed at optimum angle in the air. Projectile can ricochet even further - Should never shoot at a deer on crest of hill or bear in a tree. - Puts in perspective just how far a shotgun slug can go. - 450 ft Safety zone is not a ballistic cloak, but just a small buffer between us hunters and those that don’t hunt. -
Humane Killing of Livestock Using Firearms
Humane Killing of Livestock using Firearms This is the downloadable PDF version of the online guide. As such, some of the features are missing, including video footage and web links. The online version may be accessed from www.hsa.org.uk Introduction In all livestock production systems, no matter how well they are managed, there will be times when animals have to be humanely destroyed in order to protect their welfare. In most cases, these animals will be casualties which have not responded to treatment, or emergencies (animals with serious physical injuries or in acute, unrelievable pain). The latter may occur: on-farm; in transit; in markets, lairages or collection centres; or as a result of accidents on the public highway, at racecourses, shows or exhibitions. Used properly, firearms provide one of the quickest and most effective methods of humane killing of livestock. This publication has been written for all those, particularly veterinary surgeons, knackermen, slaughtermen, farm staff and police firearms officers, who may be directly or indirectly involved with the killing of large farm animals. It covers the humane destruction of cattle, sheep, pigs, deer, goats and horses, using humane killers, handguns, rifles and shotguns, discharged at close quarters, i.e. within 25 centimetres of the target – the animal’s head. All of these weapons fire free projectiles (single bullets or shot-charges) and their use is intended to kill the animals outright, with no need for further action on the part of the operator. This has definite advantages in certain situations where exsanguination or pithing would be undesirable or inappropriate. -
Hunting Ordinance (1).Pdf
Hunting Ordinance, Requirements for Hunting We do not have a HUNTING MAP showing locations in which you are permitted to hunt in Washington Township. Use this ordinance to determine if you meet the requirements and are able to hunt on property within Washington Township. 72.000 - DISCHARGE OF FIREARMS ORDINANCE Sec. 2: The following words, terms and phrases when used in this Ordinance shall have the meaning described to them in this section, except where the context clearly indicates a different meaning: A. Firearm means any weapon or device from which is propelled, by means of explosives, compressed air or gas, springs, levers, or other mechanical devices, any missile, projectile, bullet, shot, pellet or slug. B. Private Shooting Range means any area of land, building, structure, or portion thereof kept, used or maintained, in whole or in part, for the shooting or discharge of firearms and/or weapons which is not held out for use by the general public. C. Public Shooting Range means any area of land, building, structure, or portion thereof kept, used or maintained, in whole or in part, for the shooting or discharge of firearms and/or weapons which is held out for use by the general public. D. Weapon means any device from which it is, or appears to be, capable of discharging or propelling any projectile, arrow, missile, knife, spear, bullet, shot, pellet or slug. Sec. 3: In all parts of the Township, it shall be prohibited to either discharge or attempt to discharge a firearm within 450 feet of an occupied building, dwelling, residential structure, cabin, house, or any barn or other building used in connection with a farm operation, without obtaining the written permission of the owner, renter, or occupant of the property, except in the following circumstances: A. -
1357.Full.Pdf
AMERICAN ACADEMY OF PEDIATRICS TECHNICAL REPORT Danielle Laraque, MD, and the Committee on Injury, Violence, and Poison Prevention Injury Risk of Nonpowder Guns ABSTRACT. Nonpowder guns (ball-bearing [BB] guns, used in war games designed to mark the player with pellet guns, air rifles, paintball guns) continue to cause paint when he or she is hit. Air guns have been used serious injuries to children and adolescents. The muzzle since the 16th century7,8 in warfare and to kill game velocity of these guns can range from approximately 150 as large as deer. ft/second to 1200 ft/second (the muzzle velocities of tra- The caliber of a projectile refers to its diameter and ditional firearm pistols are 750 ft/second to 1450 ft/sec- ond). Both low- and high-velocity nonpowder guns are is measured in hundredths of an inch or millimeters. associated with serious injuries, and fatalities can result The caliber affects how much energy the projectile from high-velocity guns. A persisting problem is the lack acquires before leaving the muzzle, or the end of the of medical recognition of the severity of injuries that can barrel. Tight-fitting missiles, those with little discrep- result from these guns, including penetration of the eye, ancy between the diameter of the projectile and that skin, internal organs, and bone. Nationally, in 2000, there of the muzzle, lead to higher velocities. In older were an estimated 21840 (coefficient of variation: 0.0821) nonpowder guns, the projectile was smaller than the injuries related to nonpowder guns, with approximately barrel size, leading to dissipating of compressed air 4% resulting in hospitalization. -
Choke It… Or Don't
Choke it… or don’t Many issues back in an article about patterning your shotgun, I briefly discussed chokes and how they regulate the size of the pattern. But, like most things in the sport shooting world, there is so much more to understand. Shotguns intended to shoot payloads of shot have a smooth bore. There is no rifling inside the barrel to impart spin on the payload and, interestingly, with a shot pattern would actually be counterproductive. The spin imparted by rifling would cause the shot pattern to disperse rapidly because of centrifugal force. Without spin the pattern will fly straight and will disperse more naturally by air resistance on the pellets, among other factors. This illustration helps to understand how choke works. Early on in the development of shotguns it was learned that tapering the bore diameter to some degree near the muzzle would regulate the size of the pattern at given distances. From the early 1800s on through to today the principle of applying constriction; choking the barrel down, remains relatively unchanged. It is interesting that the amount of constriction is actually quite minute. A 12 gauge shotgun, for instance, has a nominal bore diameter of 0.729 of an inch. Adding a taper down equivalent of just two hundreths of an inch changes the pattern from a 40 inch diameter at 25 yards, Cylinder choke, to a forty inch pattern at 35 yards, Modified choke. Standards were eventually established and remain to this day as illustrated in the table below. Where things get confusing is in the markings. -
Case Report of an Airsoft Gun Injury
ACS Case Reviews in Surgery Vol. 1, No. 2 Gunshot Wound to Chest with Embolization of Pellet into the Left Ventricle: Case Report of an Airsoft Gun Injury AUTHORS: CORRESPONDENCE AUTHOR: AUTHOR AFFILIATIONS: Gurria Ja, Riney Lb, Fain Ec, Brown Rd, Morales De Juan Gurria, MD a. Cincinnati Children’s Hospital Medical Center, Division of Pediatric General and Thoracic Surgery Division of Pediatric General and Thoracic Surgery, Trauma Surgery Fellow Cincinnati, OH Cincinnati Children’s Hospital Medical Center b. Cincinnati Children’s Hospital Medical Center, 3333 Burnet Ave. Division of Emergency Medicine, Cincinnati, OH ML 2023 c. Cincinnati Children’s Hospital Medical Center, Cincinnati, OH 45229 Division of Emergency Medicine, Cincinnati, OH (713) 2916850 d. Cincinnati Children’s Hospital Medical Center, [email protected] University of Cincinnati Department of Surgery, Cincinnati, OH e. Clark-Helmsworth Chair of Pediatric Cardiothoracic Surgery, Heart Institute Cincinnati Children’s Hospital Medical Center, University of Cincinnati College of Medicine, Cincinnati, OH Background Significant injuries can occur from various types of nonpowder guns (NPGs), such as BB and pellet guns. This is a case report of a gunshot wound to chest with an NPG. Summary An adolescent male presented to a pediatric emergency department (ED) hemodynamically stable after being shot at close range in the chest with an airsoft gun. Echocardiogram and computed tomography angiogram (CTA) visualized the pellet inside the left ventricle (LV). Unclear of the risk of embolization, the patient underwent cardiac exploration, which revealed no external injury to the heart or mediastinum; intracardiac exploration, however, revealed that the bullet was embedded in the LV myocardium. -
Remington Guide to Shotguns
ShotgunsTHE REMINGTON GUIDE TO AND AmmunitionShotshell WARNING! Before using your firearm, read both the Instruction Manual for your Remington firearm and the Remington Firearms Safety Guide. Remember, firearm safety depends on you! TABLE OF CONTENTS INTRODUCTION INTRODUCTION As you might imagine, we get a lot CHAPTER 1: of questions about shotgunning Shotguns here at Remington. Hunters want TYPES AND ACTIONS GAUGES to know if they can shoot 2-3/4" CHAMBER LENGTHS BARREL LENGTHS shells in their 3"-chambered gun; CHOKES SIGHTS what choke works best on late- CHAPTER 2: season pheasants; how steel shot Shotgun Shells compares to lead shot; or what the A NATOMY OF A SHOTSHELL GAUGES heck “dram equivalent” means? SHELL LENGTHS GUN POWDER The list goes on and on. So, in SHOT response, we thought we’d take CHAPTER 3: Hunting some of the most often-asked and Shooting with a Shotgun HUNTING: MATCHING GAUGES questions and create a concise, AND AMMUNITION TO GA M E easy-to-understand reference that TARGET SHOOTING you can use whenever you need it. WHERE TO HUNT AND SHOOT And here it is: The Remington Guide to Shotgun Use. If you’re just getting started with a shotgun, it will provide a wealth of information and probably answer just about every question you can dream up. If you’re an experienced shotgunner, you just might find a few bits of information that can make you even more knowledgeable. CHAPTER 1: Shotguns TYPES AND ACTIONS For as long as hunters have taken afield, there has been discussion about which type of shotgun is “the best.” This, of course, is largely a matter of opinion.